 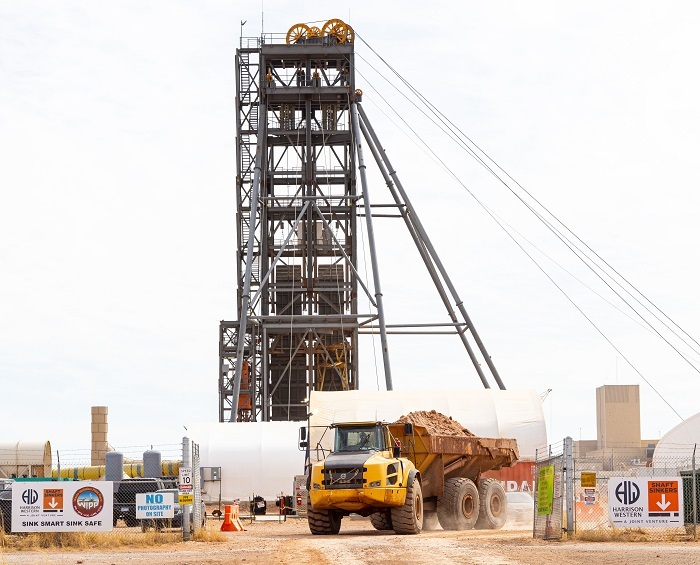 With the air intake shaft’s black headframe towering in the background, a truck hauls away salt excavated during 24-hour shaft-sinking operations at the Waste Isolation Pilot Plant.
CARLSBAD, N.M. – The Waste Isolation Pilot Plant (WIPP) recently marked a significant accomplishment when critical infrastructure that will supply air to the largest safety-related ventilation system in the DOE complex reached its final depth of 2,275 feet — after claiming an EM 2023 priority along the way.
The new air intake shaft — the underground waste repository’s largest utility shaft at 26 feet in diameter — supports the Safety Significant Confinement Ventilation System (SSCVS), which will increase underground airflow from 170,000 cubic feet per minute (cfm) to 540,000 cfm.
Increased airflow will allow for simultaneous waste emplacement, mining and bolting to take place in the underground at WIPP, the nation’s only repository for defense-related transuranic (TRU) waste. Bolting controls the movement of salt rock — known as salt creep — in the WIPP underground.
“Reaching this milestone is a real tribute to the crews who worked safely and compliantly around the clock,” said Mark Bollinger, EM Carlsbad Field Office manager. “Congratulations to the workforce on this big step toward the creation of more airflow in the WIPP underground, an important part of the new WIPP infrastructure.”
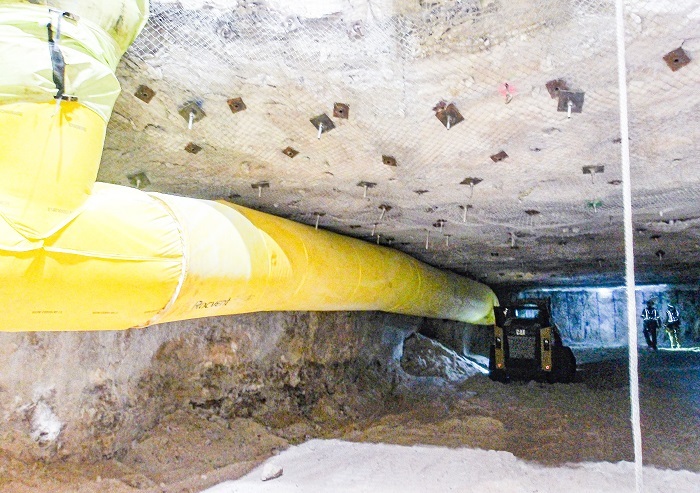 Above the utility shaft’s final depth of 2,275 feet, crews are already cutting horizontally into the salt to create connecting passageways, or drifts, to the Waste Isolation Pilot Plant mine.
Salado Isolation Mining Contractors (SIMCO), WIPP’s management and operations contractor, is overseeing the SSCVS and utility shaft projects. Crews from SIMCO’s subcontractor, the joint partnership of Harrison Western and Shaft Sinkers, reached the shaft bottom by working a 24/7 schedule to support the project.
“Completion to depth is a great achievement,” said Ken Harrawood, SIMCO president and program manager. “This milestone sets the stage for all of our future progress to the west, including Panel 11.”
The drilling crews reached the depth of the WIPP waste disposal rooms in early July, achieving the EM 2023 priority ahead of schedule. Horizontal passageways were created on either side of the shaft. These will be further mined to connect to the existing WIPP underground and provide access drifts, or connecting passageways, for new waste disposal panels that have been authorized at WIPP.
The final depth of the air intake shaft, at 2,275 feet, provides space below the repository level for work areas and infrastructure, such as communications and electricity, that will support mining activities.
Located in Southeast New Mexico about 26 miles east of Carlsbad, WIPP was constructed in the 1980s for disposal of defense-generated TRU waste. The repository is carved out of a 2,000-foot-thick salt bed formed 250 million years ago. TRU waste is disposed of 2,150 feet underground in rooms mined from the salt bed.
-Contributor: Roy Neese
 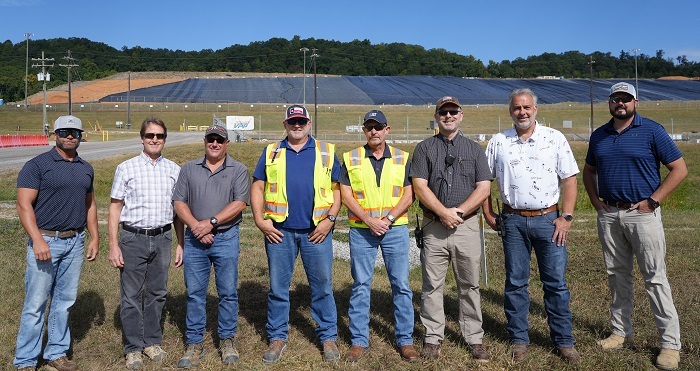 Oak Ridge cleanup contractor UCOR’s water management team at the Environmental Management Waste Management Facility. From left, Josh Pemberton, Patrick Mullen, Gary Buttry, Matt Hagenow, Tim Brown, Jeff Grindstaff, Wes White and Brandon Justice. Not pictured: Annette Primrose and Russell Hunsaker.
DOE bestowed three Sustainability Awards and an honorable mention last week to a trio of EM sites for achievements in innovative water management practices, strategic partnerships to strengthen the workforce, high performance sustainable building construction and water conservation.
Oak Ridge received two awards, the Office of River Protection (ORP) at the Hanford Site received one and the Paducah Site was given honorable mention. The awards were presented as part of DOE’s first Sustainability Summit.
Also at the event, the Department presented the Idaho Cleanup Project and Portsmouth Site with Green Fleet Awards. Read EM Update’s coverage of those two awards here.
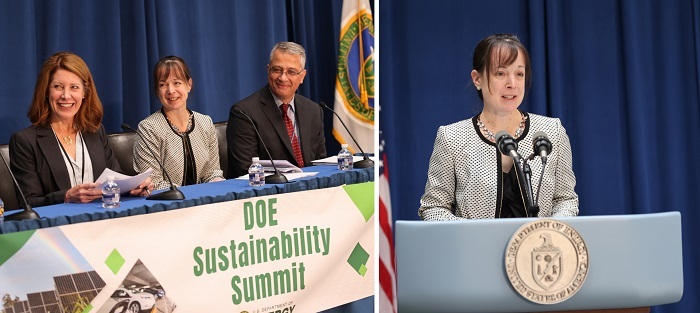 Kristen Ellis, EM acting associate principal deputy assistant secretary for EM's Office of Regulatory and Policy Affairs, pictured at right, took part in a panel session during DOE’s first Sustainability Summit held last week. Ellis provided updates on EM’s work sustainability and climate resiliency planning as well as EM contributions to DOE’s Cleanup to Clean Energy initiative. The summit focused on the Department’s overall sustainability goals, including 100% carbon pollution-free electricity by 2030, 100% acquisition of zero-emissions vehicles by 2027, a net-zero building portfolio and site climate resiliency plans. Other panelists pictured are Sheila Feddis, director of science laboratories infrastructure, DOE’s Office of Science, and Ahmad Al-Daouk, deputy associate administrator, National Nuclear Security Administration.
Oak Ridge
In the outstanding sustainability program/project category, the Department recognized Oak Ridge Office of Environmental Management (OREM) contractor UCOR for its unique water management practices at OREM’s onsite disposal facility, the Environmental Management Waste Management Facility. Crews installed an enhanced operational cover that sheds clean stormwater runoff from the landfill.
During fiscal year 2022, Oak Ridge received 54 inches of precipitation, and the cover helped divert water away from the facility and return more than 22 million gallons of clean water back to the local ecosystem.
“We are very proud of the positive results of this innovative design to protect our environment,” said Emily Day, UCOR’s regulatory strategy and integration manager. “Over the past decade, the enhanced operation cover has returned nearly 175 million gallons of clean water back to the local ecosystem, which means we don’t have to actively manage this water or transport it to a treatment facility.”
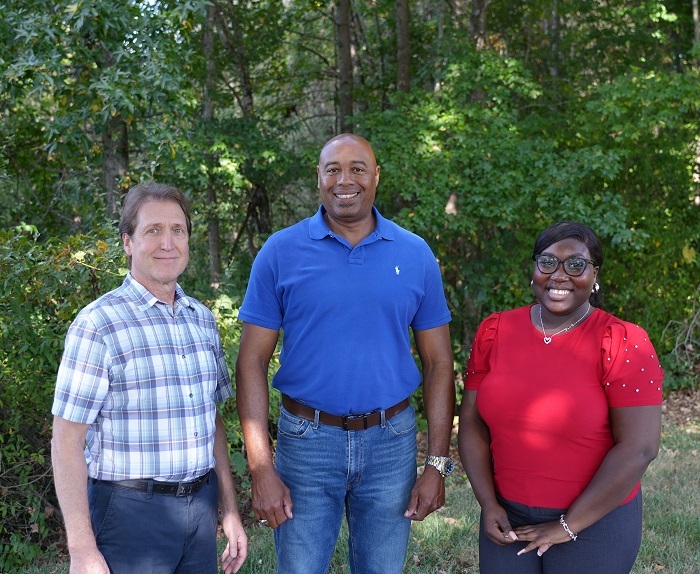 From left, Patrick Mullen, Darris Upton and Sierra Generette were instrumental in efforts to build strong relationships in the Scarboro community in Oak Ridge.
In the strategic partnerships category, DOE recognized UCOR’s work in Oak Ridge’s Scarboro community. The contractor hosted a meeting with community leaders and other residents to share information, build relationships and remove communication barriers. At the meeting, community members expressed interest in local employment opportunities supporting EM’s cleanup mission. As a result, UCOR developed a pilot program to spotlight those opportunities to residents.
At a follow-up workshop, UCOR shared a variety of career information, including local apprenticeship programs like the East Tennessee Apprenticeship Readiness Program. The meeting generated enough registrations to fill the entire next class, and all Scarboro community residents who completed the class were hired as full-time UCOR employees.
“We were so pleased with the success of the pilot program that we have developed our ‘UCOR in a Suitcase’ initiative,” said Sonya Johnson, UCOR director of public affairs and stakeholder management. “The goal is to build on the success of the Scarboro Workforce Workshop in other underserved communities in East Tennessee.”
Office of River Protection
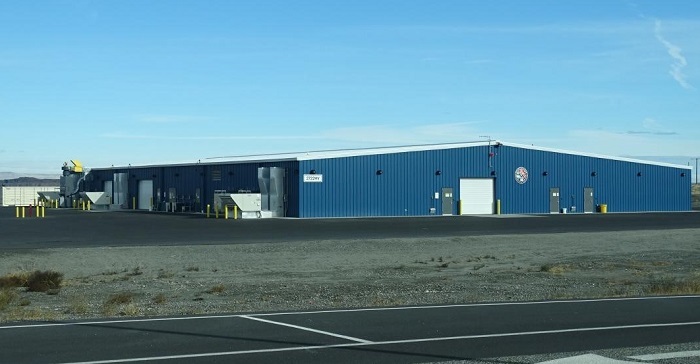 Having craft workers supporting the Hanford Site's tank waste storage and treatment mission under one roof at the Multi-Craft Maintenance Facility instead of multiple smaller facilities enhances work planning, communication, and coordination, thereby improving safety and efficiency, according to EM’s Office of River Protection.
The Department recognized ORP with a High Performance Sustainable Building Award for its new workshop completed last year for craft workers supporting Hanford's tank waste storage and treatment mission. Watch a video about the project here.
The building layout of the 27,000-square-foot Multi-Craft Maintenance Facility improves efficiency by providing craft spaces for workers under the same roof, according to Washington River Protection Solutions (WRPS). The tank operations contractor teamed with the craft workers, starting with the design phase, to make sure the facility would meet their needs. It replaces multiple smaller facilities.
Environmental considerations influenced some features of the building, including repurposing excess equipment from contractor Hanford Mission Integration Solutions. Leftover building materials will also be repurposed for future building projects.
“Having a centralized location for the crafts improves efficiency and creates a greater sense of collaboration,” said Jim Lynch with the ORP tank farms program division.
The facility allows projects to transition easily from craft-to-craft workspaces within the building. As many as 100 people could be working in the facility throughout any given day, including electricians, carpenters, tool crib attendants, painters and insulators, pipefitters and millwrights, and instrument technicians.
Lynch also said the facility plays an important role in moving Hanford projects forward, including preparation to treat tank waste under the Direct-Feed Low-Activity Waste Program.
Paducah Site
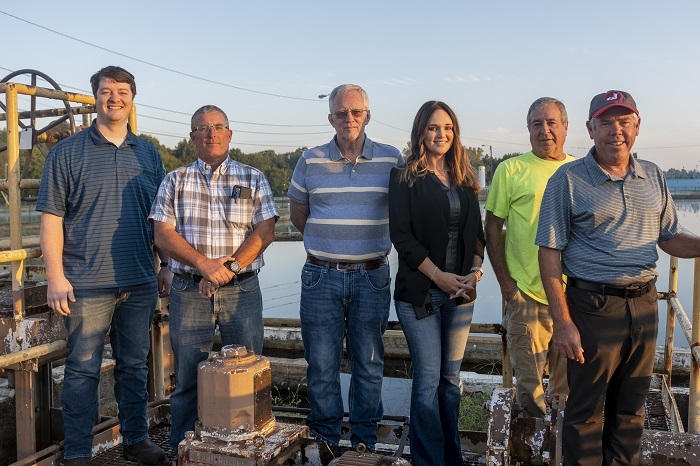 EM Paducah Site deactivation and remediation contractor Four Rivers Nuclear Partnership employees, from left, Byron Brown, Matt Maurer, Dale Donohoo, Stacy Cook, Andy Anderson and Ronald “Sunny” Summers supported the replacement of a raw water pump that led to the conservation of about 1 million gallons of water per day.
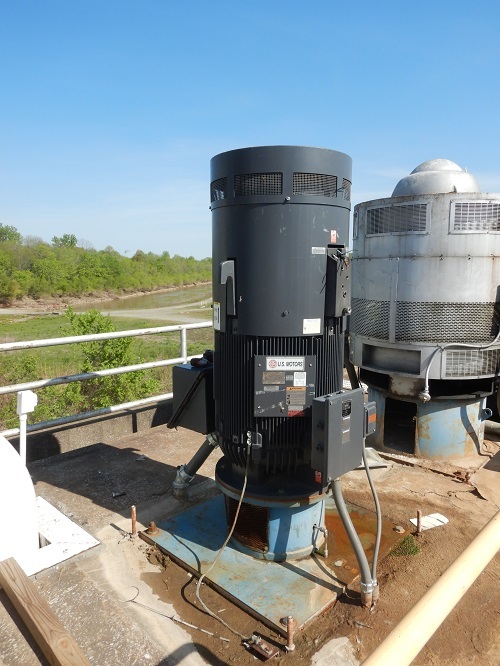 |
|
Paducah received honorable mention in the outstanding sustainability program/project category for its installation of a replacement raw water pump, at left, that has conserved approximately 1 million gallons of water per day and reduced electricity usage by approximately 63%. The pump supplies the C-611 Water Treatment Plant. The project was completed as part of ongoing utility optimization at the site. |
-Contributors: Susanne Dupes, Dylan Nichols, Matt Roberts
 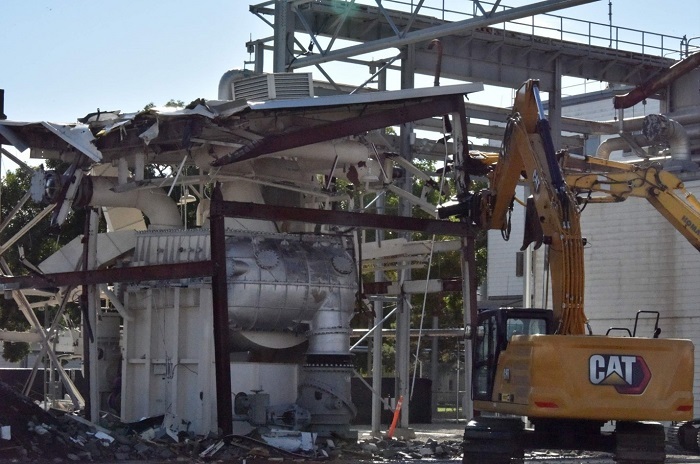 Crews demolish one of two massive steam condensers at the Naval Reactors Facility’s Aircraft Carrier 1st Gen. Westinghouse prototype facility. It was the prototype for the USS Enterprise, the nation’s first nuclear-powered aircraft carrier.
IDAHO FALLS, Idaho – EM crews at the Idaho National Laboratory (INL) Site are making significant progress decommissioning the prototype for a reactor plant used for the first nuclear-powered submarine.
Known as the Submarine 1st Generation Westinghouse (S1W) prototype, the land-based reactor was built inside a section of a submarine hull at the Naval Reactors Facility on the Arco Desert west of Idaho Falls. The Office of Naval Reactors entered into an agreement with EM to carry out the S1W facility demolition and other deactivation and decommissioning (D&D) efforts.
Crews with EM contractor Idaho Environmental Coalition are dismantling the S1W’s hull and engine compartments. They have also begun deactivating the reactor compartment and associated systems by removing shielding components to prepare the reactor vessel for eventual disposition at the Idaho CERCLA Disposal Facility at the INL Site. CERCLA stands for the Comprehensive Environmental Response, Compensation and Liability Act.
To date, the project has sent an estimated 250 tons of non-radiological contaminated metals for recycling. The S1W deactivation and demolition (D&D) project is scheduled for completion in November 2025.
EM workers have begun early deactivation and decommissioning activities at the Aircraft Carrier 1st Gen. Westinghouse (A1W) prototype with D&D work on the ancillary buildings around the A1W aircraft carrier prototype. They have demolished a non-contaminated concrete retention basin and one of the massive steam condensers for A1W. This early work has cleared space to support equipment staging for future D&D work inside the prototype.
Turnover of the main A1W facility for D&D, which remains on schedule, is being done in a phased approach in close coordination with the EM and Naval Reactors contractors.
Between 1954 and 1995, the INL Site’s Naval Reactors Facility was home to three active nuclear propulsion prototypes — the S1W, A1W and the Submarine 5th Gen. General Electric. Although these historic prototype facilities are no longer used, they provided important testing opportunities for the Navy and training for nearly 40,000 personnel.
-Contributor: Carter Harrison
 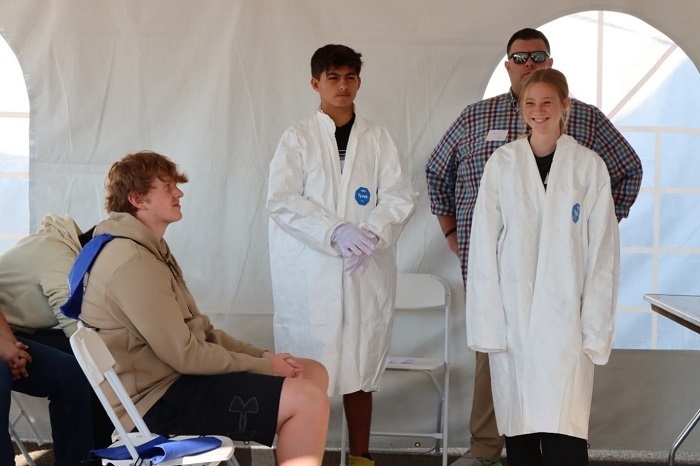 Waverly High School students Joshua Medukas, second from left, and Rachel Remy, far right, learn the importance of proper doffing and donning from Mid-American Conversion Services Training Specialist Jason Rodgers, second from right, at one of the Science Alliance’s 14 hands-on science activity stations.
PIKE COUNTY, Ohio – More than 1,200 area students recently converged on EM’s Portsmouth Site for the 12th annual Science Alliance, one of the largest science events in southern Ohio.
Hosted by EM, the event aims to provide students with a view of career opportunities through hands-on science experiments and demonstrations focused on science, technology, engineering, art and math (STEAM) with federal and contractor project management and subject matter experts.
Over the past several years, the event has grown to include local manufacturers and businesses, which gives students a better idea of local jobs available after graduation. This year, students met with representatives from 10 area businesses, including Portsmouth Site contractors Fluor-BWXT, Enterprise Technical Assistance Services and Mid-American Conversion Services.
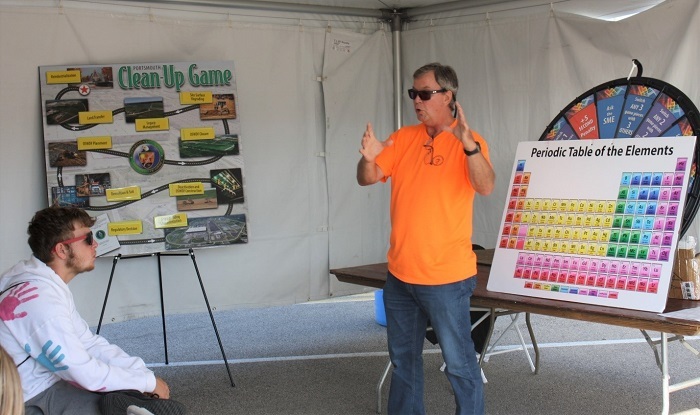 Federal Project Director Jud Lilly, right, leads the Portsmouth Clean-Up Game where students work together to better understand the ongoing work process with the end goal of site reindustrialization.
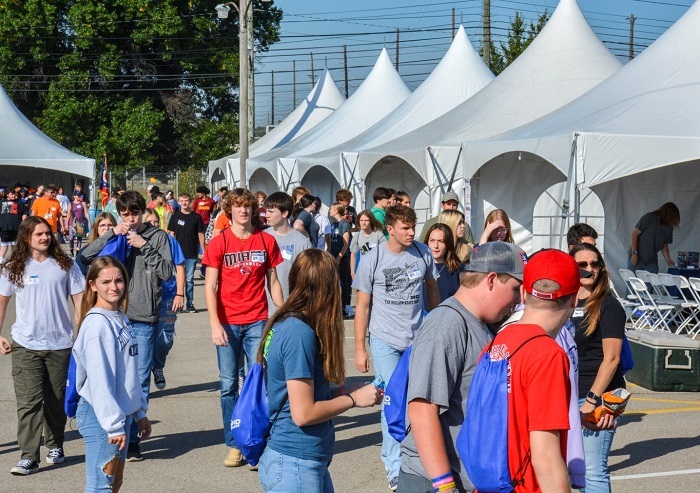 Students from 24 local high schools rotate between stations at the Portsmouth Science Alliance.
“Science Alliance is a great way for local students to begin exploring the next step after graduation,” said Portsmouth Site Lead Jeremy Davis. “It’s wonderful to see so many students excited about the potential that comes with a STEAM career.”
In addition, representatives from nearly a dozen Ohio and Kentucky universities offered application tips and provided details about their schools for those considering a college education.
-Contributor: Cindi Remy

RICHLAND, Wash. – The Hanford Site recently served as a backdrop for training DOE protective forces on readiness for active assailant situations.
EM Richland Operations Office contractor Hanford Mission Integration Solutions (HMIS) conducted the training in collaboration with the National Nuclear Security Administration (NNSA) and included protective forces from NNSA’s Office of Defense Nuclear Security and first responders from other DOE sites. The five-day training course for more than 100 personnel was held at Hanford’s HAMMER Federal Training Center and the nearby Patrol Training Academy.
“Safety and risk reduction are paramount to our One Hanford mission and the broader EM complex,” said Brian Harkins, EM Hanford assistant manager for Mission Support. “Hanford’s exceptional training facilities provided this real-life workshop, helping DOE protective forces and emergency responders continue to develop skills they need to respond to an active assailant at one of our facilities.”
The training incorporated a blend of classroom sessions and scenario-based activities, including live-fire operations.
Participants engaged in training focused on neutralizing assailants. The training was designed to increase confidence for response, enhance problem-solving skills, minimize potential casualties and establish a foundation for future training.
“This type of joint exercise is increasingly beneficial as we prepare for ever-changing security incidents,” said Hanford Patrol Deputy Chief Paul Hughes. “Training with other sites allows us to share ideas and bring consistency to best practices.”
HAMMER and Hanford Patrol provided logistical support, subject matter experts and safety support. HMIS teams provided training schedules and supplied the necessary equipment and officers for the event to meet safety and policy standards. HAMMER stands for Hazardous Materials Management and Emergency Response.
“The training showcased DOE’s commitment to enhancing active assailant response capabilities across the complex,” said Harkins. “This collaborative, hands-on approach enhances the skills and readiness of protective personnel to mitigate potential threats and safeguard our nation’s critical assets.”
-Contributor: Cerise Peck
Six new security police officer graduates at EM’s West Valley Demonstration Project gather with their instructors for a photo after their recent graduation ceremony at the site. From left: Sgt. Joseph Yerpe; Lt. James Madsen; security police officer Damin Crowley, Skye Dailey, Kyle Herbert, Andrew Wooley, Joshua Coolidge and Greg Steiner; and Sgts. Travis Radomski and Jason Dry.
WEST VALLEY, N.Y. – EM’s West Valley Demonstration Project (WVDP) recently held a graduation ceremony for six security police officers who completed a seven-week course through a unique partnership with the local sheriff’s office.
Normally, the officers take the course at DOE’s National Training Center (NTC) in Albuquerque, New Mexico. However, in 2021 the WVDP management team — which consisted of representatives from EM, its cleanup contractor CH2M HILL BWXT West Valley (CHBWV), and security subcontractor Paragon Energy — developed a plan for the officers to be trained by instructors from Paragon and the Cattaraugus County Sheriff’s Office using sheriff’s office facilities. The training plan was approved by the NTC.
West Valley chose the course through the sheriff’s office again this year. Six new recruits at West Valley, and one from EM’s Waste Isolation Pilot Plant, completed the training, which included firearm qualifications, defensive tactics, use of force, first aid and combat casualty care, improvised explosive device and bomb training, vehicle stops, DOE tactical doctrine, physical fitness, and other required courses of study.
The partnership continues to provide quality training that meets NTC standards and requirements, while saving taxpayers money, according to WVDP officials.
“We are especially proud of your successful completion of the seven-week protective force training course that challenged both your physical and mental capabilities,” Jennifer Dundas, assistant director of the West Valley Office of Technical Services, told the new security police officers.
The six West Valley officers who completed the course had previously worked as unarmed security officers at the site.
“Through your training, you now have greater capabilities as a security police officer graduate than you did before,” said John Rendall, CHBWV president and general manager. “I hope that every day is a boring day, but you know that you are well prepared if the day comes when it is not.”
Deputy Sheriff Sgt. Jason Dry said the recruits handled the course admirably and with professionalism.
“I feel safer as an officer of the law knowing that these new recruits are available to protect the site and people in the surrounding communities,” Dry said.
Dave Schuman, CHBWV safeguards and security manager, said it was important for the West Valley management team to recognize the graduates for completing the training, and to show their families gratitude for their efforts.
“This training pushed these recruits both mentally and physically, and we applaud them for their commitment and perseverance,” Schuman said.
Darren Boone, CHBWV Environment, Safety, Health and Quality manager, provided closing remarks at the graduation ceremony.
“If you were not touched by this graduation ceremony, you weren’t listening. We can pretend that we know what these recruits went through, but in the end, we can only imagine what it was like to sacrifice so much so that you can put yourself in harm’s way to protect others,” Boone said. “There are many things that threaten our safety and security; but knowing you are trained, prepared and ready makes us all feel safer. For that, I am truly grateful.”
-Contributor: Joseph Pillittere
 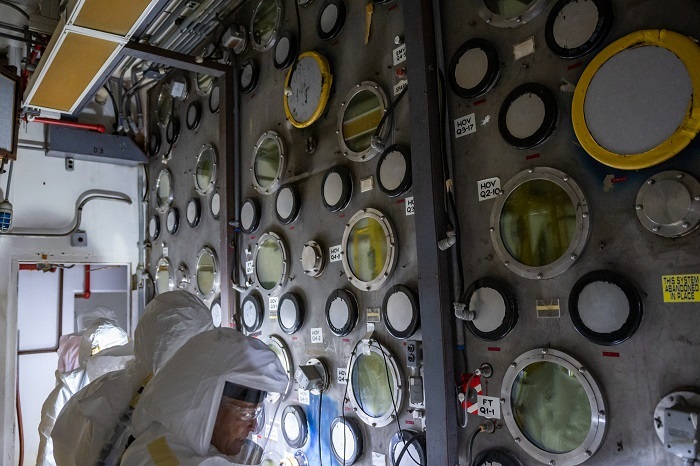 A team with EM contractor Central Plateau Cleanup Company conducts an inspection inside the Plutonium Uranium Extraction Plant at the Hanford Site. Workers regularly survey and inspect hundreds of waste sites and dozens of facilities to help ensure safe and efficient remediation.
RICHLAND, Wash. – A low-profile team with EM Richland Operations Office (RL) contractor Central Plateau Cleanup Company (CPCCo) plays a high-profile role in maintaining the safety and integrity of various Hanford Site waste sites and aging facilities.
The Field Operations team, consisting of about a dozen experienced workers, conducts routine surveys and monitors potential radiological, biological and industrial hazards at approximately 1,500 waste sites and 50 aging facilities within the central area of the Hanford Site.
Waste sites include old waste cribs, ponds, trenches, burial grounds, vaults and demolition sites. Cribs are aging underground structures.
“Every member of our team is vital to our mission success, none more so than our site surveillance teams, who often work in the background performing work that contributes to the overall advancement of the current cleanup mission,” said Andy Wiborg, EM Projects and Facilities Division team lead for Hanford’s Central Plateau Cleanup Project. “The information they gather through monitoring and inspection activities is invaluable for assessing the status of these waste sites and structures, which helps inform future remediation planning.”
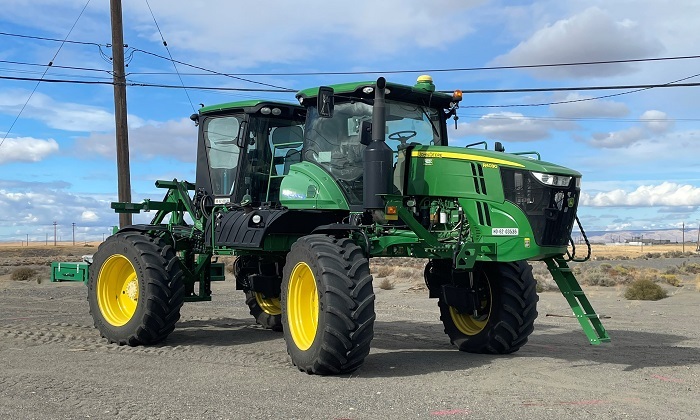 Workers with EM contractor Central Plateau Cleanup Company use a tractor equipped with radiation detectors to perform surveys of large waste sites at the Hanford Site.
Data on waste sites and facilities are logged in a Hanford database that documents and tracks historical information, investigations, remediation and closure-action activities.
The team uses an array of equipment to safely survey the waste sites, which range in size from a small parking lot to an 18-hole golf course. The equipment, with radiation detectors onboard, includes a tractor for large waste sites, a four-wheel-drive pickup truck and a smaller tractor. The team also uses walking-stick detectors for small sites and spot surveys.
“We survey the waste sites annually, semiannually or quarterly, depending on the history of issues and requirements at each site,” said Roy Plunkett, CPCCo’s Field Operations team manager.
In addition to surveys, the team conducts thorough inspections of waste sites to detect changes in conditions. They clean up small areas of contamination and remove surface debris.
The team also inspects facility exhaust stacks, emergency equipment and fire extinguishers, and performs general housekeeping.
-Contributor: Mark McKenna
 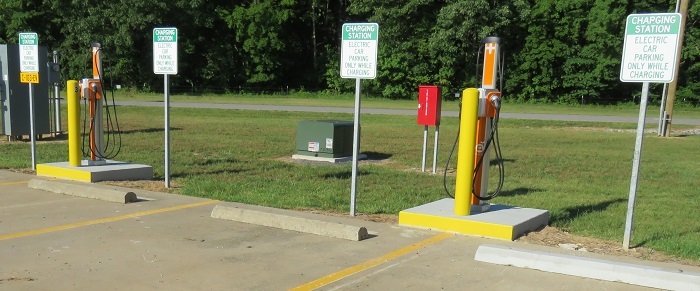 Pictured are two dual-port electric vehicle charging stations installed near the Paducah Site Office with infrastructure to support three additional dual-port stations in the near future.
PADUCAH, Ky. – EM’s Paducah Site recently received a jolt of energy with the installation of six new electric vehicle charging stations, an addition that enhances the site’s infrastructure while helping to improve the environment.
Swift & Staley Inc. (SSI), the Paducah Site infrastructure support services contractor, set up two dual-port stations at three locations, for a total of 12 charging ports at the site. The EM crews built the charging locations for future expansion to accommodate nine additional dual-port stations, which will eventually bring the site’s total to 30 charging ports.
All of the charging stations are powered by an off-site electrical supplier. The Paducah Site participates in the Green Energy Program and recently started purchasing 100% renewable energy. Kentucky Utilities offers that program to customers that want to support the development of electricity generated by regional wind and solar renewable resources.
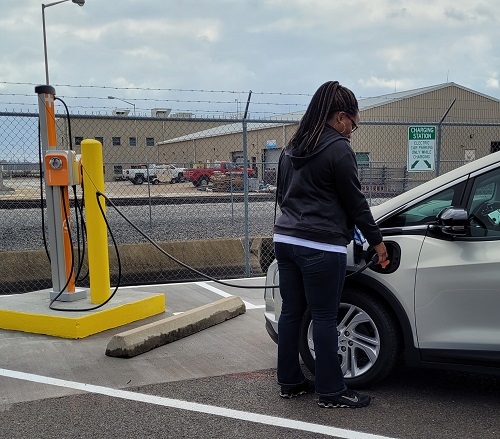 |
|
Swift & Staley Inc. employee Latrice Ford charges the first zero-emissions vehicle at the Paducah Site. |
Paducah contractors are currently placing orders through the U.S. General Services Administration to convert light-duty, gasoline-powered vehicles to electric zero-emissions vehicles as they become available. The first of these electric vehicles arrived at the site in February, and as more come, the electric vehicle charging equipment becomes increasing critical to the site.
“This is the first step in our commitment to implement the new requirements of a Biden administration executive order on catalyzing clean energy industries and jobs through federal sustainability,” SSI Project Manager Tammy Courtney said. “We are working with DOE to prepare the site for the future delivery of additional zero-emissions, light-duty vehicles from GSA.”
-Contributor: Stacey Marinelli

PIKE COUNTY, Ohio – EM’s infrastructure support services contractor at the Portsmouth Gaseous Diffusion Plant has marked 2 million consecutive safe work hours — or zero recordable injuries and illnesses — since the inception of its contract in 2016. “I am proud of the attention to safety North Wind has exhibited over the last seven years,” Portsmouth Site Lead Jeremy Davis said. “Safety is always a top priority at the Portsmouth Site, so it’s important we recognize our contractor’s commitment to these high standards.” North Wind’s scope of work includes roads and grounds, janitorial, shipping and receiving, facility maintenance, information technology, security and records. North Wind crews also complete several special construction projects, including paving, culvert replacement and renovations. The company’s employees, pictured here, relate their success to their partnership and collaboration with DOE and the local United Steelworkers, along with implementation of the DOE Worker Safety and Health Program, the Integrated Safety Management System and employee safety culture. North Wind’s motto is “Where Safety Leads, Performance Follows.” DOE’s Voluntary Protection Program has awarded the company four Star of Excellence awards and two Legacy of Star awards.
-Contributor: Matthew Miller
|