 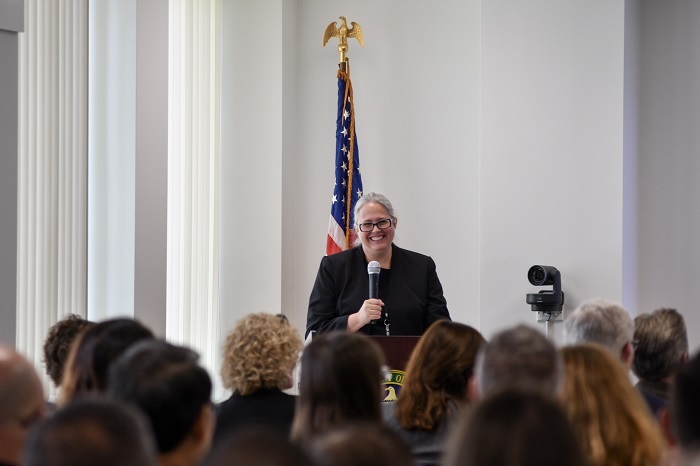 U.S Department of Energy Office of Environmental Management Senior Advisor Candice Robertson addresses employees and answers questions at Oak Ridge Office of Environmental Management’s all-hands meeting. It was her first trip to the site since being named head of the cleanup program in June.
OAK RIDGE, Tenn. – Major themes of growing partnerships and continued progress came into focus during a visit to Oak Ridge by U.S. Department of Energy Office of Environmental Management (EM) Senior Advisor Candice Robertson — her first trip to the site since becoming head of the cleanup program in June.
Roberston’s brimming agenda included visiting teams from DOE programs, contractors, stakeholders, higher education institutions and others supporting and benefiting from the Oak Ridge Office of Environmental Management’s (OREM) cleanup mission.
She kicked off the visit with remarks at the Nuclear Opportunities Workshop in Knoxville, Tennessee, where hundreds of attendees gathered to hear about industry developments, business opportunities and advancements in research and technologies.
Excitement and optimism were on display at the event with a growing number of companies in the nuclear industry expressing interest and locating on land OREM has cleaned and transferred to the community for economic development.
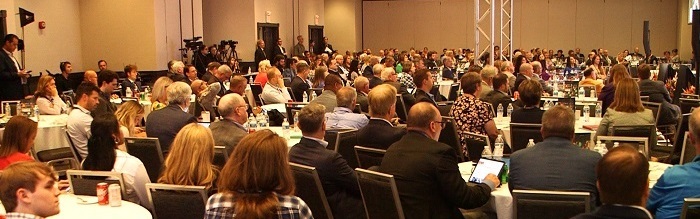 More than 600 attendees gathered at this year’s Nuclear Opportunities Workshop to hear news and perspective from top leaders in the nuclear field, including U.S Department of Energy Office of Environmental Management Senior Advisor Candice Robertson.
On the following day, Robertson made multiple stops at major cleanup projects across the Oak Ridge Reservation.
At the Y-12 National Security Complex, EM’s top official observed construction underway on the Mercury Treatment Facility and the final stages of deactivation at Alpha-2. Demolition of the 325,000-square-foot former Manhattan Project enrichment facility, an EM 2024 priority, is scheduled to begin this fall.
She also viewed OREM’s current and future disposal sites. The EM Waste Management Facility is nearing full capacity, and fieldwork is underway on a new facility that provides the capacity needed to complete future cleanup.
Robertson also traveled to Oak Ridge National Laboratory (ORNL), where she got a firsthand look at ongoing deactivation projects at former reactors and isotope labs. These projects are paving the way for demolitions that will transform the central campus and support future modernization at the site.
She also visited the Uranium-233 Disposition Project at ORNL, where employees have already surpassed a processing goal among EM’s 2024 priorities.
The final day of her trip began with a message to community and business leaders at the East Tennessee Economic Council.
Robertson discussed how progress in Oak Ridge would not be possible without partnerships with the community and business leaders in the room as well as the workforce, labor organizations, regulators and Congress.
In her remarks, the head of EM also discussed factors critical to future success.
“One of my top priorities is maintaining a world-class workforce here in Tennessee, and across what is the world’s largest environmental cleanup program,” said Robertson. “We can’t do anything without the right people and without the next generation of leaders. And with over 90% of cleanup work executed by contractors, having the best of private industry on the job, at the right time and at a fair price, is critical.”
That focus was evident in her final meeting of the trip with leadership from the University of Tennessee, Tennessee Tech University, Roane State Community College, Pellissippi State Community College and the Oak Ridge school district.
Together, they discussed how their schools are launching and expanding programs that are helping train and educate the future federal and contractor workforce that will push the EM mission forward.
For more about Robertson’s visit and an exclusive full one-on-one interview, watch the next episode of Energycast that airs on OREM’s YouTube channel on Aug. 28.
-Contributor: Ben Williams
 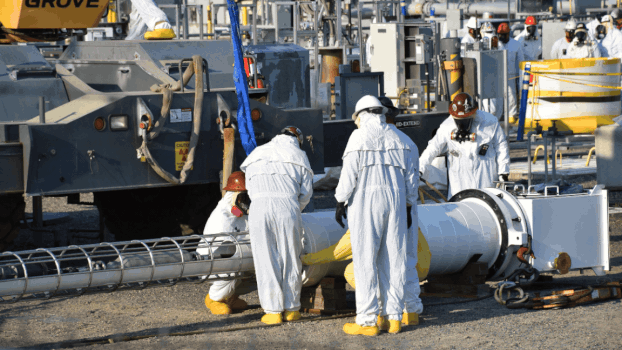 The pump mast for the Test Bed Initiative Demonstration project has an integrated ion exchange column to pretreat waste at the Hanford Site, preparing it for grouting.
RICHLAND, Wash. — Hanford Site workers are installing equipment to demonstrate how an alternative treatment technology could safely accelerate cleanup of radioactive tank waste.
The Test Bed Initiative (TBI) Demonstration will treat approximately 2,000 gallons of tank waste and ship it to commercially licensed facilities in Texas and Utah that will immobilize it in grout and dispose of it.
“The TBI Demonstration does not impact our preparations to immobilize tank waste in glass and supports the Department’s goal to consider additional options for safely and efficiently treating low-activity waste at the site,” said Brian Vance, the U.S. Department of Energy (DOE) Office of Environmental Management top manager at Hanford.
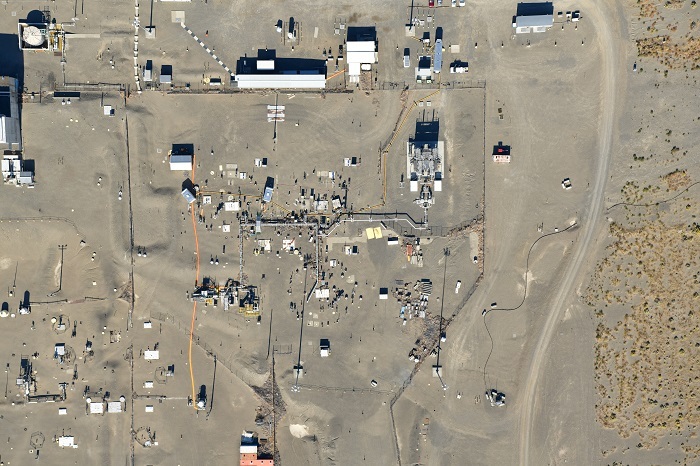 The Test Bed Initiative Demonstration project will pretreat waste in Tank SY-101 in the 200 West Area at the Hanford Site.
DOE and its contractor, Washington River Protection Solutions, are installing a control room, shipping totes and other equipment to begin the TBI Demonstration. Workers will install and test the equipment through September, with treatment operations set to take place by the end of the year. The Department plans to ship the treated waste in fiscal year 2025 after laboratory testing ensures it meets requirements.
Using this approach will safely treat low-activity waste from Hanford tanks and dispose of it outside Washington state in a manner that would reduce risks to workers, the public and the environment consistent with industry standards.
The TBI Demonstration is consistent with recommendations from the National Academy of Sciences to address potential barriers and to consider more modular capabilities as the Department ramps up the Hanford tank waste mission.
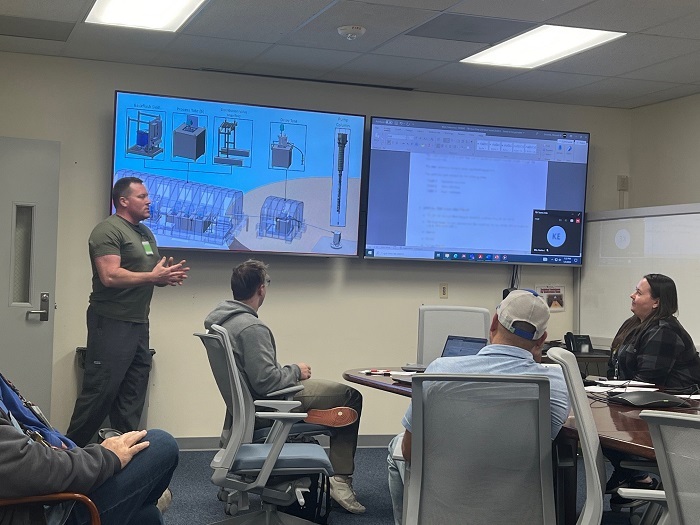 Doug Kennedy, Tank Farm Projects engineer, explains the Test Bed Initiative Demonstration project to craft workers and riggers during a meeting in January 2024.
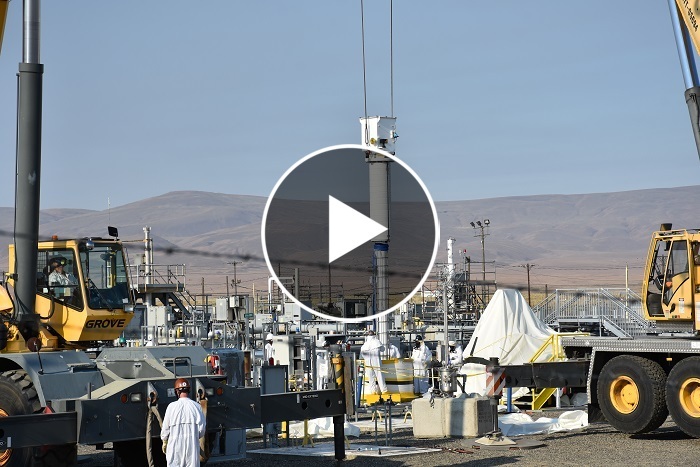 EMTV: Watch this video on the installation of equipment to support the Test Bed Initiative Demonstration project in SY Farm.
The demonstration expands on previous treatment of three gallons of waste for offsite grouting, demonstrating the ability to treat some of Hanford’s low-activity waste using commercial, licensed, permitted facilities.
The Washington State Department of Ecology issued a research, development and demonstration permit for construction to begin July 18. Any proposal to treat, stabilize and dispose offsite of more than the 2,000 gallons would be evaluated in separate regulatory reviews and evaluations.
You can learn more about the system and demonstration project here.
 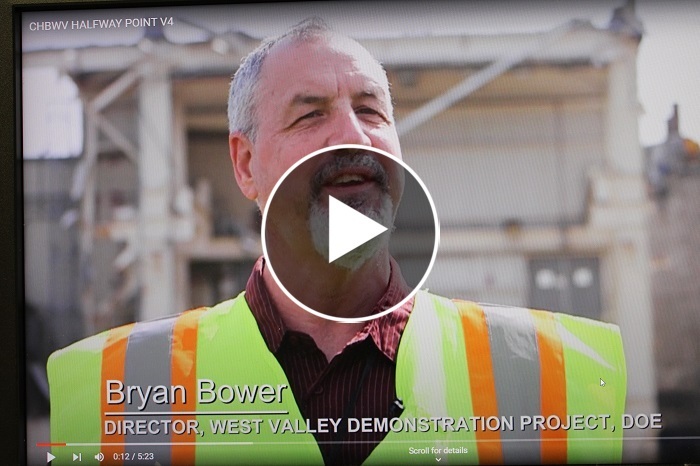 West Valley Demonstration Project Director Bryan Bower appears in the latest Main Plant Process Building demolition video to thank employees for their hard work in reaching the project’s 50% completion mark.
WEST VALLEY, N.Y. — A new video released today by the West Valley Demonstration Project (WVDP) captures cleanup progress by the U.S. Department of Energy Office of Environmental Management (EM) and its contractor as they highlight the halfway point in the demolition of the Main Plant Process Building.
The video features subject matter experts from EM and contractor CH2M HILL BWXT West Valley (CHBWV) with more than 200 years of combined experience in nuclear decommissioning and environmental cleanup.
“The purpose of this video is to thank every employee here and commend them for their safety and compliance with local, state and federal regulations while performing this work,” WVDP Director Bryan Bower said. “It all started 20 years ago with the deactivation and decontamination of the Main Plant. Dedicated men and women went room by room and removed contaminated piping and equipment to help get us where we are today. This is truly an incredible workforce.”
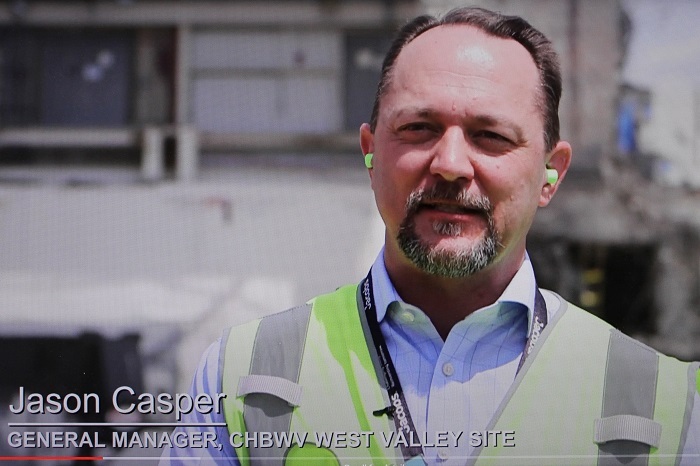 Jason Casper, CH2M HILL BWXT West Valley president, recognizes the efforts of the workforce in reaching the 50% completion milestone in the safe demolition of the Main Plant Process Building.
The Main Plant is one of the most difficult facilities to be removed from the site. Some employees have worked their entire careers in the building, supporting operations, deactivation, and now demolition. The building’s successful deconstruction will further reduce environmental risks and position the site for the next phase in cleanup. The demolition is expected to be completed in fiscal year 2025, which begins this October.
The video features subject matter experts who provide technical support and oversight to ensure work is performed safely.
“We have excellent craft and skilled workers at the site,” said Stephen Bousquet, WVDP assistant director of the Office of Project Management. “They work hard every day to ensure that the work done here is protective of the public and environment.”
EM’s planned approach to safely deconstruct the Main Plain incorporates best practices and lessons learned from WVDP and the greater DOE complex. It includes use of deliberately planned and sequenced demolition, implementation of robust work controls and use of specialized tools and techniques.
“The engineering and planning for this project was extremely detailed and comprehensive so we could execute this work safely at a deliberate speed,” CHBWV President Jason Casper said. “This is a spectacular group of people performing this work. It’s truly been a team effort among EM, CHBWV, union workers and subcontractors.”
-Contributor: Joseph Pillittere
AIKEN, S.C. — A successful U.S. Department of Energy Office of Environmental Management (EM) collaboration is advancing progress toward processing non-aluminum spent nuclear fuel (NASNF) at the Savannah River Site (SRS).
Environmental Management Operations personnel at SRS have partnered with Savannah River National Laboratory (SRNL) as part of the Accelerated Basin De-inventory (ABD) mission.
Spent nuclear fuel stored in the site’s underwater storage basin, called L Basin, is either covered, or clad, in aluminum or a combination of zirconium and stainless steel, commonly referred to as NASNF.
To process all remaining spent nuclear fuel in L Basin, which is the goal of the ABD mission, the collaborative team has created the first set of NASNF dissolution flowsheets, which serve as recipes for processing the atypical fuel elements. The flowsheets specify things such as chemical amounts, temperatures and how the material flows through the process.
“Having this first set of plans for processing a portion of the NASNF is a huge accomplishment, taking several years of technology development at SRNL,” said James Therrell, Nuclear Materials Program manager for EM contractor Savannah River Nuclear Solutions.
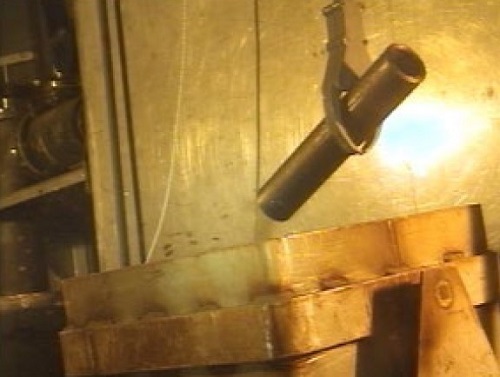 |
|
A view of a non-aluminum spent nuclear fuel element. |
Therrell noted that almost 400 NASNF bundles safely stored in L Basin need to be processed for permanent disposal in the coming years.
“With SRNL’s help, SRNS was able to select the first group of NASNF that can be safely processed in the H Canyon chemical separations facility at SRS,” he said. “This material will eventually be stabilized in a glass form by the site’s liquid waste contractor. We also have set up the rest of the program for success by establishing plans for ongoing technology development to deal with the remaining NASNF.”
The makeup of the roughly 400 NASNF bundles varies in content, size and composition, making some of the fuel more challenging to dissolve. Each different type of fuel requires specific flowsheets due to safety requirements.
The site will use an electrolytic dissolver to process the first set of NASNF. While the aluminum-clad spent nuclear fuel can be chemically dissolved, a relatively easy process involving heating nitric acid to dissolve the aluminum, the zirconium- and stainless-steel-clad fuel is more challenging and must be electrolytically dissolved, adding electricity to the nitric acid dissolution process.
SRNL performed experiments to overcome challenges for that work, and SRNS developed strategies to prepare the fuel for use in the dissolver.
“SRNL has spent years evaluating and tackling the challenges of processing NASNF,” said Tam Truong, SRNL researcher. “We have conducted electrolytic dissolution experiments and leveraged processing knowledge and experience to develop the dissolution parameters for the first group of NASNF.”
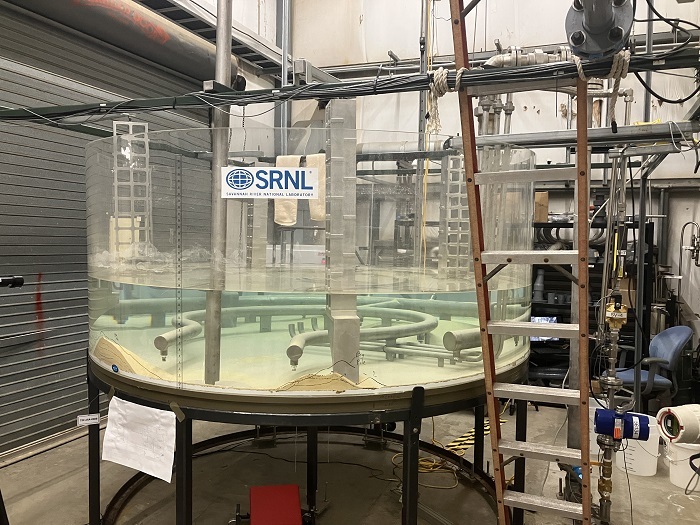 The mock-up Dissolver Solids Removal System at Savannah River National Laboratory was used to demonstrate a full-scale jet cleanout system to remove undissolved material from the H Canyon electrolytic dissolver, one of the challenges faced for non-aluminum spent nuclear fuel processing.
Truong continued, “As the process can generate insoluble or undissolved material, we have demonstrated a full-scale jet cleanout system to remove the undissolved material, allowing further dissolution to continue. The ongoing complementary collaboration between SRNL and SRNS strengthens our processing capabilities.”
Therrell concurred, saying, “SRNL developed an impressive residue cleanout prototype that has provided the essential data to allow the processing facilities to finalize equipment designs.”
An electrolytic dissolver at H Canyon can support NASNF missions in addition to H Canyon’s standard chemical dissolution capability.
The origin of most NASNF is from historic test reactors, including one from SRS.
“One of the intriguing aspects of this program is the historical significance of what these unique fuels provided to our country with regards to reactor designs and understanding,” Therrell said. “It feels good to be a part of a team that can help close the loop on these efforts.”
The ABD mission at SRS provides a path for spent nuclear fuel stored in L Basin to be chemically or electrolytically dissolved in H Canyon, and then disposed of through the SRS liquid waste system.
“The collaboration between SRNS and SRNL to make significant progress on a challenging effort is another example of SRS using it’s unique resources to help make the world safer,” said Therrell.
-Contributor: Lindsey MonBarren
LOS ALAMOS, N.M. — Environmental sampling efforts and how they inform cleanup decisions was the key topic of discussion at a recent Environmental Management Cleanup Forum in Los Alamos.
The U.S. Department of Energy Environmental Management Los Alamos Field Office (EM-LA) and Newport News Nuclear BWXT Los Alamos (N3B) host the forums as part of a commitment to keep stakeholders and the community informed on the Los Alamos National Laboratory (LANL) legacy cleanup.
The forum was also an opportunity for new EM-LA Manager Jessica Kunkle to introduce herself to the public. Kunkle shared her desire to maintain strong engagement with stakeholders, pueblos and local communities. EM-LA Deputy Manager Ellie Gilbertson provided an update on some EM-LA top priorities, including the Hexavalent Chromium Project Expert Technical Review and EM-LA Strategic Vision.
N3B Environmental Remediation Program Manager Troy Thomson discussed how N3B conducts a robust sampling program to identify the nature and extent of the contamination, determine its risk, adhere to federal and state standards, and receive the regulatory approval to remediate, if necessary. Thomson highlighted how the program helps verify the effectiveness of legacy waste cleanup operations at LANL.
Thomson covered the process N3B takes to sample groundwater and surface water, soils and known disposal sites for legacy contaminants of concern and their sources. Groundwater monitoring locations include springs and regional aquifer wells, which can be up to 1,200 feet deep.
|
The low-head weir pictured is one of many stormwater controls that help prevent contaminated sediment from being transported downstream. Other types of controls include berms, detention basins and grade-control structures. All are included in an annual maintenance and inspection program. |
|
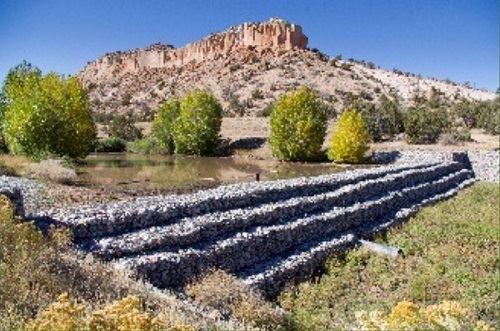 |
Thomson also provided examples of stormwater run-on and runoff controls, such as earthen and rock berms, and riprap, which is rocky material to prevent erosion. N3B samples soil and stormwater in canyons and watersheds across LANL. Currently, 193 stormwater sample sites are monitored.
From May 2018 to June 2024, N3B collected 22,770 water samples; 15,549 soil and sediment samples; and 3,879 vapor samples. All sampling data is available through the IntellusNM public portal. Documents and reports for the LANL legacy cleanup are located in EM-LA’s Electronic Public Reading Room.
Following Thomson’s presentation, the floor was opened to all attendees, both in person and virtually, for questions and comments on sampling and other topics on the legacy cleanup.
The next forum is set to take place this fall.
-Contributors: Stephanie Gallagher, Elicia Sacco-Williams
 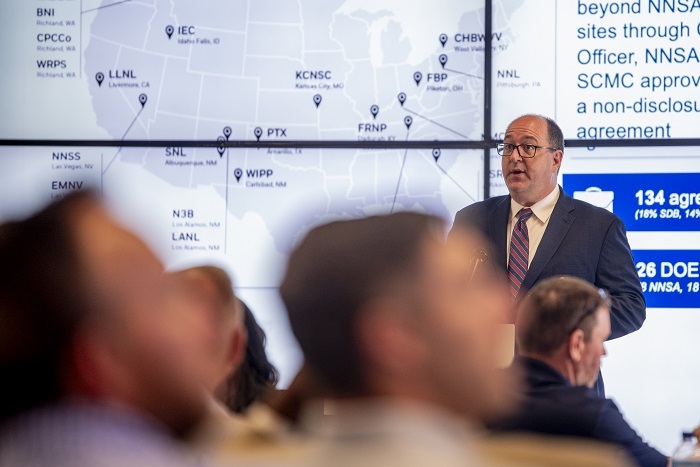 U.S. Department of Energy Supply Chain Management Center Principal Customer Programs Leader John O’Connell speaks to representatives of small businesses at a workshop in Paducah, Kentucky.
PADUCAH, Ky. — A U.S. Department of Energy (DOE) center demonstrated its commitment to empowering small businesses at a recent workshop in collaboration with the DOE Office of Environmental Management (EM) Portsmouth/Paducah Project Office (PPPO) and a Paducah Site contractor.
With nearly 90 people attending, the workshop focused on the Supply Chain Management Center (SCMC) mission to foster partnerships benefiting local businesses and enhance the resilience of the supply chain across the DOE complex. The center is dedicated to simplifying the buying process to enable savings for EM and National Nuclear Security Administration prime contractors.
"We recognize the invaluable role small businesses play in driving innovation and ensuring a strong supply chain. Through partnerships and workshops like these, DOE continues to reach out to small businesses to provide new opportunities to participate and contribute to our mission," PPPO Manager Joel Bradburne said.
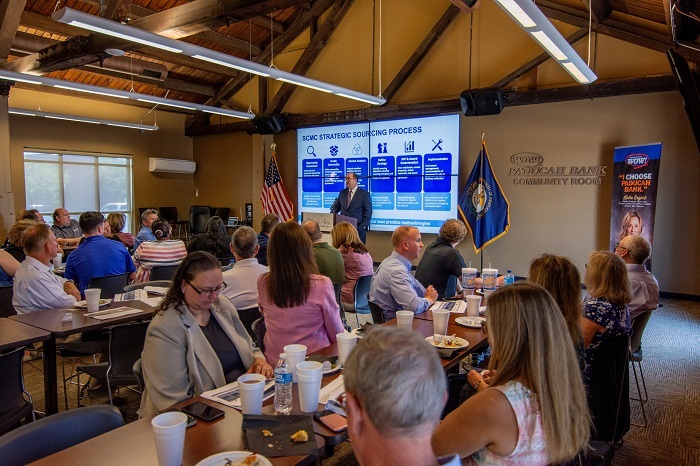 Representatives of nearly 90 small businesses, including industrial suppliers, staffing agencies and commercial contractors, take part in an event with U.S. Department of Energy Supply Chain Management Center Principal Customer Programs Leader John O’Connell in Paducah, Kentucky.
Held in Paducah, the event provided small businesses with insights to participate in DOE's supply chain. Attendees gained practical knowledge about navigating government contracts with SCMC and networked with employees of DOE and Four Rivers Nuclear Partnership (FRNP), the EM Paducah Site deactivation and remediation contractor.
The center’s work with small businesses results in savings for DOE sites across the complex. At the Paducah Site, FRNP exceeded a fiscal year 2024 goal of $600,000 in cost savings working with vendors that have SCMC agreements.
Participants praised the workshop for its educational format and the networking opportunities it provided. By bridging the gap between small businesses and procurement processes, the SCMC continues to strengthen the competitiveness of local enterprises.
“The Paducah business community appreciates DOE and FRNP’s commitment to growing local business through events like the SCMC workshop,” said Steve Hawkins with Hannan Supply of Paducah. “The information shared at the workshop provided insight on opportunities that exist at the DOE Paducah Site to expand what businesses like ours can offer.”
The Paducah Site and FRNP remain committed to expanding outreach to small businesses, aiming to create a more competitive supply chain ecosystem benefiting businesses, communities and the nation as a whole.
-Contributor: Dylan Nichols
 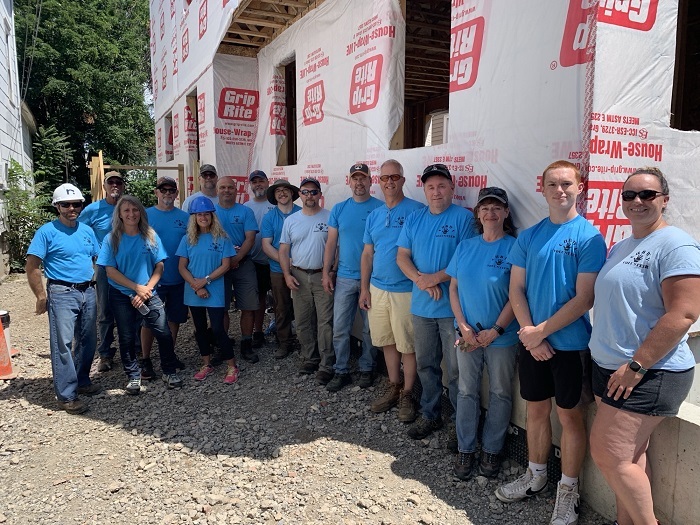 West Valley Demonstration Project team members and members of their families stand in front of a new house being built for a family in need. The dwelling is part of Habitat for Humanity Buffalo’s mission to provide affordable homeownership to low-income families in Buffalo’s surrounding area. From left: Joseph Pillittere, Neil Armknecht, Michelle Schweickert, Darren Boone, Elizabeth Lowes, Kevin Murray, Dave Malecki, Rob Davis, Kyler Casper, Jason Casper, Keith Koralewski, Tom Dogal, Dave Loop, Peggy Loop, Ethan Martinet and Dustee Martinet.
WEST VALLEY, N.Y. — Volunteers from the West Valley Demonstration Project (WVDP) recently worked with Habitat for Humanity Buffalo to build a new house in downtown Buffalo, New York.
"Volunteers help provide the light at the end of the tunnel many families don't think is possible when it comes to having a safe home,” said DJ Manou, volunteer manager with Habitat for Humanity Buffalo. “Your help building these homes allows us to make that a reality."
On a day off from work at WVDP, employees with the U.S. Department of Energy Office of Environmental Management (EM) and cleanup contractor CH2M HILL BWXT West Valley (CHBWV) rolled up their sleeves to help install hurricane straps and build roof gables for the new three-bedroom house.
“Today’s success speaks volumes to the generosity and kindness of our employees,” said Robert Davis, WVDP administrative officer. “This clearly demonstrates the commitment our employees have for their community and the positive impact that kindness can have on a community.”
Over the years, EM and CHBWV employees at WVDP have helped people in need, including Day of Caring activities, annual food drives, Toys For Tots campaigns and volunteer opportunities with other nonprofit organizations.
Ask CHBWV President and General Manager Jason Casper about volunteering, and he'll tell you it’s all about helping people and building communities.
“It is a privilege and a pleasure to be a part of an event that makes a difference in our community,” Casper said. “I am also grateful that our employees, who work hard all week, would give a day’s worth of their free time for such a worthy cause.”
For more than 30 years, Habitat for Humanity Buffalo has worked to build strength, stability and self-reliance through homeownership. Established by volunteers concerned about the lack of affordable homes in Buffalo, the organization has constructed more than 300 houses in the city. Nearly two-thirds of its projects have taken place at houses donated to the organization or purchased at a low cost.
-Contributor: Joseph Pillittere
 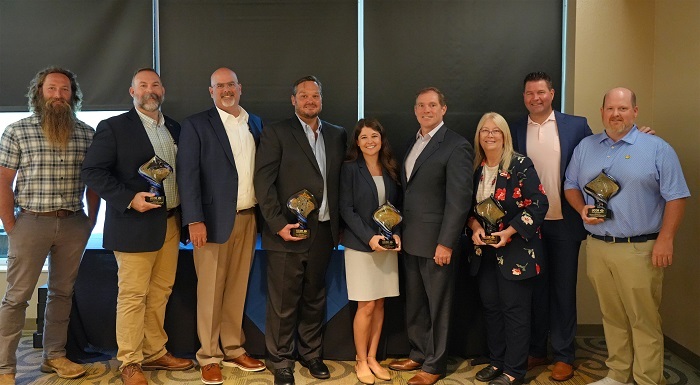 Oak Ridge cleanup contractor UCOR recognized six small businesses at a recent annual awards ceremony. Representatives from the winning businesses include, from left: David Stevens and Nick Trzcinski from Aleut Demolition Services; Mark Morgan and Mike Lamon from CTI and Associates; Olivia Rockett and Chad Drummond from Drummond Carpenter; Rebecca Barr from Barr Technical Services; and James Luby and Jason Watson from Premier Contracting and Technical Services.
OAK RIDGE, Tenn. — Oak Ridge Office of Environmental Management (OREM) cleanup contractor UCOR recently recognized six small businesses for their critical support to the U.S. Department of Energy Office of Environmental Management (EM) cleanup mission.
“Small businesses are often the unsung heroes behind our progress,” OREM Small Business Program Manager Carol Jennings said. “They provide important services that help us complete projects on schedule and on budget, and they share ownership in our successes.”
Since UCOR began its current contract with OREM in 2022, it has far exceeded DOE’s goal to award 45% of subcontracting dollars to small businesses. During that period, the company awarded 85% of its subcontracted work, totaling $559 million, to small businesses.
Each recipient at this year’s event was recognized as a valued partner, especially for outstanding customer service and exceptional responsiveness in supporting cleanup work across DOE’s Oak Ridge Reservation.
Partnerships with subcontractors have enabled UCOR to advance cleanup and several key projects at the Y-12 National Security Complex (Y-12) and Oak Ridge National Laboratory (ORNL).
One of the most impressive examples is CTI & Associates. UCOR subcontracted the company to perform early site preparation for the Environmental Management Disposal Facility, a key piece of infrastructure vital for future cleanup. CTI & Associates helped complete that work $10 million under budget and six months ahead of schedule.
UCOR President and CEO Ken Rueter told attendees what they do makes a difference to the cleanup mission.
“Everyone in this room has demonstrated time and time again your commitment to excellent performance, to partnership with us, and to safety,” Rueter said.
UCOR’s awards for top performance and the small businesses that received them this year are:
-
Small Business of the Year: CTI and Associates, an Oak Ridge-based environmental consulting and engineering firm, has evolved from geotechnical engineering to a full-service contractor.
-
Small Disadvantaged Business of the Year: Aleut Demolition Services, based in Oak Ridge, specializes in site preparation and secure construction services, including radioactive and hazardous structures.
-
HUBZone Small Business of the Year: Impres Technology Solutions, based in Round Rock, Texas, provides technology services, including cybersecurity, storage and networking, cloud solutions, and information technology modernization. A HUBZone is a historically underutilized business zone.
-
Woman-Owned Small Business of the Year: Barr Technical Services, based in Oak Ridge, supports the procurement of goods and services. The company offers business management and support services to government and commercial entities.
-
Veteran-Owned Small Business of the Year: Drummond Carpenter, headquartered in Orlando, Florida, provides services in environmental and water resources, engineering and applied research.
-
Service-Disabled, Veteran-Owned Small Business of the Year: Premier Contracting and Technical Services is an Oak Ridge-based business that supplies hard-to-find large equipment as well as industrial and office supplies.
-Contributor: Ryan Getsi
 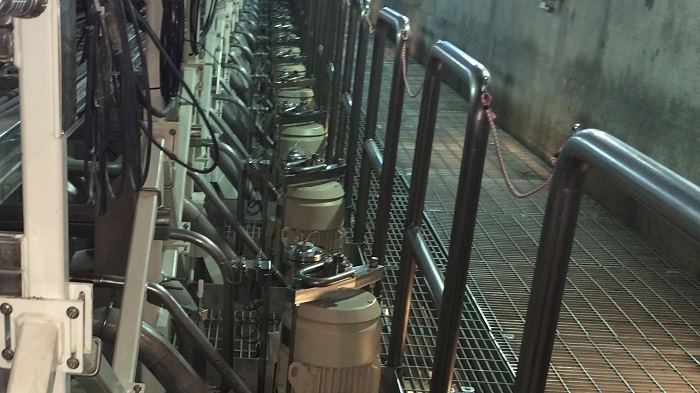 The bank of contactors inside the Salt Waste Processing Facility at Savannah River Site removes radioactive cesium from salt waste. However, the contactors have collected unwanted solids and require frequent chemical cleaning to operate efficiently, resulting in lengthy downtime for the facility. The arrival of 16 new contactors is expected to significantly reduce that downtime and will enable the facility to make extensive run times at higher flow rates.
AIKEN, S.C. — The U.S. Department of Energy (DOE) Office of Environmental Management (EM) has received a shipment of replacement centrifugal contactors for the Salt Waste Processing Facility (SWPF) at Savannah River Site (SRS), which should increase production at the facility by reducing the amount of downtime for maintenance.
The specially engineered contactors are used to remove radioactive cesium from the liquid salt waste stored in underground, carbon-steel tanks at SRS.
By purchasing 16 spare contactors, Savannah River Mission Completion (SRMC), the SRS liquid waste contractor, can now change out an entire bank of extraction contactors instead of replacing individual contactors as they show signs of wear. By having the spare bank of contactors, EM has the best opportunity for longer run times at higher flow rates.
Jim Folk, EM’s assistant manager for waste disposition, said the contactors are vital to the success of the SRS liquid waste mission.
“With the arrival of these spare contactors, we expect SWPF will make great strides in the effort to process liquid waste in a timely and safe manner,” Folk said. “Shorter outages will help keep the liquid waste mission on schedule to finish in 2037 to reduce risk to our community, environment and workers.”
The contactors operate in the Central Processing Area of SWPF. A solvent is fed to one end of a bank of centrifugal contactors while the waste is fed to the other end in a counter-current flow.
The solvent extracts the cesium, with each successive contactor stage extracting more, resulting in a decontaminated salt solution stream and a cesium-laden solvent stream. The solvent stream is stripped of its cesium and washed, and the solvent is reused. The cesium-laden solution, known as strip effluent, is transferred to the Defense Waste Processing Facility to be combined with sludge from the tank farm — a grouping of underground waste tanks — and stabilized through vitrification, or immobilization in glass. The decontaminated salt solution continues through the remainder of the SWPF process and eventually goes to the Saltstone Production Facility, where it is mixed with dry ingredients to form a grout that is pumped into Saltstone Disposal Units for permanent disposal.
SRMC’s Steve Howell, SWPF and End Stream Delivery director, said replacing an entire bank of contactors would previously eliminate a month from the processing schedule because in-service contactors had to be removed, overhauled and then reinstalled during the outage.
"While pauses in processing provide our staff the ability to perform other routine maintenance also, the pauses were considerably longer than we would have liked,” Howell said. “These additional contactors will give us more control over our processing schedule.”
Since coming online in October 2020, SWPF has processed more high-activity liquid waste than the former system processed in 11 years. SRMC’s goal is to improve SWPF’s processing rate so that all liquid waste tanks can be emptied, cleaned and closed by 2037.
-Contributor: Jim Beasley
|