 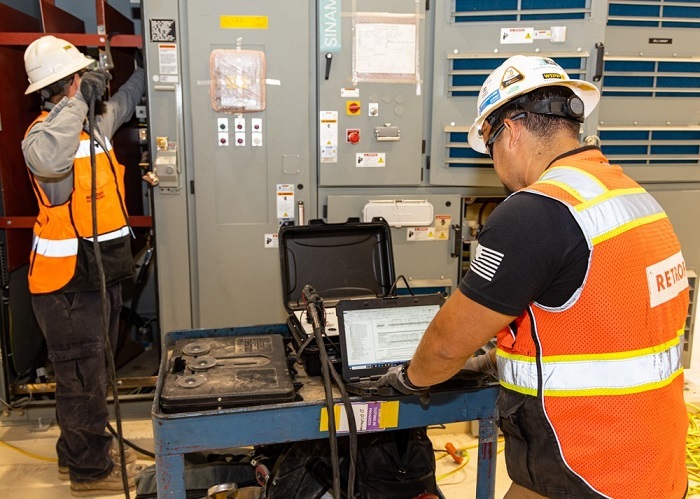 Trae Jones, left, and Andrew Sauceda of subcontractor Electrical Reliability Services test electrical circuits during commissioning of the Waste Isolation Pilot Plant’s Safety Significant Confinement Ventilation System. The start of the system’s commissioning activities meets an EM 2023 priority.
CARLSBAD, N.M. — The Waste Isolation Pilot Plant (WIPP) workforce recently met an EM 2023 priority when they began commissioning the site’s new large-scale ventilation system, also known as the Safety Significant Confinement Ventilation System (SSCVS).
When completed and online, the SSCVS facility — the largest containment ventilation system in the DOE complex — will significantly increase airflow to the WIPP underground, the nation’s only deep geological salt repository for defense-related transuranic (TRU) waste.
Commissioning kicked off last month as crews began testing the first set of electrical cables that will supply power to SSCVS mechanical equipment, such as motors, fans and massive air filtration units.
“This achievement is the culmination of many people’s efforts to support the engineering, procurement and construction of WIPP’s SSCVS project,” said Ralph Musick, Capital Asset Projects manager for Salado Isolation Mining Contractors, WIPP’s management and operations contractor. “Initiating commissioning is a careful, step-by-step process to eventually integrate the SSCVS into daily WIPP operations.”
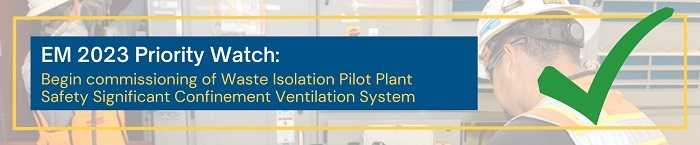 As facility construction nears completion, key systems are individually turned over to commissioning for methodical testing to ensure each component and system can be energized and functions as designed. When system testing has been completed, integrated testing is performed to assure that all components of the facility work together properly. After all testing, the facility is handed over to trained WIPP operations personnel to bring the new facility online.
The SSCVS works in tandem with a new air utility shaft, also under construction at WIPP. The shaft sends additional air into the 2,150-foot-deep WIPP underground repository, and the SSCVS pulls air through the repository, removes salt and filters the air before it’s released to the environment. When fully online, the new ventilation will increase underground airflow from 170,000 cubic feet per minute (cfm) up to 540,000 cfm. Increased airflow will allow for simultaneous underground waste emplacement, mining and bolting activities. Bolting controls the movement of salt rock — known as salt creep — in the WIPP underground.
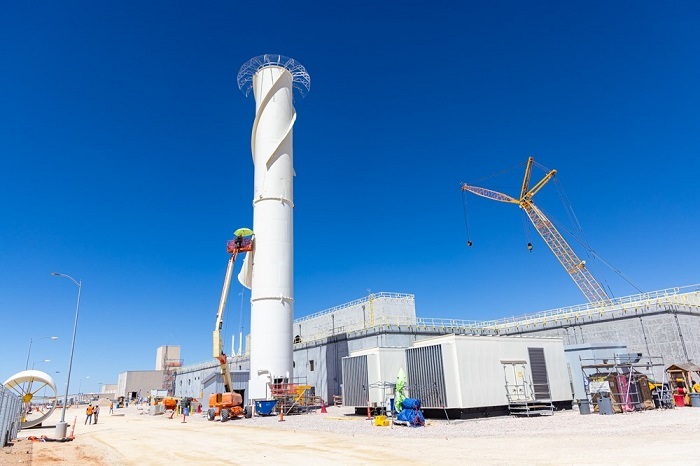 A 125-foot-tall environmental exhaust stack towers over the New Filter Building, one of two buildings that make up the Safety Significant Confinement Ventilation System at the Waste Isolation Pilot Plant.
SSCVS – a ‘safety first’ design
The system serves as an added safety defense in the unlikely event of a radiological incident in the WIPP underground by directing airflow from the underground facility to a series of high-efficiency particulate air (HEPA) filtration units.
“The SSCVS will enhance the quantity, and quality, of air flow for our workforce in the WIPP underground mine,” said Michael Gerle, Environmental Regulatory Compliance director for EM’s Carlsbad Field Office. “Additionally, the new infrastructure will ensure our operations remain safe for the environment and the public.”
The SSCVS project includes two primary buildings, the Salt Reduction Building and the New Filter Building. The former pre-filters salt-laden air coming from the WIPP underground, while the latter has fans and HEPA filtration to further remove contaminants from the exhaust air.
-Contributor: George Rangel
 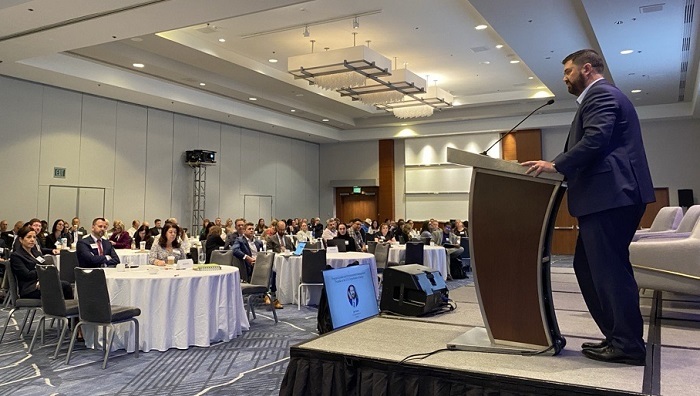 EM Principal Deputy Assistant Secretary Jeff Avery addresses attendees duing the 22nd Annual Intergovernmental Meeting with the U.S. Department of Energy on Nuclear Weapons Waste Cleanup.
MINNEAPOLIS — The 22nd Annual Intergovernmental Meeting with the U.S. Department of Energy on Nuclear Weapons Waste Cleanup brought together EM, local, state and tribal officials from across the country last week to discuss how they can advance the cleanup mission.
EM and other DOE senior leaders participated in discussions about a variety of topics, including priorities, strategic communications, technology innovation, waste transportation, climate resiliency, cleanup budgets and reuse of former DOE land.
EM officials addressed questions and concerns and provided updates on the status of cleanup at the 15 remaining sites, planning for the future workforce, clean energy development opportunities, protection of cultural and historical landscapes, and an emerging contaminant migrating into the environment from chemicals used in all types of materials called per- and polyfluoroalkyl substances (PFAS). Attendees also participated in an interactive budget development exercise.
In his plenary address, EM Principal Deputy Assistant Secretary Jeff Avery reflected on his first year at EM and noted that the cleanup program’s success is due to the efforts of many, including stakeholders and their meaningful engagement and input.
“EM is fortunate that our sites are surrounded by, truly, a cadre of leaders who understand the cleanup mission and have always been ready to pitch in,” said Avery. “Your communities have served our nation for decades in support of national security. Your communities also hold great potential for helping to solve the most pressing challenges as we look ahead — preserving peace, boosting clean energy, creating good paying jobs and protecting environmental and cultural resources.”
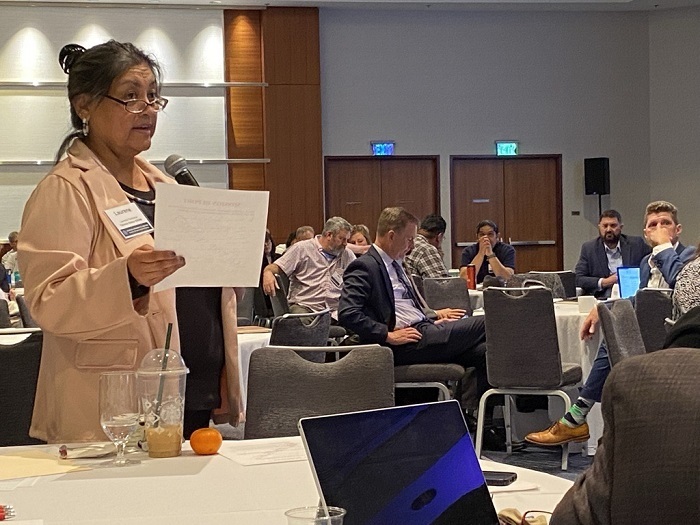 Yakama Nation Program Manager Laurene Contreras speaks during the 22nd Annual Intergovernmental Meeting with the U.S. Department of Energy on Nuclear Weapons Waste Cleanup.
Avery highlighted significant accomplishments, including the startup of the Integrated Waste Treatment Unit at the Idaho Cleanup Project; the safe and successful demolition of the first gaseous diffusion process building at the Portsmouth Site; and treatment of tank waste at the Hanford Site.
And just like safety, engagement requires constant vigilance and two-way communication, Avery noted.
“We are continuously looking for ways to strengthen relationships through open channels of communication and trust,” he said. “Of course, these conversations are not always easy. And there will not always be agreement across the board. But having the ability to address tough questions, appreciate different perspectives and have frank conversations can really make all the difference in the world.”
And that is exactly the intent of the two-and-a-half-day meeting that drew about 200 participants.
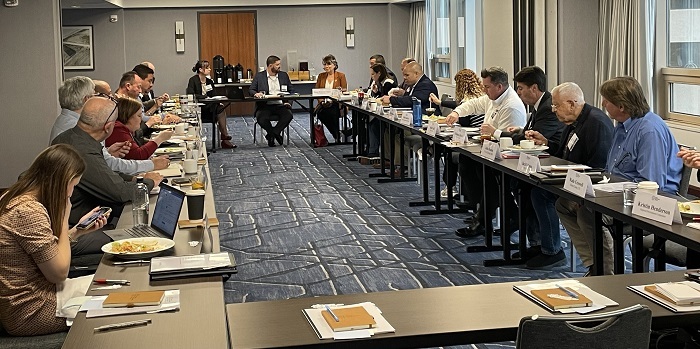 Members of the Energy Communities Alliance, pictured here, and other stakeholder groups held individual meetings prior to the 22nd Annual Intergovernmental Meeting with the U.S. Department of Energy on Nuclear Weapons Waste Cleanup, providing the location for meaningful discussions.
The annual meeting is a forum for state, local, tribal and federal officials to discuss priorities and strategies for managing and storing defense nuclear waste and for remediation of production sites. It's a collaborative effort led by the National Governors Association Federal Facilities Task Force, and national intergovernmental groups partnering in, and affected by, the ongoing cleanup of defense related nuclear waste, including the:
Looking to the future, Avery discussed EM’s upcoming 2024-2034 Strategic Vision, which serves as a planning tool and framework of priorities for overcoming remaining challenges and achieving more cleanup in the coming decade. He encouraged the intergovernmental community to provide feedback in advance of the document’s release.
RICHLAND, Wash. — A member of the Hanford Site workforce is among a group of up-and-coming professionals under 40 who the National Safety Council (NSC) recently spotlighted as “Rising Stars of Safety” for demonstrating exceptional safety leadership.
Courtney Smith, an Occupational Safety and Industrial Hygiene Program manager with EM Richland Operations Office contractor Central Plateau Cleanup Company (CPCCo), was one of 36 individuals from eight countries and various industries who were honored for their commitment to innovation, collaboration and creating safer workplaces.
“Safety is not just a word, but a way of life at the Hanford Site,” said Stan Branch, EM Safety and Health Division director for the Hanford Site. “The Department and its contractors are committed to the highest safety standards and practices to protect our workforce, and Smith really exemplifies all those values.”
Smith was nominated in part for her role in designing and implementing CPCCo’s all-employee Healthy & Mission Ready Program. The initiative tasks project teams with creating videos, webpages and other activities to promote monthly health and safety topics, enhancing worker engagement and focusing on total worker health.
|
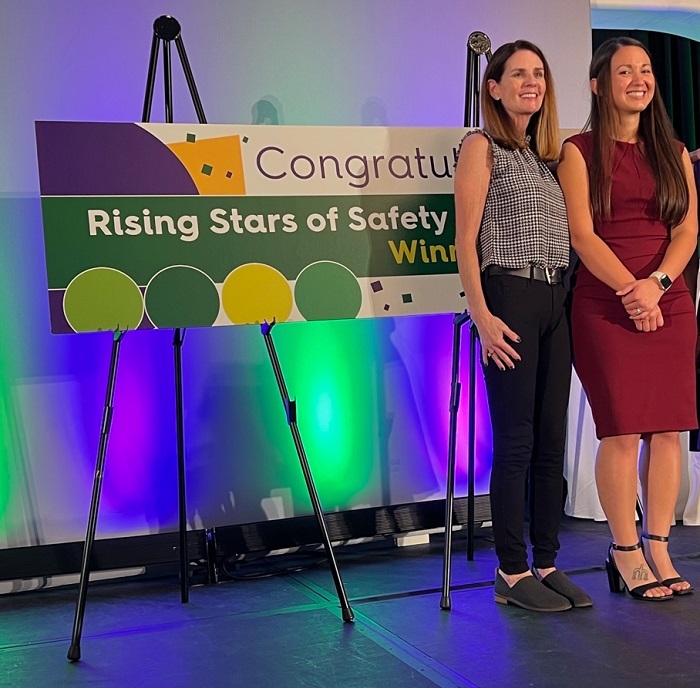 Courtney Smith, right, Occupational Safety and Industrial Hygiene Program manager for EM Hanford Site contractor Central Plateau Cleanup Company, was recognized as one of the National Safety Council’s “Rising Stars of Safety” at last month’s annual conference in New Orleans. Smith was joined at the conference by Megan Proctor, left, the company’s Environmental, Safety and Health director.
Smith also leads CPCCo’s partnership with the Safety & Health Management Program at Central Washington University, fostering connections with university students to share real-world safety and health experiences and innovations developed at the Hanford Site with the next generation of nuclear workers.
“Smith sets an extremely high bar for herself, her team and the entire workforce,” said Megan Proctor, CPCCo Environmental, Safety and Health director. “She leads by example by putting safety first and being the first to jump in to tackle a difficult task.”
Smith was happy to receive the council’s recognition and noted that the support and commitment of her team members is integral to her success.
“I am excited to be named an NSC Rising Star, but my success is attributed to the support and dedication of my amazing team,” said Smith. “They make safety their No. 1 priority. Safety really is a team effort.”
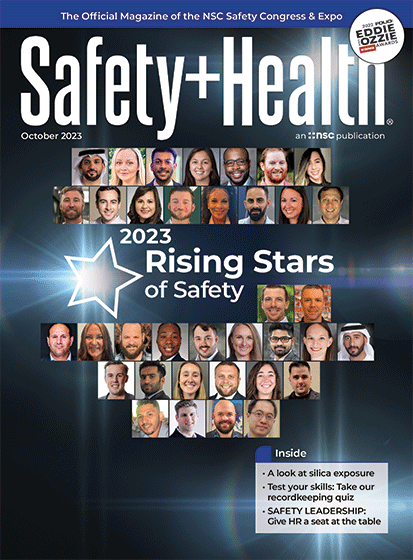 |
|
Courtney Smith was among 36 “Rising Stars of Safety” highlighted in the October issue of the National Safety Council’s Safety+Health Magazine. Smith is the Occupational Safety and Industrial Hygiene Program manager for EM Hanford Site contractor Central Plateau Cleanup Company. |
Smith and her fellow Rising Stars were recognized at an awards ceremony Oct. 24 in New Orleans, which was held in conjunction with the 2023 NSC Safety Congress & Expo, the nation’s largest gathering of safety and health professionals.
You can see the full Class of 2023 Rising Stars here.
-Contributor: Karisa Saywers
 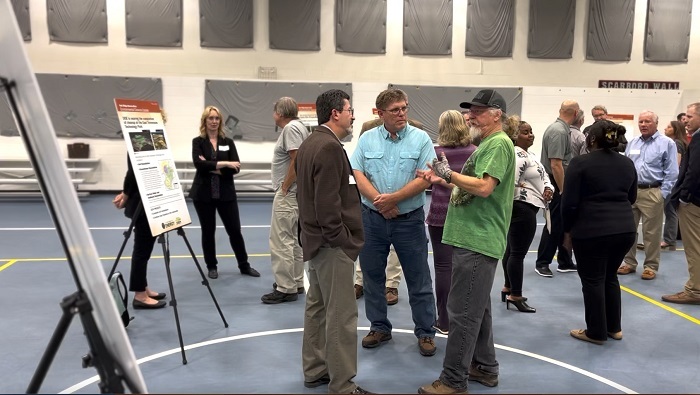 The Oak Ridge Office of Environmental Management and contractor UCOR recently hosted a two-hour public information session that provided community members an opportunity to hear about cleanup progress and ask questions to project managers overseeing the work.
OAK RIDGE, Tenn. — The Oak Ridge Office of Environmental Management (OREM) recently held an open house event, part of its ongoing commitment to keep the public informed about cleanup progress at the Oak Ridge Reservation, which is located in two counties in East Tennessee and near a population of more than 100,000 residents.
“We really want the community to come out and really take advantage of these opportunities,” said Sierra Generette, environmental justice and public engagement specialist with OREM cleanup contractor UCOR.
The two-hour event at a Scarboro Community Center gymnasium featured large posters showing graphics, photos and text explaining projects underway. Directors and project managers from EM and UCOR shared information and answered questions from the area residents.
Staff members from the Tennessee Department of Environment and Conservation were also on hand to speak with members of the public.
“They’re here to answer your questions, so if you’re looking at a poster and you may not know what’s going on, this is what they’re here for,” said Generette.
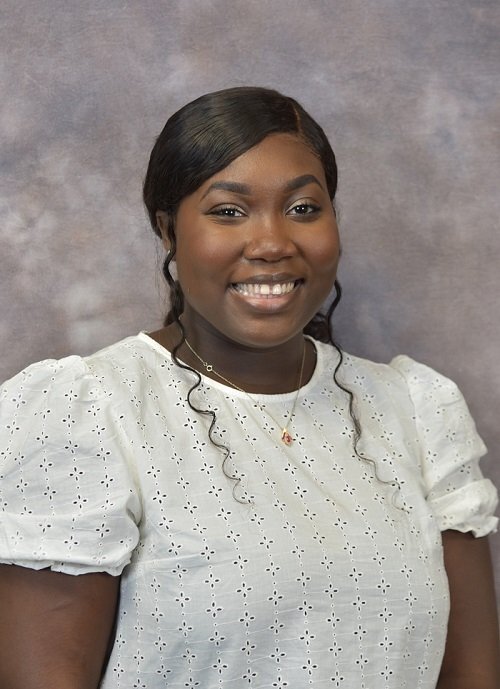 |
|
“We want to make sure that we’re not just talking to the community when there’s a regulatory decision or commenting period.”
-Sierra Generette, environmental justice and public engagement specialist with Oak Ridge Office of Environmental Management cleanup contractor UCOR
|
Information focused on OREM’s progress towards completing soil cleanup and developing groundwater remediation plans at the East Tennessee Technology Park, demolition at Oak Ridge National Laboratory, deactivation at the Y-12 National Security Complex and preparation for the construction of the Environmental Management Disposal Facility (EMDF).
This latest outreach event gave a much more comprehensive view of the Oak Ridge cleanup mission than OREM’s previous open house event, which centered on the EMDF and its role in providing the waste disposal capacity needed to continue cleanup efforts.
“We want to make sure that we’re not just talking to the community when there’s a regulatory decision or commenting period,” said Generette. “We want the community to feel like they’re safe, well-informed, and that they can have a one-on-one interaction with the people that work at our companies.”
OREM plans to continue hosting similar public information sessions, at least annually, to provide a forum where the community can hear about cleanup progress nearby and connect with leaders who oversee the work. Notices about such events will be posted on OREM’s website.
-Contributor: Summer Dashe
 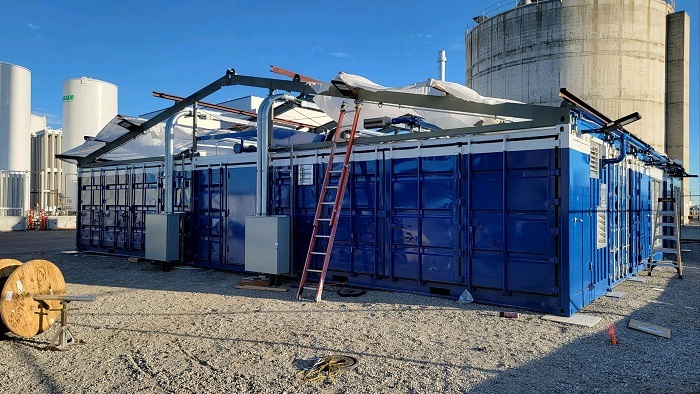 Crews recently installed a new nitrogen plant adjacent to the Integrated Waste Treatment Unit. Onsite generation of nitrogen will allow the plant to maintain steady-state operations.
IDAHO FALLS, Idaho — When EM's radioactive liquid waste treatment facility at the Idaho National Laboratory Site resumes operations early next year, it will be using nitrogen generated onsite, a reliable source of the gas necessary for mission completion.
Quite simply, the Integrated Waste Treatment Unit (IWTU) cannot run without nitrogen.
During the last year, a host of challenges affected the ability of IWTU to dependably receive daily shipments of the inert gas. Nitrogen is crucial to keeping the billions of tiny beads in the IWTU’s primary reaction vessel moving while liquid waste is injected into the super-heated vessel allowing the liquid to adhere to the beads. Nitrogen is also used to prepare the granulated activated carbon beds — which remove mercury from the treated sodium-bearing liquid waste — for operations, and other plant functions.
IWTU now has a turnkey, commercial nitrogen gas generator source, next to the facility, which will reliably provide the millions of cubic feet of high-purity nitrogen that the facility uses weekly during operations. Nitrogen is generated by simply separating the gas from ambient air.
“Having nitrogen generation right next to the plant allows us to have a constant, real-time supply of this gas for reliable, steady-state operations,” said Bill Kirby, senior director for liquid waste and fuels with EM cleanup contractor Idaho Environmental Coalition.
The new electric motor-driven system not only resolves the challenges of relying on offsite sources for nitrogen, it also is significantly more environmentally friendly. During its peak usage during startup and shutdown, IWTU required as many as four tanker-truck loads of nitrogen delivered daily. The switch to an onsite nitrogen source not only eliminates carbon monoxide from the diesel trucks delivering the product, but also removes six diesel-powered compressors used in the prior system.
“We have also partnered with a small business to provide the system as well as the maintenance to keep it operational,” said Kirby. “Their level of customer service is consistent with what we’ve noticed with other small businesses we employ to complete the overall cleanup mission in Idaho.”
Following five months of operations, IWTU is in a maintenance phase to replace the carbon in a downstream vessel that removes mercury during the steam-reforming process.
Starting with its launch in April, IWTU has converted more than 68,000 gallons of sodium-bearing waste from nearby underground waste tanks to a safer, granular solid. The treated material, which is about the size of coarse coffee grounds, was transferred to stainless-steel canisters and placed in concrete vaults for onsite storage.
-Contributor: Erik Simpson
 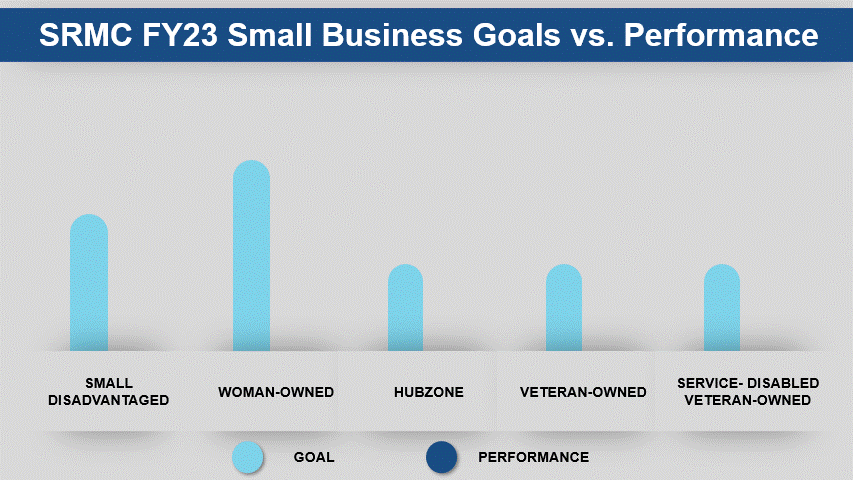 The liquid waste contractor at the Savannah River Site exceeded EM’s small business contracting goals, including all socioeconomic small business category goals, for fiscal year 2023.
AIKEN, S.C. – The liquid waste contractor at the Savannah River Site (SRS) awarded approximately 80% of its subcontracted work to small businesses in fiscal year 2023 (FY23), surpassing EM’s goal for the 12-month period by more than 30%.
This achievement means that out of the approximately $183 million committed to suppliers in FY23, Savannah River Mission Completion (SRMC) awarded more than $150 million of goods and services acquisitions to small businesses.
SRMC also met all of EM’s other socioeconomic small business category goals, including awarding at least 20%, or $67 million, in subcontracts to women-owned small businesses. Other categories include small disadvantaged business, historically underutilized business zone, veteran-owned small business and service-disabled veteran-owned small business.
More than 19,000 purchasing actions were taken in FY23 to support SRMC’s subcontracting goals. Significant procurements awarded to small businesses include purchasing frit and empty 10-foot-tall stainless steel canisters for disposing vitrified waste at the Defense Waste Processing Facility (DWPF). Inside that facility’s melter, waste is mixed with a frit, or borosilicate glass, and heated until molten, then poured into the canisters to harden.
Other significant small business procurements include pumps for DWPF, chemicals used at the Salt Waste Processing Facility, rental equipment used in construction, concrete for underground waste tanks and tank closure and to support Saltstone Disposal Unit construction, project controls scopes of work, and modeling for process improvements.
According to SRMC Chief Administrative Officer Mark Barth, partnering with small businesses to procure critical equipment and services is necessary for completing the liquid waste mission.
“Our scope of work at the Savannah River Site requires unique support, and we get that from our small business vendors,” Barth said. “Working with regional, small businesses is a way that we can use our dollars to have a positive impact on the surrounding communities.”
Also in FY23, SRMC welcomed two new protégé companies to participate in SRMC’s Mentor-Protégé Program. WesWorks is a local, woman-owned small business that specializes in the planning, management and execution of large-complex contracts. DBD is a technical advisory firm that has helped SRMC develop computer models to identify process or facility improvements to advance the liquid waste mission. The new protégés join established protégé Columbia County Concrete, a local, woman-owned small business.
According to SRMC Small Business Program Manager Ashley Hannah, the new protégés support EM’s mission.
“Having a mentor-protégé relationship with the capabilities of these small businesses is mutually beneficial for the mentor, the protégé and the Department of Energy,” Hannah said. “We are proud to support a program that maximizes opportunities for small businesses to conduct work for EM alongside SRMC.”
-Contributor: Lindsey Kennedy
 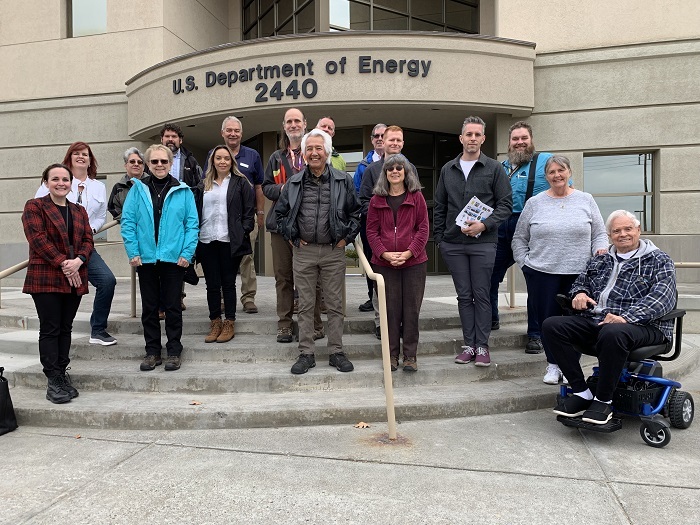 Hanford Advisory Board members were joined by several DOE officials for a tour of the Hanford Site.
RICHLAND, Wash. — New Hanford Advisory Board (HAB) members visited the EM-managed Hanford Site in October to learn about its history and cleanup progress.
Office of River Protection and Richland Operations Office Manager Brian Vance welcomed about a dozen board members during a driving tour, which included historic townsites, decommissioned nuclear reactors and other facilities used during Hanford’s plutonium production era.
HAB members also visited groundwater and soil remediation facilities, and the Waste Treatment and Immobilization Plant, which will vitrify, or immobilize in glass, millions of gallons of waste stored in Hanford’s underground tanks.
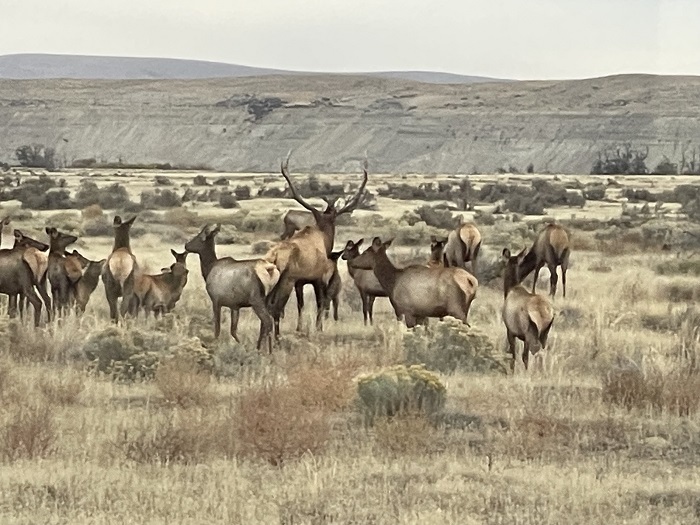 During their orientation tour of the Hanford Site, new Hanford Advisory Board members were surprised to see several elk herds migrating across the site to prepare for winter.
After the visit, HAB members met with senior leaders from each of the Tri-Party Agreement agencies — the DOE, U.S. Environmental Protection Agency and Washington State Department of Ecology — to discuss cleanup mission goals and priorities, helping the new members better understand their role in the process.
EM Senior Advisor William “Ike” White also welcomed the board members and thanked them for their participation.
“The real value in our citizen advisory boards is in providing a voice for our affected communities, providing opportunities for meaningful interactions that inform our policies and priorities for cleanup,” White said.
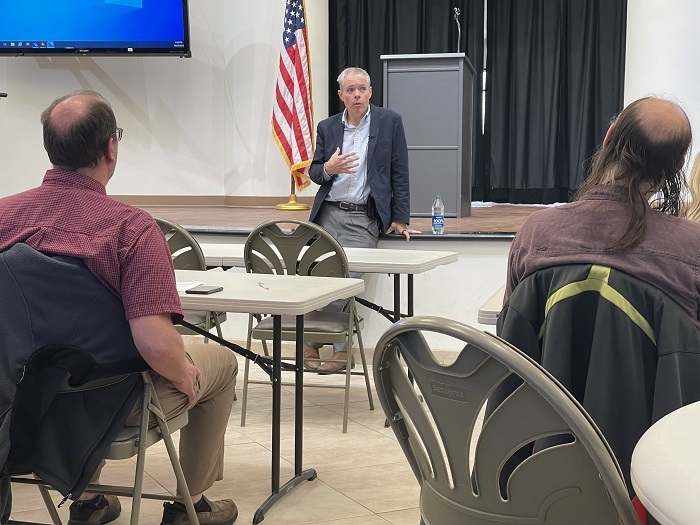 EM Senior Advisor William “Ike” White met with Hanford Advisory Board members as part of their board member orientation.
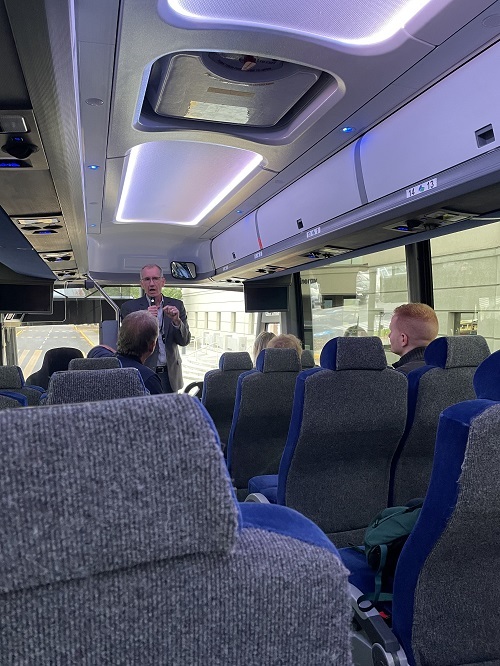 |
|
Brian Vance, EM’s Office of River Protection and Richland Operations Office manager, welcomed Hanford Advisory Board members during a recent driving tour of the Hanford Site. |
Brian Moreno, a new HAB board member representing the public-at-large, said he was struck by the sheer complexity and magnitude of the EM site compared to the rest of the country.
“While there is much riding on this project to be successful, I continue to be inspired by the transformational opportunities for our community that are yet to come,” Moreno said. “I'm excited about playing an active role in this conversation and how we set up our future generations for success.”
The HAB is the longest-serving site-specific advisory board in the EM complex. It was chartered in 1994, following the implementation of the Tri-Party Agreement in 1989. Board members provide consensus-based, policy-level advice to the three agencies to support cleanup progress.
-Contributor: MaryAnne Wuennecke
 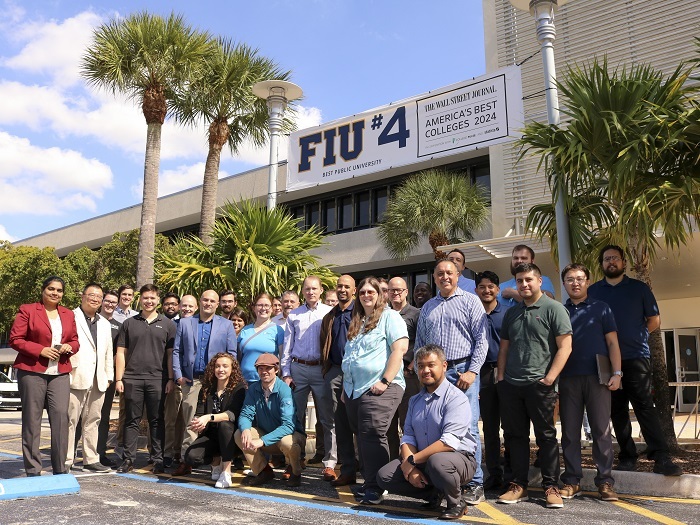 Members of the wearable robotics team gather for a photo at their recent meeting at Florida International University (FIU). They represent EM’s Technology Development Office; Sandia, Savannah River and Los Alamos national laboratories; Georgia Institute of Technology; FIU; Florida Institute for Human and Machine Cognition; and Washington River Protection Solutions.
MIAMI – Over 30 members of a team exploring the use of wearable devices to improve worker safety recently gathered at Florida International University (FIU) to discuss efforts to develop, evaluate and deploy the technology at EM cleanup sites.
FIU is among six organizations funded by EM to better understand the strains site workers face due to the physically challenging nature of their work, and to find solutions to reduce such impacts using wearable devices.
The wearable robotics program, which began in fiscal year 2020, is exploring the use of commercially available devices as well as custom solutions tailored to the unique needs of EM workers, such as compatibility with personnel protective equipment and operating in secure environments.
In a meeting with the team members, EM Office of Technology Development Program Manager Jean P. Pabón emphasized EM’s critical need to safeguard the health and safety of the workforce.
Pabón also acknowledged the team’s tremendous potential to develop innovative solutions to address EM’s challenges and needs at the field sites.
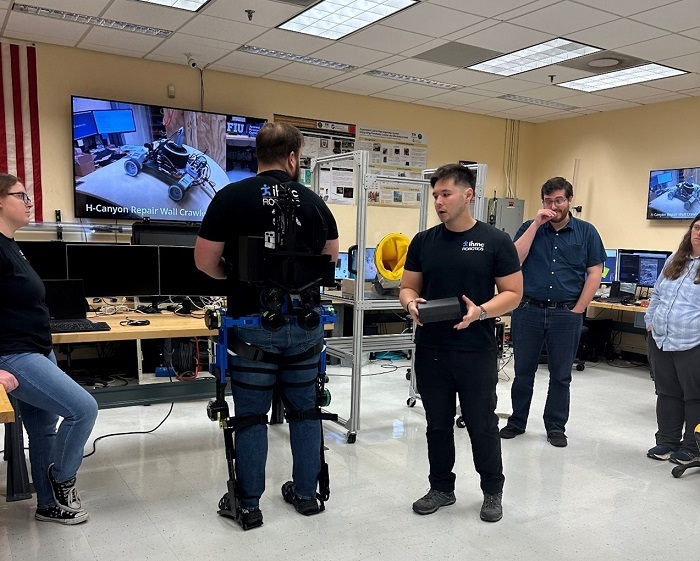 Florida Institute for Human and Machine Cognition employees exhibit a prototype for wearable robotics during the wearable robotics team’s visit to Florida International University.
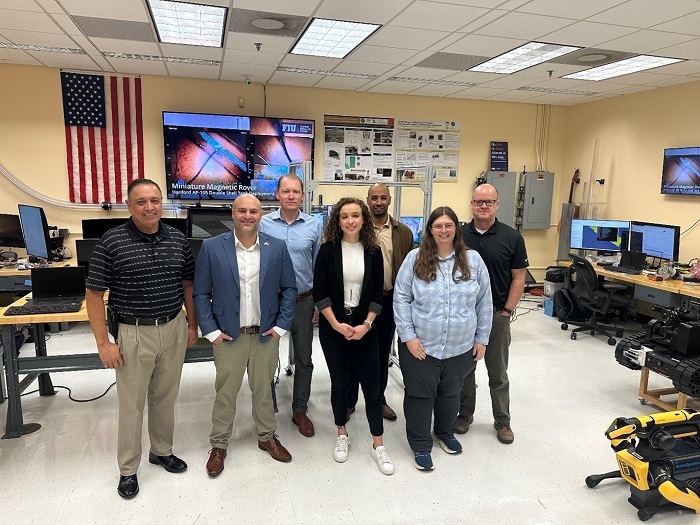 From left are Leonel Lagos, Florida International University; Jean P. Pabón, EM Office of Technology Development; Jason Wheeler, Sandia National Laboratories; Gwendolyn Bryan, Florida Institute for Human and Machine Cognition; Ani Mazumdar, Georgia Institute of Technology; Beth Boardman, Los Alamos National Laboratory; and Michael Leonard, Washington River Protection Solutions. Tanner Goins with Savannah River National Laboratory is not pictured.
In addition to FIU, the team includes representatives from Sandia National Laboratories, which leads the group’s efforts, Los Alamos and Savannah River national laboratories, Georgia Institute of Technology, and Florida Institute for Human and Machine Cognition (IHMC). Three employees from Washington River Protection Solutions, an EM Office of River Protection contractor at the Hanford Site in Washington state, also attended the meeting.
Team members provided updates on their work, addressed challenges and opportunities and discussed next steps in their efforts. They also participated in tours of the FIU laboratories, where many robotic development efforts for EM sites are underway.
“The team meets every month virtually, but these in-person meetings provide a unique opportunity to dive deeper into specific areas and to physically try on devices,” said Jason Wheeler, the Sandia project lead.
The group plans to continue meeting in person one or two times a year. Previous team meetings were held at Sandia and IHMC.
-Contributors: Leonel Lagos, Jason Wheeler
AIKEN, S.C. — Members of the Savannah River Site (SRS) workforce recently employed creative techniques to complete the vacuuming of spent nuclear fuel stored in an underwater basin to ensure continued processing of the fuel.
The fuel from foreign and domestic research reactors is safely stored in the L Area Disassembly Basin inside a former production reactor in the site’s L Area. The fuel is sent to the H Canyon at SRS for dissolution. Dissolution involves lowering the fuel into a nitric acid solution, which produces a liquid that is moved through the site’s liquid waste facilities to be vitrified, or made into glass, and safely stored onsite until a federal repository is identified.
L Area Operations Specialist Steve Osteen of Savannah River Nuclear Solutions (SRNS), the site’s managing and operating contractor, noted that a resin was deposited on a number of High Flux Isotope Reactor (HFIR) cores during L Area deionizer vessel operations in the early 1990s.
“The resin deposits rendered the cores unsuitable for dissolution and processing in H Canyon, which is the disposition path for this type of fuel,” Osteen said. “Our team had to come up with an innovative method for resin removal while the cores remained underwater to maintain adequate shielding from radiation.”
The resin is made up of tiny beads that trap radionuclides and help to remove radioactive ions from the basin water.
|
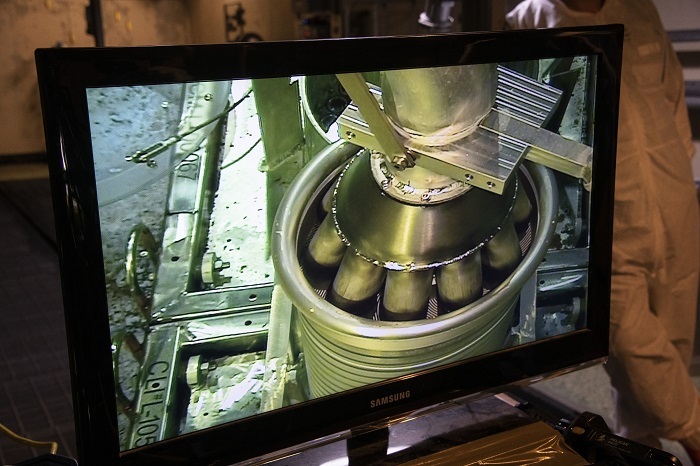 A team of Savannah River Site employees designed and installed a High Flux Isotope Reactor core cleaning station and vacuum tool to ensure continued processing of spent nuclear fuel stored in the site’s L Basin.
In 2020, a team of SRNS engineering, operations and construction employees partnered with scientists and engineers from the Savannah River National Laboratory to develop a methodology for removing the resin.
The team designed and installed an HFIR cleaning station and vacuum tool to be used with an existing basin vacuum system. HFIR cores were placed in the HFIR cleaning station, vacuumed and relocated, which allowed operators to vacuum the HFIR racks. By using this new process and associated tools, SRNS was able to recover 30 racks and add an additional 60 clean storage positions, and all HFIR cores have now been cleaned of resin.
“The ingenuity of this team in planning, designing and implementing new tools to allow for the vacuuming of the cores is commendable,” said L Area Facility Manager Neil McIntosh of SRNS. “The nearly three-year effort not only allows transfer to H Canyon of all HFIR cores currently stored in the basin but also allowed reclamation of all storage racks for future receipts.”
Now, the HFIR cores can be scheduled for dissolution and the basin can receive more cores without interrupting other operations.
“The ability of the SRNS team to always find a way to get the job done safely and efficiently is why they make a great workforce,” McIntosh said.
HFIR is the highest flux reactor-based source of neutrons for research in the U.S. using highly enriched uranium. The fuel elements, an inner and an outer element, together form a reactor “core.” The reactor is located at Oak Ridge National Laboratory in Tennessee.
 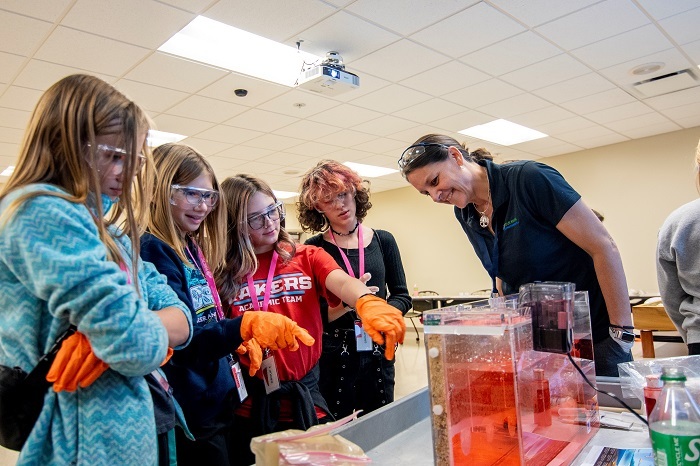 Four Rivers Nuclear Partnership Environmental Remediation Stewardship Manager Megan Mulry shows how groundwater aquifers are affected by contamination using a model at the STEM 4 Girls event.
PADUCAH, Ky. — As women account for about half of U.S. workers in the fields of math and physical science, EM’s Paducah Site continues to ensure young girls are exposed to opportunities in such STEM fields.
That’s why employees from Four Rivers Nuclear Partnership (FRNP), the deactivation and remediation contractor for the Paducah Site, showcased career possibilities during this year’s Paducah Area Chamber of Commerce STEM 4 Girls event. STEM stands for science, technology, engineering and math.
During the event, students explored hands-on activities, demonstrating many of the tools used in the deactivation and cleanup of the Paducah Site.
“It’s important for young women to see the career options available to them, especially those jobs that exist within our region,” FRNP Program Manager Myrna Redfield said. “The impact women who currently work at the site have on the next generation workforce through events like these can’t be understated and I am proud to be a part of an organization committed to providing an example to young girls in our community.”
 Four Rivers Nuclear Partnership Data Analyst Emily Coriell uses a robot to demonstrate how deactivation crews inspect piping at the Paducah Site during the STEM 4 Girls event.
Women in environmental sampling, nuclear safety, project engineering and data analysis roles at the Paducah Site spoke to girls at this year’s event about the importance of protecting the environment and highlighted new technologies in use at the site, including advancements in robotics for inspection of equipment.
“Events that allow our workforce to promote STEM careers, especially to young women, will help them become our future site leaders,” EM Paducah Site Lead April Ladd said.
Young people will have more opportunities to see how STEM fields translate into careers, Ladd added.
“DOE is encouraged with feedback we’ve received from these events and will continue to share the career opportunities at the Paducah Site with students throughout the region,” she said.
-Contributor: Dylan Nichols
|