 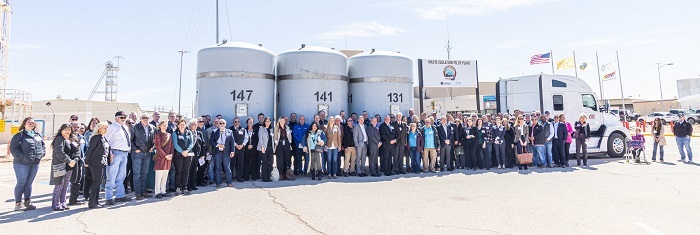 Following a ceremony recognizing the 25th anniversary of the underground waste repository, attendees gathered for a photograph next to a Waste Isolation Pilot Plant truck and empty, new transportation containers used to transport transuranic waste to the facility.
CARLSBAD, N.M. — EM’s Waste Isolation Pilot Plant (WIPP) reached a major milestone last week — 25 years of operations at the nation’s only deep, underground geological repository for disposal of defense-generated transuranic (TRU) nuclear waste.
It was a full auditorium during a recognition ceremony at the WIPP site. Attendees included officials from the DOE, Defense Nuclear Facilities Safety Board, U.S. Mine Safety and Health Administration, State of New Mexico Environment Department, as well as elected New Mexico state officials, regional and local elected officials, community leaders and civic organizations.
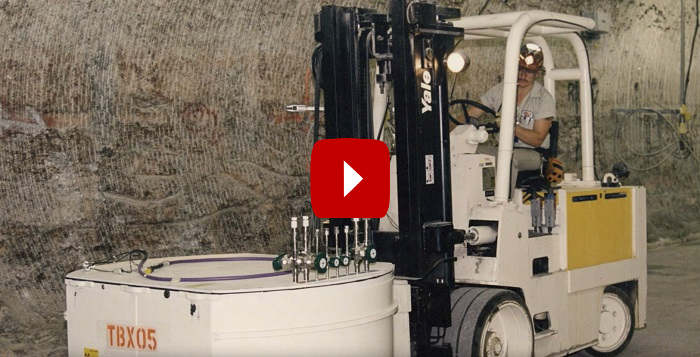 This video chronicles EM's Waste Isolation Pilot Plant history and achievements, and looks to the future as significant infrastructure upgrades are underway at the underground waste repository.
“WIPP plays a vital role not only disposing of the nation’s TRU waste, but also in our national security,” said William “Ike” White, EM senior advisor. “Because of WIPP, more than 20 DOE sites have been able to safely dispose of their TRU waste, resulting in a reduced risk to millions of Americans.”
White added, “WIPP remains the cornerstone of the U.S. DOE’s important environmental cleanup mission, permanently disposing of the nation’s TRU waste.”
Twenty-five years ago, WIPP received its first shipment of defense-generated TRU waste, marking the official beginning of operations. The shipment from the Los Alamos National Laboratory was safely transported and disposed of in the WIPP underground disposal area.
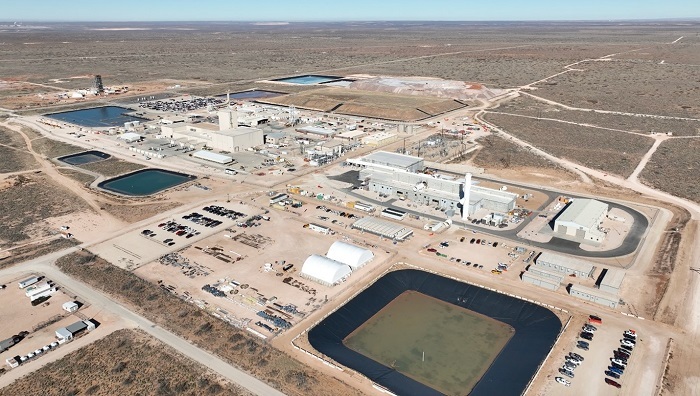 Located in southeast New Mexico, about 33 miles east of Carlsbad, New Mexico, the Waste Isolation Pilot Plant repository is carved out of a 2,000-foot-thick salt bed formed 250 million years ago. Transuranic waste is disposed of 2,150 feet underground in rooms mined from the salt bed.
“This is an exciting day for our employees and the surrounding area,” said Mark Bollinger, EM’s Carlsbad Field Office manager. “Without the dedication of the workforce, we would not be here today. Their attention to detail and safety is the reason WIPP has been so successful.”
Since WIPP’s opening on March 26, 1999, TRU waste shipments to the underground repository safely traveled over 16.5 million loaded miles, which would equate to approximately 34 round trips to the moon. This has led to the safe disposal of over 285,000 waste containers in the WIPP underground.
-Contributor: Bobby St. John
 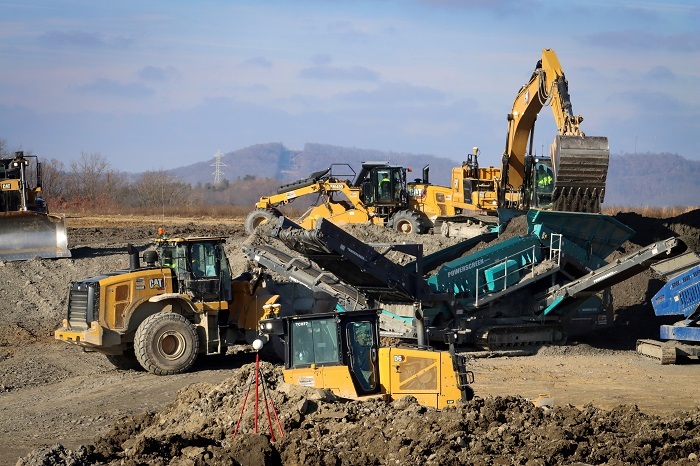 A crew at the Portsmouth Site On-Site Waste Disposal Facility screens select fill for the facility’s Cell 2.
PIKE COUNTY, Ohio — EM’s Portsmouth Site has finished excavating approximately seven acres for its On-Site Waste Disposal Facility (OSWDF) to prepare for debris from the demolition of X-333, a former uranium enrichment process building measuring more than 50 acres of floor area.
“Our On-Site Waste Disposal Facility Capital Asset Project 2 team continues to safely and successfully exceed deadlines, finishing this excavation project a month ahead of schedule,” Portsmouth Federal Project Director Jud Lilly said.
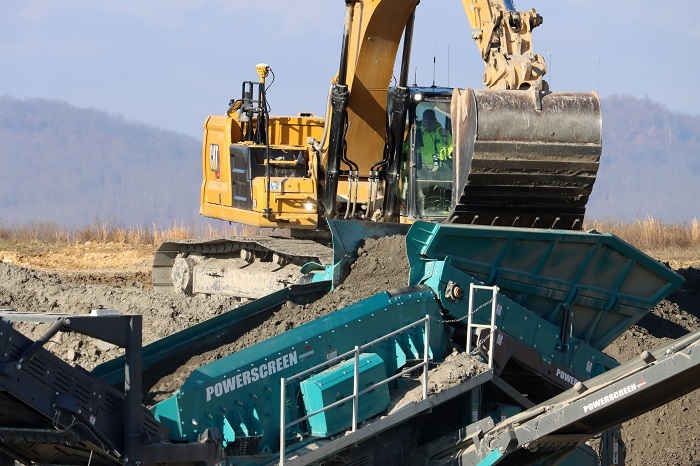 A heavy equipment operator loads excavated soil from the Portsmouth Site On-Site Waste Disposal Facility into screening equipment.
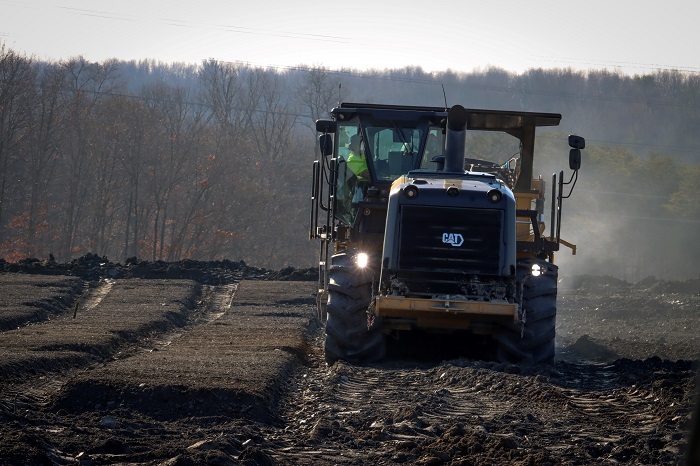 A heavy equipment operator places select fill in Cell 2 of the Portsmouth Site On-Site Waste Disposal Facility.
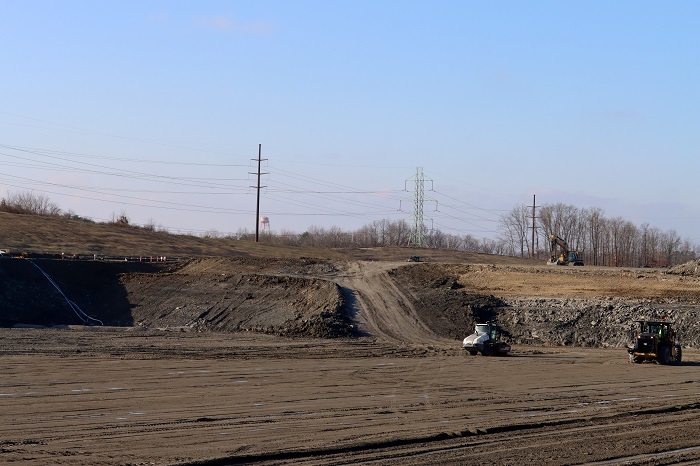 Operators use equipment to compact select fill surface inside Cell 2 for the Portsmouth On-Site Waste Disposal Facility.
Excavation was successfully completed for Cell 2, the fourth cell in a series of disposal cells planned for construction at the waste disposal facility.
“It takes a full construction season to build the cell liner system,” Portsmouth OSWDF Construction Manager John McDonald said. “The OSWDF team was dedicated and committed to achieving this first major step in Cell 2 completion.”
The next step in the process is placing select fill, the clay layer and geosynthetic material.
Select fill is soil screened per design specifications for use as backfill material and is then placed in the Cell 2 excavation, bringing it to the proper grade prior to construction of the Cell 2 clay layer. Cell 2 is slated for completion by the end of this year.
-Contributor: Michelle Teeters
 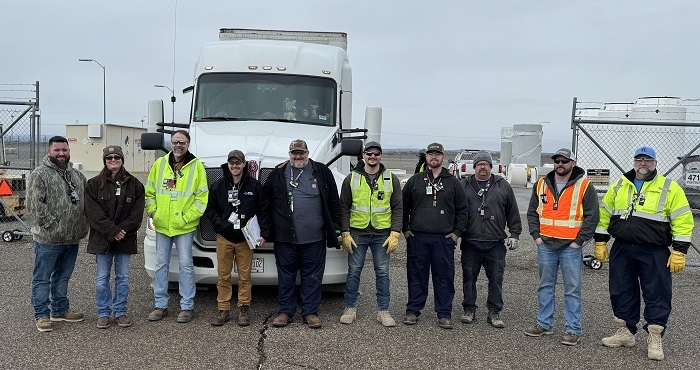 Workers with Hanford Site contractor Central Plateau Cleanup Company celebrate the completion of shipment of sodium waste off the Hanford Site. From left: Brandon Matosich, field work supervisor; Tina Carter, field work supervisor; Andy Mix, shipper; Nick Sargent, shipper; Dave Stewart Jr., nuclear chemical operator; Ivan Borshch, driver; Cosmo Zampelli Jr., deactivation & decommissioning; Sean Groff, deactivation & decommissioning; Zach Smith, driver; and Jim Drake, nuclear chemical operator.
RICHLAND, Wash. — Recent completion of a project at the Hanford Site marked a significant accomplishment, as crews from EM contractor Central Plateau Cleanup Company (CPCCo) loaded and shipped 15 drums of sodium waste from the site’s former research reactors for offsite treatment.
The waste has been stored since 2012 near Hanford’s Fast Flux Test Facility (FFTF), a former sodium-cooled nuclear research and test reactor that operated from 1982 to 1992.
FFTF was shut down in 1993 and eventually placed in long term surveillance and maintenance after deactivation and decommissioning activities were completed in 2009.
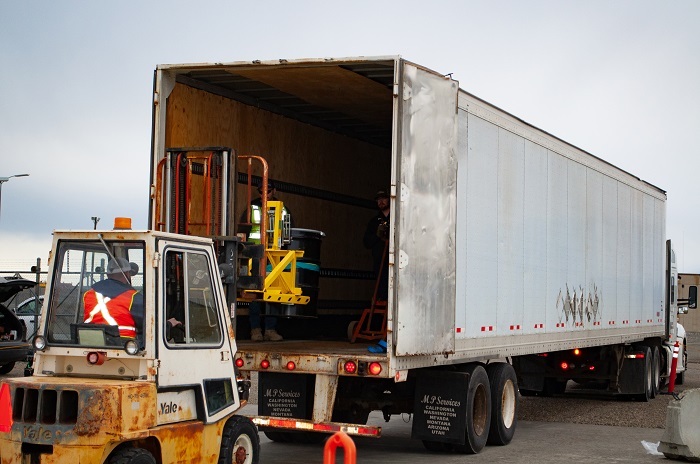 A worker with Hanford Site contractor Central Plateau Cleanup Company loads a drum of sodium waste at the Hanford Site near Richland, Washington, for transportation to an offsite treatment facility. The waste is treated to meet environmental protection requirements for a return to Hanford for safe disposal.
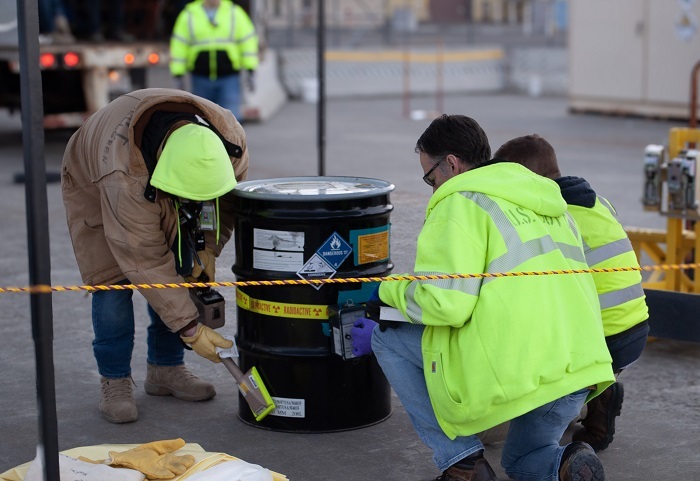 Workers survey the outsides of drums of sodium waste as part of their safety checks before loading them for the trip to an offsite treatment facility.
Sodium is challenging to manage and treat, in large part because it is corrosive and flammable.
“Our planning and preparation to ship this difficult-to-handle waste have ensured a safe treatment and disposal pathway for the sodium,” said Andy Wiborg, EM project director at Hanford. “Completion of this project eliminates a key risk on the Hanford Site.”
The waste was sent to an offsite facility, where it will be treated and repackaged to meet state and federal standards for return to the Hanford Site and safe disposal. When returned to Hanford, the drums will be disposed of in low-level burial grounds near the Central Waste Complex in Hanford's 200 West Area.
“Shipment of this sodium waste marks another significant achievement in our risk-reduction mission as we prepare for 24/7 operations at Hanford,” said Randy May, CPCCo field operations manager.
 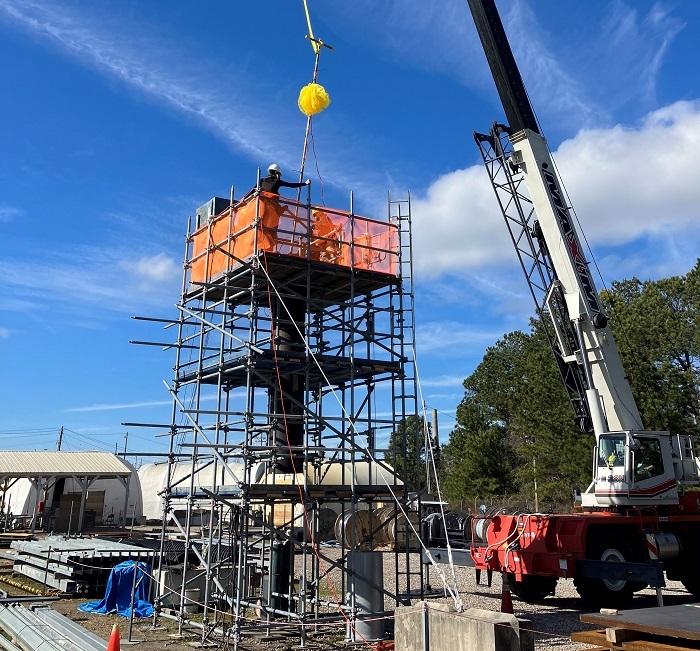 Savannah River Site workers move an innovative grinder into place for mock-up testing before proceeding to a tank where the tool will be used to grind residual welding material inside a waste tank riser.
AIKEN, S.C. — Innovation fueled the creation of a new tool at EM's Savannah River Site (SRS) that helps ensure equipment being lowered into an underground liquid waste tank does not encounter any interferences.
This grinding tool, built by the construction team for SRS liquid waste contractor Savannah River Mission Completion (SRMC), was needed to remove obstructions inside of a tank top opening — known as a riser — in H Tank Farm, one of two groupings of underground waste tanks at SRS. The tanks hold radioactive liquid waste generated as byproduct from the processing of nuclear materials for national defense, research, medical programs, and for NASA missions. Risers are used to insert equipment, such as mixing pumps and jets, into the waste tanks.
The obstructions included remnants of welding material left over from equipment previously removed from the tank in the 1970s. With obstructions remaining on the inside of the riser, crews would be unable to insert a mixing pump needed for waste removal and tank closure activities.
The team took on the difficult task led by Tony Smith, construction superintendent, and Beau Nichols, discipline engineer. Both Smith and Nichols were supported by pipefitters, the radiological protection group, and the inspection and monitoring team. The groups developed, tested and perfected the tool and its use though several mock-up evolutions.
“The tool we used was a disc grinder, with diamond grit coating, attached to a 20-foot steel tube,” Nichols said. “It utilizes guide bars on one end to prevent the disc from grinding too deeply into the riser, as well as some modifications that allow the grinder to be operated by workers who must stand at a safe distance.”
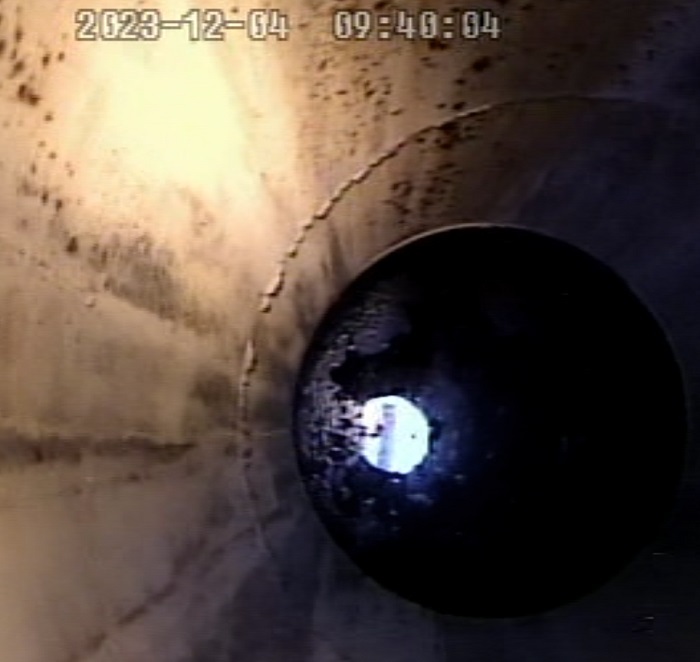 This photo shows some of the welding material that was needed to be removed from inside a waste tank riser at the Savannah River Site. The material was ground away to allow for insertion of a mixing pump.
The tool is suspended overhead from a crane and is secured at the riser opening to maintain a consistent elevation for the grinding.
Pipefitters in a protective hut were able to view their work on a closed-circuit TV monitor staged in the hut, while live video was provided by a camera attached to the tool just above the grinder. The superintendent and radiological protection personnel also viewed the video feed in a nearby command trailer while providing guidance through radio communication.
Jim Folk, DOE-Savannah River assistant manager for waste disposition, said clearing the access riser was an important step for continued treatment of the tank’s waste.
“Successful waste removal is the first step toward operational closure of a liquid waste tank,” Folk said. “This tank is one of several that is entering final stages of removal from use, and this creative solution helps the tank remain on its path to closure.”
-Contributor: Jim Beasley
 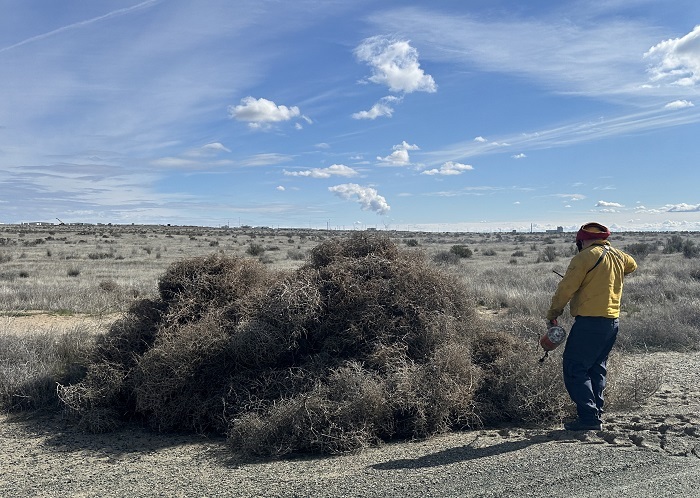 Hanford Fire Captain Dave Wheeler lights a pile of tumbleweeds on the Hanford Site during controlled burns in the spring and summer to clear brush near roadways and facilities.
RICHLAND, Wash. — The Hanford Fire Department is using prescribed burns at the 580-square-mile EM cleanup site to reduce wildfire risks in the late spring and summer.
The controlled fires help manage the significant accumulation of tumbleweeds during windstorms in southeastern Washington state that pile up in low areas, along fence lines and roads and near facilities.
“The fast-burning and mobile plants can quickly turn a manageable brush fire into a much larger wildfire,” said Brian Harkins, EM Hanford assistant manager for Mission Support. “This proactive approach to fire management underscores our commitment to sustain continuous cleanup operations and protect site personnel, government property, the community and the environment.”
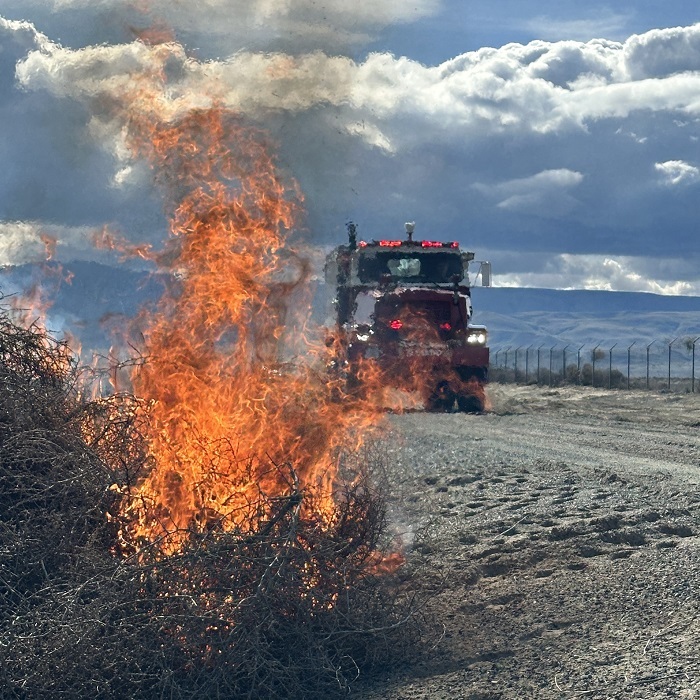 Clearing and burning brush is a proven fire protection method that can halt or hinder the spread of a wildfire.
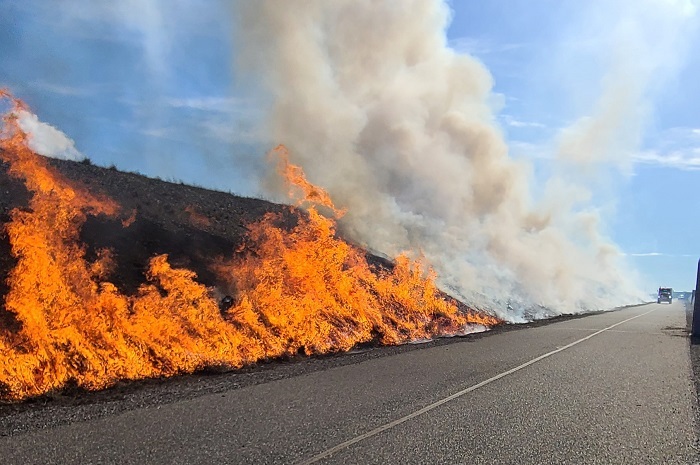 Hanford Site firefighters burn tumbleweeds that have piled up along State Highway 240, which runs through the site and has been closed during severe windstorms because large piles of tumbleweeds have blocked traffic and trapped motorists.
From March through August, the fire department, managed by contractor Hanford Mission Integration Solutions, conducts the burns, prioritizing the safety of personnel and environmental conservation.
“Prescribed burns are a safe, proven technique for reducing fire hazards,” said Nick Thomas, interim fire chief. “This method prevents the accumulation of potential fire fuels, such as dried vegetation, around critical areas, ensuring our natural landscapes are safer and more resilient.”
Safety remains a priority for the fire department, extending beyond site protections to encompass the surrounding communities. Through careful planning and implementation, the fire department uses prescribed burns as an effective risk management method, reinforcing its pledge to sustain high standards for safety at the Hanford Site.
-Contributor: Cerise Peck
 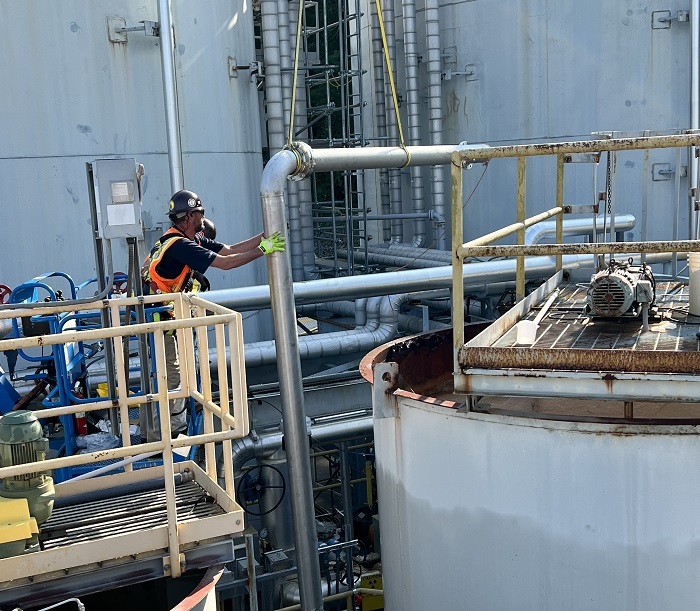 Oak Ridge crews installed approximately 5,500 feet of new piping as part of a project at the Liquid and Gaseous Waste Operations system. The work required 5,000 hours of welding to complete the nearly two miles of welded lines.
EM crews completed project three months ahead of schedule and $900,000 under budget
OAK RIDGE, Tenn. – The Oak Ridge Office of Environmental Management and contractor UCOR recently completed an extensive piping replacement project to extend the life of the Liquid and Gaseous Waste Operations (LGWO) system at Oak Ridge National Laboratory (ORNL).
Replacing the piping and completing other upgrades alleviates the recurring need for maintenance and repair of aging infrastructure built many decades ago and ensures the system's reliability. Portions of the piping had corrosion that needed to be addressed.
LGWO contains three waste treatment systems that collect, treat and reduce the volume of liquid and gaseous waste across the laboratory. LGWO encompasses more than 60 facilities and 27 miles of piping that process waste generated from cleanup operations, research and development laboratories, and active and deactivated nuclear reactors.
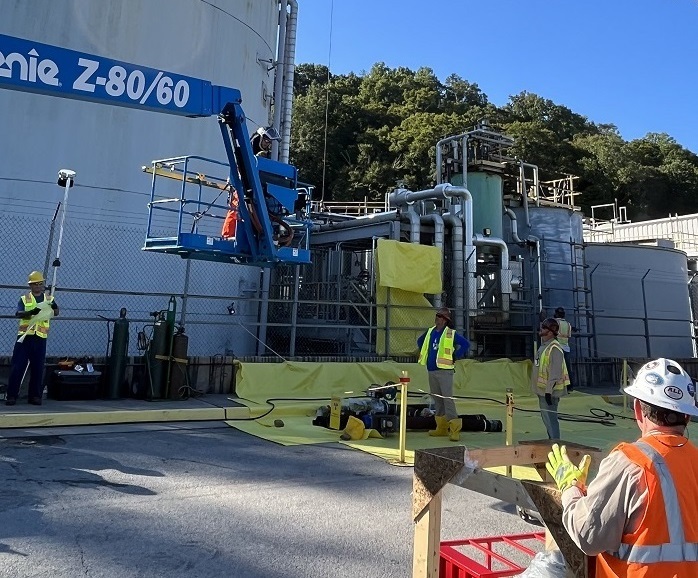 Oak Ridge’s Liquid and Gaseous Waste Operations system contains three waste treatment systems that collect, treat and reduce the volume of liquid and gaseous waste across the Oak Ridge National Laboratory. The system encompasses more than 60 facilities and 27 miles of piping.
The two-year, $18 million project replaced nearly two miles of above-ground piping and valves at the 3608 Process Waste Treatment Complex, making the system more efficient and reliable and helping avoid the possibility of disrupting ongoing ORNL operations.
The LGWO system is critical to ORNL’s ongoing missions, and an outage would result in immediate impacts at the site.
Over the span of the project, employees safely executed 132 critical lifts — a much larger number compared to typical lifts done in Oak Ridge cleanup projects. The lifts for the piping replacement project were crucial due to increased risk from lifting large, heavy fabricated piping loads over the system's critical infrastructure.
During the project, crews disposed of 115,000 pounds of waste, installed approximately 5,500 feet of new piping, conducted heat tracing to maintain the proper temperature of the piping, and installed insulation. The work required 5,000 hours of welding to complete the nearly two miles of welded lines.
UCOR completed the project three months ahead of schedule and $900,000 under budget. The work is the latest of several modernization efforts of LGWO facilities.
Most recently, workers completed replacement of the Distributed Control System, which controls LGWO’s instrumentation.
Other efforts included installing a new pretreatment facility that treats low-level liquid waste and allows it to be diverted from storage tanks directly to the Process Waste Treatment System, and replacing a diesel generator that powers critical pumping stations and valve boxes if power is interrupted.
-Contributor: Shannon Potter
 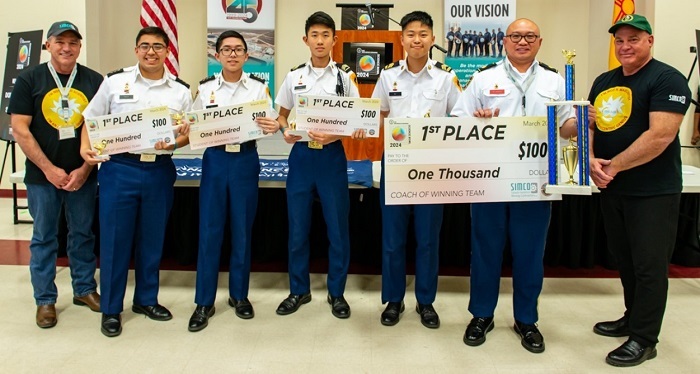 Roswell’s New Mexico Military Institute team emerged as the first-ever southeastern New Mexico DOE Regional Science Bowl champion. Salado Isolation Mining Contractors President and Program Manager Ken Harrawood, far left, and EM Carlsbad Field Office Manager Mark Bollinger, far right, presented trophies and gift certificates to the students and coach.
CARLSBAD, N.M. — The Waste Isolation Pilot Plant (WIPP) recently held its first-ever DOE Regional Science Bowl, joining what has become a yearly tradition across the complex for EM sites such as Savannah River, Portsmouth and Paducah.
Salado Isolation Mining Contractors (SIMCO), WIPP’s management and operations contractor, organized and sponsored the event. SIMCO Education Outreach Lead Joy James-Foster led a local community effort that brought together regional high schools, students, a local college and dozens of WIPP volunteers.
After hours of an intense Saturday competition, only one team remained and won the inaugural southeastern New Mexico Regional Science Bowl. Roswell’s New Mexico Military Institute team was crowned the regional champion and will represent southeastern New Mexico at the upcoming National Science Bowl in Washington, D.C.
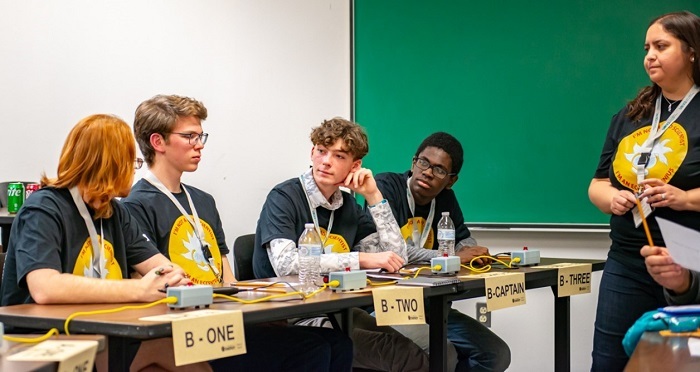 EM’s Waste Isolation Pilot Plant (WIPP) held its first-ever DOE Regional Science Bowl last month, featuring seven teams competing for a spot at the National Science Bowl. Salado Isolation Mining Contractors, WIPP’s management and operations contractor, organized and sponsored the event, hosted by Southeast New Mexico College in Carlsbad, New Mexico.
Hosted at Southeast New Mexico College, this year’s Regional Science Bowl consisted of seven teams, facing off for the chance to show off their knowledge at one of the most prestigious national academic science competitions. Participating schools included Carlsbad High School, Carlsbad Early College, New Mexico Military Institute and Hobbs High School.
The New Mexico Military Institute team, made up of two sophomores, a junior and senior, were able to hold off the other teams to claim victory. While demonstrating exceptional knowledge in the fields of math and science, the team took the No. 1 title, securing its spot at the national competition set for April 25-29.
-Contributor: Bobby St. John
|