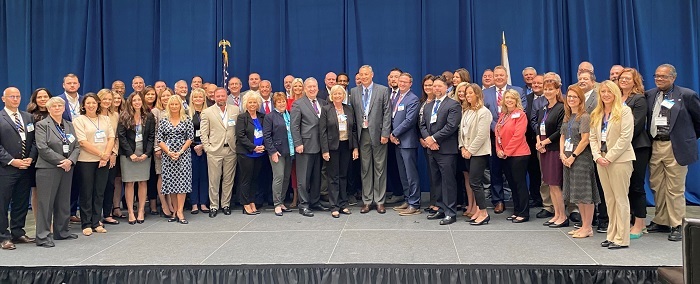 More than 60 local leaders from Paducah, Kentucky join Portsmouth/Paducah Project Office Manager Joel Bradburne and others for a photo during the annual Paducah Area Chamber of Commerce two-day Washington, D.C. Fly-In.
WASHINGTON, D.C. – Local leaders from Paducah, Kentucky recently visited Washington, D.C. to meet with EM Senior Advisor William “Ike” White and other senior DOE officials to discuss the post-cleanup future for the Paducah Site.
White participated in a discussion with the 65-person contingent, part of the Paducah Area Chamber of Commerce’s annual two-day D.C. Fly-In trip.
Sandra Wilson, Paducah Area Chamber of Commerce president, presented the community’s priorities related to the Paducah Site, focusing on how to begin a roadmap to future use as the community considers the current and future state of the site. Other discussions included federal funding and support for continued cleanup efforts.
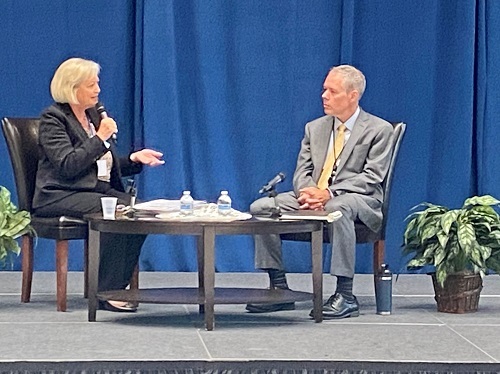 |
|
Paducah Area Chamber of Commerce President Sandra Wilson, left, speaks with EM Senior Advisor William “Ike” White during the chamber’s annual trip to Washington, D.C. |
The Paducah group also talked with Todd Shrader, director of project management at the DOE Office of Clean Energy Demonstrations, and Kate Gordon, senior advisor to Energy Secretary Jennifer Granholm, about possible synergies between their offices and the Paducah community.
The delegation hopes conversations with key officials each year will lead to continued backing of the Paducah Site in addition to sustained positive relationships.
It was the chamber’s 19th trip to D.C. The group plans to continue the annual visits for years to come.
-Contributor: Zachary Boyarski
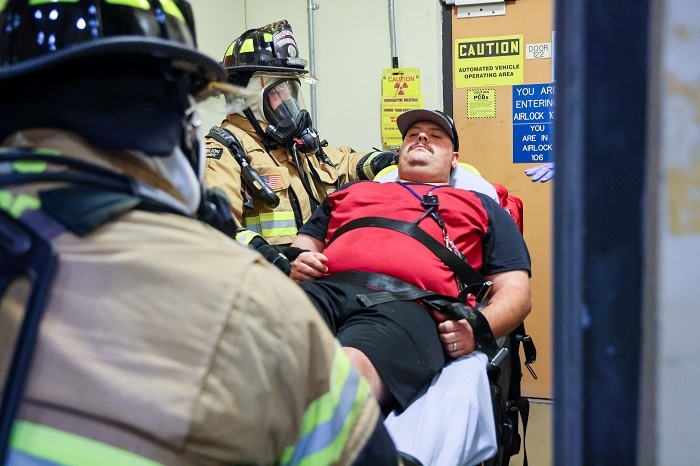 Waste Isolation Pilot Plant (WIPP) firefighters and paramedics Jesse Solano, left, and Jakoda Mathews prepare to transport Nick Thompson, who portrays a victim, from the WIPP waste handling building to a waiting ambulance during a mock event as part of an annual emergency training exercise.
CARLSBAD, N.M. – Consider the following heart-pounding scenario hundreds of employees responded to as part of the EM Waste Isolation Pilot Plant’s (WIPP) recent annual emergency exercise:
A plane crashes at the WIPP site, bursting into flame and igniting a wildland grass fire. One of the plane’s engines smashes through the security fence and on through the wall of the waste handling building. Barrels of waste burst open, spreading contamination, and a waste handler is injured and contaminated.
In addition to dozens of drills throughout the year, the graded exercise ensures WIPP personnel are prepared to respond in an actual emergency.
In the training scenario, operators in WIPP’s Central Monitoring Room, with their hands suddenly extremely full, assess the multiple situations and start to dispatch WIPP personnel. The incident commander puts a call out for mutual aid from Carlsbad and Hobbs emergency medical services to assist with the “injured” victims, and Eddy County Fire and Rescue to assist with the crash fire.
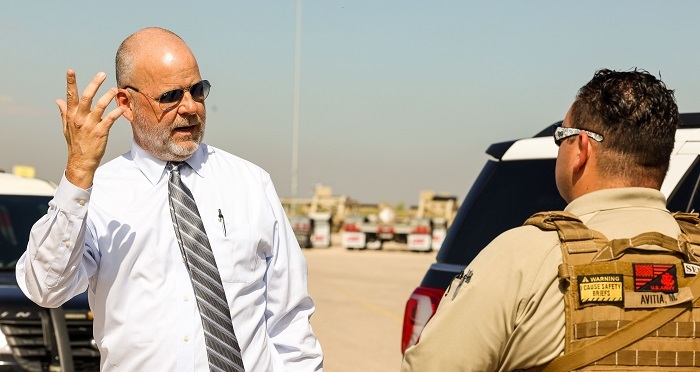 At the Waste Isolation Pilot Plant site, an insistent media member with the fake name of Chris Taylor was played by Brett Hansard, manager of the risk communication and management program at DOE’s Argonne National Laboratory. He bothered security as he tried to get more information about the incident portrayed in the emergency exercise.
Site personnel are directed to stay indoors, and office wardens begin the task or accounting for personnel in their areas. Underground personnel, 2,150 feet below the surface in WIPP’s repository, go to their assembly areas to await further instruction as radiological control technicians take readings on the surface.
Employees at the WIPP site and the Skeen Whitlock Building in Carlsbad participated in the simulated event. In Carlsbad, 26 miles west of the WIPP site, the Emergency Operations Center (EOC) was staffed and activated, and the adjacent Joint Information Center (JIC) began to field mock calls from the anxious public and media. The EOC worked with the facility shift manager at the site for an evacuation of nonessential personnel by bus.
An insistent media member played by Brett Hansard, manager of the risk communication and management program at DOE’s Argonne National Laboratory, pestered security personnel at the WIPP site, trying to get more information. Hansard used the name Chris Taylor in the scenario.
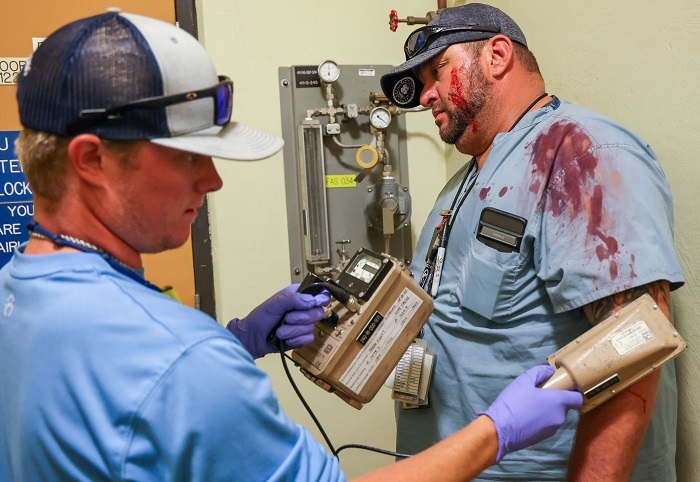 Radiological control technician Logan Norwood checks bloodied mock victim Derrick Jameson, a waste handler, for contamination following a simulated accident during the Waste Isolation Pilot Plant’s annual emergency exercise last month.
Whew!
“The complexity was designed to test response efforts from multiple emergency response organizations, such as the Central Monitoring Room, Emergency Operations Center, Joint Information Center, WIPP fire and security departments, and outside agencies. The result was an exercise that challenged coordination and response efforts across the board,” said John Sanford, emergency management manager for WIPP maintenance and operations contractor Nuclear Waste Partnership.
The event took months to plan.
“The WIPP full-scale exercise was the result of a joint planning effort from multiple WIPP personnel and departments, as well as our mutual aid partners,” Sanford said. “While there were a few opportunities for improvements identified, the exercise was an overall success. WIPP Emergency Management wishes to thank all of the organizations that participated and supported the exercise from planning to execution, including mutual aid organizations and agencies.”
-Contributor: Roy Neese
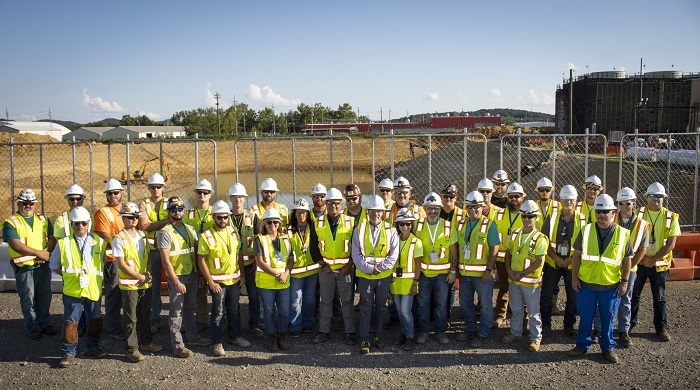 Crews at the X-231B Biodegradation Plot, a former landfill, safely completed a significant milestone three days ahead of schedule. On Aug. 12, they removed the final cubic yard of more than 195,000 cubic yards of soil for engineered fill at the On-Site Waste Disposal Facility.
PIKE COUNTY, OHIO - Crews at EM's Portsmouth Site recently finished excavating the first of five legacy landfills whose soil will be used to support the On-Site Waste Disposal Facility (OSWDF).
Work on the X-231B Biodegradation Plot began last fall and involved removing more than 195,000 cubic yards of soil for use as engineered fill at the OSWDF.
“By using impacted soil from legacy groundwater plumes and old landfills onsite instead of buying clean fill for the OSWDF, environmental cleanup of the site has been accelerated, providing more remediated land for future reuse,” said Joel Bradburne, manager of the Portsmouth/Paducah Project Office.
The X-231B milestone was completed three days ahead of schedule. The next target to be excavated will be the nearby legacy landfill X-231A Biodegradation Plot.
Five legacy landfills and five groundwater plumes will be excavated at the Portsmouth Site to support decontamination and decommissioning.
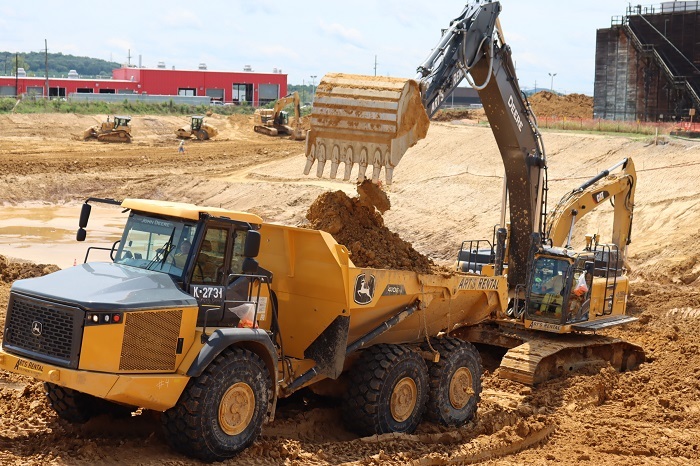 A heavy equipment operator loads soil into a dump truck for transport to the On-Site Waste Disposal Facility.
Soil from X-231B is being used at the OSWDF as engineered fill for debris from the site’s X-326 Process Building, which was demolished earlier this year. The engineered fill must meet waste acceptance criteria governing what is permissible for the disposal facility. Each individual landfill or plume requires an approved excavation work plan to ensure safety, protectiveness and compliance.
“This was a great accomplishment for the site,” said Greg Wilkett, site project director with Fluor-BWXT Portsmouth, EM's Portsmouth Site decontamination and decommissioning contractor. “It takes everyone working as a team to get a task like this completed. The accelerated environmental cleanup work was accomplished safely by project personnel providing 24-hour coverage, five days a week, in two shifts.”
To enhance the condition of the excavated soil going to the OSWDF, crews used a fast-acting drying agent to reduce moisture content in the soil and to help keep work on schedule. From there, conditioned soil is loaded onto trucks and transported to the OSWDF.
-Contributors: Michelle Teeters, Jack Williams
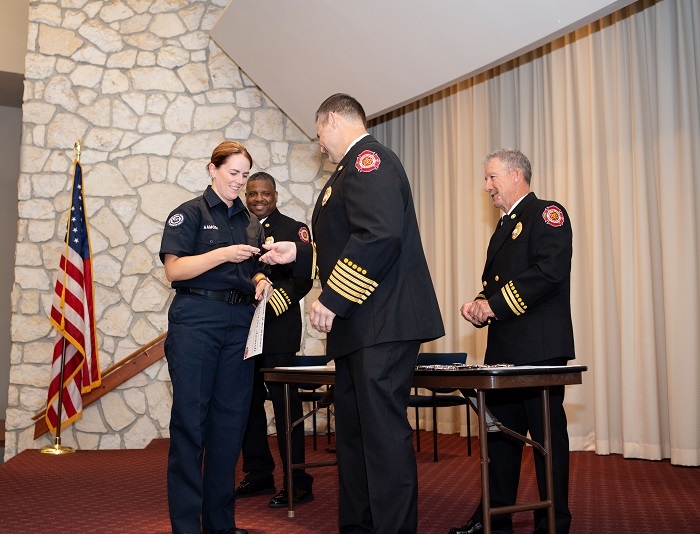 Firefighter Christina Aamodt receives her badge from Chief Todd Roper during a Hanford Fire Department ceremony recognizing graduates of the New Recruit Training Academy, a 16-week training course covering a range of courses and hands-on fire training.
RICHLAND, Wash. – EM Richland Operations Office (RL) contractor Hanford Mission Integration Solutions (HMIS) recently held a formal ceremony for the Hanford Fire Department, recognizing 28 graduates of the New Recruit Training Academy and 13 individuals who received promotions.
The fire department enlists new recruits in a 16-week academy covering a range of courses and hands-on fire training that will serve them well beyond the borders of Hanford. From fire alarm system knowledge to wildfire training, these firefighters must show drive, determination and flexibility to join the ranks at Hanford.
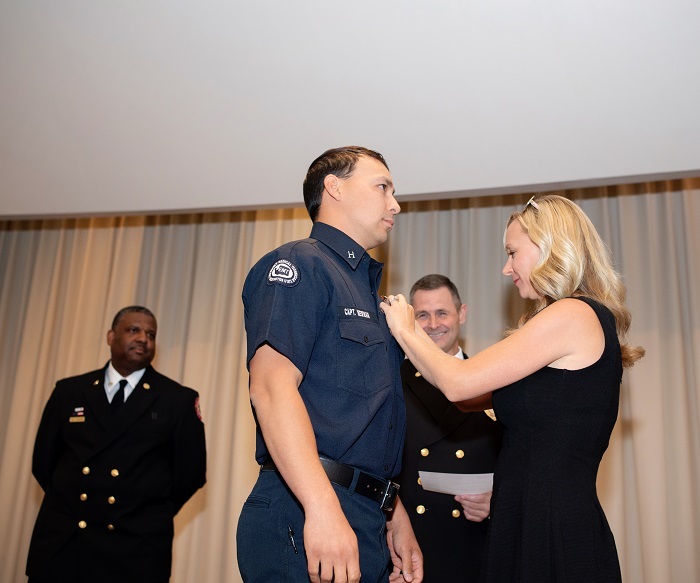 Capt. David Newman receives his promotional pin from his wife, Karen, during a ceremony held by the Hanford Fire Department recognizing individuals who received promotions between 2019 and 2022.
During the ceremony, Brian Vance, manager of EM’s Office of River Protection and Richland Operations Office, acknowledged efforts put forth during the training and expressed the significance of being a Hanford firefighter.
“It is great to celebrate these accomplishments and your decision to serve Hanford,” said Vance. “The contribution of the Hanford Fire Department is important to the Hanford mission, our community and the Pacific Northwest.”
Sharing personal stories of watching the Hanford Fire Department in action, HMIS President Bob Wilkinson congratulated the new recruits on their efforts.
“This is an elite group, who are good at what they do, and you have demonstrated the capacity to work hard day in and day out to earn a spot on this team,” said Wilkinson. “Welcome to Hanford.”
-Contributor: Melissa Ver Steeg
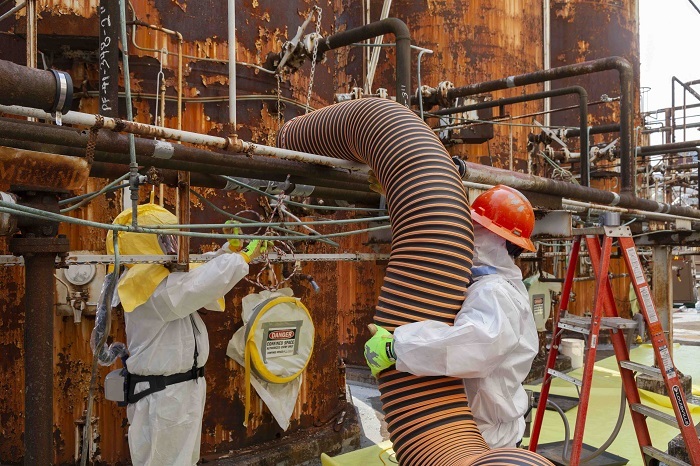 UCOR continued deactivation on the old Column Exchange (COLEX) equipment outside the Alpha-4 facility at the Y-12 National Security Complex during the cleanup contractor’s most recent fee evaluation period. The COLEX equipment had been used for lithium separation, a process requiring large amounts of mercury. UCOR’s efforts outside the Alpha-4 facility recovered 1.7 tons of mercury, preventing a large environmental release.
OAK RIDGE, Tenn. – EM recently awarded Oak Ridge cleanup contractor UCOR approximately $27.5 million for its performance from Nov. 1, 2021 through May 22, 2022, amounting to 85% of the available fee for the evaluation period.
The Oak Ridge Office of EM (OREM) issued its fee determination scorecard for UCOR for the seven-month period after completing its evaluation of the contractor.
EM releases information relating to contractor fee payments — earned by completing the work called for in the contracts — to further transparency in its cleanup program.
UCOR received “excellent” ratings for project management and business systems, quality and safety culture, and regulatory and stakeholder activity; a “good” rating for operations management; and “high confidence” for cost and schedule incentive, according to the scorecard.
Following are significant accomplishments by UCOR during the evaluation period:
- Completed work $129 million under budget.
- Recovered 1.7 tons of mercury from Alpha-4, bringing the total amount of mercury recovered at Alpha-4 to approximately 7 tons. This decreased the risk of release, moved the facility closer to demolition preparation, and reduced the mercury vapor at the facility, all of which will reduce the cost of demolition preparation and further improve worker safety.
- Advanced cleanup of excess contaminated facilities at the Oak Ridge National Laboratory and the Y-12 National Security Complex and continued actions required to close the East Tennessee Technology Park (ETTP).
- Adapted to changing conditions resulting from COVID-19-pandemic related supply chain issues and staff shortages.
- Awarded about 73% of its subcontracts to small businesses — surpassing its goal of 65% — and exceeded four of five small business socioeconomic goals.
- Streamlined review and approval processes to enable accelerated transfer of excess ETTP land to the community.
While UCOR continues to be responsive to incidents and improve work planning and controls, OREM noted additional improvements are needed related to electrical hazards and asbestos.
View the full fee determination scorecard for UCOR here.
-Contributor: Ben Williams
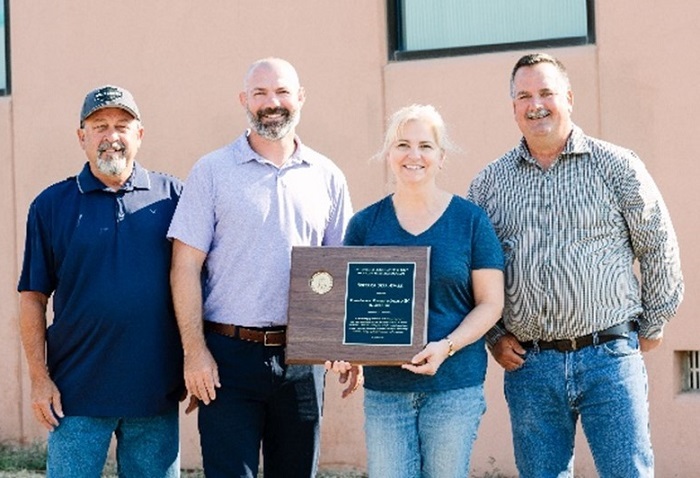 Pictured from left: Rick Ennis, Hanford Atomic Metal Trades Council safety representative; Garrett Knutson, Hanford Laboratory Management and Integration (HLMI) Environmental Health & Safety manager; Kristine Bowen, HLMI Voluntary Protection Program coordinator; and Ron Tucker, HLMI facility operations manager.
RICHLAND, Wash. – EM contractor Hanford Laboratory Management and Integration (HLMI), which runs the Hanford Site’s 222-S Laboratory, received the Voluntary Protection Program ( VPP) Superior Star award from DOE at a recent national conference in Washington, D.C.
“The Superior Star award is the result of a commitment to safety by the employees and management of HLMI,” said Kristine Bowen, HLMI VPP coordinator. “Management, leadership and employee involvement in everything from work planning, hazard evaluations and assessments to suggesting improvements demonstrates the principles of VPP.”
The VPP Superior Star is awarded to companies that consistently meet safety and health goals and achieve illness and injury rates better than 50% below the industry average. HLMI received the award at the Voluntary Protection Programs Participants’ Association Safety + Symposium.
“Earning the VPP Silver Star is the first step toward improving our safety performance in the coming years,” said Garrett Knutson, Environmental Health & Safety manager with HLMI.
Working through cooperative efforts among labor, management, and government at DOE contractor sites, DOE’s VPP promotes improved safety and health performance through public recognition of outstanding programs.
-Contributor: Tracie Arnold
|