 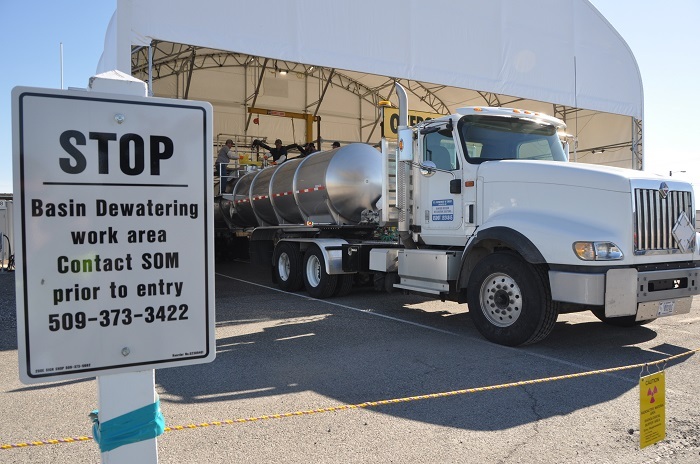 Hanford Site work crews fill the first tanker truck with wastewater from the K West Reactor spent-fuel storage basin in preparation for sending it to the site’s Effluent Treatment Facility for processing.
Removal of contaminated water further protects Columbia River
RICHLAND, Wash. — The U.S. Department of Energy Office of Environmental Management (EM) is draining the last large concrete basin at the Hanford Site that stored reactor fuel rods during the World War II and Cold War era plutonium production mission.
Workers are pumping out contaminated water from the 1.2-million-gallon basin in the K West Reactor and hauling it by tanker truck to a nearby treatment facility. Completing this project will further enhance the protection of groundwater and the Columbia River as the cleanup effort at Hanford progresses.
“Getting the contaminated water out of this basin is a key step in our risk-reduction mission,” said Andy Wiborg, EM’s acting deputy assistant manager for River and Plateau cleanup. “This effort will eliminate the risk of a leak of contaminated water to the groundwater about a quarter-mile from the Columbia River.”
The K West Reactor and nearby K East Reactor were built in the 1950s and operated through the early 1970s to irradiate uranium fuel rods for chemical processing to produce plutonium. The basins in both reactors also stored irradiated, or spent, fuel from the last operating nuclear reactor at Hanford, N Reactor.
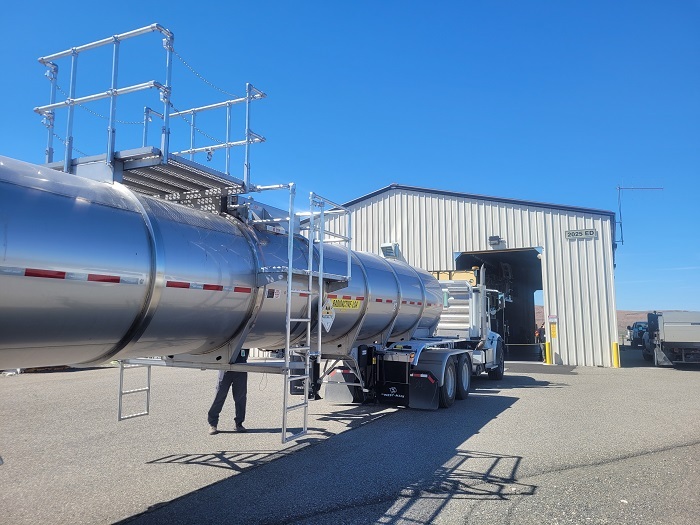 The first tanker truck filled with wastewater from the K West Reactor spent-fuel storage basin arrives at the Hanford Site’s Effluent Treatment Facility for processing.
The Hanford team will drain the basin and stabilize it with grout for future demolition. Teamwork among Hanford contractors is a key factor in the ongoing success of the project.
EM contractor Central Plateau Cleanup Company (CPCCo) is leading the project and has filled more than 60 tanker trucks to date holding about 8,000 gallons each. Contractor Hanford Mission Integration Solutions is driving them to an onsite treatment facility. Washington River Protections Solutions will process the wastewater at Hanford’s Effluent Treatment Facility to remove contaminants for disposal in lined, engineered trenches.
“The collaboration between Hanford contractors reinforces the value of our One Hanford approach, with everyone working together to keep the cleanup mission moving forward,” said Wiborg.
The K West Reactor basin is 125 feet long and 65 feet wide and was filled with 16 feet of water when operating. The water cooled the uranium fuel pushed out of the reactor core and shielded workers from radiation as they stood above on grates to move the fuel into storage bins.
To prepare the basin for draining, cleanup workers stood on those same grates and used long-handled tools to move radioactive equipment and debris into underwater bins and steel tubes. The debris included canisters that held spent fuel, canister racks, pumps, hoses, hand tools, construction materials, and components of a water treatment system.
“The work by multiple teams to characterize, sort and stage debris in the basin has made it possible for us to begin to remove the water and prepare for grouting the basin,” said CPCCo’s Mike Kruzic, who manages closure projects at the reactor area. “It is also great to see the teamwork between three Hanford contractors committed to advancing this risk-reduction project."
  Brian Malone, left, and Chris Rachford Jr. use an aerial lift to remove asbestos pipe insulation from piping once used to support uranium enrichment in the X-333 Process Building at the Portsmouth Site. Approximately 6.5 miles of asbestos pipe insulation need to be removed throughout the facility.
PIKE COUNTY, Ohio — U.S. Department of Energy Office of Environmental Management (EM) crews at the Portsmouth Site relied on detailed planning, collaboration and teamwork to successfully complete characterization activities in the X-333 Process Building, which is slated for demolition early next year.
The characterization included approximately 134,000 measurements, analyses and documentation of all equipment components, piping and valves that could contain uranium deposits at X-333.
X-333 is one of two remaining large process buildings with 65 acres of floor space, formerly used for uranium enrichment at the Portsmouth Gaseous Diffusion Plant. It was the first process building in the cascade of facilities used for enriching uranium and contained the largest process gas equipment onsite.
Fluor-BWXT Portsmouth (FBP), the deactivation and demolition contractor at the Portsmouth Site, assigned nearly 90 employees to the Portsmouth Non-destructive Assay/Characterization Criticality Incredible (NDA/CCI) team. Non-destructive assay entailed measuring the quantities of uranium deposits that remained from enrichment operations in dozens of miles of process pipes.
While characterizing X-333, the team used a unique aid to attain precise data.
“The team incorporated a multi-step verification process to ensure all the information was as accurate as possible,” Portsmouth Site Lead Jeremy Davis said. “Their progress in the X-333 Process Building is appreciated and does not go unnoticed.”
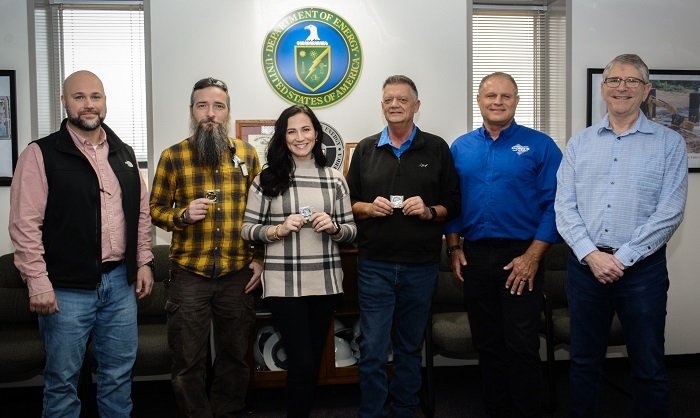 Portsmouth Site Lead Jeremy Davis and Safety System Oversight Engineer Dick Mayer show appreciation to the Portsmouth Non-destructive Assay (NDA)/Characterization Criticality Incredible team leaders for their efforts in characterizing equipment in the X 333 Process Building. From left: Davis, Fluor-BWXT Portsmouth (FBP) Project Support Manager Robert Graves, FBP NDA Deputy Director Amanda DeHart, FBP NDA Director Ricky Walls, FBP Site Project Director Greg Wilkett, and Mayer.
Earlier this year, FBP’s NDA/CCI group was recognized for their efforts in safely and conscientiously characterizing enrichment equipment in X-333.
“It is difficult to build and maintain a program this size that runs smoothly,” EM Portsmouth Site Safety System Oversight Engineer Dick Mayer said. “Safely and correctly completing the work on time can be a challenge. We are fortunate to have one of the best teams around to do the job.”
FBP NDA/CCI Deputy Director Amanda DeHart credits the progress to effective teamwork.
“The NDA/CCI team worked hand in hand with deactivation, nuclear criticality safety and the nuclear safety organizations to safely orchestrate the successful deactivation and characterization efforts,” DeHart said. “Collectively, the improvements resulted in a 90% reduction in measurements required for characterization as opposed to the efforts in the X-326 Process Building.”
The X-333 demolition project is slated to begin in early 2025. It will be the second of three large process buildings to be torn down at Portsmouth. In 2022, EM crews completed the demolition of the X-326 Process Building, marking the most significant cleanup milestone to date at the site.
-Contributor: Michelle Teeters

IDAHO FALLS, Idaho — Members of the U.S. Senate Armed Services Committee (SASC) recently toured the Idaho Nuclear Technology and Engineering Center (INTEC) at the Idaho National Laboratory Site. Pictured from left: U.S. Naval Reactors staff member Erik Anderson; SASC professional staff members Adam Trull and Jonathan Epstein; U.S. Government Accountability Office detailee Julia Coulter; U.S. Department of Energy Office of Environmental Management (EM) Idaho Cleanup Project Site Manager Mark Brown; EM INTEC Programs Assistant Manager Nick Balsmeier; and Naval Reactors Idaho Branch Office Program Management and External Affairs Assistant Manager Chris Henvit.
SIMI VALLEY, Calif. — A new automated pumping system is up and running at the Former Sodium Disposal Facility (FSDF) on the U.S. Department of Energy (DOE) Office of Environmental Management’s (EM) Energy Technology Engineering Center (ETEC) site at the Santa Susana Field Laboratory (SSFL).
Located northwest of Los Angeles, California, SSFL is a 2,850-acre former rocket engine testing and energy research facility. DOE conducted research and development in Area IV, a 290-acre portion of SSFL, and EM is charged with cleanup of residual contamination that remains at the site.
Pumping water manually has taken place at FSDF since 2017 as part of interim cleanup measures “to protect groundwater by capturing and removing contaminated material, keeping it away from the deeper bedrock groundwater,” said Ian Lo, project engineer at the ETEC site.
When ETEC was in use as a nuclear energy and liquid metals research facility in the 1950s through 1980s, test equipment was placed in ponds at FSDF in Area IV for cleaning.
The design, development and installation of the new solar-powered automated system began in 2023 and was completed in May.
“The automation of the [well system] allows for more frequent [and] greater pumping volumes at the site,” Lo said. “Using solar power reduces the site’s energy needs, making it a more sustainable cleanup solution.”
 |
|
Song Chen with U.S. Department of Energy Office of Environmental Management contractor CDM Smith checks the solar skid panel and reviews data on the human-machine interface software used for the automated groundwater interim measures project in Area IV at Santa Susana Field Laboratory. Photo courtesy of Sandra Ramos Hernandez. |
Sandra Ramos Hernandez with U.S. Department of Energy Office of Environmental Management contractor CDM Smith adjusts the control valve for automated groundwater extraction well C-24 in Area IV at Santa Susana Field Laboratory. Photo courtesy of Song Chen. |
|
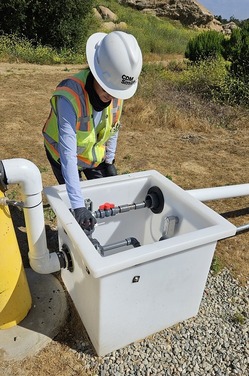 |
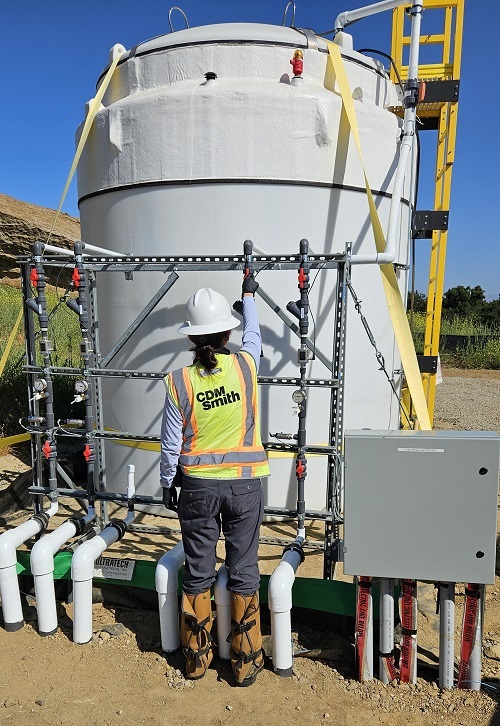 |
|
Sandra Ramos Hernandez with U.S. Department of Energy Office of Environmental Management contractor CDM Smith adjusts the ball valve on piping manifold located at the 5,000-gallon double-walled groundwater storage tank installed as part of the automated groundwater interim measures project in Area IV at Santa Susana Field Laboratory. Photo courtesy of Song Chen. |
The system automatically turns on as the sun rises and turns off when the sun sets, Lo said. It also has remote viewing and data collection capabilities, as well as built-in sensors that will shut it down and alert operators in the event of a system issue.
In the two months since automation began in May, more than 9,700 gallons have been pumped through the system. In comparison, a total of 2,344 gallons were pumped manually from the same four wells between January and March 2024.
“It is exciting to see this new automated groundwater extraction system come online to accelerate the DOE’s cleanup efforts at SSFL,” said Josh Mengers, EM’s federal project director at ETEC. “As we work with the state on final groundwater and soil cleanup plans, we’ll continue to innovate with safety and sustainability in mind, and use the latest science to complete this remediation.”
Since 2017, EM has removed more than 40,000 gallons of contaminated groundwater as part of its remediation work and due to efforts to ensure the site is ready to implement the proposed corrective measures.
In November 2020, DOE published a record of decision for groundwater cleanup at SSFL that describes monitoring and treatment approaches to addressing contaminants and potential areas affected at ETEC, as well as interim actions.
The California Department of Toxic Substances Control (DTSC), which regulates cleanup at the site, released a programmatic environmental impact report in June 2023 highlighting possible impacts of remediating contaminated soil and groundwater at Santa Susana. EM is also working with Boeing and NASA, which are responsible for remediating other portions of the site.
DOE is currently working with the state on final groundwater and soil treatment approaches that will be implemented once final plans have gone through the proper environmental process. After the DTSC approves the final groundwater and soil remediation plans, the next step will be a public comment period.
-Contributor: Melissa Simon
 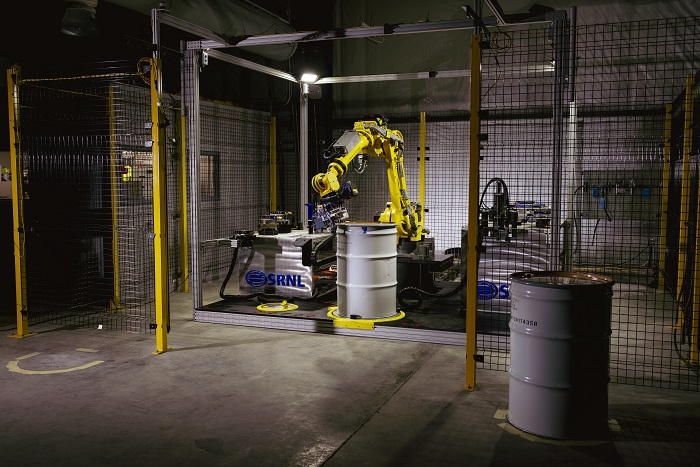 The criticality control overpack drum inspection process will use a robotic arm to perform pre-use inspections and security checks after the drum is delivered to the inspection area by an automated guided vehicle.
AIKEN, S.C. — A U.S. Department of Energy Office of Environmental Management (EM) team at the Savannah River Site (SRS) recently entered the final testing stage of a multi-year project to introduce automation to its mission to downblend surplus plutonium for permanent disposal and remove it from South Carolina, benefiting personnel while saving taxpayer dollars.
The Surplus Plutonium Disposition (SPD) Program mission will expand the existing plutonium dilute-and-dispose process in a plutonium handling and interim storage facility at SRS to support the removal of plutonium from the state.
As part of the mission, the downblended material is packaged in 55-gallon criticality control overpack (CCO) drums and staged on a designated storage pad until it is characterized and ready to be shipped to EM’s Waste Isolation Pilot Plant (WIPP) in New Mexico for disposal.
In 2019, while evaluating potential efficiency improvements to packaging operations, Savannah River Nuclear Solutions (SRNS), the managing and operating contractor at SRS, and the National Nuclear Security Administration (NNSA) identified the benefits of automation. Through NNSA funding, SRNS partnered with Savannah River National Laboratory (SRNL) to assess a long-term strategy for infusing automation into future operations.
“The SRNS-SRNL team determined that automation could be used for the SPD Program — both for receipt and inspection of incoming empty CCOs and for facilitating movements of loaded drums on an interim storage pad, where they are held until shipment to WIPP for disposal,” said Rich Koenig, Advanced Technology Program manager for SRNS.
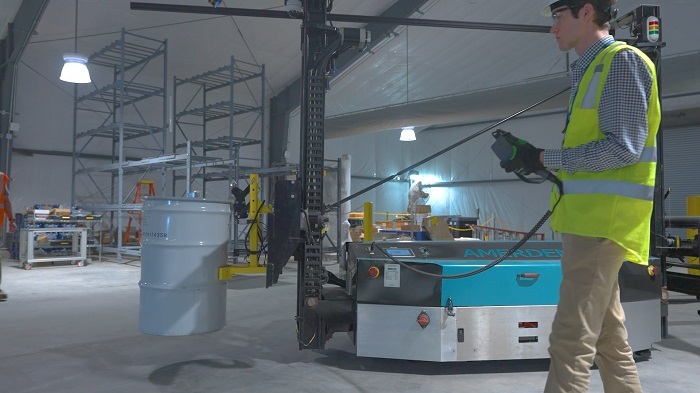 An automated guided vehicle, shown here, will be used to deliver shipping containers between staging and shipping inspection locations in a characterization and storage facility at Savannah River Site.
Koenig explained that automation serves three primary benefits.
“First, it allows SRNS to reassign operators who would normally perform the receipt and inspection tasks to areas where their skills are better utilized,” he said. “The second benefit is the cost savings that will be realized through increased throughput and the reduction in process costs. And the third eventual benefit incorporates ALARA principles by using an automated guided vehicle (AGV) to remove operators from areas with elevated radiological dose.”
ALARA, which stands for As Low As Reasonably Achievable, is a set of principles that seeks to limit worker exposure to radiation as much as possible by limiting the time workers are exposed and providing shielding or alternative work methods, such as automation, to keep workers safe.
“We have tens of thousands of CCOs coming into the plutonium handling and interim storage facility over the next three decades,” said Koenig. “Before diluted plutonium is packaged into the CCOs, they have to be inspected and reviewed before delivery into a security area, ensuring the safety and security of the workers and the materials.”
The CCO inspection process is the first area to use automation within the SPD Program. The process will use a robotic arm to perform pre-use inspections and security checks after the drum is delivered to the inspection area by an AGV. SRNL engineers developed custom tooling and software for the inspection process.
The CCO Characterization and Storage Pad facility at SRS will provide the second automation opportunity, where an AGV will deliver shipping containers between staging and shipping inspection locations. With the addition of a specialized tool on the AGV, drums can be placed in horizontal storage racks to increase the storage capability on the pad by 50% over the current process of storing drums on stacked pallets.
“Using the AGV will allow us to stack drums more safely and efficiently in horizontal positions. Without the AGV, that process would take several operators and a forklift working in a radiological area. By automating the process, we remove the operator from specific work hazards, and we incorporate ALARA principles to reduce radiation exposure, all while greatly expanding our storage capacity,” said Koenig.
With the opportunity to use automation across the U.S. Department of Energy complex, representatives from several EM sites have already visited SRS to learn more.
“This is a really exciting venture for SRS,” said Koenig. “I am looking forward to seeing how automation can benefit operations and processes in the future.”
Plutonium is diluted, or downblended, at SRS in a process that mixes plutonium oxide with a multicomponent adulterant to produce a proliferation-resistant form that can never again be readily used in nuclear weapons.
To view a video highlighting automation, click here.
-Contributor: Lindsey MonBarren
 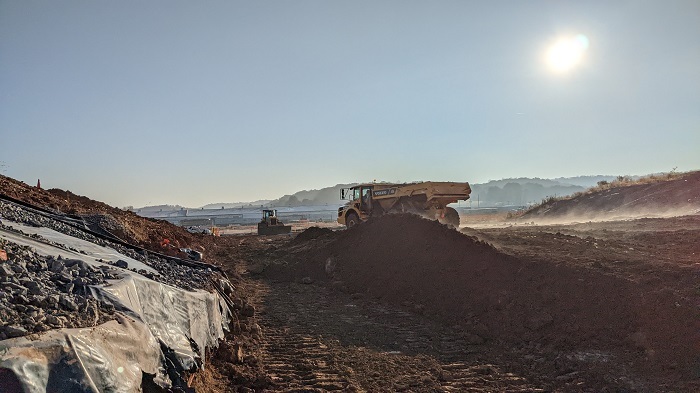 Initial estimates projected approximately 20,000 cubic yards of contaminated soil requiring removal from Exposure Unit-21. That grew to over 103,000 cubic yards as remediation progressed and soil sampling indicated additional excavation would be needed.
Oak Ridge is on track to complete all soil remediation at East Tennessee Technology Park — an EM 2024 priority — in coming weeks
OAK RIDGE, Tenn. — The Oak Ridge Office of Environmental Management (OREM) and contractor UCOR have completed the largest soil remediation at the East Tennessee Technology Park (ETTP).
The three-year-long project removed more than 100,000 cubic yards of contaminated soil, which equates to nearly 8,500 dump truck loads, from the footprint of the massive K-25 building. The mile-long, U-shaped building was demolished in 2013, leaving behind areas of contaminated soil that needed to be addressed.
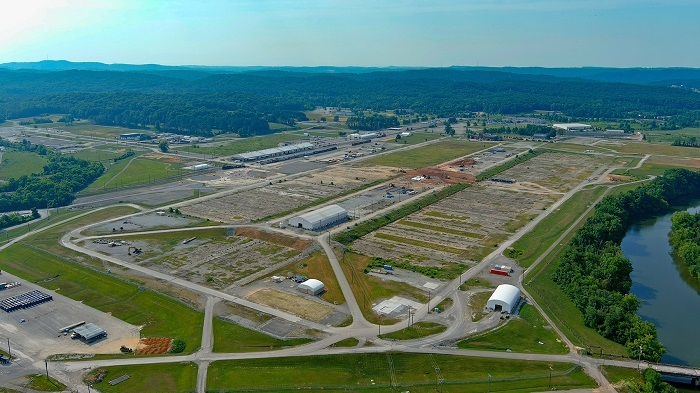 An aerial view of work beginning in the middle of the K-25 Building footprint, known as Exposure Unit-21.
Demolition of K-25, once the largest building in the world, was part of a larger effort to remove an entire uranium enrichment complex. Over the span of that project, OREM removed more than 500 buildings with a combined footprint that could span 225 football fields. That work was completed in 2020.
When major soil remediation began at ETTP in 2018, UCOR divided the site into parcels of differing sizes, called Exposure Units (EU). The largest remediation effort, called EU-21, encompassed the area inside the U shape of the K-25 Building footprint.
“We’ve experienced a lot of challenges during soil remediation, both at EU-21 and all across ETTP,” said Jimmy Hughes, UCOR area project manager. “The amount of soil needing remediation increased significantly from initial estimates, but through smart planning and innovative approaches, we managed to keep the project on schedule.”
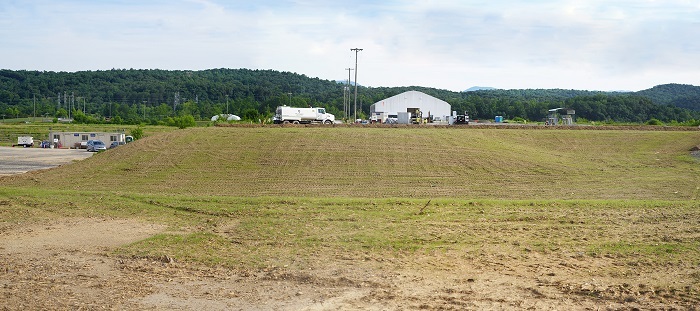 A view of a portion of Exposure Unit-21 after site restoration and reseeding.
Initial estimates projected approximately 20,000 cubic yards requiring removal from EU-21. That grew to over 103,000 cubic yards as remediation progressed and soil sampling indicated additional excavation would be needed.
Across the entire ETTP site, initial estimates indicated that approximately 100,000 cubic yards of soil would need to be excavated — an amount that would eventually rise to more than 470,000 cubic yards.
Some of the approaches that helped keep remediation efforts on track included shipments by rail for some of the waste, implementing efficient methods for loading and transporting excavated soil, and reusing topsoil excavated from other OREM projects for backfill.
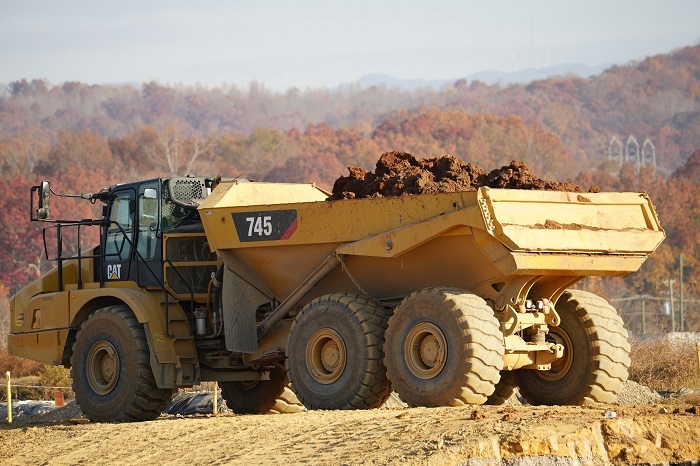 U.S. Department of Energy Office of Environmental Management crews have completed the largest soil remediation project at the East Tennessee Technology Park, excavating more than 100,000 cubic yards of soil from the middle of the K-25 Building footprint. That equates to nearly 8,500 dump truck loads.
Nearly all soil remediation at ETTP is complete. Finishing all soil remediation at ETTP is an EM priority for 2024. UCOR will complete the few remaining tasks in the coming weeks.
“We’ve taken the next big step to complete our cleanup mission at the East Tennessee Technology Park,” said Joanna Hardin, OREM’s ETTP portfolio federal project director. “Finishing soil remediation is a major milestone because it allows us to transfer the remaining parcels of land to the community for beneficial and economic reuse.”
-Contributor: Wayne McKinney

RICHLAND, Wash. — New chemical technologists at the Hanford Site’s 222-S Laboratory, operated by contractor Navarro-ATL, are engaged in a four-month education program. It focuses on learning the importance of safety and compliance when analyzing the physical and chemical characteristics of waste samples. The U.S. Department of Energy Office of Environmental Management and its contractor partners rely on the analysis to safely manage tank waste and to prepare to treat the waste through the Direct-Feed Low-Activity Waste Program. Experienced chemical technologists provide daily individual and small-group training on the job. This hands-on training is followed by a mid-course and final evaluation for the new personnel to demonstrate they have the skills and knowledge required to support the mission.
 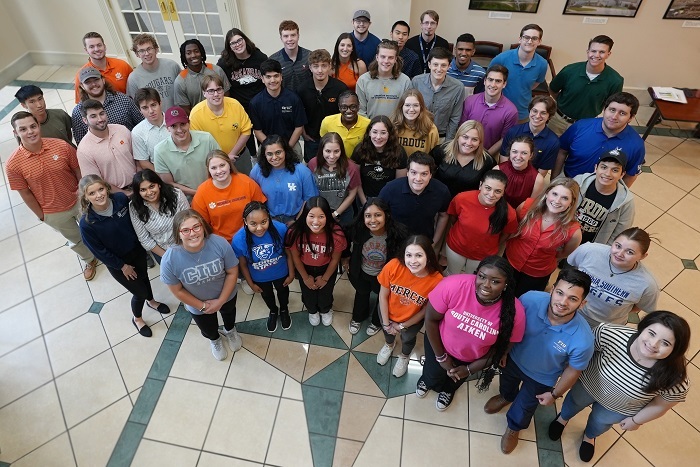 Savannah River Mission Completion (SRMC) has welcomed the largest class of summer interns in the program’s history to the SRMC team.
AIKEN, S.C. — The U.S. Department of Energy Office of Environmental Management (EM) liquid waste contractor at the Savannah River Site (SRS) has welcomed the largest class of interns in the program’s history.
Sixty college students — up from 44 last year — are working within Savannah River Mission Completion (SRMC) this summer, supporting the SRS radioactive liquid waste cleanup mission and bringing fresh perspective in the areas of engineering, environmental science, biology, chemistry, business, communications and more. About a dozen students are returning interns.
The interns hail from Mercer, Brigham Young, University of South Carolina (USC), Clemson, University of Florida, USC Aiken, Georgia Tech, University of Arkansas, University of Georgia, University of Kentucky-Paducah, Georgia Southern, University of Virginia, Purdue, Michigan, Rose-Hulman, University of Kentucky, West Virginia University, Charleston Southern, University of Tampa, Florida International University, Oklahoma State, Columbia International, Georgia State, Benedict College, Augusta University, and Georgia College & State University.
SRMC President and Program Manager Dave Olson said SRMC strives to assign meaningful work and projects to the summer interns while providing the opportunity to be learners first and contributors second.
“These students will be learning alongside some of the best employees who are focused on our mission to safely reduce the risk to the community and the environment of the radioactive liquid waste stored in waste tanks at SRS,” Olson said. “We are thrilled to have them on the team, and we are here to support in many ways, including sharing the standards of our safety culture and core values and behaviors.”
Gabriella Thomas, a business student from USC Aiken, is working in SRMC’S Procurement Compliance and Systems group. She supports the procurement system administration by helping implement new systems, which includes revisions to existing procedures and training that is required resulting from system updates.
“Coming to work every day has been so enjoyable,” Thomas said. “I will use what I’ve learned about the supply chain system and logistical aspects of owning a business and eventually apply it to my own business one day.”
The summer interns have a well-rounded experience planned at SRMC, including professional development sessions, facility tours, technical lectures, community service projects, social outings after hours and senior management networking activities.
-Contributor: Colleen Hart

RICHLAND, Wash. — After practicing in a nonradioactive environment this spring, workers at the Hanford Site recently used a robotic arm to help remove an old 34-foot pump from a large underground tank, called AP-102, that stores radiological and chemical waste. Workers also used a system that encapsulated the pump in a shielding bag as it was removed from the tank, protecting workers from contaminants. U.S. Department of Energy Office of Environmental Management contractor Washington River Protection Solutions regularly removes and replaces aging equipment, but the long pump had small spaces that could trap radiological and chemical tank waste, which required the use of the shielding bag. The tank infrastructure is being upgraded to support the Direct-Feed Low-Activity Waste Program to immobilize tank waste in glass.
|