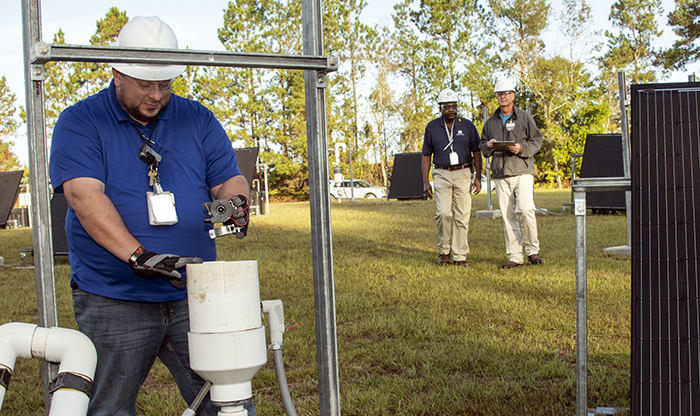 Savannah River Nuclear Solutions (SRNS) Mechanic Thad Ashely, foreground, checks components of a soil vapor extraction unit, as SRNS engineers Joao Cardoso-Neto, background, left, and John Bradley inspect solar panels.
AIKEN, S.C. – EM recently reached a milestone at the Savannah River Site (SRS) by fully transitioning to low-cost solar-powered technology to clean up solvents in a closed basin and the groundwater beneath it.
The system is expected to save about $200,000 a year, mostly due to the need for less electricity, equipment maintenance, and personnel.
For decades, SRS personnel have worked to remove nonradioactive degreasing solvents from the groundwater beneath the former pond-like body of water, known as the M-Area Settling Basin.
“All the water and the contaminated soil that formed the bottom of the basin were removed during the first phase of the project about 20 years ago,” said John Bradley, an engineer with EM contractor Savannah River Nuclear Solutions (SRNS). “Since that time, we’ve made significant progress remediating a large source of degreasing solvents found in the soil and groundwater beneath the former basin using an active remediation process referred to as dynamic underground stripping.”
In that process, steam is injected into the soil and groundwater to mobilize subsurface contaminants. A network of underground piping and equipment then extracts those contaminants. This system has removed about 500,000 pounds of the solvents from the location.
After years of remediation requiring that highly mechanized system, SRS now uses the solar-powered soil vapor extraction units, known as microblowers, to remove remaining solvents from groundwater beneath the earthen-capped basin.
Installed at multiple wells, these units generate a vacuum to exhaust the chemical vapors. Each unit requires only 20 to 40 watts of solar power to run its primary component, a compact, high-speed fan. A single unit removed 234 pounds of solvent compounds from the subsurface during a 10-month test.
“Early active groundwater cleanup projects at the M-Area Settling Basin concentrated on using more aggressive methods to separate and remove the contaminants from tens of millions of gallons of groundwater,” said Joao Cardoso-Neto, an SRNS project manager. Cardoso-Neto noted that these cleanup technologies require the power of large electric pumps, support facilities, and monitoring equipment.
The amount of degreasing solvents remaining at this location is now so small that the expense of using the highly mechanized methods cannot be justified when alternate low-cost methods are just as effective, Bradley said.
“The time had come to transition completely from active groundwater cleanup methods related to the M-Area Settling Basin Project to the passive microblowers,” Bradley said. “It was like going from a 60-horsepower blower to a hairdryer. We have high expectations of continued success at this cleanup site.”
Cardoso-Neto said SRS has a history of addressing complex environmental challenges with innovative technologies.
“Our plans are to continually move from active to passive methods to remediate soil and groundwater across the site. We are using several proven passive environmental cleanup systems that have had a major, positive impact. It’s a promising future for our cleanup programs at the Savannah River Site,” Cardoso-Neto said.
More than 60,000 pounds of nonradioactive contaminants, such as the degreasing solvents, have been removed from the groundwater beneath M Area since 2008 at a cost savings of more than $5 million, adding to the 1.6 million pounds of nonradioactive material have been removed beneath SRS since cleanup programs began at SRS in the 1980s.
-Contributor: DT Townsend
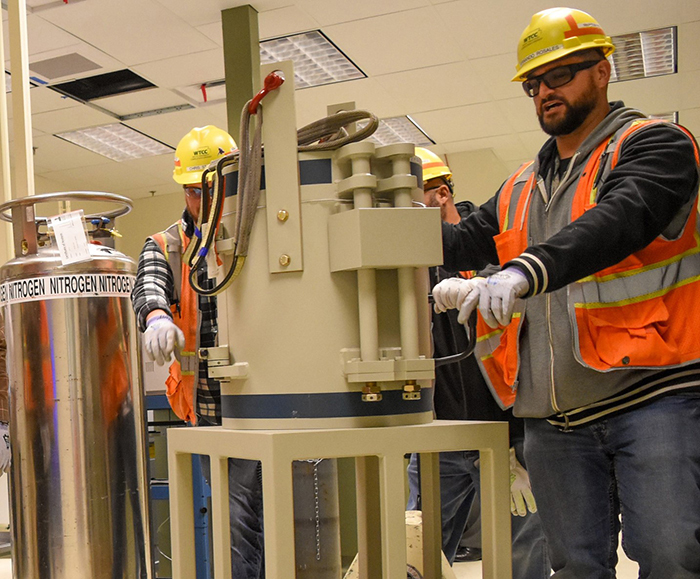 RICHLAND, Wash. – Construction is complete at the EM Hanford Waste Treatment and Immobilization Plant’s Analytical Laboratory, and work is now focused on installing scientific instruments and preparing the lab for commissioning. The instruments being set up will allow chemists to conduct a variety of chemical and radiological tests and analyses to confirm that glass produced by the Low-Activity Waste vitrification facility meets regulatory requirements and standards. Both facilities are integral to EM’s Direct-Feed Low-Activity Waste (DFLAW) program to begin tank waste treatment by the end of 2023. During DFLAW operations, chemists will analyze approximately 3,000 process samples annually. Installation of the instruments will continue throughout the fall. From left, Hanford Waste Treatment and Immobilization Plant laborers Chris Starkel, Noel Macias, and Fernando Rosales install a gamma-ray detector shield inside the laboratory.
-Contributor: George Rangel
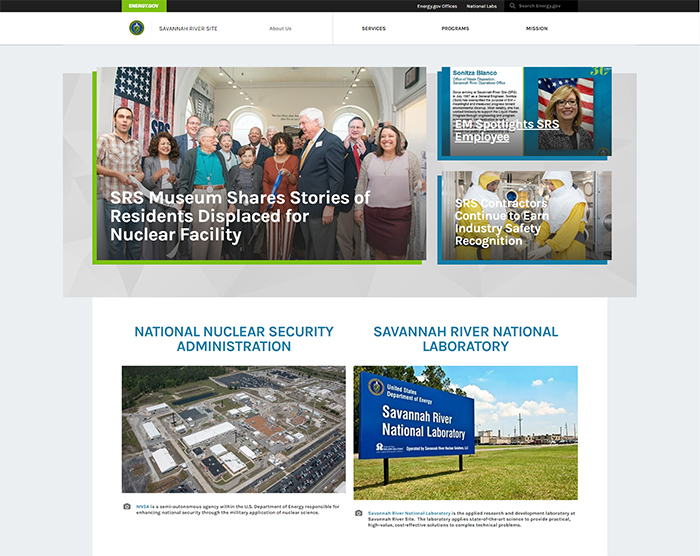 A view of the homepage for the new Savannah River Site website.
AIKEN, S.C. – DOE-Savannah River (DOE-SR) recently introduced a new user-friendly website with a simple design that delivers timely information about the missions of the Savannah River Site (SRS).
The new website features a similar look to EM’s website and is hosted on DOE’s www.energy.gov platform. It replaced the Savannah River Operations Office website and offers a variety of information for stakeholders, media, and the public.
The website will better showcase the information and services SRS provides online, DOE-SR Office of External Affairs Director Amy Boyette said.
“The new homepage features links to our most recent publications and press releases,” Boyette said. “The site navigation is structured to correspond to the EM website, making it easier to navigate and locate information about our programs.”
The homepage also provides convenient links to websites for the National Nuclear Security Administration and the Savannah River National Laboratory.
Other aspects of the website include information about the SRS tours program, the Savannah River Site Citizens Advisory Board, fact sheets, workforce demographics, and the site’s history.
The new website provides a more modern online experience with increased capabilities for mobile platforms and easily searchable content.
Visit the new SRS website here.
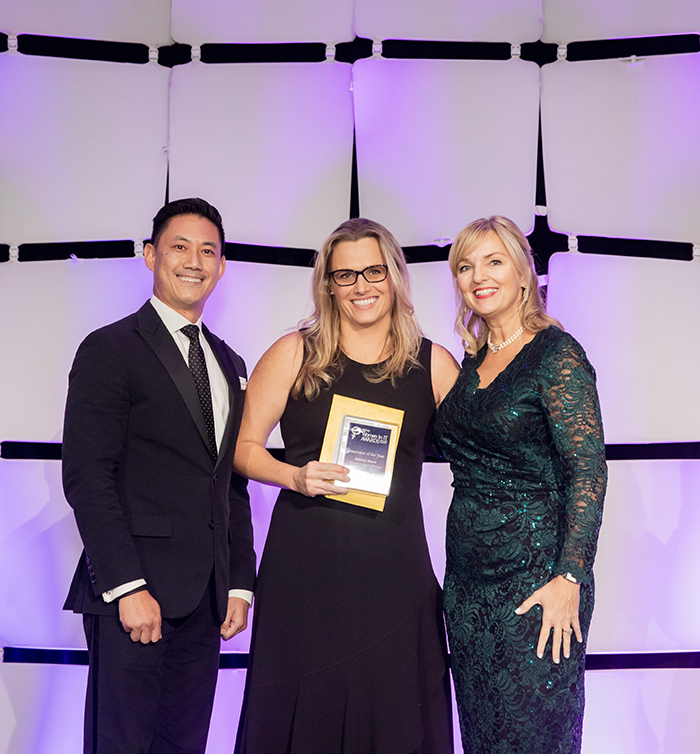 Ashley Ward, center, from EM Richland Operations Office contractor Mission Support Alliance, receives the Innovator of the Year Award at the 2019 Women in IT Awards Silicon Valley ceremony in San Francisco.
RICHLAND, Wash. – From a pool of more than 300 nominees, Ashley Ward, with EM Richland Operations Office contractor Mission Support Alliance (MSA), was recently selected for the Innovator of the Year Award at an event highlighting achievements by women in the information technology (IT) field.
Ward, who serves as MSA’s director of information systems, was integral to bringing new technology in water utility work to the Hanford Site, creating the potential to reduce costs, improve efficiency, and increase worker safety.
“I’m truly overwhelmed to receive this award,” Ward said following the 2019 Women in IT Awards Silicon Valley ceremony in San Francisco. “This could not have been possible without my great team and all of their hard work.”
Partnering with MSA’s public works organization, Ward and her team outfitted EM workers with augmented-reality headsets, providing them with more information readily available in the field and expanded communication capabilities.
Ben Ellison, chief information officer for the Hanford Site, said Ward is a fantastic leader who is always looking for ways to improve efficiency.
“Ashley is a true innovator in every sense of the word,” Ellison said. “The use of this technology at Hanford has the potential to be a game changer for years to come. Congratulations to Ashley and MSA for a job well done.”
Todd Synoground, MSA vice president for public works, also commended Ashley on the award.
“Ashley has that unique characteristic of being a technical expert in her field while also being a strong and dynamic leader,” Synoground said. “Her innovative thinking and uncanny ability to identify creative solutions are second to none.”
Ward leads a team of over 150 IT professionals who develop and maintain a majority of the more than 1,600 computer applications for Hanford, including medical-monitoring applications, geographic information systems, business management systems, and quality assurance applications.
-Contributor: Patrick Conrad
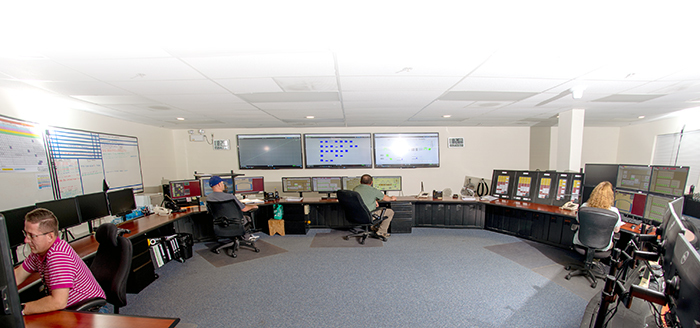 The development of innovative automated systems at the Hanford Site has led to improved operational safety and efficiency as the site prepares for round-the-clock operations to treat tank waste. From a new central location, pictured here, operators can control nuclear waste transfers, monitor ventilation flow, and detect chemical vapors to protect workers from potential exposure.
RICHLAND, Wash. – EM’s Hanford Office of River Protection (ORP) recently completed several upgrades years in the making to support the underground waste tanks’ transformation to new digital automation systems.
These systems focus on worker safety, efficiency, reliability, flexibility, mobility, and cost effectiveness as Hanford prepares to begin treating tank waste by the end of 2023.
“We’re making a better future happen now,” said Mirwaise Aurah, process and control system engineering manager with ORP tank farms contractor Washington River Protection Solutions (WRPS). “Making tank farm information available remotely increases worker safety.”
Workers can view radiological conditions and industrial hygiene information on large displays at tank farm access points and on Hanford computers.
A new central control room has been established with new capabilities, including remote monitoring of ventilation flow and systems to detect and monitor chemical vapors, protecting workers from potential exposure.
A new suite of more than 60 software products has also been deployed to improve the pace and efficiency of operations.
“Development of new and innovative automated solutions has led to improved safety and efficiency,” said Dimple Patel, ORP tank farms instrumentation and control safety system oversight engineer. “As the suite of digital tools grows and improves, it prepares us for a much higher pace of operations to support round-the-clock treatment of tank waste.”
This technology initiative provides two new training simulators that create realistic scenarios, so operators can respond effectively in the field.
“Our goal is to have our operators trained so well that the correct response to an abnormal process condition becomes muscle memory,” said Karthik Subramanian, WRPS chief engineer.
“These full-scope operator training simulators provide a key element to meeting that goal.” Patel added, “With technological capabilities in place to improve worker safety, simplify operations, and provide timely and accurate information at the touch of a button, Hanford tanks technology is upgraded for the next phase of cleanup.”
-Contributor: Denise Mellene
|