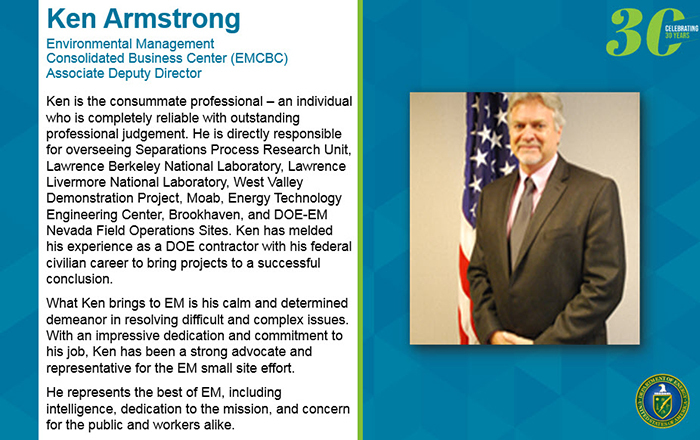 Back to Top
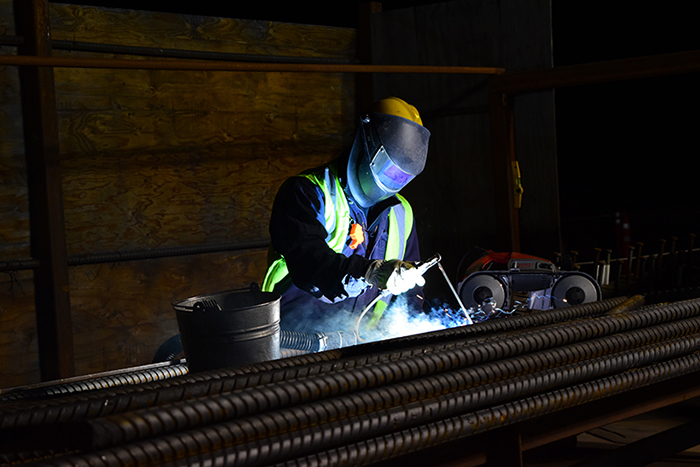 It may be dark outside, but a welder on the night shift at Hanford’s Waste Treatment and Immobilization Plant is creating sparks as he welds rebar.
RICHLAND, Wash. – Even when the sun sets each day on the EM Hanford Waste Treatment and Immobilization Plant (WTP) jobsite, workers continue moving the project forward on its path to treating tank waste.
“We like to fly under the radar as much as possible, be the silent partners,” said Kelly Lofton, night shift superintendent with Bechtel National, Inc., the WTP contractor. “If we can complete a job at night and the day shift comes in and asks, ‘Wait, when did that get done?’ then I consider that a win.”
There are just under 250 employees who work the night shift, about a tenth the size of the day shift workforce. For people working in construction, the night shift starts at 6 p.m. and ends at 4 or 4:30 a.m.
“The night shift expands the project’s work production, helping meet milestones and moves us forward toward completion,” Lofton said. “Even with a small crew, we’re able to complete work the day shift is unable to finish.”
One of the biggest limitations for the day shift workforce is congestion; there are more people and more equipment moving.
“Fewer people working can be a benefit,” said Tracey Hagood, Effluent Management Facility piping superintendent. “During the day, two or three crews would have to stop working if we wanted to move a lift or large piece of equipment. We have more flexibility to move work around and work in areas that are hard to get to when there are more people.”
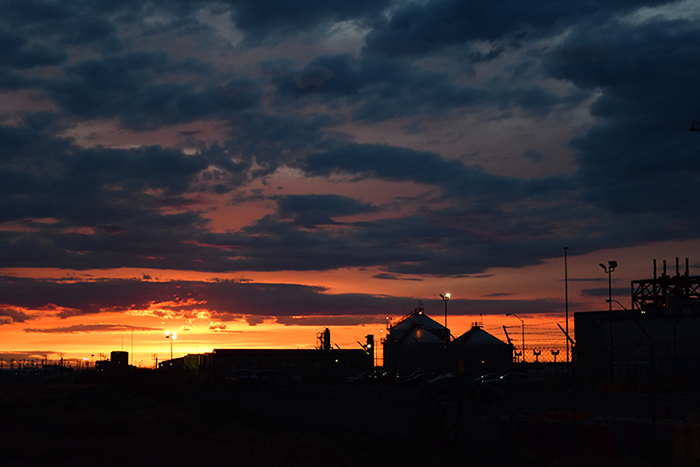 The sun may go down, but work doesn’t stop at Hanford’s Waste Treatment and Immobilization Plant.
A small administrative staff supports the night shift workers, which includes the superintendents, field engineers, startup engineers, a construction technician, health and safety personnel, an administrative assistant, and quality assurance personnel. However, limited access to the staff creates challenges, and careful work planning and coordination is essential.
“Communication is the biggest challenge,” Lofton said. “Our superintendents come in at 4 p.m. to do turnover with the day shift. We have to work with the day shift to make sure that we both have what we need and that we’re supporting each other.”
This includes identifying work scope, answering questions, and ensuring the night shift has the right materials and equipment before work begins, because getting them later can be challenging.
“There are advantages to being on an overnight shift,” said Bobby Campbell, electrical superintendent. “I like the problem-solving aspect of working the night shift. There are fewer resources available to us, so we have to come together to answer questions and work through the issues we encounter.”
It’s not difficult to see why some people enjoy the night shift; the jobsite is relatively quiet compared to the hustle and bustle of the day shift. While there are still the unmistakable sounds of construction, there are fewer people moving about, fewer radios going off, and fewer vehicles moving.
“It’s a different lifestyle,” Lofton said. “Family balance can be difficult because you’re sleeping when everyone else is awake. You have to have the support of your family and you have to watch your vitamin D levels. But it’s quieter and easier to focus on getting the work done.”
It's clear the night shift crew members are instrumental in helping WTP reach its goals, and they are proud of what they do.
“We’re one team,” Hagood said. “We’re all here – whether day shift or night shift – to complete the job while maintaining quality and keeping everyone safe.”
-Contributor: Darcy Richardson
Back to Top
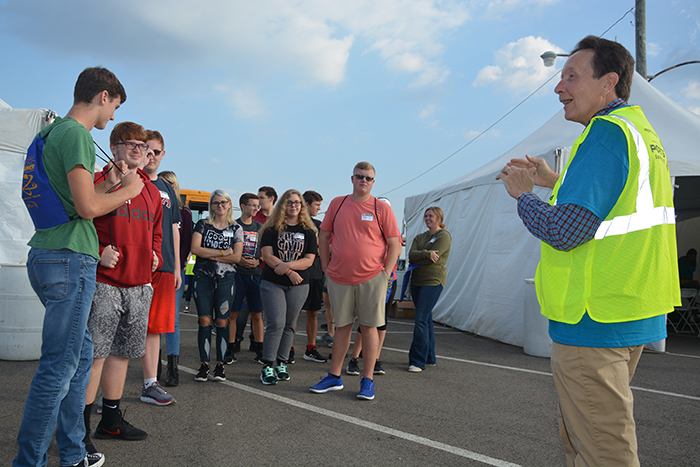 Portsmouth Site Lead Jeff Bettinger welcomes students to the Portsmouth Gaseous Diffusion Plant site for the 10th Science Alliance event.
PIKE COUNTY, Ohio – EM is on the lookout for students like high school junior Brooke Childers, who recently attended the Science Alliance at the Portsmouth Gaseous Diffusion Plant site.
EM’s Science Alliance is an interactive event that showcases a range of science, technology, engineering and mathematics (STEM) subjects and the fields associated with them. The event is part of DOE’s effort to encourage young people to consider fields of science when making career plans.
“I’ve been looking at a lot of different things, including science,” said Childers, who attends Waverly High School in Waverly, Ohio. “This event has broadened some of the subjects I will consider because many of them appeal to me. And it’s really fun.”
EM conducted the 10th version of the event earlier this month and welcomed nearly 1,500 students from 32 southern Ohio high schools. Interactive demonstrations in 15-minute intervals provide the students an array of subjects, and an opportunity to interact with representatives from regional universities and employers.
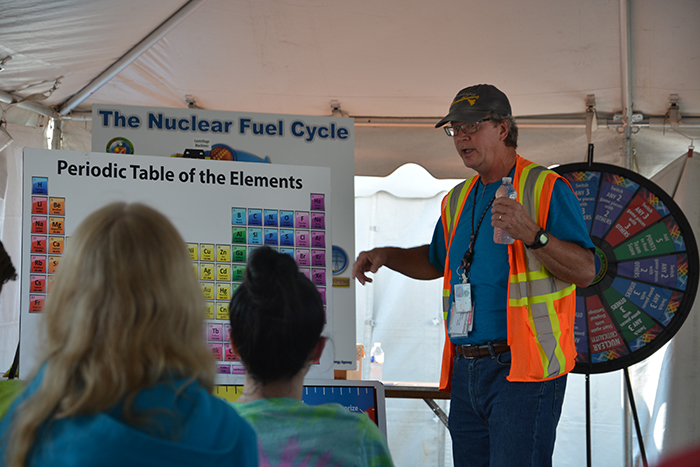 Jud Lilly of EM’s Portsmouth/Paducah Project Office provides an orientation on chemistry and the nuclear fuel cycle at the Science Alliance event.
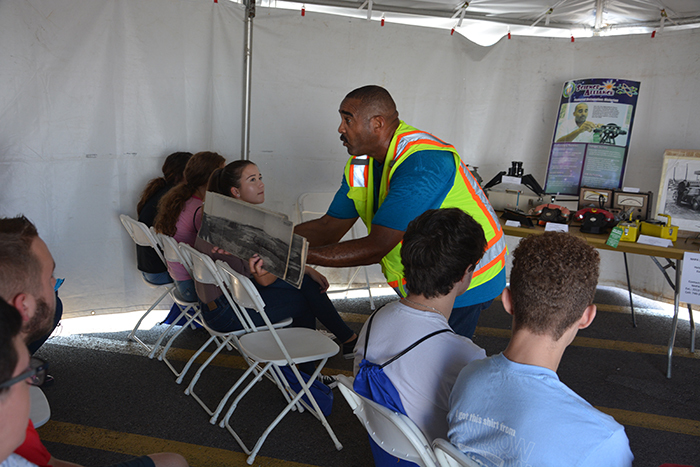 Marc Hill with EM contractor Fluor-BWXT provides a demonstration on historic preservation at the Science Alliance event.
One of the employers is General Electric Aviation, which has its jet engine test operation in nearby Peebles, Ohio. Amy Swango, who organized the company’s display, said interacting with students not only informs them of opportunities, but helps the company address workforce development needs.
“We can draw engineers from anywhere, but not everyone wants to stay here long term, so we think it is important to make young people here aware of what we do and what we offer,” Swango said. “It’s fascinating that many airplanes that fly over us every day have engines that were tested at our plant. That puts a seed in their minds that there are opportunities right here.”
That approach is exactly what motivates teachers like Britnee Inman, a chemistry and biology teacher at nearby Manchester High School. Inman said it is important for young people to recognize the opportunities and STEM careers within their grasp.
“This is good for our students because we are in a low socioeconomic school district. It is advantageous for our students just to see the opportunities that are available, some of the jobs here at the plant site, and the businesses that are in the area,” Inman said. “The students like to see all the information from the colleges. We’ve had several recent graduates go into science fields because they came to this event.”
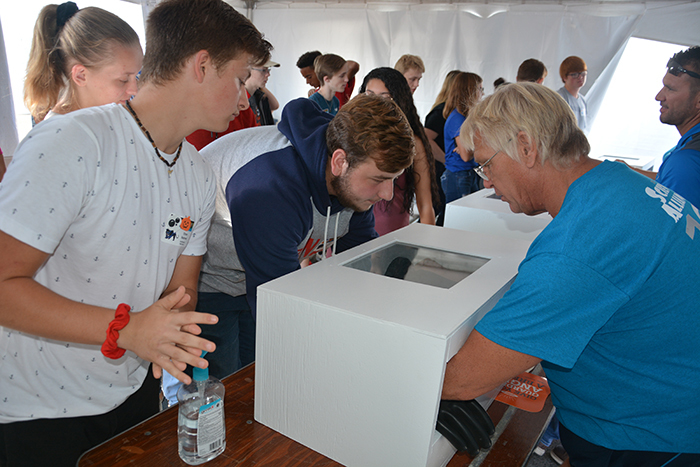 Dan Minter with EM contractor Portsmouth Mission Alliance, right, works with students during a glovebox demonstration at EM’s Science Alliance event.
That marriage of interests and needs was the driver when the event was originally conceived in 2010, said EM Project Coordinator Greg Simonton of the Portsmouth/Paducah Project Office.
“The nation has a need for more kids to get involved in the sciences. Check. Our young people need opportunities. Check. Our regional businesses need to foster an infrastructure of local employees for workforce continuity. Check,” Simonton said. “Science Alliance is not just an everyday science fair. This event changes lives, changes the way we think about STEM education, and addresses bigger challenges that we all face.”
Nick Mowery, a junior at Valley High School in Lucasville, said the event showed him areas of studies with which he was not familiar.
“It was great to talk to the universities and see all their various majors. I really liked the robotics demonstrations shown by Shawnee State University,” he said. “Science Alliance is a really cool thing where students can get information that can help them in their lives.”
-Contributors: Rick Greene, Donnie Locke
Back to Top
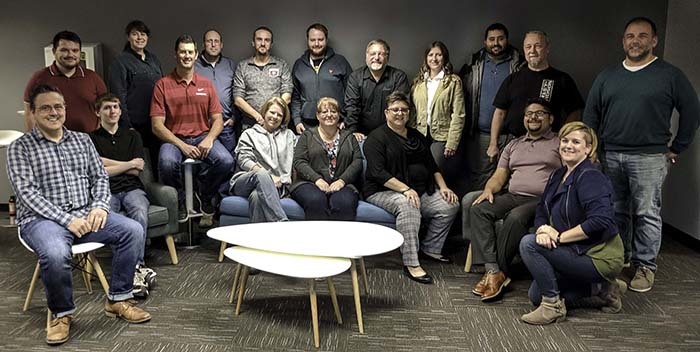 The cybersecurity team with EM Richland Operations Office contractor Mission Support Alliance (MSA) plays an important role in protecting workers and the Hanford Site from potential cyberattacks. MSA has developed a series of strategies and programs to keep up with the fast-paced cyber world, including training exercises for workers, simulated attacks of the network, and round-the-clock network monitoring to identify possible threats.
RICHLAND, Wash. – Working to keep the Hanford Site’s computer network secure, EM Richland Operations Office (RL) contractor Mission Support Alliance (MSA) is combating new and more advanced cyberthreats through training exercises for workers, simulated network attacks, and 24-7 monitoring to identify possible risks.
“Cyberthreats are an ongoing challenge, and we need to stay ahead of those out to do harm,” said Corey Low, director of the RL security, emergency services, and information management division. “MSA continues to do a great job of educating workers and making sure they have the proper training to help identify potential threats and minimize network damage.”
Each month, MSA responds to an average of 45,000 attempted breaches of the Hanford computer network or firewalls. The team also handles more than 200 suspicious email reports, an average of 7 percent of which are potentially malicious and escalated for further evaluation.
This year, MSA acquired a cyber range, a virtual environment used for cyberwarfare training, which allows the team to run simulated attacks on the network to develop and test response procedures. These simulations appear real to end users and can be run safely without affecting the Hanford network.
Additionally, as the site’s industrial control systems, such as water, sewer and electrical services, become electronic and part of the Hanford network, MSA focuses on keeping them safe from potential cyberattacks.
“Computer hackers are coming up with new and innovative ways to breach networks,” said John Roach, MSA’s cybersecurity director. “This is why our team continues to play a proactive role in identifying different ways we can educate ourselves and the workforce about the importance of being safe online.”
-Contributor: Ginger Benecke
Back to Top
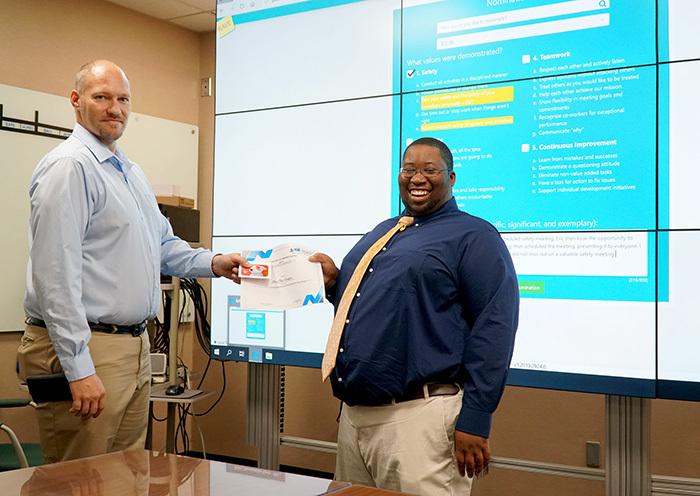 Savannah River Remediation (SRR) Process Applications Engineer Eric Dantzler, right, receives a gift card from his co-worker Jason Hargrave. Dantzler was nominated for the reward through SRR’s new RAVE (Recognizing Achievement of Values and Expectations) application for demonstrating SRR’s core values of safety and ownership.
AIKEN, S.C. – Engineers with EM’s liquid waste contractor at the Savannah River Site (SRS) have developed and implemented new technology to recognize and reward employees promptly for positive behaviors, actions, and attitudes.
Through the innovative application called RAVE (Recognizing Achievement of Values and Expectations), employees with Savannah River Remediation (SRR) can nominate peers who demonstrate specific behaviors and attitudes that reinforce SRR’s values of safety, integrity, continuous improvement, teamwork, and ownership. After a nomination is approved by management, the nominee picks up a gift card as a token of appreciation.
One of SRR’s expectations of teamwork is to recognize co-workers for exceptional performance, and RAVE is a simple and meaningful way to do that, according to SRR Chief Engineer Phil Breidenbach.
“Our RAVE winners don’t just remember the gift card — that is simply a perk,” Breidenbach said. “What makes the most impact is knowing that your co-worker or manager took the time to acknowledge your performance and hard work. That speaks volumes.”
Thanks to the automated system, the mean time from when a nomination is submitted to when the nominee receives the gift card is 41 minutes.
“One of the keys to effective positive reinforcement is timeliness,” Breidenbach said. “Positive reinforcement works best when it is immediate or as close to when the actual behavior occurred as possible. The quick turnaround time for employees to be recognized for their behavior helps make this new program a big success and improves the effectiveness of positive reinforcement.”
Since the app’s launching in June 2019, almost 200 nominations have been awarded through RAVE.
-Contributor: Colleen Hart
Back to Top
|