
This year marks the 10th anniversary of the annual event
ARLINGTON, Va. — U.S. Energy Secretary Jennifer Granholm is scheduled to deliver an in-person keynote address at the 10th Annual National Cleanup Workshop set for Sept. 16-18 this year at the Crystal Gateway Marriott in Arlington, Virginia.
Granholm joins a growing list of federal representatives, industry officials and state and local leaders speaking at this year’s workshop, billed as the premier annual gathering to discuss progress in environmental cleanup of former government weapons sites and nuclear research facilities.
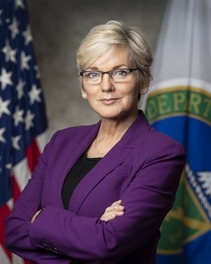 |
|
U.S. Energy Secretary Jennifer Granholm is set to deliver an in-person keynote address at the 10th Annual National Cleanup Workshop this year. |
U.S. Department of Energy Office of Environmental Management (EM) Senior Advisor Candice Robertson will also provide remarks, as well as several other speakers, including:
- U.S. Rep. Chuck Fleischmann of Tennessee, chair, U.S. House Committee on Appropriations Energy and Water Development Subcommittee;
- Jeff Avery, EM principal deputy assistant secretary;
- Greg Sosson, EM associate principal deputy assistant secretary for field operations;
- Kristen Ellis, EM associate principal deputy assistant secretary for regulatory and policy affairs;
- Dae Chung, EM associate principal deputy assistant secretary for corporate services;
- James McConnell, associate principal deputy administrator, National Nuclear Security Administration;
- Brent Gerry, mayor, City of West Richland, Washington, and chair, Energy Communities Alliance (ECA); and
- Rebecca Casper, mayor, City of Idaho Falls, Idaho, and vice-chair, ECA.
Check out the full agenda here, recently released.
The workshop kicks off with a meeting for early career professionals and concludes with the U.S. House Nuclear Cleanup Caucus on Capitol Hill.
Hosted by ECA with the cooperation of the Energy Facility Contractors Group and EM, the workshop brings together more than 750 senior DOE executives, officials from DOE sites, industry leaders, local elected officials and community stakeholders to discuss EM’s progress to address the environmental legacy of the Manhattan Project and Cold War-era U.S. nuclear weapons program.
Click here to register for this year’s workshop.
Check out EM’s coverage of past workshops here:
 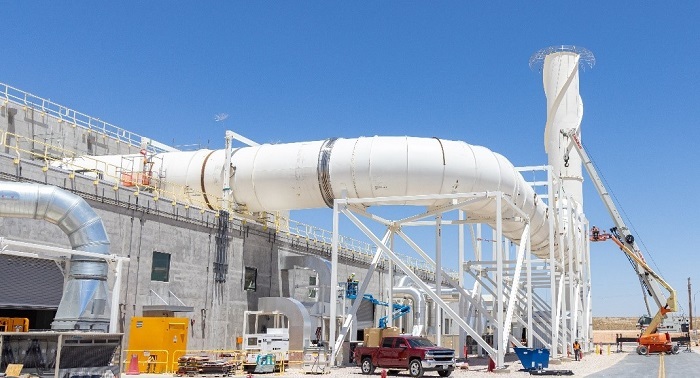 Construction crews put the finishing touches on large ductwork for the new Safety Significant Confinement Ventilation System facility at the Waste Isolation Pilot Plant. With the construction phase complete, testing and commissioning will begin to bring the facility online by summer 2026.
CARLSBAD, N.M. — The U.S. Department of Energy (DOE) Office of Environmental Management (EM) has achieved a significant milestone by completing construction of the Safety Significant Confinement Ventilation System (SSCVS) facility — a new, state-of-the-art, large-scale ventilation system at its Waste Isolation Pilot Plant (WIPP).
This milestone marks the delivery of the SSCVS facilities and systems necessary to move forward with the full testing and commissioning phase to bring the facility online and operational in 2026.
“Finishing the Safety Significant Confinement Ventilation System construction phase marks a momentous investment in WIPP’s operational infrastructure,” said Mark Bollinger, EM’s Carlsbad Field Office manager. “When fully online, the SSCVS will greatly increase the quality of airflow to the underground repository and enhance WIPP’s ability to reliably deliver on DOE’s national security and environmental cleanup missions.”
Salado Isolation Mining Contractors (SIMCO), WIPP’s management and operations contractor, began SSCVS commissioning phase work in early fall 2023 as construction crews began turning over initial portions of the facility and systems to startup and commissioning teams.
“Completing SSCVS construction allows us to pivot our focus to testing and commissioning the remaining SSCVS systems,” said Ken Harrawood, SIMCO’s president and program manager at WIPP. “We will take a measured and methodical — people, plant, paper — approach to safely bring the SSCVS fully online.”
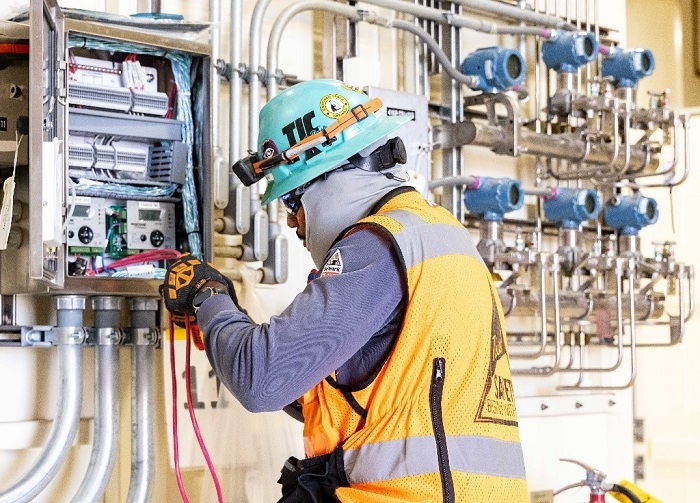 A control panel undergoes testing at the newly constructed Safety Significant Confinement Ventilation System facility at the Waste Isolation Pilot Plant (WIPP). Salado Isolation Mining Contractors, WIPP’s prime management and operations contractor, is testing and commissioning to safely integrate the new ventilation system into daily operations.
Testing and commissioning includes testing systems, integration, developing operational procedures and guidelines, training and qualifying staff. After all testing is completed, the facility is handed over to trained WIPP operations personnel to bring the new facility online. The SSCVS commissioning phase is currently 85% complete.
When fully online, the SSCVS facility will significantly increase airflow through the WIPP underground. Air exiting the underground will be able to pass through a high-efficiency particulate air (HEPA) filtration system made up of 22 filtration units.
How the SSCVS works
The SSCVS will work in tandem with WIPP’s new utility shaft, which will provide a new entry point for air into the WIPP underground repository. The SSCVS pulls air through the repository, removes salt and can send the air through the HEPA filtration units before it’s released to the environment. When fully online, the new ventilation will increase underground airflow from 170,000 cubic feet per minute up to 540,000 cubic feet per minute.
The SSCVS includes two primary buildings. The Salt Reduction Building pre-filters salt-laden air coming from the WIPP underground, while the New Filter Building has fans and HEPA filtration to further clean the air.
What is WIPP?
WIPP remains the United States’ only deep geological repository for nuclear waste. It’s a system of disposal rooms mined out of an ancient salt bed 2,150 feet underground. It has operated since 1999, celebrating its 25th anniversary of accepting transuranic waste from DOE cleanup sites across the U.S. The waste consists of items contaminated with small amounts of plutonium and other human-made radioactive elements. The waste has been accumulating since the 1940s as part of the nation’s nuclear defense program dating back to the Manhattan Project.
-Contributor: George Rangel
 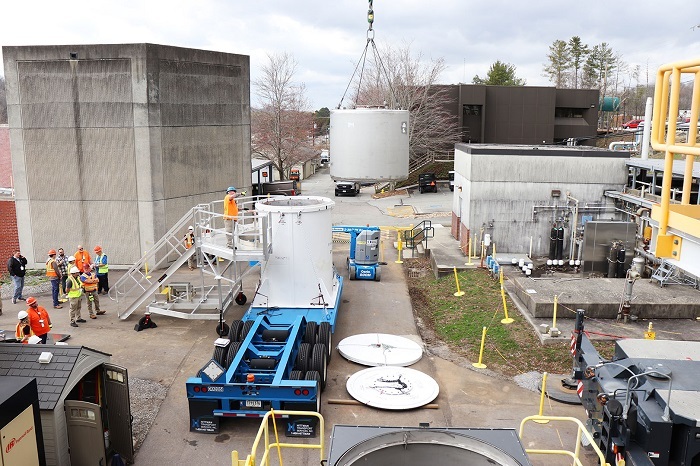 Employees move processed material to a shipping cask for permanent disposal offsite. Since processing began in the U-233 Disposition Project, Isotek has shipped approximately 350,000 pounds of waste for disposal.
OAK RIDGE, Tenn. – The Oak Ridge Office of Environmental Management (OREM) and contractor Isotek achieved a 2024 priority for the U.S. Department of Energy Office of Environmental Management (EM) while also crossing another major milestone in the highest priority cleanup project at Oak Ridge National Laboratory (ORNL).
OREM and Isotek surpassed EM’s goal of processing 35 canisters of uranium (U)-233 in 2024. They have processed 39 canisters so far this year, bringing the total to 100 canisters processed as part of the U-233 Disposition Project.
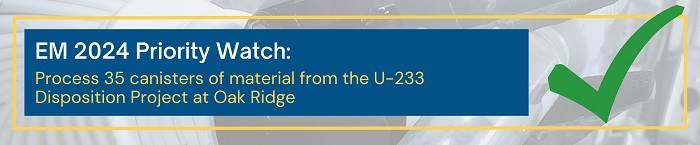 The project is focused on eliminating the inventory of U-233 stored in the world’s oldest operating nuclear facility, located at ORNL. That material presents risks and is costly to keep safe and secure. Originally created in the 1950s and 1960s for potential use in reactors, U-233 proved to be an unviable fuel source.
“Getting to this point has taken a lot of hard work,” said Sarah Schaefer, Isotek president and project manager. “Each canister can present its own unique challenges, but the people at Isotek always figure it out and keep us moving forward.”
Half of the U-233 inventory was disposed of between 2011 and 2017; however, the remaining material requires processing to convert it into a form safe for shipment and disposal.
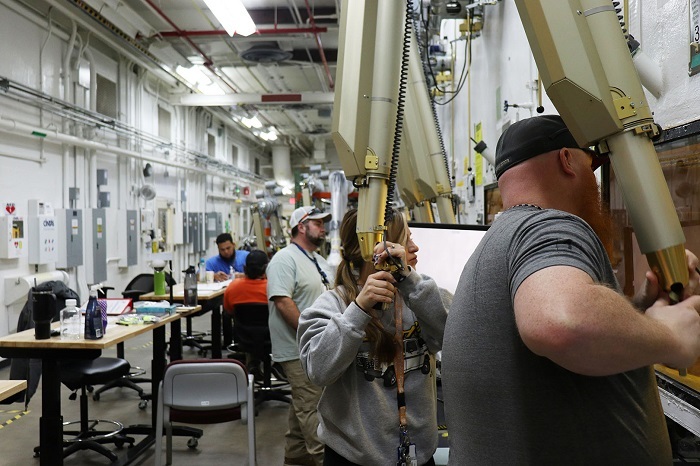 Isotek employees are processing the higher-dose uranium-233 in hot cells into a form safe for shipment and disposal.
Isotek began processing the lower-dose material in 2019 and higher-dose material in 2022. The current processing campaign for the higher-dose material is 25% complete and slated for completion in 2026.
Isotek has shipped approximately 350,000 pounds of waste for disposal since processing began in the U-233 Disposition Project.
As Isotek progresses through the remaining inventory, the contents of the canisters will present more challenges, such as a higher radiation dose or more difficulty in opening the canisters.
“Isotek has already designed and tested the equipment needed to process the next type of U-233, and we intend to begin processing it before the end of this year,” said Schaefer.
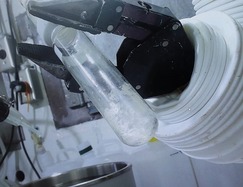 |
|
Isotek employees are extracting thorium-229, an extremely rare isotope, from uranium-233 material before it is processed and disposed of. Those isotopes are helping supply clinical trials for a promising form of next generation cancer treatment. |
Additionally, an agreement with TerraPower allows Isotek to extract thorium-229, an extremely rare isotope, from the material before it is processed and disposed of.
Isotek extracts the thorium-229 before it’s shipped to TerraPower. The company uses that extracted material to recover actinium-225, a medical isotope critical to a promising form of next generation cancer treatment called targeted alpha therapy.
Earlier this year, TerraPower announced it distributed the first samples of actinium-225 to two pharmaceutical companies to support the development of the revolutionary cancer treatment.
Once all thorium-229 has been extracted over the next four years during the remainder of the U-233 Disposition Project — an estimated 40 grams — 100 times more doses of next generation cancer treatments will be available annually than are currently available worldwide.
Global demand for actinium-225 is expected to increase as more treatments are developed, making the work performed by OREM and Isotek more vital and impactful.
-Contributor: John Gray
 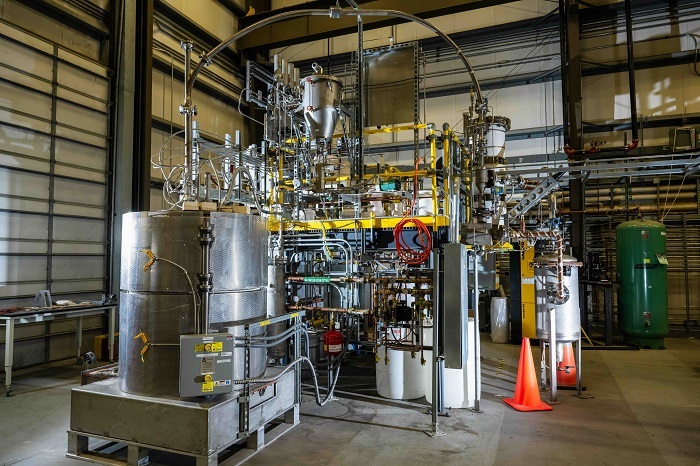 This scaled-down vitrification plant at the Pacific Northwest National Laboratory is being commissioned to test various waste glass components and configurations.
RICHLAND, Wash. — For more than a decade, the U.S. Department of Energy Office of Environmental Management’s Office of River Protection has collaborated with national and international laboratories, universities and glass industry experts to plan and prepare for 24/7 operations at the Waste Treatment and Immobilization Plant (WTP) at the Hanford Site.
When operational, WTP will begin vitrifying millions of gallons of radioactive and chemical waste stored in Hanford’s large, underground tanks since national defense operations during World War II and the Cold War era. Vitrifying the waste entails immobilizing it in glass through mixing in large melters.
When cooled, the waste components do not sit inside the glass, rather they become part of the glass itself, chemically bound in place for safe disposal.
The waste treatment preparations include work by experts in national facilities: Pacific Northwest National Laboratory (PNNL) in Richland, Washington; Idaho National Laboratory in Idaho Falls; the Vitreous State Laboratory in Washington, D.C.; and Savannah River National Laboratory in Aiken, South Carolina. The international counterparts include universities in England and the Czech Republic, colleagues in Sweden and Israel, and institutes in France and Japan.
Over the years, the national labs have developed a large database of glass properties, from which PNNL has built chemical-property models and a glass-formulation program to run the vitrification process more efficiently. In addition, Rutgers University, Washington State University – Pullman and Sheffield Hallam University in England have contributed through studying the structure of glass and how it can be used to control the properties of various wastes.
The University of Chemistry and Technology in Prague has contributed through testing how various waste streams are fed to melters, and scientists in Israel, Sweden and England have studied waste glass durability and how it compares to that of naturally occurring glasses that have existed in the environment for thousands of years.
In addition, communication with Corning Inc., formerly Corning Glass Works, ensures alignment with current industrial glass manufacturing developments, and discussions with counterparts in France and Japan help ensure correlation with similar research where technologies, waste streams and immobilization strategies differ slightly.
The international effort has been instrumental in helping Hanford anticipate and address engineering and operational challenges to immobilize waste in glass. PNNL, the lab closest to WTP and directly connected to the Hanford Site, has been the integrator of the effort, maintaining the largest staff, a diverse array of laboratory equipment and several key testing platforms.
-Contributor: Albert Kruger
 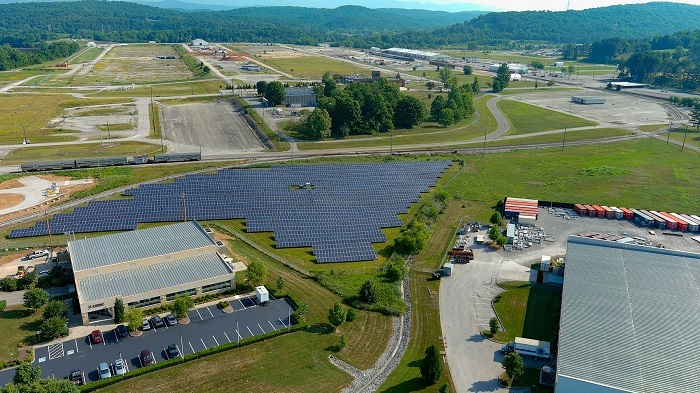 Oak Ridge's East Tennessee Technology Park is home to several clean energy initiatives, including this 1.2-megawatt solar array.
OAK RIDGE, Tenn. – The U.S. Environmental Protection Agency (EPA) has recognized the Oak Ridge Office of Environmental Management (OREM) and cleanup contractor UCOR for successful cleanup of the East Tennessee Technology Park (ETTP).
EPA presented its Superfund National Priorities List Award to OREM and UCOR as part of the seventh annual National Federal Facility Excellence in Site Reuse Awards. The awards highlight the accomplishments of federal agencies, states, tribes, local partners, communities and developers in restoring and reusing once-contaminated land at federal facilities.
After two decades of cleanup, planning and development, the 2,200-acre former uranium enrichment site at Oak Ridge is now home to a multi-use industrial park, Manhattan Project National Historic Park and nature conservation area.
“We’re proud of how our cleanup of ETTP has eliminated environment risks and transformed the site into an attraction for growing businesses,” said Erin Sutton, OREM’s Quality and Mission Support Division director. “Our projects have resulted in the transfer of more than 1,700 acres to the community to generate new economic opportunities.”
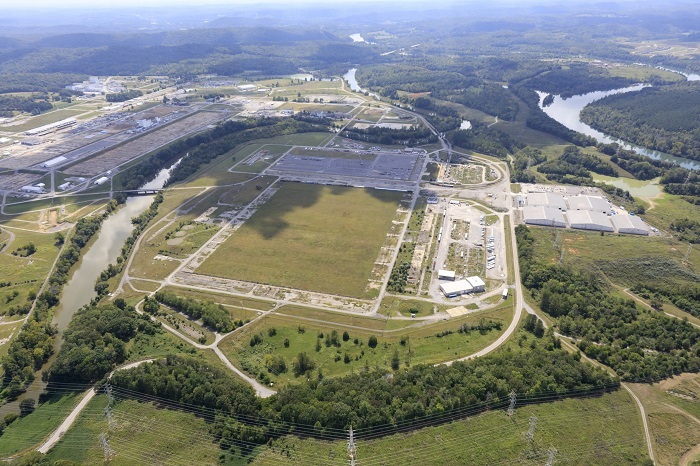 Kairos Power will construct its demonstration facility on the footprint of the former K-33 Building at Oak Ridge. The Oak Ridge Office of Environmental Management demolished the former enrichment facility and transferred the land to the community for economic reuse.
More than 20 businesses are currently operating at the site, and that number continues to increase with next generation nuclear companies and other entities.
The latest announcement is a $100 million investment from Kairos Power. The company expects to break ground on its demonstration facility later this year at ETTP after receiving approval for its construction permit.
EPA created the National Federal Facility Excellence in Site Reuse Awards to recognize exceptional work remediating a federal site for its beneficial use and creating positive impacts to the community.
“We appreciate EPA’s recognition of this massive cleanup effort, one of the largest ever undertaken anywhere,” Ashley Saunders, UCOR Program and Sustainability Program manager, said. “Successful cleanup of the East Tennessee Technology Park underscores the value of strong partnerships and a collaborative vision shared by the community, other federal agencies, the state and local community partners.”
-Contributor: Mike Butler
 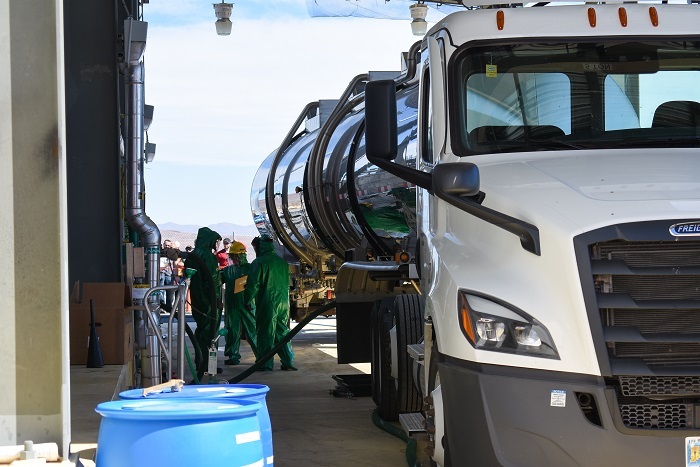 Workers unload a tanker truck carrying sodium hydroxide to the Hanford Site’s Waste Treatment and Immobilization Plant. This will be the first chemical fed into the plant’s melters to simulate Hanford tank waste during the cold commissioning phase.
RICHLAND, Wash. — Workers recently unloaded a shipment of more than 10,000 gallons of sodium hydroxide delivered to the Hanford Site’s Waste Treatment and Immobilization Plant (WTP). The liquid sodium hydroxide will be the first chemical fed into the plant’s melters to simulate Hanford tank waste.
“The delivery of sodium hydroxide is an important precursor to several months of testing using simulated waste, known as the cold commissioning phase,” said Mat Irwin, the U.S. Department of Energy Office of Environmental Management’s acting assistant manager for the WTP Project. “WTP crews will test the waste processing and exhaust treatment systems in the plant’s Low-Activity Waste Facility before introducing actual tank waste into the plant during hot commissioning.”
Commissioning of the facility is an important step in preparing to vitrify, or immobilize in glass, millions of gallons of radioactive and chemical waste from Hanford’s large underground tanks.
A second, longer-term use of sodium hydroxide will be to treat hazardous liquids coming from the facility’s exhaust treatment system and the system that treats liquids generated during the vitrification process.
Many industries use sodium hydroxide, commonly known as lye, as a versatile chemical. However, sodium hydroxide, like other industrial chemicals, has to be treated as a hazardous substance. To ensure the safe handling of the chemical onsite, workers are required to follow strict safety protocols during its use, which includes storing it in an isolated tank at the WTP.
“Our team prepared for this delivery by implementing safety measures to ensure the safe handling, storage and use of sodium hydroxide onsite,” said Rick Holmes, Bechtel National Inc. principal vice president and general manager for Waste Treatment Completion Company, primary subcontractor to Bechtel. “The team’s success marks an important step toward cold commissioning later this year and preparing for the future sustained production of vitrified waste.”
During future waste treatment operations, treated waste from Hanford’s underground tanks will be fed directly to melters inside the Low-Activity Waste Facility. The waste will be mixed with glass-forming materials and heated, and then poured into stainless steel containers for disposal at Hanford’s Integrated Disposal Facility.
 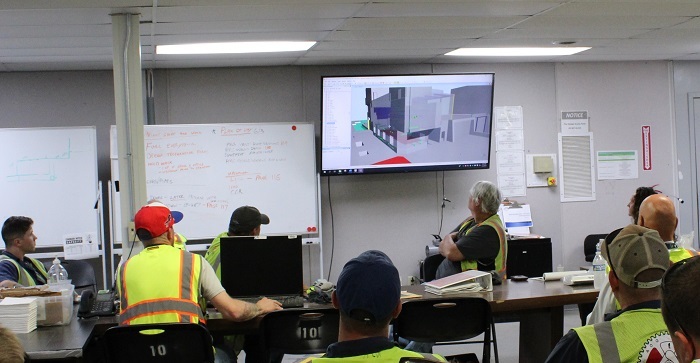 A 3D model is used at a pre-job briefing at the West Valley Demonstration Project to show employees what to expect during their shift as they continue deconstructing the Main Plant Process Building and removing waste.
WEST VALLEY, N.Y. – The U.S. Department of Energy Office of Environmental Management (EM) and its cleanup contractor at the West Valley Demonstration Project drew from innovation and teamwork to create a 3D model of the Main Plant Process Building currently undergoing demolition.
Created with the help of onsite engineers and a contracted company, the 3D model shows everything from walls and support beams to equipment and piping.
“The West Valley team used collaboration and inclusion to their advantage when developing this innovative tool,” EM West Valley Project Management Assistant Director Stephen Bousquet said. “This tool helps our team to be safer as they continue to deconstruct the Main Plant in a methodical and deliberate manner.”
The development team realized early on that old drawings either didn’t match up or did not reference other drawings due to deactivation work EM crews have undertaken at the facility over the past 30 years. This made it difficult to determine the structural aspects of the building, the method to take it down safely and the right equipment to use.
The West Valley team provided drawings rendered into the 3D model software. Over 18 months, the model took shape with the capability of showing the structure in 3D.
The 3D model was used to determine the rate and sequence of how crews would deconstruct the Main Plant, which has been successful with no incidents, unplanned radiological releases or injuries.
The model showed the locations of more than 120 items requiring special handling and packaging. It also pinpointed multiple locations of specialty piping with high radiation potential and asbestos-containing material, which is hazardous. Crews applied all required safety measures for that material to the Main Plant demolition.
Engineers used the model to evaluate the plant’s walls, components, structural members and obstructions, allowing for an analysis of structural integrity and hazard points as the demolition sequence unfolded.
“We use this model everyday in our pre-job briefings and on both shifts,” said Scott Chase, deputy facility disposition manager with CH2M HILL BWXT West Valley, EM’s cleanup contractor at the site. “It allows our crews to see through the wall of the building and what to expect once work starts. If they see something that’s not right or could impact safety, they have the right to stop work.”
The above-grade portion of the Main Plant is one of the last major facilities remaining at West Valley. Its successful demolition will further reduce environmental risks and position the site for the next phase in cleanup. The demolition is expected to be completed in the fiscal year that begins this October.
-Contributor: Joseph T. Pillittere
 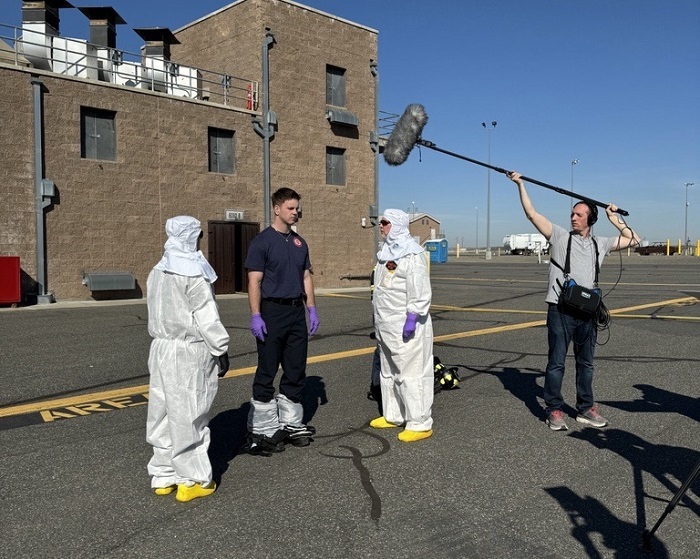 The Hanford Site has implemented a new training video detailing best practices for safely doffing potentially contaminated firefighter gear, and it is now part of the site’s biennial training for radiological control technicians.
RICHLAND, Wash. — The Emergency Management and Preparedness team with Hanford Site contractor Hanford Mission Integration Solutions (HMIS) gave a presentation at the 2024 Emergency Management Symposium.
The annual event provides an opportunity for emergency management personnel to engage with their peers throughout the U.S. Department of Energy (DOE) complex, sharing ideas and information related to training, exercises and planning. During the presentation, HMIS highlighted firefighter safety at the Hanford Site and emphasized the importance of safely removing firefighting gear after entering potentially contaminated areas.
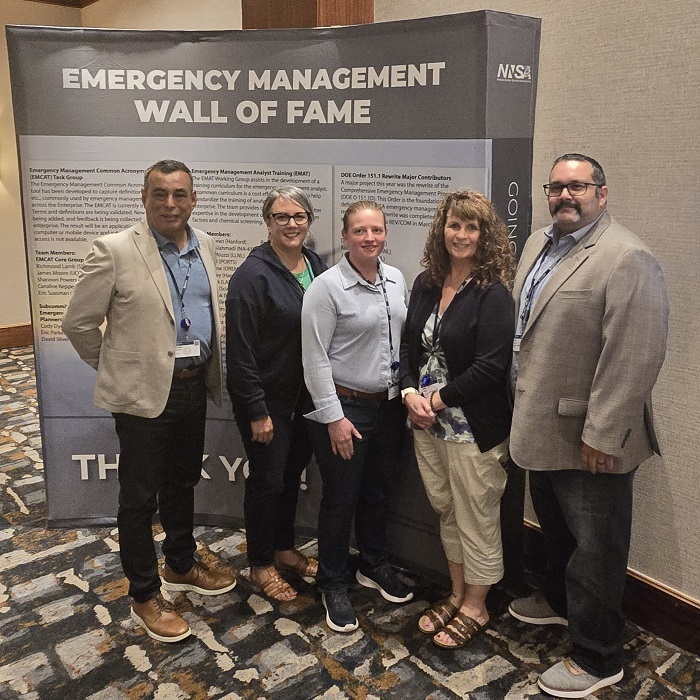 Ted Morales, Dulcie Allen, Renae Harvey, Gina Miller and Jose Garcia. Members of the Emergency Management and Preparedness team with Hanford Mission Integration Solutions attended the 2024 Emergency Management Symposium, giving a presentation highlighting the Hanford Site’s new doffing training and procedures.
Jose Garcia, an emergency preparedness specialist with HMIS, spoke about the challenges of training for radiological firefighter gear removal, known as doffing, in a multi-contractor environment like the Hanford Site. He explained that Hanford’s contractors each had their own doffing procedures, but the procedures had to be standardized so that any of the radiological control technicians available to respond to a drill or emergency event followed the same doffing process.
Representatives from the One Hanford team collaborated to develop a new emergency procedure, establishing sitewide training requirements for the contractor doffing teams. These requirements include standardized biennial classroom training and a new training video detailing a firefighter doffing scenario.
Garcia presented the video to the first responders subcommittee at the symposium, which includes firefighters and trainers from across the complex.
"Our contractor teams recognizing that an improvement opportunity existed in our emergency preparedness procedures was excellent,” shared Briana Lindberg, DOE’s Emergency Preparedness Program manager at Hanford. “This type of collaboration and continuous improvement ensures the continued safety of our people and the progress of our mission."
-Contributor: Jill Harvill
|