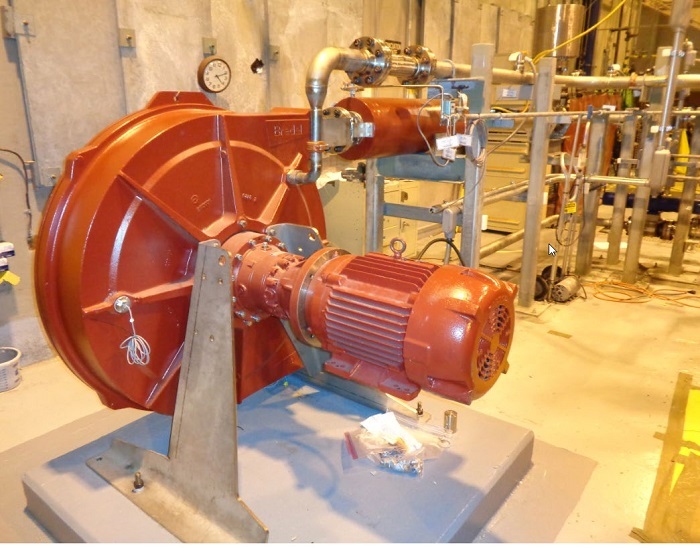 Savannah River Remediation (SRR) made significant improvements to the Saltstone Hopper Overflow Container at the Savannah River Site’s Saltstone Production Facility. Pictured is the container’s recovery pump, foreground, with piping and additional new equipment as part of the facility improvements.
AIKEN, S.C. – EM has developed a new, innovative system that reduces both operational downtime and personnel exposure at a key facility in the Savannah River Site (SRS) liquid waste system.
The Saltstone Production Facility (SPF), operated by EM’s liquid waste contractor Savannah River Remediation (SRR), receives decontaminated salt solution sent from the Salt Waste Processing Facility. SPF processes that solution into saltstone grout by mixing the liquid feed with dry materials. The grout is then pumped from SPF to saltstone disposal units, where the saltstone grout solidifies into a monolithic, non-hazardous, and solid low-level form, safe for permanent disposal.
At SPF, an overflow system called the Saltstone Hopper Overflow Container (SHOC) works as a safety feature that collects grout or flush water during instances such as grout pump hose ruptures, hopper overflow, or grout line overpressurization. Previously, any material that exceeded the SHOC capacity flowed into a process room trench that transferred the material to a nearby collection tank. Grout accumulated in the trench would harden and had to be chipped out by hand.
SRR developed and implemented a solution that solved this problem. The team installed a new system to reroute overflow from the SHOC and return the material to the grout line to prevent the material from entering the trench. Changes to the SHOC system included new equipment, such as piping and a recovery pump.
These modifications decrease facility downtime by months, reduce personnel exposure during recovery efforts and increase automation in plant response.
Jim Folk, DOE-Savannah River assistant manager for waste disposition, said strengthening SPF with the SHOC modifications will allow EM to continue its critical liquid waste mission.
“The Saltstone Production Facility is an important piece in the overall liquid waste system,” Folk said. “It is vital that the plant is running at its optimum capacity, especially now that it is receiving waste output from the Salt Waste Processing Facility.”
The innovations to the SHOC design, coupled with intensive maintenance over the last four years, are prime examples of SRR’s core values of continuous improvement and teamwork in action, according to Mark Schmitz, SRR chief operating officer and deputy project manager.
“The improvements made to the Saltstone Hopper Overflow Container demonstrate an impressive blend of expert design and skillful labor,” Schmitz said. “The improved system not only mitigates risk to the facility, but it also removes a significant burden on our maintenance and operations crews.”
-Contributor: Colleen Hart
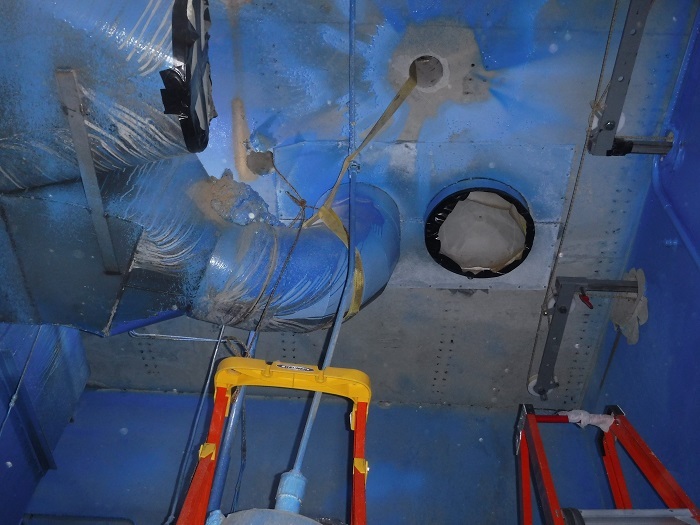 Workers at the West Valley Demonstration Project prepare a section of a ventilation duct to be cut inside the Vent Wash Room. The room had been used to support former reprocessing cells inside the Main Plant Process Building.
WEST VALLEY, N.Y. – EM workers continue to reduce risks and prepare to deactivate the Main Plant Process Building (MPPB) for what will be the West Valley Demonstration Project’s (WVDP) most complex demolition since crews knocked down the Vitrification Facility in 2018.
As part of the latest work, crews are removing a 26-inch-diameter ventilation duct that carried exhaust from past operations at the MPPB. They are performing the work remotely to reduce exposure risk.
“The effort in the Vent Wash Room involves extensive planning and deliberate execution to perform the work safely and compliantly,” said Steve Bousquet, EM WVDP deputy federal project director for the Main Plant. “The WVDP team continues to reduce legacy risks while protecting employees, the public and the environment.”
The Vent Wash Room had housed a ventilation "scrubber” that removed airborne particulates resulting from fuel reprocessing operations that ceased in 1972. The location supported former reprocessing cells inside the MPPB.
EM and prime contractor CH2M HILL BWXT West Valley (CHBWV) have completed 14 of 28 cuts to the ventilation duct and removed seven of 19 sections of the duct from the Vent Wash Room. Prior to this work, crews constructed a containment tent above the work area and an access door to support the project.
“Close work activities like this involve teamwork and sharing lessons learned throughout the process,” said Tom Dogal, CHBWV facility disposition manager. “The WVDP team used employee feedback to further improve execution while also adhering to enhanced COVID-19 protocols.”
Several other areas within the MPPB — including the product purification and chemical process cells, and a fuel receiving and storage facility — sent exhaust to the Vent Wash Room through the ductwork. The exhaust was then directed to a ventilation exhaust cell where it was filtered before being discharged to the plant’s stack.
-Contributor: Joseph Pillittere
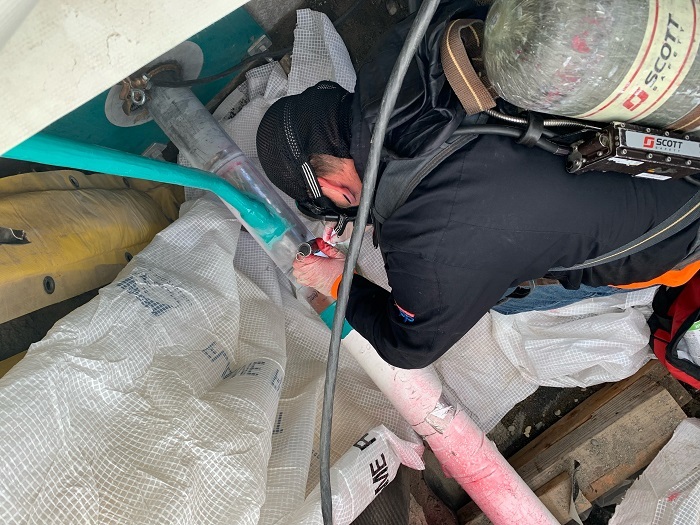 A worker installing new waste transfer lines between large, underground tanks and Hanford’s evaporator facility welds a secondary encasement on one of the lines. The project is on track for completion by the end of 2022 and will support the treatment of tank waste for disposal as part of the Direct-Feed Low-Activity Waste Program.
RICHLAND, Wash. – As the Hanford Site prepares for the start of operations to treat tank waste for disposal, workers are upgrading a number of facilities to ensure they are ready to support around-the-clock operations.
At the 242-A Evaporator, workers are upgrading equipment used to remove water from tank waste and systems that transfer waste to and from large, underground tanks near the facility. The upgrades will also extend the evaporator facility’s service life.
“Using the evaporator to create waste storage space in the double-shell tanks allows us to continue to retrieve waste from single-shell tanks and strategically stage waste for the next era of cleanup at Hanford, treating tank waste via the Direct-Feed Low-Activity Waste Program,” said Delmar Noyes, EM Office of River Protection (ORP) assistant manager for Tank Farms.
Located in Hanford’s 200 East Area near underground storage tanks and the Waste Treatment and Immobilization Plant, the evaporator boils waste at low pressure in steam heat to evaporate water from the waste. The resulting waste slurry is transferred back to a nearby double-shell tank farm, known as AW, for continued safe storage. The evaporated water is filtered and transferred to Hanford’s nearby Effluent Treatment Facility for additional treatment and disposal.
ORP tank operations contractor Washington River Protection Solutions (WRPS) has installed new waste transfer piping connections, called nozzles, in the AW Farm and the evaporator facility. To minimize worker exposure to radiation while installing nozzles at the evaporator, workers drilled through 22-inch-thick reinforced concrete walls that provide shielding from outside the building. Now, workers are making progress on the next phase of the project, installing new, double-walled waste transfer lines.
“Work is now focused on excavating trenches that are up to seven feet deep in some areas between the AW Farm and the evaporator, and welding together sections of transfer lines. In all, workers will install more than 1,200 feet of transfer lines,” said Dustin May, project manager for WRPS.
The project is scheduled for completion by the end of 2022, well ahead of the projected start date of tank waste treatment operations.
-Contributor: Mark McKenna
New EM senior leader Jay Mullis shared the cleanup program’s priorities and strategic vision in addressing two key stakeholder groups recently.
Mullis assumed duties on Nov. 1 as acting associate principal deputy assistant secretary for regulatory and policy affairs. The former field manager of the Oak Ridge Office of Environmental Management is no stranger to interactions with state regulators and community leaders.
On Nov. 16, Mullis met with regulators from the National Governors Association’s Federal Facilities Task Force. He provided a comprehensive update on EM’s radioactive waste management program, including progress being made on disposition of tank, transuranic and low-level radioactive wastes.
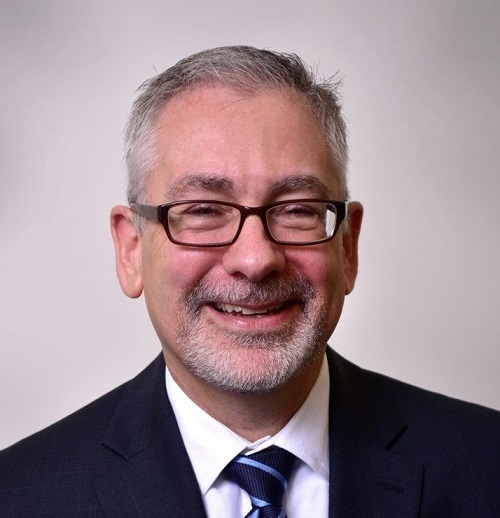 |
|
Jay Mullis has met with two key stakeholder groups since assuming duties as EM’s acting associate principal deputy assistant secretary for regulatory and policy affairs on Nov. 1. |
On Nov. 17, Mullis conferred with DOE’s State and Tribal Government Working Group (STGWG). Raymond Martinez, representing the Pueblo de San Ildefonso, of New Mexico, outlined improved communications, natural resource damage assessment and climate resiliency as key areas of interest to tribal nations. Mullis shared EM’s priorities, stating “EM’s mission is more than just tearing buildings down. it’s about meeting our obligations to the most impacted communities.”
The meeting also provided a focused discussion on DOE’s Long-Term Stewardship Working Group and a follow-up discussion on DOE’s Climate Adaptation and Resiliency Plan.
“There were many thought-provoking ideas shared,” said EM Tribal Affairs Program Manager Jill Conrad, adding that many STGWG priorities align with Biden administration goals.
Established in 1989, STGWG includes representatives from states and tribes near DOE sites or facilities. The Federal Facilities Task Force, formed in 1993, brings together governor-designated representatives from states near DOE sites or facilities.
|