Workers install a new hoist in the Main Plant Process Building to be used for moving waste boxes and drums and other work when the West Valley Demonstration Project returns to full operations.
WEST VALLEY, N.Y. – An EM facility disposition crew recently replaced a hoist in the Main Plant Process Building, marking the West Valley Demonstration Project’s (WVDP) first work activity in which workers donned personal protective equipment while following safety protocols due to COVID-19.
Replacing the hoist in the Equipment Decontamination Room, as WVDP operated in an essential mission-critical posture, also signified progress toward a broader project — the future demolition of the Main Plant Process Building — included in EM’s priorities for 2020.
The new equipment will be used to shift an aerial lift into a chemical process cell and move boxes and drums filled with waste when the site returns to full operations and crews resume deactivation work inside a former reprocessing cell in the building.
Before replacing the hoist, employees discussed questions and concerns with supervisors and senior staff in a collaborative, inclusive manner. The discussions focused on how to maintain social distancing while helping one another don and doff personal protective equipment, including respirators.
The team agreed to a safe approach in which employees maintain six feet of distance when possible and wear face masks. Only one worker at a time is allowed to exit an area to avoid clustering, and they must cover the respirator exhalation ports with towels to reduce exhaled vapor droplets from escaping while the workers help each other put on equipment, among other things.
EM WVDP Safety and Site Programs Team Leader Jennifer Dundas commended the team members for their pre-job briefing and work.
“Encouraging employees to speak freely when confronting an issue or challenge is the best way to solve a problem,” Dundas said. “It fosters the sharing of ideas and allows everyone an opportunity to be part of the solution. In the end, their agreed-upon solution helped them to safely complete this work activity.”
Lessons learned from the project will be applied to future cleanup work at the site. The lessons include the importance of refocusing on safety, being aware of changing conditions and new protocols, and getting reacquainted with procedures, work packages, and radiation work permits.
-Contributor: Joseph Pillittere
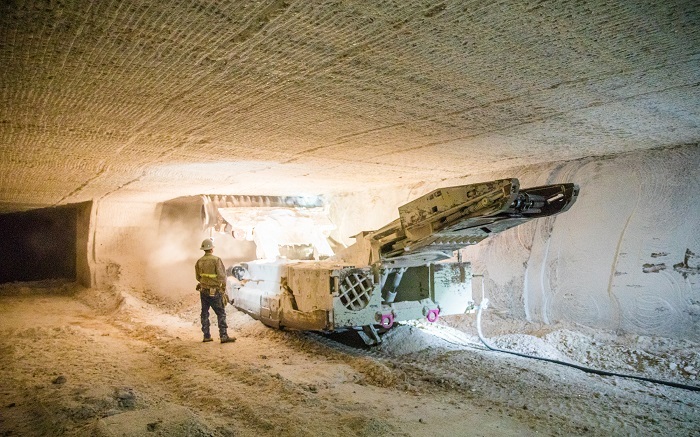 A worker operates a continuous mining machine 2,150 feet underground at the Waste Isolation Pilot Plant to create additional disposal rooms for transuranic waste. The rooms are carved out of 250-million-year-old bedded salt formation and measure 33 feet wide by 13 feet high, and are as long as a football field minus the end zone.
CARLSBAD, N.M. – EM’s Carlsbad Field Office (CBFO) recently released the fiscal 2019 fee determination for Nuclear Waste Partnership (NWP), the management-and-operations contractor for the Waste Isolation Pilot Plant. In total, NWP earned approximately $14.3 million, representing 83 percent of the total fee available in fiscal 2019. NWP’s fee determination included approximately $3.3 million in subjective award fee, or 76.1 percent of the available award fee. The contractor also earned approximately $11 million in fee tied to a set of performance-based incentives (PBIs), or 85.2 percent of the total available.
“I carefully considered the contractor’s performance in five areas of the fiscal year 2019 performance evaluation measurement plan in determining the fee award,” said Kirk Lachman, who served as the CBFO deputy manager and fee determination official.
The award fee determination for NWP’s performance in fiscal 2019 was based on the following five subjective criteria:
- Mission performance
- Regulatory compliance
- Management performance
- Safety and health performance
- Cost control
Some of NWP’s accomplishments in fiscal 2019 were:
- Implemented significant improvements to the transuranic (TRU) waste emplacement processes and procedures that allowed the contractor to maintain shipping rates at eight to 10 shipments per week in fiscal 2019.
- Initiated the first use of a battery electric load haul dump truck in the underground, improving the underground air quality.
- Developed and implemented a plan for recovery of a breached cesium source for another federal organization.
EM also noted several areas for improvement, including the need to address longstanding issues to prevent them from developing into more significant problems; compliance with nuclear safety requirements; untimely resolution of issues; and subcontractor oversight.
NWP also had the ability to earn fee tied to PBIs, which represented specific milestones or metrics. The PBIs available for NWP in fiscal 2019 included improved safety in underground operations; additional WIPP underground air supply ventilation flow rate; WIPP line item capital asset projects; general plant projects, infrastructure projects, and major maintenance activities; radiological protection improvements; and TRU waste emplacement.
More information on WIPP’s fiscal 2019 fee determination, including NWP’s fee scorecard, can be found here.
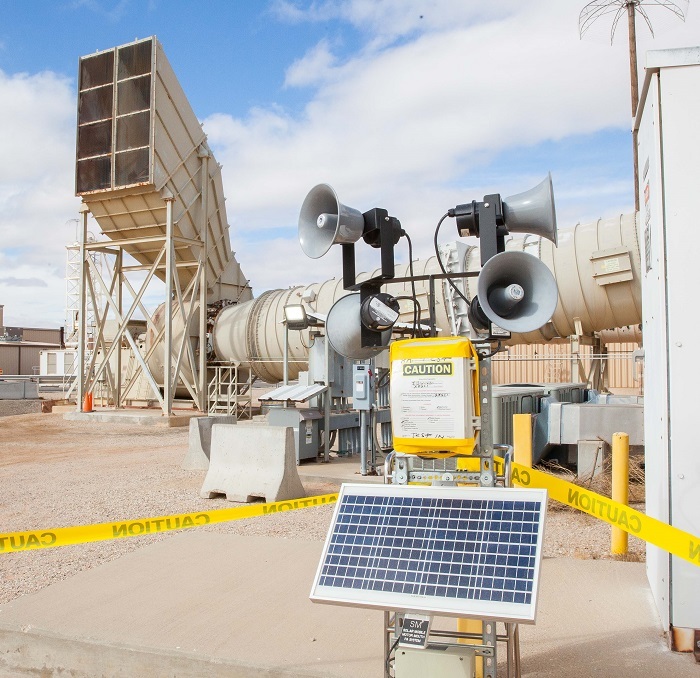 The Waste Isolation Pilot Plant’s most recent maintenance outage included work on ventilation fan motors and systems, shown here.
CARLSBAD, N.M. – EM Waste Isolation Pilot Plant (WIPP) workers completed an immense amount of work during a two-day planned power outage that occurred while the site operated in an essential mission-critical posture due to the COVID-19 pandemic.
The WIPP engineering, maintenance, and operations departments completed a lengthy to-do list during the outage that uncoupled power from the WIPP core, including the waste handling. It was the culmination of a two-week push to complete projects during the mission-critical period.
“Each individual involved with this work scope showed several core values like ownership, respect, continuous improvement, and teamwork,” WIPP operations manager Don McBride said. “While we did have some hurdles to clear, each individual pushed through these challenges and we accomplished this work as a team.”
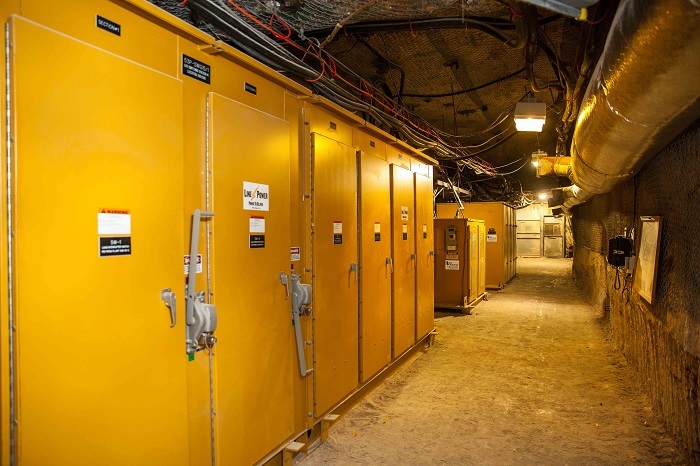 Substations in the Waste Isolation Pilot Plant underground power everything from computers to giant mining machines.
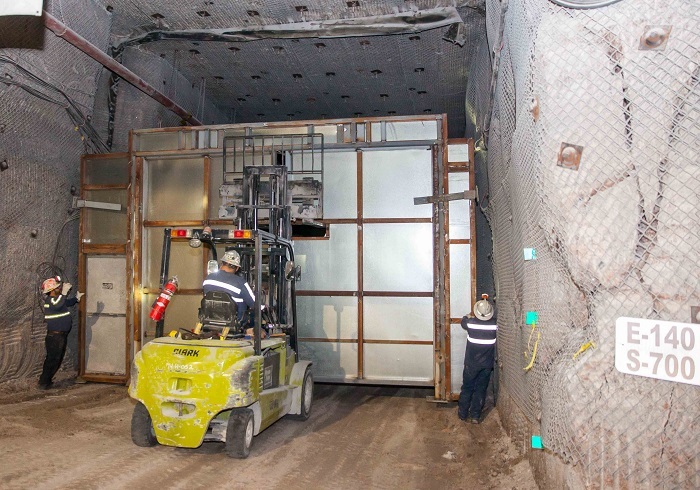 Bulkheads such as this one being installed in the Waste Isolation Pilot Plant (WIPP) underground help control airflow in different loops, or circuits. During the recent maintenance outage, remote controls connected to WIPP’s Central Monitoring Room were added to some bulkheads.
Completed work included extensive transformer and substation maintenance. Substations in the WIPP underground power everything from desktop computers to giant mining machines. Substations take a 13,800-volt feed from a commercial provider and “step down” the high voltage into usable voltages at the site. Workers also finished preventive maintenance on waste hoist circuit breakers, and preventive maintenance, testing, and other work on ventilation fans.
Crews also performed work on three bulkheads, which help control airflow in different loops in the WIPP underground, and added remote-control capability to a louvered bulkhead, known as a regulator, that can redirect air from one circuit to another. A large rollup door between a processing bay and the waste hoist was repaired, and a longstanding connectivity issue between a fire alarm panel and the underground evacuation lights system was fixed.
An audible alarm was added to the shutdown process for the Supplemental Ventilation System, alerting the Central Monitoring Room in the event the system shuts down. Workers also completed updates to the central monitoring system, which monitors all critical systems at the site and funnels information to the Central Monitoring Room, which is staffed around the clock.
-Contributor: Roy Neese
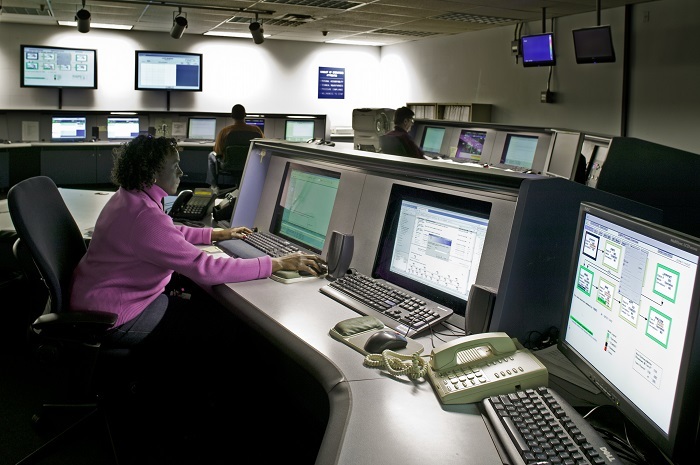 Janice Sandford, forefront, and other operators are shown in the Defense Waste Processing Facility control room. Savannah River Remediation recently upgraded its control system hardware and software.
AIKEN, S.C. – The EM program at the Savannah River Site (SRS) has completed a significant and extensive upgrade to modernize computer systems across the site's liquid waste facilities and maintain cybersecurity industry standards.
In a two-and-a-half-year process, SRS liquid waste contractor Savannah River Remediation (SRR) upgraded the distributed control system (DCS) to a newer platform and completed an entire computer hardware refresh. The DCS is a specially designed automated control system software with physical control elements located throughout SRS liquid waste facilities, including the Defense Waste Processing Facility, Saltstone, and the Tank Farms. These facilities use processing equipment and instrumentation monitored and controlled by operator personnel via the DCS.
More than 100 physical DCS controllers throughout the facilities were replaced to be compatible with the new, modern software and its processor requirements. The control system software consists of these controllers within each facility, all connected by a communications network. The controllers are used to interface with the facility equipment and instrumentation.
This upgrade was a multimillion-dollar infrastructure improvement effort and a key part in the overall push for upgrading liquid waste systems, according to SRR Chief Operating Officer and Deputy Project Manager Mark Schmitz.
“Planning for and executing infrastructure improvements is key to ensuring reliable operations, all with an eye toward our core value of continuous improvement,” Schmitz said. “This project is one on the many infrastructure projects happening at SRR to ensure liquid waste operations continue to be robust and efficient well into the future.”
Detailed planning went into this project, including use of offline development and test systems beforehand, and involved people from numerous groups within SRR. The upgrade was successfully implemented with minimal facility operational impacts.
The DCS upgrade was an effort included in SRR’s strategic plans to position the liquid waste system to safely operate at higher throughput rates necessary to support the near-term start of operations of the Salt Waste Processing Facility.
-Contributor: Colleen Hart
|