Wind Energy
Sandia Wake Imaging System Successfully Deployed at the SWiFT Facility
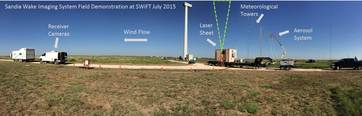 Figure 1.
Sandia Wake Imaging System deployed at the SWiFT Facility in July 2015.
The Sandia Wake Imaging System (SWIS) was
deployed for a full-scale field demonstration at the Sandia Scaled Wind Farm
Technology (SWiFT) Facility in Lubbock, Texas over the first three weeks of
July 2015. The successful field-demonstration was a culmination of over 3 years
of technical development, more than a year of safety, environmental and
regulatory approvals, and the efforts of 20 individuals from across Sandia and
its partners. The team collected hours of inflow data covering a 3.5 m square
viewing region along with simultaneous measurements from a nearby sonic
anemometer, the SWiFT Sandia meteorological tower, and a Pentalum SpiDAR LiDAR
system operated by Texas Tech University researchers. In the coming months, the
Sandia team will be analyzing over 50 gigabytes of data collected to learn more
about how the SWIS operates in the field and what improvements would be most
effective at helping achieve experimental measurement requirements for the next
campaign.
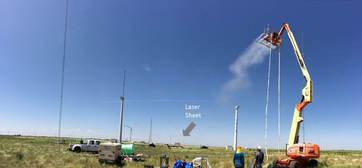 Figure 2.
A view upwind of the aerosol generating system.
The Sandia Wake Imaging System (SWIS) was
developed to improve the spatial and temporal resolution capabilities of
velocity measurements within wind farms. These high-resolution velocity
measurements are needed to provide the necessary data for validating
high-fidelity simulations. SWIS uses a technology (explained thoroughly in a
previous report) where the
velocity component measured and quality of the measurement depends on the
configuration of the transmitter (laser sheet), receiver (camera), and viewing
region. As a result of the complicated measurement dependence on setup
configuration and the need to meet the validation requirements at many
locations in a wind turbine wake, a software tool that models the physics of
SWIS was developed to better predict and anticipate the system’s performance
when deployed at the Scaled Wind Farm Technology (SWiFT) facility. Data from
the recent field test will be used to verify the accuracy of this tool for
future test campaign planning.
The
experience and data obtained from this recent field test will be used to guide
the next phase of the project in the coming year. Through ongoing discussions
with high-fidelity modelers and experimentalists with complimentary
instrumentation, the SWIS team will refine the system to meet upcoming
experimental objectives. This may include upgrades to hardware and software
systems as well as data post-processing techniques to prepare for future
verification and validation exercises planned under the Atmosphere to Electron
(A2e) and other research programs. For more information, please contact the
author below.
Brian
Naughton,
(505) 844-4033.
Institute for Advanced Composites Manufacturing Innovation – Inaugural
Members Meeting
Sandia Wind Department technical staff
members Josh Paquette and Brian Naughton attended the inaugural members meeting
for the newly formed Institute for Advanced Composites Manufacturing Innovation
(IACMI) in Knoxville, TN, June 16th
– 18th. A few hundred
attendees from the composites industry, academic institutions, and government
agencies gathered to learn about opportunities to participate in the newest
institute to join the National Network for Manufacturing Innovation,
established through the Revitalize American Manufacturing Act.
The program began with a signing ceremony
between the DOE Assistant Secretary for Energy Efficiency and Renewable Energy
David Danielson, IACMI CEO Craig Blue, and University of Tennessee Executive
Vice President David Millhorn. Following were a series of presentations on the
organizational structure and goals of the IACMI. The Five Year Technical Goals
for IACMI include:
-
25% lower
carbon fiber-reinforced polymer (CFRP) cost
-
50%
reduction in CFRP embodied energy
- 80%
composite recyclability into useful products
These goals will be achieved through the
integrated research and development work conducted in 5 technology areas: Wind
Turbines, Vehicles, Compressed Gas Storage, Design, Modeling & Simulation,
and Composite Materials & Process. Each technology area is headed by a director
that will help coordinate research within and between technology areas to
ensure the work meets the overall institute goals.
Sandia National Laboratories looks forward to
bringing their 25 plus years of experience in wind turbine composites and
manufacturing to the institute to work with previous and new industry and
academic partners to realize the Institute’s goals and enhance the
competitiveness of US composites manufacturing.
For more information, please contact the
authors below.
Brian Naughton,
505-844-4033.
Josh Paquette,
505-844-7766.
Version 24 of the Composite Materials Database Now Available for
Download
Wind turbine
blade growth continues to have the largest impact on energy capture and LCOE
reduction. While the 40-45 meter blade is today’s mainstream segment, it is
estimated that blades over 50m will be the global norm by 2020, as the industry
continues to develop higher power rating and lower-wind-speed turbines. This
considerable growth in blade length drives challenging technical and economic
demands on blade designers requiring a constantly improving understanding of
composite material behavior in realistic wind applications.
To address
this continued need, Sandia National Laboratories has partnered with Montana
State University since 1989 to test and report key data and trends of
fiber-reinforced polymers (composites) and other materials used in the
construction of wind turbine blades. As
of 2015, researchers at Montana State University have compiled the results of
over 16,000 tests on 500 materials into a publically available database along
with technical papers explaining key trends to meet this critical industry
need.
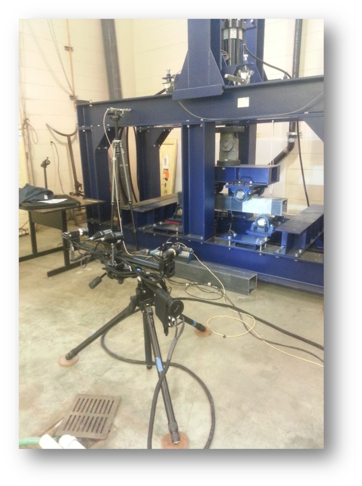 Figure 3. Montana
State University researchers have added acoustic emission and digital image
correlation instrumentation to enhance the data collection capabilities of the
sub-structure test fixture.
Recent
additions to the blade materials database include:
- Unidirectional
and + 45 static and fatigue results for three epoxy resin systems
(Hexion 035, 135 and 145) with fiberglass fabrics
-
Static and
fatigue results for Materia pDCPD and glass fiber composites
-
Updated
references, contacts, links to complete reports discussing data.
The latest
database (v.24.0) is available for download here.
Related
publications can be accessed on Sandia’s website
and the Montana State University Composite Technologies Research Group website.
For more
information please contact the author below.
Brian Naughton,
(505) 844-4033.
Water Power
Lab Researchers and FOA Awardees Collaborate on WEC Survival
Researchers
from Sandia and NREL will be working with awardees of DE-FOA-0001310
on the survival analysis of wave energy converters (WECs). Up to three awardees
will collaborate with lab researchers with the aims of increasing device
survivability and reducing system design margins. Design response analysis
methods and processes developed at Sandia and NREL will be employed to produce
more accurate predictions of extreme responses and design loads for the
awardees’ devices.
Ryan
Coe, (505) 845-9064.
Water Power: Wave Energy – Device
Modeling: Development of a 1:17 Scaled
Model
A large number of theoretical studies have
shown promising results in the additional energy that can be captured through
control of the power conversion chains (PCCs) of resonant WEC devices. The
numerical models employed in these studies are, however, idealized to varying
degrees. The objective of the Resilient Nonlinear Controls (RNLC) project is to
validate the extent to which control strategies, given real world limitations,
can increase the energy production of rigid-body WEC devices. RNLC includes
both numerical and experimental components in order to make the difficult leap
from idealized, theoretical paper studies to deployable WEC hardware.
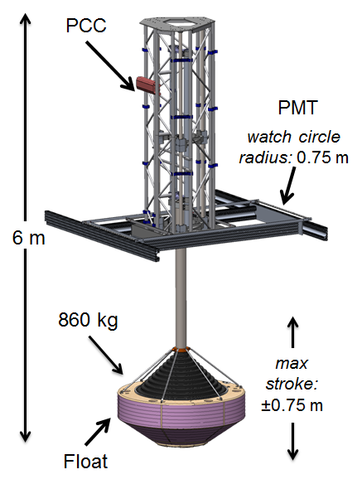
Figure 4.
General overview of the T3R2 device.
A 1:17 scaled WEC shown in Fig. 4, named T3R2
(three-translations, two-rotations), has been designed and is currently being
constructed for the experimental component of this project. The operational
principle of the device was selected to provide a test-bed for control
strategies, in which a specific control strategies effectiveness and the
parameters on which its effectiveness depends can be empirically determined.
Numerical design studies were employed to determine the device geometry, so as
to maximize testing opportunities in the Maneuvering and Seakeeping (MASK)
Basin at the Naval Surface Warfare Center’s David Taylor Model Basin.
To better approach the reality of
ocean-deployed WECs, a number of sources of nonlinearity were intentionally
included in the T3R2's design. Additionally, the device was designed such that
the presence of these nonlinearities, which include dynamics, viscous losses,
overtopping and breaching events, nonlinear hydrostatics/hydrodynamics as well
as motion constraints, can be largely controlled, either via mechanical
``locks'' or through the input to the system (i.e. basin waves).
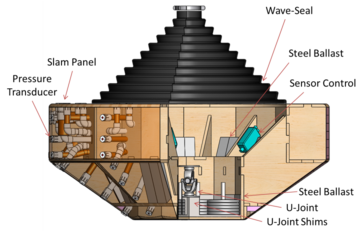
Figure 5.
Detailed view of the float.
T3R2 is selectively allowed to move in three
dimensions. The T3R2's float is connected to the power conversion mechanism
through a lockable universal joint (see ``U-joint'' in the detailed
representation of the float Fig. 5). Detailed views of the planned and as
currently constructed power conversion chain are shown in Fig. 6. The motions of
the body in roll and pitch (yaw is not allowed) nonlinearly couple into the
heave DOF thus affecting power conversion. A planar motion table (PMT) allowing
the entire device (body plus power conversion mechanism) to translate in the
horizontal plane was selected to emulate the mooring systems of most deep water
devices (see ``PMT'' in Fig. 4). The PMT is also selectively controllable such
that the device can be locked in a given x-y location. The restoring force
provided by the PMT will mimic a compliant mooring system and will result in
large natural resonances in surge and sway that are outside of the model-scale
waves.
The sensor suite developed for T3R2 is broad
in nature and will result in a wealth of large scale experimental data. Sensors
have been chosen that allow for real-time control, model validation, and health
monitoring. All motions of the device will be tracked redundantly through
on-board sensors and an external motion tracking system. Force in all the
translational degrees of freedom will be measured. A series of sensors shown in
Fig. 5 will monitor the pressure distribution on one quadrant of the float.
Lastly, impact events (slam) will be recorded with fast-rise pressure sensors
as well as in-house developed slam panels.
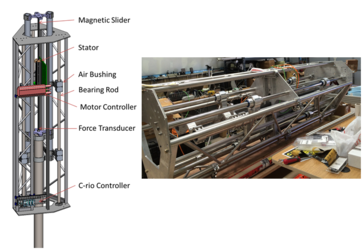 Figure
6. Detailed view of the PCC and as currently
constructed PCC.
Oregon Wave Energy Trust (OWET) Ocean Renewable Energy Conference X,
Portland, Oregon (4/14–17/2015)
Jesse Roberts of Sandia National Laboratories (SNL) attended and
presented at the Oregon Wave Energy Trusts (OWTET) 10th annual Ocean
Renewable Energy Conference in Portland, Oregon. The conference was co-located with
HydroVision International which had over 3,000 attendees from all over the
world. Jesse was part of a special panel with Al Livecchi of the National
Renewable Energy Lab and Simon Geerlofs of Pacific Northwest National Lab. The
panel introduced mechanisms for Industry and National Lab engagement with focus
on the newly launched Small Business Voucher (SBV) pilot program. The SBV pilot
program will give small, clean-energy companies access to national lab
expertise and resources to help small businesses overcome the technical
challenges that hinder their technical and economic growth. Although the SBV program crosses over many
renewable energy areas, this panel focused on marine renewable energy. After
the introduction of the SBV program, each Lab representative provided a brief
overview of the marine hydrokinetic (MHK) projects and capabilities performed
within their respective water power departments. The remainder of the panel
session was spent addressing audience questions about the SBV program and
Laboratory capabilities. There was quite
a bit of excitement from those present about the new SBV program. It was quite
clear that the SBV program will provide the most direct mechanism to date for
industry-national laboratory collaboration.
Jesse Roberts, (505) 844-5730.
|