 At the height of the Cold War, the Ford Building was used to test components used in five nuclear reactors at the Savannah River Site. An excavator is shown here removing a section of the facility’s metal roof.
AIKEN, S.C. – EM has completed demolition of a large metal storage building at the Savannah River Site (SRS) that formerly contained mechanical systems used to remotely raise and lower control rods within nuclear reactor vessels during the Cold War.
Made by the Ford Motor Company, these control systems played an important role within the site’s now dormant reactors.
The teardown of the facility, known as the Ford Building, brings the number of structures that have been deactivated and decommissioned at SRS to 292.
“We no longer need to incur the ongoing costs associated with maintaining obsolete structures like the Ford Building. We can safely and efficiently demolish unneeded buildings to eliminate the need for surveillance and maintenance, while preventing any potential release of hazardous substances to the environment,” said Steve Conner, a project manager with Savannah River Nuclear Solutions (SRNS), the site’s management and operations contractor. “These are all good reasons to move forward and prepare for the next building to be safely demolished.”
Workers will seal the Ford Building’s original concrete flooring with six inches of new concrete.
Decades ago, employees at the Ford Building worked daily on hundreds of control rod assemblies, which were used to ensure a stable nuclear criticality within reactor vessels, said Grady Friday, SRNS decontamination and decommissioning project lead.
“Ford was making more than cars in those days,” Friday said.
A system at the facility could insert or withdraw a control rod at a slow, steady rate to fine tune reactor operations. In the event of an emergency, the system allowed neutron-absorbing rods to drop, using gravity in the reactor core to slow or stop the reactor.
Later, the Ford Building was reconfigured to function as a repair facility for nuclear reactor heat exchangers. These devices removed heat from heavy water used to control the temperature within a reactor vessel by transferring the heat to water circulating inside the exchanger.
“Along with the heat exchangers came the potential for radioactive contamination,” said Friday. “A large metal-walled containment room was built within the Ford Building with a negative air flow system that exhausted air through HEPA (high-efficiency particulate air) filters to remove any potential radioactive particles. The room was about 100 feet long and 40 feet wide.”
-Contributor: DT Townsend
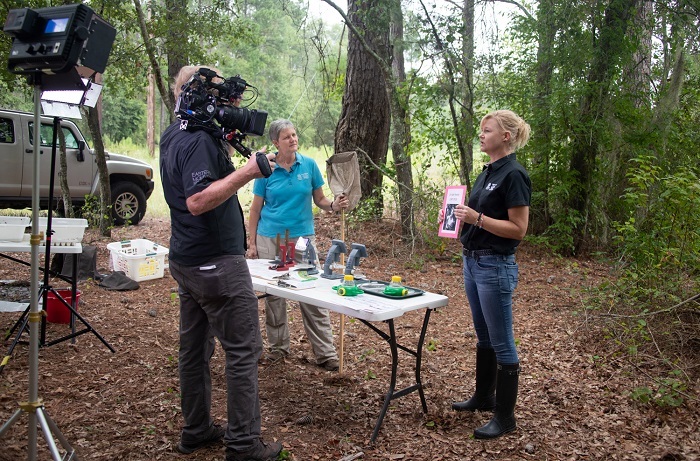 Savannah River Nuclear Solutions (SRNS) is creating a series of videos and learning resources to bring Savannah River Site (SRS) ecology to classrooms in place of traditional field trips to SRS. Beth Eberhard, left, and Kimberly Fickling, both with the University of South Carolina Aiken Ruth Patrick Science Education Center, are shown working on the lesson “Wet Wonders.” SRNS employee Brad Bohr is recording the presentation.
AIKEN, S.C. – With popular environmental field trips to the Savannah River Site (SRS) on hold due to the COVID-19 pandemic, EM contractor Savannah River Nuclear Solutions (SRNS) is bringing the site visit experience to the students virtually.
SRNS has hosted local students as part of its Science and Technology Enrichment Program (STEP) for many years. Now, SRNS is conducting virtual field trips to benefit students from elementary school to high school, and the first lesson is called “Wet Wonders.” It allows students to study biotic factors that determine the health of a pond by capturing and examining macro invertebrates.
“This lesson provides a great demonstration of the groundbreaking work of environmental research pioneer Dr. Ruth Patrick who was hired by SRS in the 1950s to do a baseline study of the environmental health of the site prior to construction,” said Kim Mitchell, with the SRNS education outreach division.
Mitchell noted that educators can play a series of videos for their students or request representatives from the University of South Carolina Aiken Ruth Patrick Science Education Center (RPSEC) to visit their classrooms. Teachers or the RPSEC representatives can also provide materials such as water samples containing aquatic creatures. Combined with the videos, this classroom “virtual field trip” creates an experience comparable to a real-time visit to a pond at SRS.
Since the in-person field trips were paused earlier this year, Mitchell and her team have been reorganizing nearly all of their outreach programs in an effort to remain relevant to the education community.
“We’re definitely going virtual within our competitive programs such as Future City, Science Bowl, and Science Fair,” said Mitchell. “We may use a combination of options related to our science and literacy outreach programs involving teach-ins at area middle schools and the Innovative Teaching Mini-Grants Program for educators.”
The virtual approach to field trips allows organizers to reach a larger number of students, said Francine Burroughs, manager of the SRNS talent management and education outreach divisions.
“Even our employee volunteers have been stepping it up, eager to assist in finding new ways to reach students in this new virtual world, particularly regarding our STEM-based (science, technology, engineering and math) programs and events,” Burroughs said.
STEP provides hands-on STEM opportunities through real-world, issues-oriented investigations that focus on responsible environmental stewardship. Supported by DOE-Savannah River, SRNS, RPSEC, the National Audubon Society, and the U.S. Forest Service, the program is offered to educators and students in the region around SRS.
-Contributor: DT Townsend
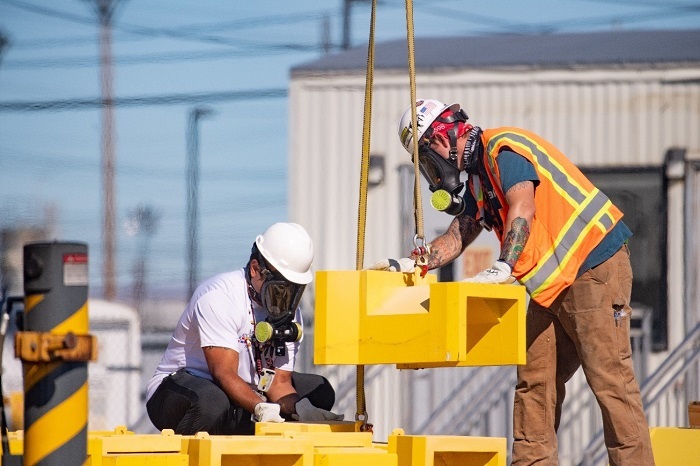 Hanford tank operations contractor Washington River Protection Solutions recently received an award from the National Safety Council, recognizing workers for their engagement in workplace safety programs and commitment to sharing a safety mindset in the local community.
RICHLAND, Wash. – EM Hanford tank operations contractor Washington River Protection Solutions (WRPS) recently received the National Safety Council’s Community Advancement Award, an honor that recognizes companies for a commitment to safety performance in two distinct areas: employee-led safety programs, and safety outreach and engagement in the community.
WRPS has been involved in the DOE Voluntary Protection Program, accident prevention councils, and creation of employee-generated safety videos.
“This award is well earned,” said Bradley Eccleston, safety and health manager for EM’s Office of River Protection. “WRPS has a critical role in the Hanford cleanup mission and has consistently provided safety innovation and leadership amongst the workforce and within the community.”
WRPS employees also support the community after work hours through conducting safety briefings for local Habitat for Humanity projects; sharing use of robotics and engineering innovations with local schools, colleges, and universities; and volunteering with food drives and fundraising initiatives to aid programs focused on families.
“Our team continues to safely complete mission-critical work, increase safety performance, and collaborate with our community partners to promote the safety and well-being of others,” said John Eschenberg, WRPS president and CEO. “I am proud to be part of this team and see our workers’ dedication recognized by a distinguished national organization.”
WRPS has been safely completing significant projects at the tank farms for the past 12 years, with a focus on the EM 2020 priority of completing Direct-Feed Low-Activity Waste construction and turnover to commissioning. Recently, WRPS completed successful testing of the Tank-Side Cesium Removal system, which will pretreat low-activity waste.
-Contributor: Jack Donnelly
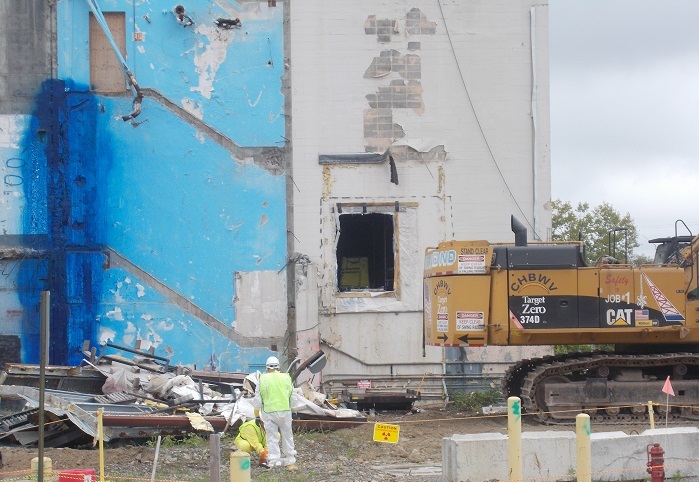 WEST VALLEY, N.Y. – Demolition crews at the West Valley Demonstration Project (WVDP) recently demolished an acid recovery cell airlock and lift table. The cell was used in reprocessing, where processed liquids, such as acid, were recovered and filtered for reuse. This 100-square-foot structure was constructed in early 2009 to support asbestos-containing material abatement, decommissioning, and vessel removal from the cell. The airlock had a lift table that brought containers to the top of the acid recovery cell; waste containers were loaded and then lowered back down. A fork truck could then lift and remove the waste box out of the airlock. The photo at top shows the project underway, while the photo immediately above shows completion of the demolition.
-Contributor: Joseph Pillittere
|