 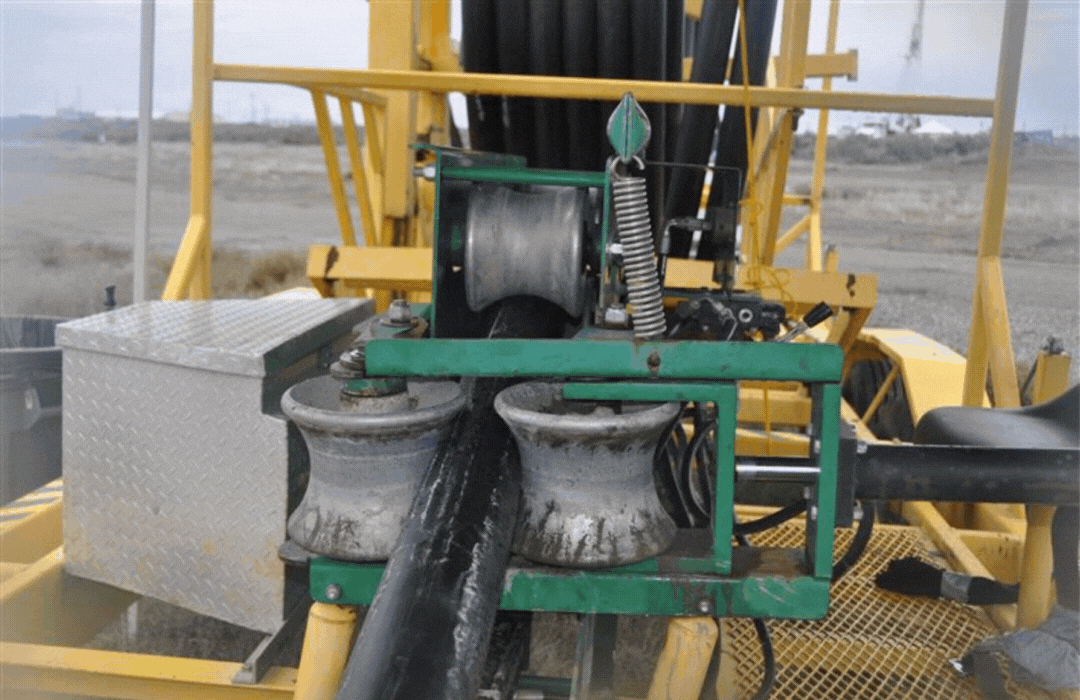 Workers with EM contractor Central Plateau Cleanup Company are installing piping to expand the Hanford Site’s groundwater treatment network. They use a specialized machine to straighten hundreds of feet of coiled piping and reduce the number of connections, significantly improving efficiency in the field.
RICHLAND, Wash. — EM construction crews at the Hanford Site are laying it on the line — literally — to expand the treatment capacity of the site’s already robust groundwater cleanup program.
The expansion project by contractor Central Plateau Cleanup Company requires the installation of 54,000 feet — more than 10 miles — of specialized plastic piping to connect the 200 West Pump and Treat Facility, Hanford’s largest groundwater treatment plant, to about a dozen new groundwater extraction wells. The expanded network of wells will increase the capacity of the treatment facility from 2,500 to 3,400 gallons per minute to capture more chemical and radiological contaminants from the groundwater under the site’s Central Plateau.
The original approach to installing the piping involved placing and connecting each 40-foot section individually, a labor-intensive endeavor. Enter the Line Tamer, a machine that straightens hundreds of feet of coiled pipe at a time and reduces the number of connections, significantly expediting installation. To date, crews have installed more than 26,000 feet of the piping using the machine.
“The use of this specialized equipment is another example of our award winning groundwater team finding and implementing an innovative and cost effective solution to boost our treatment efforts,” said Naomi Jaschke, project director for Hanford’s soil and groundwater division. “Expanding the capacity of our largest treatment facility will potentially reduce costs and shorten the time needed to meet cleanup goals, with protection of the Columbia River our ultimate mission.”
The 200 West facility is one of Hanford’s six pump-and-treat systems, with five smaller facilities located along the Columbia River. Collectively, the systems have treated more than 2 billion gallons of contaminated groundwater annually for nine consecutive years, with crews on track to make it a decade in fiscal year 2024, which ends Sept. 30.
Currently the 200 West facility alone treats more than 1 billion gallons of groundwater each year on the Central Plateau. Expansion of the system will allow for as much as 650 million additional gallons of groundwater to be treated annually.
The extraction wells pump contaminated water from the aquifer, which can be up to 200 feet below the surface in some areas. The water moves through the system, which removes contaminants using specialized resins, air stripping and granular activated carbon. The treated water is then injected back into the ground and helps push untreated groundwater toward the extraction wells, continuing the cycle.
“Our team expects to begin connecting to some of the extraction wells this month, with construction and installation of the new pipelines completed later this spring, a significant acceleration over the initial plan,” said Bill Barrett, Central Plateau Cleanup Company’s chief operating officer. “I’m proud of our continued focus and commitment to finding efficiencies in cost and schedule as we advance this critical expansion effort.”
The full expansion project is expected to be completed by September.

PADUCAH, Ky. — Each March, EM takes an opportunity to celebrate and highlight the extraordinary achievements and contributions of women across the DOE complex.
This year, women who work at the Paducah Site shared their stories and reflected on the influences of women throughout the 70-plus-year history of the site in a special video feature as part of Women’s History Month.
“You see that example and it encourages you and you just want to continue to carry that on,” said Stacey Marinelli, reflecting on the impact women have made at Paducah. Marinelli is an engineering manager with Swift and Staley, the site's infrastructure support services contractor.
 Thanks in part to the contributions from women across the DOE complex, including Paducah, today women make up nearly half of United States workers in the fields of math and physical science, according to the U.S. Census Bureau. In 2023, DOE reported women accounted for more than half of new hires throughout the U.S. energy sector. These tremendous strides would not be possible without the dedication and perseverance of the women who set the stage for future generations.
“Three of the four contractors at the Paducah Site are led by women, which would have been unheard of when the plant was built in the 1950s,” said April Ladd — herself, the second-ever female lead at the Paducah Site. “As I started my career, the women who mentored me had a huge impact. Those women have my deepest gratitude for stepping up in a male-dominated industry and leading by example.”
-Contributor: Dylan Nichols
 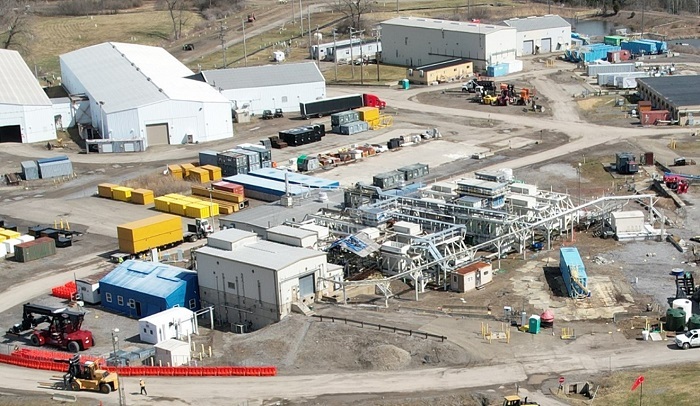 A tank where EM crews performed a video inspection is located in this grouping of underground waste tanks at the West Valley Demonstration Project.
WEST VALLEY, N.Y. – EM crews recently completed a virtual inspection of an underground tank that once stored liquid waste from spent fuel reprocessing operations at the West Valley Demonstration Project in the 1960s and ‘70s.
The work is part of an ongoing effort by EM and its West Valley cleanup contractor to better characterize residual waste, including sludge sampling and analysis. Results of the analyses will help determine disposition alternatives for the remaining content in the tank.
“Obtaining better samples is an important part of the characterization process,” said Stephen Bousquet, West Valley assistant director of Project Management. “Better samples lead to improved characterization, which leads to safer planning and execution. Comprehensive planning combined with solid information leads to a safe and successful outcome.”
EM crews had retrieved and solidified waste from that tank and two others through a process called vitrification from 1996 to 2002. Over 98% of the curies were removed from the waste tanks and vitrified. A curie is a unit used to measure the intensity of radioactivity in a sample of material. The 278 stainless steel canisters of resulting vitrified waste are being held at a temporary onsite storage pad until a permanent repository is available for their disposal.
For that vitrification effort, workers had neutralized the waste from the tank recently inspected, known as 8D-4, and blended it with other high-level waste in a second, larger tank called 8D-2. That allowed crews to use Tank 8D-4 to support vitrification efforts. The vessel received condensate and other liquids from vitrification.
Following vitrification activities, EM crews used the 14,300-gallon Tank 8D-4 to support deactivation of the site’s Vitrification Facility, which EM crews successfully demolished in 2018. The tank currently has about 3,900 gallons of residual liquid waste or sludge from the facility deactivation.
Although EM had completed initial liquid and sludge sampling from the tank in 2012, an additional archived sludge sample was shipped offsite for analysis last year. Additional samples were needed to better characterize the tank’s content for future disposition and cleanup. The camera inspection provided additional insight on the liquid level and depth of the sludge, which will help workers obtain better depth sludge samples for offsite analysis.
EM acquired a high-definition, radiation-resistant video camera and light assembly used in nuclear and non-nuclear applications. The camera, which also has pan and tilt capabilities, was lowered into the tank with sleeving to minimize camera and cord contamination. Once workers obtained video footage inside the tank, the camera was removed, surveyed as clean and released for future use.
Three liquid samples were sent offsite for analysis last month. More samples are expected to be dispatched for analysis.
“Our team continues to use their collective knowledge to find ways to improve processes, planning and execution of challenging work,” said Peggy Loop, manager of Waste and Site Operations for EM's West Valley cleanup contractor, CH2M HILL BWXT West Valley. “Comprehensive planning improves safety, quality and compliance.”
-Contributor: Joseph Pillittere
 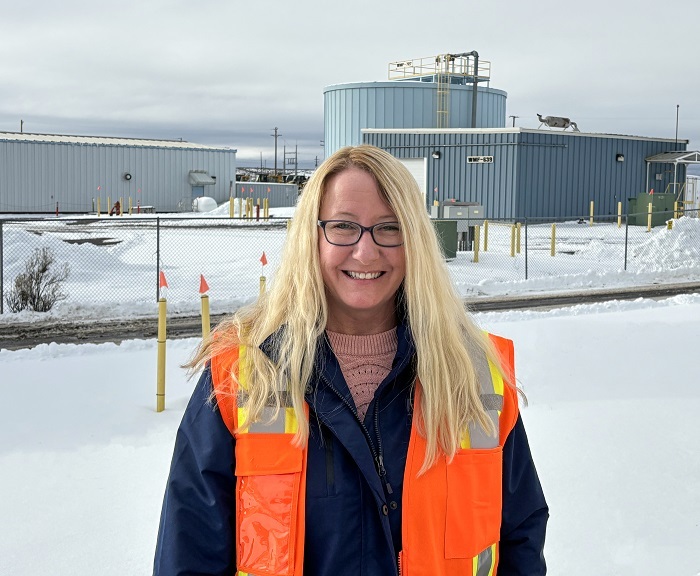 Advanced Mixed Waste Treatment Project Transportation Manager Rachelle Hubler has supported Idaho Cleanup Project contractors for 22 years and helps ensure transuranic waste shipments safely depart Idaho.
Manager reflects on 22-year career at site, including variety of roles and commitment to regulatory compliance, environmental safety
IDAHO FALLS, Idaho — Rachelle Hubler has made a career supporting EM’s cleanup contractors at the Idaho National Laboratory (INL) Site’s Advanced Mixed Waste Treatment Project (AMWTP), where she has been a driving force behind the facility’s success for 22 years.
Hubler started at AMWTP in 2002, a year before operations began at the facility, and her career is marked by diverse roles and a dedication to ensuring regulatory compliance and environmental safety.
“I have had the opportunity for multiple job assignments on this project, from working in environmental, safety and health, to packaging and transportation operations,” Hubler said.
 Each of those functions plays an integral part in the mission at AMWTP. The focus of work at the facility is to characterize, treat, package and ship transuranic (TRU) waste that was sent to and stored on the INL Site during the Cold War. AMWTP’s mission ensures long term protection of the Snake River Plain Aquifer.
In her current role as AMWTP transportation manager, Hubler orchestrates the shipment of TRU waste by navigating a complex web of regulations, a role she has held for 12 years and describes as both challenging and fulfilling.
“I manage a team that is responsible for packaging and transportation regulatory compliance in accordance with the U.S. Department of Transportation, the DOE, Environmental Protection Agency regulations and Nuclear Regulatory Commission requirements for all shipments that leave our facility,” Hubler said.
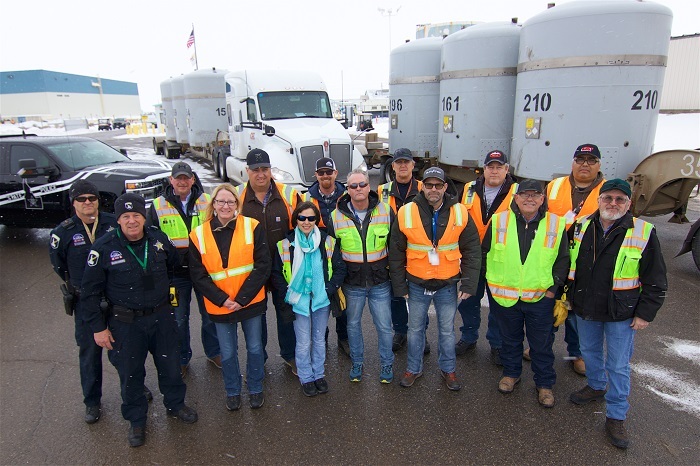 Rachelle Hubler and other members of the Advanced Mixed Waste Treatment Project Packaging and Transportation team pose with Idaho State Police officers in front of a transuranic waste shipment before it departs for the Waste Isolation Pilot Plant.
Meticulous attention to detail ensures each shipment is executed compliantly as employees move through dozens of steps. Hubler says that efficiency is refined by a dedicated team and years of experience.
“I have seen a huge reduction in our waste footprint during the last 22 years because we continuously look for opportunities to improve,” Hubler says. “I am proud to be part of a team of highly qualified and dedicated people who work together to solve challenges.”
These efforts are being rewarded by results, as more than half of all the waste emplaced at EM’s Waste Isolation Pilot Plant (WIPP) in New Mexico originated from AMWTP. In addition, more than 7,000 TRU waste shipments have left AMWTP since operations began there in 2003, traveling a collective 10 million miles between eastern Idaho and New Mexico. Recently, AMWTP completed the largest annual waste reduction in a decade.
Hubler emphasizes that continued AMWTP success relies on the strength of EM’s collaborative partnerships at the state and federal levels.
“Regulated shipments require a large support group. I work closely with many different organizations, including WIPP transportation personnel and the Idaho State Police,” she says. “These partnerships are critical to keeping a steady backlog of shippable inventory, ensuring our shipping equipment is safe and meeting WIPP’s shipping schedule.”
Much work remains, but Hubler is undaunted.
“I look forward to continuing successful shipments to WIPP, meeting our commitment to the people of Idaho and seeing that last TRU waste shipment depart Idaho for WIPP.”
-Contributor: Carter Harrison
RICHLAND, Wash. — An employee with EM Hanford Site 222-S Laboratory contractor Navarro-ATL recently encountered a chemical that required removal from the site by the local explosive ordnance disposal (EOD) unit after the chemical was placed in a safe configuration. Workers executed established procedures and practices to ensure the safety of the sample and the workforce throughout the process.
Navarro-ATL has been stabilizing and transporting aged chemicals to offsite treatment, storage and disposal facilities since the start of its contract in 2021. The contractor expects all aged chemicals to be offsite by the end of this year.
"The safe analysis of high-level waste samples is the priority of our operation at the 222-S Lab to support risk reduction in the cleanup mission," said Robert Schroeder, Analytical Operations director for Navarro-ATL. "We balance the workload to maintain that priority against the need to address the backlog of chemicals leftover from years of past laboratory operations."
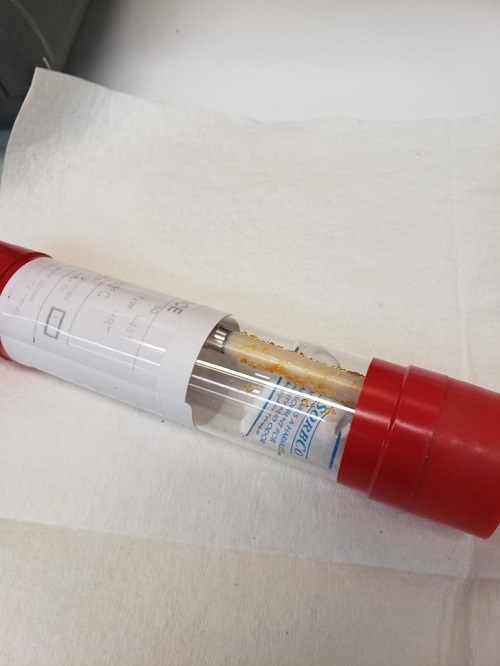 |
|
The appearance of crystals within this vial indicates that the chemical inside may have reacted with air, resulting in a potentially dangerous situation at the Hanford Site requiring the vial to be taken offsite for safe disposal by the local explosive ordnance disposal unit. |
On Feb. 20, a lab worker preparing aged chemicals for offsite shipment encountered a vial which contained a small amount of aged nonradioactive chemicals awaiting disposition.
The worker noticed that crystals had formed within the vial, indicating the chemical inside may have reacted with air, creating a potentially dangerous situation.
The worker immediately stopped work and followed procedures for the abnormal condition, including exiting the area and notifying operations management.
As a matter of caution, operations management evacuated workers from the areas adjacent to the chemical location and notified the Hanford Emergency Operations Center and Hanford Fire Department. Fire department staff went to the laboratory and determined that the quickest and safest means of disposition was to contact the local EOD unit to move the chemical offsite for destruction. Based on the worker’s quick response to the abnormal condition, the EOD unit removed the vial from the site, and work resumed at the laboratory within hours.
"The worker's swift action and the contractor's decision to contact the Emergency Operations Center for immediate removal was the right approach to this abnormal condition," said Paul Schroder, Hanford deputy assistant manager for Tank Waste Operations. "Safety is always the priority, as it was in this situation."
Work done at the 222-S Laboratory represents a critical component of Hanford Site cleanup since it is the primary onsite laboratory for analyzing both radioactive and nonradioactive samples supporting all Hanford projects.
 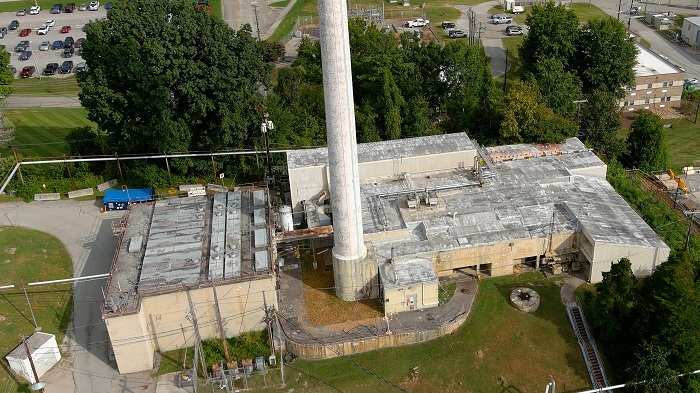 An aerial view of a filter house, fan house and 200-foot-tall exhaust stack that provided support to the Graphite Reactor, which is located about 100 feet away from these facilities.
OAK RIDGE, Tenn. — EM team members are priming three support facilities at Oak Ridge National Laboratory (ORNL) for teardown in the near future.
Oak Ridge Office of Environmental Management (OREM) cleanup contractor UCOR is deactivating the Graphite Reactor ancillary facilities. The buildings include the filter house, or Building 3002, fan house, or Building 3003, and exhaust stack, or Building 3018. They were previously used to filter and release exhaust from Graphite Reactor operations.
Their removal will continue OREM’s transformation of ORNL’s central campus, eliminate hazards and enhance visitor access to a historic landmark.
The oldest reactor in the world, the Graphite Reactor was designated a historic landmark in 1966 and is a key component of the Manhattan Project National Historical Park. It was the first facility built at ORNL during the Manhattan Project, and it will remain for visitors to learn about the history of the site.
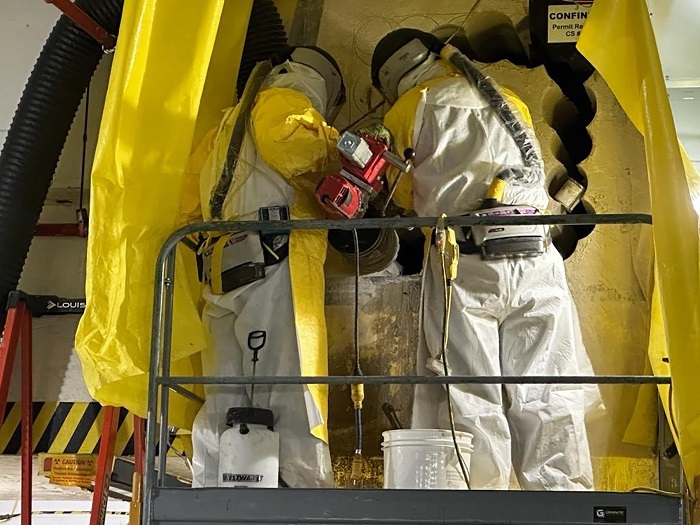 Crews drill to open access to an air duct that connects a fan house to an adjacent stack to perform required characterization work.
Constructed in 1948, the filter house filtered air from the air‐cooled Graphite Reactor prior to exhaust through the fan house and adjacent stack. Building 3003 housed the fan room, providing ventilation for the reactor and exhausting to the 200-foot-tall stack, which dates to 1943.
Maneuvering equipment to support deactivation has been challenging. The ancillary facilities are located on a hill approximately 100 feet from the reactor and within 20 feet of a fence line for a neighboring operational facility.
Much of the work throughout last year involved crews sampling the buildings and ducts. This characterization work supports future open-air demolition of the facilities.
Ready access was not available to Building 3002, so crews created an access door to enter and conduct sampling. Crews also drilled access into a duct connecting Building 3002 and Building 3003, enabling sampling crews to also initiate characterization of this area.
 Teams inside a filter house bag HEPA filters for disposal. The filters were used to capture contamination when the building was in use.
Once crews had access inside Building 3002, they conducted deactivation activities, including the removal of numerous filters. They took out HEPA filters and hundreds of contaminated rock wool filters that were originally thought to be removed.
With the filters out, employees are preparing to decontaminate Building 3002’s interior. That process includes vacuuming and using a solution for overall decontamination and again for targeted “hot spot” decontamination. The final step involves applying a fixative to prevent the spread of contamination during demolition.
Additionally, the team has started planning to place compressive low-strength material, which is a cement-like substance, in a duct between the Graphite Reactor and Building 3002 to isolate the facilities from each other prior to demolition.
The upcoming work moves the facilities closer to demolition, planned for next year.
-Contributor: Carol Hendrycks
 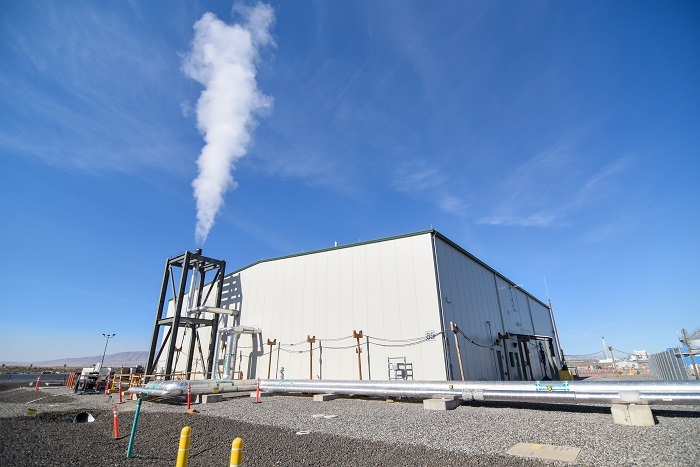 A grant from the Department of Energy’s Assisting Federal Facilities with Energy Conservation Technologies Program will partially fund the replacement of this diesel-powered steam plant on the Hanford Site with an electric one. The steam plant will supply steam for waste treatment processes at the site’s Waste Treatment and Immobilization Plant. The electric steam plant has the potential to save the Department millions of dollars in energy costs per year when it’s fully operational.
RICHLAND, Wash. — Plans to replace diesel-generated steam with electrically generated steam at the Hanford Site’s Waste Treatment and Immobilization Plant (WTP) are getting a funding boost from a recent $5 million DOE Assisting Federal Facilities with Energy Conservation Technologies Program grant.
The grant will partially fund the addition of a steam plant that uses electric boilers — instead of the current plant that uses diesel-powered boilers — to supply steam for WTP waste treatment processes.
Hanford’s tank waste treatment mission is vital to site cleanup, but energy intensive. This grant will allow Hanford to significantly reduce carbon emissions by substituting electric boilers for the diesel-powered boilers, with potential savings to the government of millions of dollars a year in energy and maintenance costs. The addition of an electric steam plant for WTP will also allow Hanford to make significant progress toward achieving the net-zero emissions goals of an executive order aiming to catalyze clean energy industries and jobs through federal sustainability.
“We’ll see a triple payback because, thanks to the grant, we can now free up $5 million in funding that would’ve been earmarked for the project,” shared Elaine Porcaro, EM’s chief engineer at Hanford who submitted the grant application. “Once the electric boilers are installed, we’ll save millions more per year in energy cost savings. We can do a lot with those cost savings every year by reinvesting it in cleanup.”
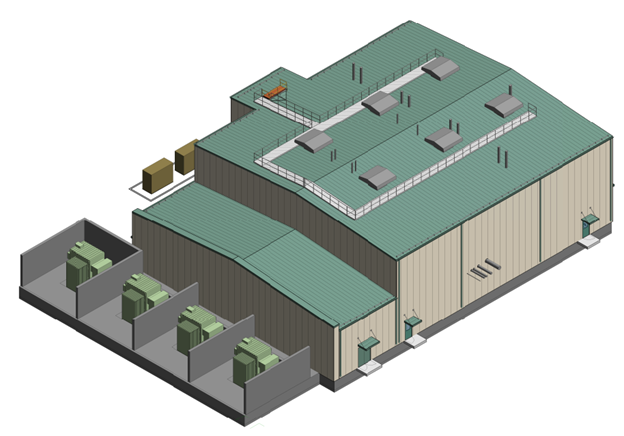 This conceptual sketch shows a preliminary design for a proposed electric steam plant at the Hanford Site. The plant will use electric boilers instead of the current diesel-powered ones to generate steam for the site’s Waste Treatment and Immobilization Plant.
Much of the data Porcaro used in Hanford’s grant application came from a study developed by Energy Manager Christian Seavoy, with Hanford contractor Hanford Mission Integration Solutions. Seavoy’s study looked at Hanford’s potential energy usage and carbon emissions over the next 15 years and found that replacing the diesel boilers with electric ones would help Hanford reduce its carbon footprint by 43.3 million kilograms of carbon dioxide per year, or the equivalent of taking 9,636 gas-powered cars off the road for a year.
“The clean and affordable power available here at Hanford really works to our benefit in this situation because the costs to operate an electric steam plant will be so much lower than fuel costs for a diesel-powered plant,” said Seavoy. “Plus, we have an opportunity to drastically reduce our emissions. We can really make a big difference.”
-Contributor: Shane Edinger
RICHLAND, Wash. — EM’s Office of River Protection awarded Hanford Site Waste Treatment and Immobilization Plant contractor Bechtel National Inc. (BNI) approximately $9.5 million, or about 92%, of the available fee for work performed on the High-Level Waste (HLW) Facility last year.
EM releases information relating to contractor fee payments — earned by completing the work called for in their contracts — to further transparency in its cleanup program.
BNI’s performance was evaluated against seven subjective fee criteria. The contractor received four “excellent” and three “good” performance ratings for those criteria and an overall performance rating of “excellent,” according to the award fee determination scorecard.
Noteworthy performance in these areas included the following:
- Established a strong and highly experienced senior HLW Project senior leadership team and made significant progress in establishing corporate partnerships to leverage broader industry expertise for completion of the HLW Facility design;
- Initiated deployment of a fully integrated, multi-functional, integrated team of qualified and experienced personnel, including engineering, nuclear safety, procurement, construction, startup, commissioning and operations;
- Completed a comprehensive update to the HLW Facility code of record; and
- Strengthened the leadership team supporting the HLW Facility and consistently demonstrated effective, open and transparent communications.
Areas for improvement in BNI’s performance include the following:
- The efficiency and timeliness of the procurement process for plant equipment, plant material and construction subcontracts.
- The timeliness of construction material awards and resolution of field changes to support schedule achievement for planned construction activities.
View the BNI fee determination scorecard here.
|