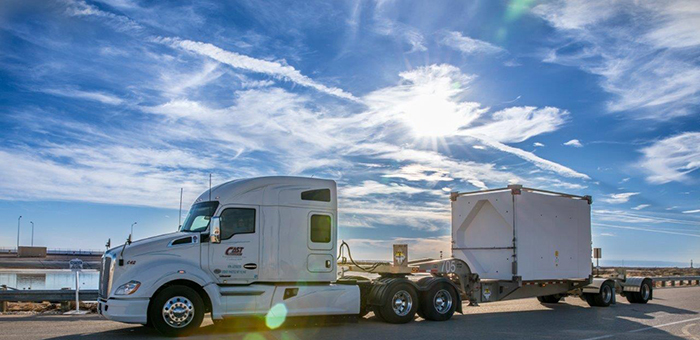 The first Transuranic Package Transporter Model 3 cask shipped in six years recently arrived at EM's Waste Isolation Pilot Plant.
CARLSBAD, N.M. – The Waste Isolation Pilot Plant (WIPP) recently accepted its first large-box cask in six years, the culmination of a long process toward a major goal. The shipment came from the EM program at the Savannah River Site (SRS).
The Transuranic Package Transporter Model 3 (TRUPACT-III) cask allows an EM generator site to package and ship large-sized defense transuranic waste in a single box that would otherwise have to be broken down into smaller waste boxes.
Large transuranic waste includes contaminated glove boxes, used motors, and large-scale analytical equipment. The TRUPACT-III cask, just over 8 feet square and 14 feet in length, weighs about 50,000 pounds loaded and is transported on a custom designed trailer. By comparison, the workhorse TRUPACT-II weighs up to 19,250 pounds loaded.
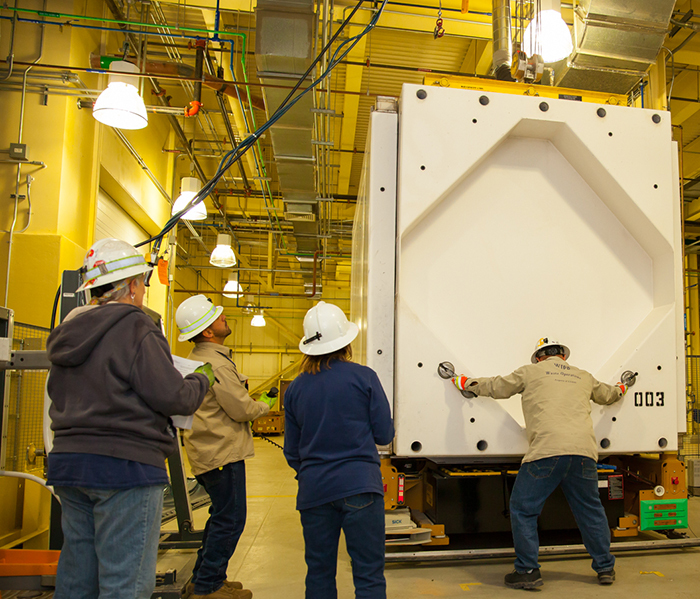 A worker removes the 6,000-pound cover of a Transuranic Package Transporter Model 3 cask during a practice session at the Waste Isolation Pilot Plant.
The TRUPACT-III accelerates the pace of cleanup at EM sites across the DOE complex and reduces risk to worker safety.
To get the casks back to work, though, was not a simple process. Teams at both SRS and the WIPP receiving facility were retrained and recertified for the effort. Workers ensured equipment used six years ago was in working condition.
“Implementation of new waste certification requirements and readiness performance allowed WIPP to add these standard large boxes back into the portfolio of waste packages, which can be safely shipped to WIPP for disposal,” said Mark Pearcy, chief operating officer and deputy operations manager of Nuclear Waste Partnership, the WIPP management and operations contractor.
“I’m very proud of this accomplishment, which only occurred through the teamwork of the Savanah River Site waste generator, the National TRU Program, and WIPP,” Pearcy said.
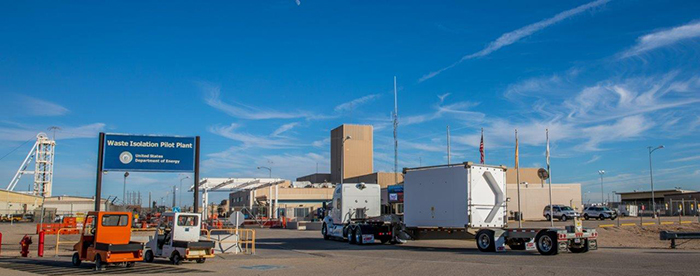 A truck hauling the first Transuranic Package Transporter Model 3 cask shipped in six years pulls up to the front gate at the Waste Isolation Pilot Plant (WIPP). The tower in the background, at center, houses a waste hoist that transports transuranic waste to the WIPP repository, 2,150 feet below the surface.
An automated transporter that the TRUPACT-III rides atop was overhauled, and workers were retrained in its use. Also repaired was the payload transfer station where large boxes are pulled from the cask and transferred to a pallet for processing.
The automated transporter carries the TRUPACT-III into a separate bay from the TRUPACT-II’s inside WIPP’s waste handling area. The cask’s multiple-bolt front end is removed and stood up in a storage rack before the box inside the cask is removed. Through the whole process, radiological control workers take readings inside and outside the cask.
The first TRUPACT-III came to WIPP in 2011, 12 years after the facility opened to take the nation’s defense transuranic waste. TRUPACT-III shipments were halted after a truck fire and unrelated radiological event in February 2014 temporarily closed WIPP.
All shipments are tracked using DOE’s Transportation Tracking and Communications satellite-based tracking and communication system. Its users have access to shipping schedules, emergency response information, and real-time positioning for each shipment.
-Contributor: Roy Neese
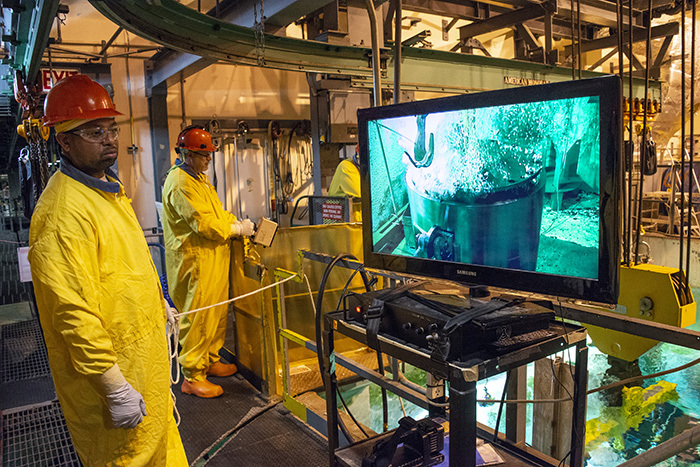 Savannah River Nuclear Solutions employees Erik Tucker, left, and Randy Fanning watch as the inner lid of a High Flux Isotope Reactor (HFIR) spent nuclear fuel shipping cask is removed under water in the L Area disassembly basin. Receipt and disposition of the HFIR fuel is part of SRS’ support of spent nuclear fuel disposition and DOE’s nonproliferation work.
Two Savannah River Site (SRS) contractors recently earned 95 percent or more of award fees available to them.
Savannah River Nuclear Solutions (SRNS), the SRS management and operations contractor, received an overall “very good” rating and more than $25.5 million — or 95 percent of the available award fee — for its performance from Aug. 1, 2018 through July 31, 2019.
Centerra-SRS received an overall “excellent” performance rating for the evaluation period of April 1, 2019 through Sept. 30, 2019 and an award of more than $3.1 million, or 97 percent of the available award fee.
EM releases information relating to contractor fee payments — earned by completing the work called for in the contracts — to further transparency in its cleanup program.
Savannah River Nuclear Solutions
Mike Budney, the DOE-Savannah River (DOE-SR) manager and fee determining official, noted SRNS safely performed its missions and pointed to the contractor’s illness and injury rates, which are well below EM's established goals.
“SRS has enjoyed a long history of supporting national defense, while maintaining the highest possible safety and security standards,” Budney said. “The site’s future success relies on our ability to continue developing innovative technologies and performing unique operations in a safe and compliant manner.”
Additional SRNS achievements noted in the fee determination scorecard include:
- Completed an accelerated deactivation strategy for Building 235-F and addressed the H Canyon exhaust tunnel.
- Finished a road culvert replacement and repavement project ahead of schedule and within budget.
- Renovated a building for a “one-stop shop” combining employee training, badging, and medical testing.
- Completed all regulatory milestones and commitments on or ahead of schedule, including management of over 560 site permits, and collection, analysis, and reporting of more than 10,000 environmental samples.
- Implemented a new streamlined process for managing regulatory compliance, replacing seven databases and tools and resulting in an estimated cost savings of $80,000 in the first year.
- Reached more than 30,000 students and educators through 14 science, technology, engineering and math (STEM) programs and events.
- Exceeded small business awards goals and received 12 small business achievement awards.
DOE-SR identified areas for improvement for SRNS:
- SRNS did not verify that subcontractor safety and health documentation was compliant with an amendment to regulatory requirements. SRNS requested subcontractors submit changes to relevant safety documentation based on the new regulatory requirements. No subcontractors provided modified documentation to reflect the amendment updates.
- Issues with equipment failures delayed an accelerated readiness assessment schedule.
View the SRNS fee determination scorecard for SRNS here.
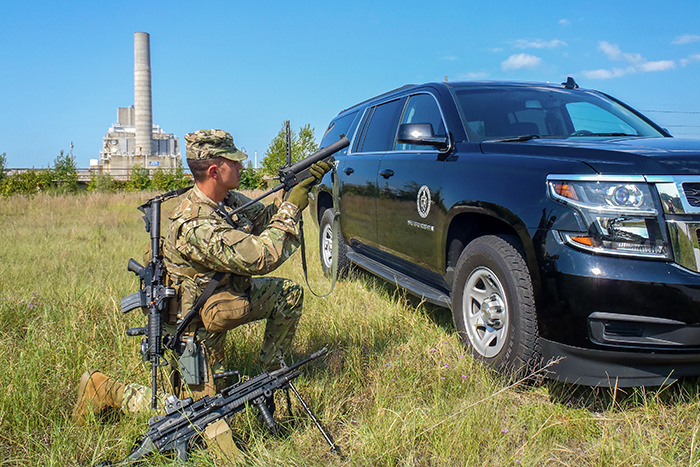 A Centerra-SRS employee simulates deployment of state-of-the-art weaponry at the Savannah River Site.
Centerra-SRS
The protective force services contractor demonstrated the effective and competent execution of the SRS security mission at the site perimeter barricades, in law enforcement operations, and at sensitive national security facilities in protection of special nuclear materials, according to the Centerra-SRS fee determination scorecard.
Budney said the Centerra-SRS achievements demonstrate overall excellent practices in protection of SRS national security interests and resources.
“Centerra-SRS has demonstrated a commitment to excellence in meeting the challenges ahead in support of ongoing critical missions,” he said.
Following are Centerra-SRS achievements noted in the scorecard:
- Officers conducted effective traffic enforcement and accident investigations; responded to over 2,600 calls for service; and issued just over 1,000 traffic citations and warning tickets.
- The aviation operations department was awarded the 2018 Jeff Snow Memorial Aviation Program Award, honoring the department as the top program within the DOE complex based on excellence, innovation, compliance, maintenance, training, and safety.
- Centerra-SRS safely and effectively conducted an exercise to assess safeguards and security elements employed in response to site-specific threats and over 160 other tests; supported nine facility emergency management drills; and conducted an annual drill to ensure compliance with emergency management response actions.
The evaluation noted performance deficiencies in the area of protective force operations and training that included three individual single point failures involving inefficient entry control inspections or inattention to duty, and housekeeping matters associated with excess equipment and ammunition. Each of the deficiencies were thoroughly addressed with appropriate investigation and corrective actions, according to the scorecard.
View the Centerra-SRS fee determination scorecard here.
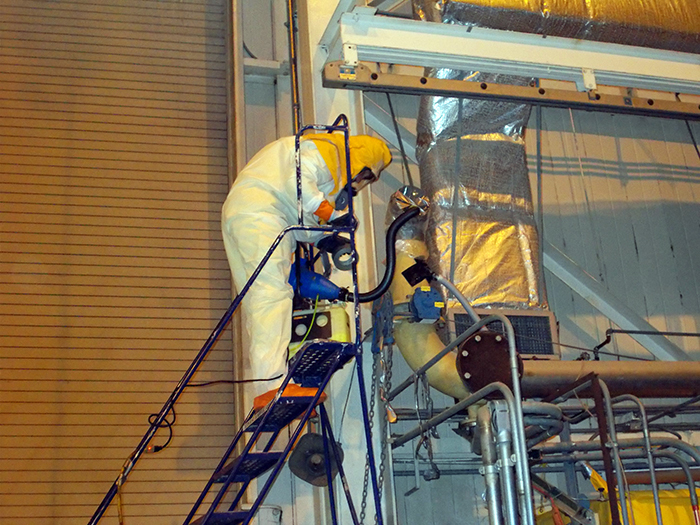 An operator inside the former fuel receiving and storage facility at the West Valley Demonstration Project Site pumps a fogging agent inside a pipe to fix suspected contamination. This work was part of deactivating the building for eventual demolition.
WEST VALLEY, N.Y. – An EM crew recently finished deactivating a facility at the West Valley Demonstration Project (WVDP) Site after safely removing asbestos-containing material.
Piping and insulation inside the former fuel receiving and storage facility contained the material that needed to be removed to prepare for eventual demolition. Workers pulled out 700 feet of piping — equivalent in length to about 17 school buses end to end — over five months.
“This team used their combined knowledge and lessons learned from previous asbestos-containing material work activities to safely complete this project,” EM WVDP Federal Project Director Steve Bousquet said. “The safe and compliant disposition of asbestos-containing material is another important step in the progress towards the future demolition of this facility.”
Other deactivation work at the facility included isolating piping, applying fixative to piping, and relocating two 69,000-pound waste containers.
The building was used from 1965 to 1972 to receive and store spent nuclear fuel before it was reprocessed to recover reusable plutonium and uranium.
Bill Freaney, a deactivation and decommissioning crew foreman with CH2M HILL BWXT West Valley, EM’s WVDP cleanup contractor, commended his crew members for their hard work and dedication to safety during the project.
“Working with asbestos-containing material is the most physically challenging work at the site when you include radiological and industrial hazards, layers of protective clothing, and limited mobility,” Freaney said. “This crew used lessons learned to enhance safety, improve efficiency, and reduce exposure to job related hazards. They put their collective knowledge into practice.”
-Contributor: Joseph Pillittere
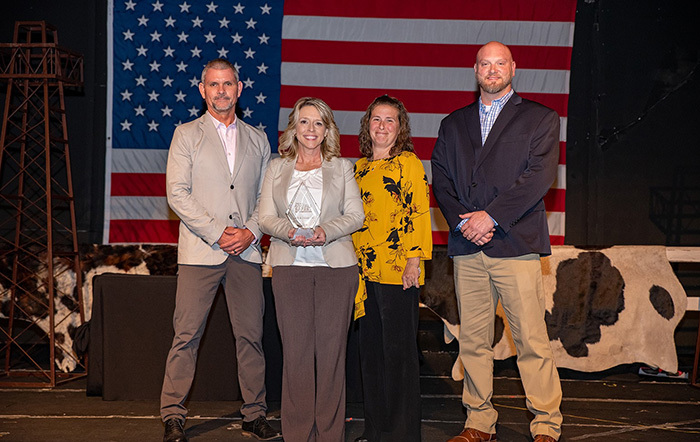 Swift & Staley Inc. employees accept the EHS Today America’s Safest Company award in Dallas, Texas late last year. Pictured from left are John Hobbs, environment, safety and health manager; Tammy Courtney, vice president and project manager; Angie Gilbert, safety team secretary; and Jason Gilbert, United Steel Workers safety representative.
PADUCAH, Ky. – The environment health and safety magazine EHS Today has named EM’s prime infrastructure contractor at the Paducah Site as one of America’s Safest Companies.
Every year, EHS Today recognizes companies with exceptional occupational safety, health, environmental, and risk management efforts. Swift & Staley Inc. (SSI) was one of 16 companies honored at the publication’s safety leadership conference in Dallas, Texas late last year.
“SSI’s safety and health program is founded on the philosophy that all accidents are preventable, and that safety is the first priority for all work,” said Tammy Courtney, SSI project manager. “Safety is not a program layered on top of the real work, but is an integral part of doing any work. SSI is not a ‘safety right now’ company but a ‘safety always’ company.”
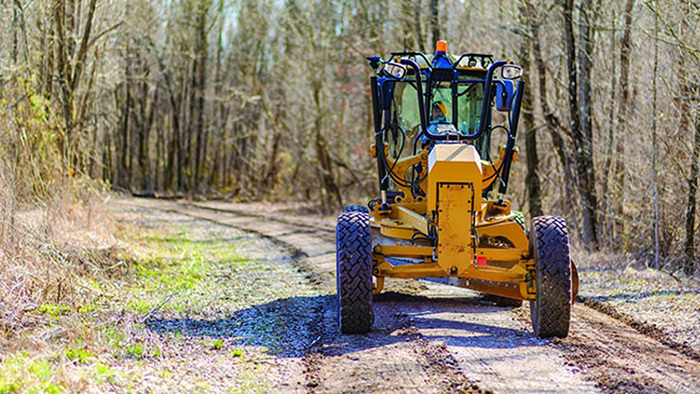 Heavy Equipment Operator Jeff Walls grades one of the 32 miles of roads maintained by Swift & Staley Inc. at the Paducah Site.
SSI’s primary responsibilities at the Paducah Site include roads and grounds maintenance, janitorial services, safeguards and security program management, information technology and cybersecurity, radiological monitoring services, records management and document control, facilities maintenance, property management, and training.
EHS Today identifies companies that meet criteria for America’s Safest Companies, such as support from leadership and management for environmental, health, and safety efforts; employee involvement in those efforts; innovative solutions to safety challenges; and good communication about the value of safety.
The Paducah Site is situated on 3,556 acres in western Kentucky. Built as part of the U.S. nuclear weapons complex, the gaseous diffusion plant enriched uranium from 1952 to 2013, originally for military reactors and nuclear weapons, and later for commercial nuclear power fuel.
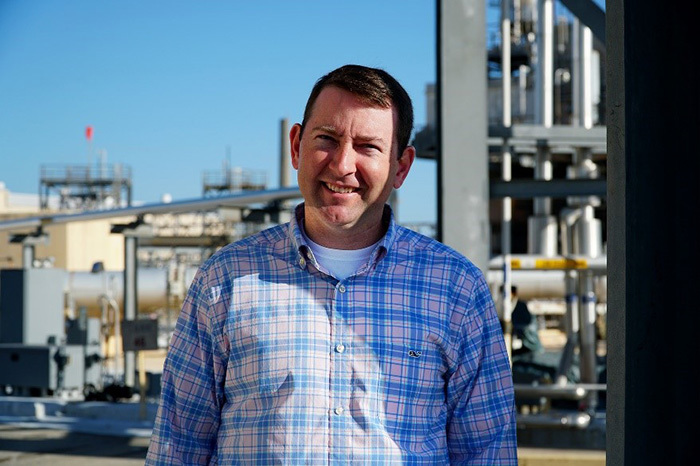 Savannah River Remediation Project Controls Specialist Patrick Cunning pictured at F Tank Farm.
AIKEN, S.C. – As a former college golfer and current project controls specialist, Patrick Cunning is navigating the course of costs and schedules for tank closure project teams at EM’s Savannah River Site (SRS).
A lifelong Aiken resident, Cunning graduated from the University of South Carolina, where he played college golf alongside classmates who now hold Professional Golfers’ Association tour cards.
Being part of a team and competing in golf through high school and college prepared Cunning for his responsibilities at SRS, where he works for Savannah River Remediation (SRR), the site’s liquid waste contractor.
“Asking questions has enabled me to learn ways to continuously improve and develop new skills,” Cunning said. “I take pride in my game on the golf course and also in what I provide my company, because we are each a part that represents the team.”
Cunning provides project controls support for tank closure, helping prepare waste tanks for salt dissolution. In that process, radioactive salt waste is dissolved inside the tanks before it’s mixed into salt batches containing a chemical makeup suitable for processing at the future Salt Waste Processing Facility.
The analyses performed by Cunning and other project controls specialists track a project’s cost and schedule performance against its baseline to determine the project’s performance.
Cunning also worked with the SRR construction division to keep the Saltstone Disposal Unit (SDU) project on track. SDUs permanently store decontaminated salt solution — the result of processed salt waste — mixed with a cement-like grout, making saltstone.
Editor's note: In an occasional series, EM Update profiles early career professionals across the EM complex.
|