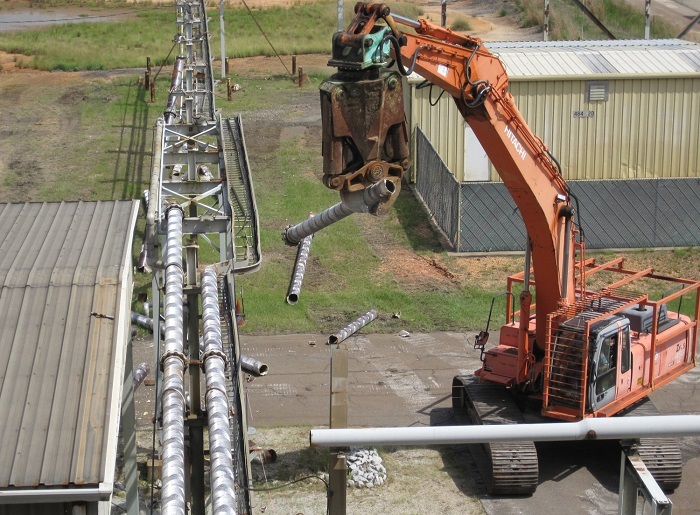 A portion of the 4,000 environmental cleanup milestones met by EM and its contractors at the Savannah River Site over the years involved cleanup of the site’s D Area. Here, Savannah River Nuclear Solutions personnel manage the demolition of structures and steam lines that crisscrossed this major remediation project.
AIKEN, S.C. – EM and its contractors at the Savannah River Site (SRS) recently achieved their 4,000th environmental cleanup milestone under a state-issued hazardous and mixed-waste permit and an agreement enacted by state and federal regulators.
“Hitting this milestone validates the excellent performance and dedication of our workforce regarding cleanup projects, programs and compliance across the Savannah River Site,” said Rick Sprague, senior vice president of environment, safety, health and quality for Savannah River Nuclear Solutions (SRNS), the site’s management and operations contractor since 2008.
EM cleanup at SRS is governed by a Resource Conservation and Recovery Act hazardous and mixed-waste permit and the Federal Facility Agreement (FFA), which was signed by DOE, the South Carolina Department of Health and Environmental Control (SCDHEC) and U.S. Environmental Protection Agency in 1993.
EM and its contractors at the site met all 4,000 milestones on or ahead of schedule, the most recent of which involved EM proposing wells to sample for contaminants from groundwater beneath the site’s Mixed Waste Management Facility.
“Not once did we miss a deadline. Often, we came in ahead of schedule, sometimes months ahead,” SRNS FFA Liaison Shelia McFalls said. “I think we all have reason to take pride in that. I’m proud of my co-workers’ exceptional work ethic.”
The 4,000 milestones involved a range of cleanup initiatives, permits, testing and projects, and the workforce accomplished them by partnering with the regulators using a core team process, according to McFalls. The team consists of officials from SCDHEC and EPA, with support from subject-matter experts from the regulatory agencies and SRNS.
“Working together with the best interests of all involved is the primary objective of this process,” said McFalls. “The mutual respect displayed, positive reinforcement given for innovative ideas and the sharing of expectations are but a few reasons this concept has been so successful and rewarding. It’s a comprehensive and proven approach to environmental cleanup established here at the Savannah River Site.”
Examples of milestones met using the core team process include:
- Grouting and permanently closing two nuclear reactor buildings.
- Preventing nearly 7,000 curies of tritium from entering the Savannah River, saving $208 million by drawing up irrigated water containing legacy tritium through 62 acres of pine trees, which harmlessly released the isotopes into the atmosphere through photosynthesis.
- Constructing a large underground water-permeable wall made of 1.5 million pounds of iron filings from reclaimed automobile engines. The wall neutralizes Cold War-era chemical solvents found in the aquifer beneath SRS and acts like a giant water filter to remove and break down degreasing solvents.
- Completing cleanup of more than 90 acres of coal ash-contaminated land a year earlier than scheduled, saving $8 million. This large undertaking consolidated more than 400,000 cubic yards of coal ash under a protective geosynthetic material and thick earthen caps.
“I’m looking forward to see what happens next. We have several major projects on the horizon and high expectations regarding our future milestones,” said Sprague.
-Contributor: DT Townsend
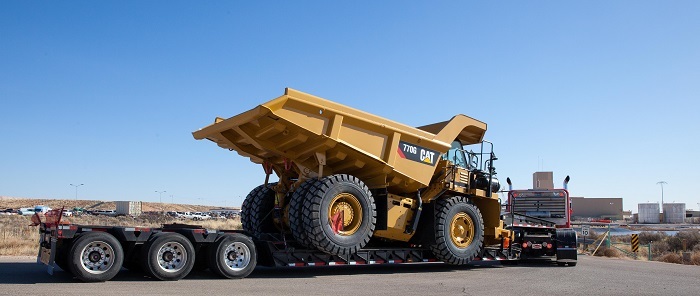 A new 40-ton salt haul truck arrives at EM’s Waste Isolation Pilot Plant. The machinery and its environmentally friendly diesel engine replace a standard diesel model that will be refurbished and used as a backup.
It might look like the bright yellow salt haul truck it replaces at the nation’s only transuranic waste repository, but the newest piece of machinery is far more advanced than its predecessor.
The new Caterpillar 770G is an environmentally friendly, 40-ton hunk of technology and brawn that will carry salt from WIPP’s salt hoist to surface stockpiles. It takes five trips of the salt hoist to fill it up.
While the new model might resemble the 770 model it replaces on the outside, it’s anything but under the sheet metal.
Instead of exhausting carbon soot, sulfur dioxide and nitrogen dioxide like a standard diesel, the 770G features a Tier IV Final diesel engine that uses a prodigious amount of technology to reduce tailpipe emissions to water and carbon dioxide. The engine accomplishes low emission numbers by using multiple major technologies, including a secondary chamber that burns the soot that would go out the exhaust of previous diesels.
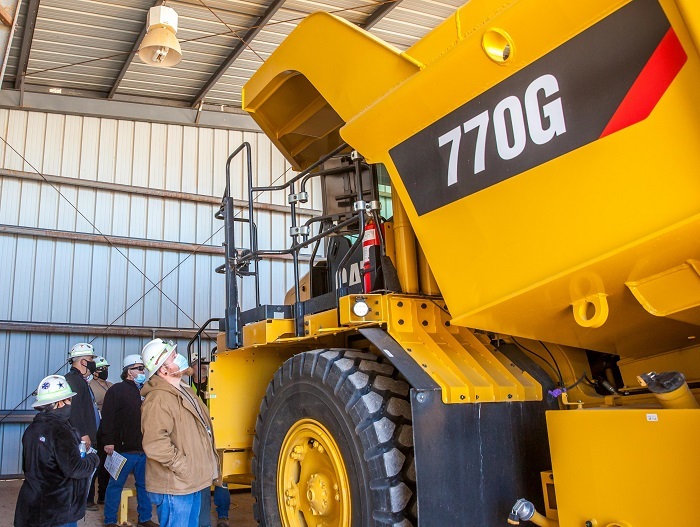 Waste Isolation Pilot Plant (WIPP) hoisting workers, who drive mined salt from WIPP’s underground to surface stockpiles, get their first look at a new truck that will haul salt to areas north of the site. It features diesel technology that reduces soot and other emissions.
Tier 4 diesel engine standards are the Environmental Protection Agency’s strictest mandated emissions requirements for off-highway diesel engines. The requirement regulates the amount of particulate matter, or black soot, and nitrogen oxide that can be emitted from an off-highway diesel engine.
Based on an engine’s horsepower rating, Tier 4 requirements were phased in starting in 2008. By the time Tier 4 regulations were fully implemented in 2015, particulate matter and nitrogen oxide emissions had been reduced 99% compared to 1996 levels.
Tier IV also is the technology being retrofitted onto diesel engines in the WIPP underground to reduce emissions.
The new 770G model, which arrived in early January, replaces a standard-diesel 770 model obtained in January 2010 that has 4,948 operating hours. The former is being sent out to be refurbished for use as a backup.
Hoist crew drivers were briefed on the new model’s maintenance and operations features inside a giant shed that houses WIPP’s two big trucks.
The trucks have been redesigned with major advancements in emissions control technology, transmission and traction control systems; frame, drivetrain and cooling system enhancements; added operator amenities such as a new seat location that reduces vibration and driver fatigue; and serviceability improvements. The screen to monitor the new electronics is four times larger than the screen in the previous truck.
-Contributor: Roy Neese
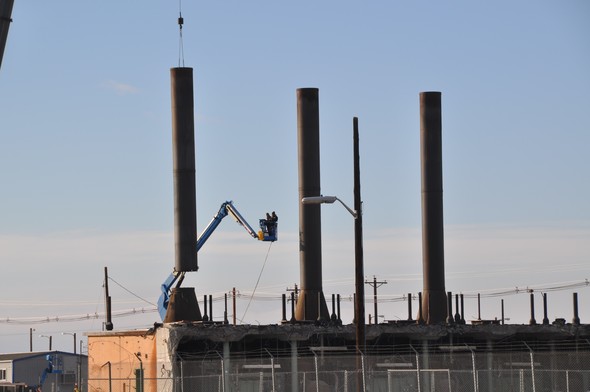 A crane lifts the first of three old ventilation stacks after workers cut through it. Removal of the 50-foot-tall towers changes the Hanford Site skyline near the Columbia River.
RICHLAND, Wash. – Workers with EM Richland Operations Office (RL) contractors Central Plateau Cleanup Company and Hanford Mission Integration Solutions recently teamed to remove three 50-foot-tall exhaust stacks near the Columbia River, further transforming the Hanford Site skyline.
Since last fall, crews have been tearing down a decommissioned boiler building that provided heat to numerous facilities that supported the K West Reactor during Cold War operations.
To allow below-grade demolition of the K West structure to continue, the large ventilation stacks connected with the building had to be removed. While previous stack removal projects at Hanford involved controlled explosives, this effort required a little more finesse.
 Mike Peterson, a journeyman pipefitter with EM contractor Central Plateau Cleanup Company, uses a torch to cut through one of three 50-foot-tall ventilation stacks, part of the demolition of an old boiler building that supported the K West Reactor during Hanford Site operations.
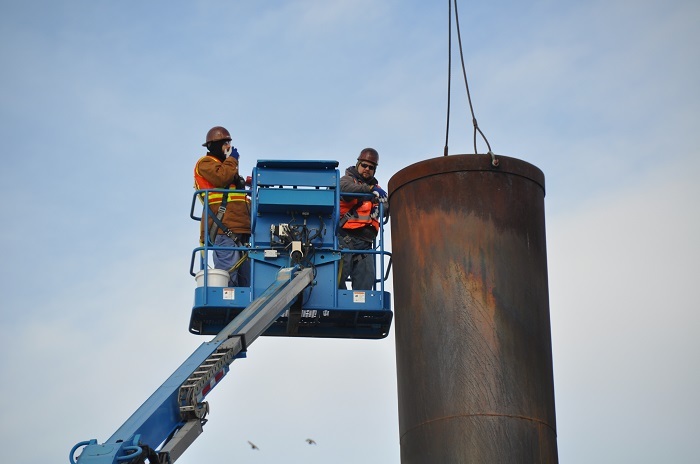 Ironworkers Jason Hemperly, left, and Mike Aldrich, with EM contractor Hanford Mission Integration Solutions, prepare to attach a crane’s cable to one of three exhaust stacks to enable the 7,000-pound steel tower to be safely lowered to the ground after it is cut from an old boiler building on the Hanford Site.
The joint contractor effort required extensive preparation and close coordination among several teams. Ironworkers rigged a crane to each stack for stability, while a pipefitter on an aerial lift carefully cut the almost 50-foot-tall steel towers with a torch. When the cutting was complete and the aerial lift moved out of the way, the crane operator lifted each 7,000-pound stack, safely lowering them to the ground. Several spotters on the ground ensured the well-orchestrated plan proceeded as designed.
See this video for more sights and sounds from the stack removal project.
“The safe completion of complex projects like this reinforces the value of our collaborative One Hanford approach: everyone working toward a common goal to accomplish the mission,” said Mark French, RL federal project director for Hanford’s Columbia River corridor and Central Plateau. “These stacks were visible from a long distance, and their removal provides very visual evidence of the ongoing cleanup progress.”
The stacks will be cut into smaller pieces and disposed at Hanford’s onsite engineered landfill. Final demolition activities on the structure are expected to be finished later this month. The project is part of ongoing efforts to reduce risk to the nearby Columbia River.
-Contributor: Dieter Bohrmann
|