Take Action Today: Have a conversation with each of your employees individually or schedule an open-ended strategic meeting and ask each of your team members what their thoughts are on their role within the company. Listen and take note of what they say and what they want. Start working on implementing changes immediately, before they move on to a more fulfilling opportunity.
2. Keep a Positive Culture
Employees will go the extra mile if they feel responsible for the results of their work, have a sense of worth in their jobs, believe their jobs make good use of their skills and receive recognition for their contributions. A positive culture means employees feel this way every day and your company should establish a series of values as the basis for culture such as honesty, excellence, attitude, respect and teamwork. A company that creates the right culture will have an advantage when it comes to attracting and keeping good employees
When it comes to employee recognition, BLR, Business and Legal Resources, says employees should be rewarded at a high level to motivate even higher performance. The use of cash payouts could be used for on-the-spot recognition. These rewards have terrific motivational power, especially when given as soon as possible after the achievement. It’s important for employers to say “thank you” to employees for their efforts and find different ways to recognize them.
Take Action Today: Identify at least one employee who is going above and beyond and recognize them for their hard work and dedication or buy lunch for your entire crew on an especially long work day. This can go a long way towards making employees feel valued.
Read more at ForConstructionPros.com
The 64th semi-annual Street Maintenance and Collections Systems school was held in March and brought 192 public workers from across the state together for three and a half days of career development.
The twice-yearly event is sponsored by the American Public Works Association (APWA) Oregon chapter with support from the Oregon T2 Center. This Spring’s school was held at the Valley River Inn and kicked off with a keynote presentation by Shelly Campbell on Trauma Nurses Talk Tough. Her talk outlined the consequences of distracted driving, seatbelt safety, driving under the influence, how items in a vehicle become projectiles in a crash, and how fragile our bodies are.
The school offered 49 different courses for participants to choose from, covering topics ranging from safety training to workplace conflict. Most sessions focused on technical topics for both road maintenance and collections systems workers, including three Roads Scholar classes. Included in this school was three different equipment trainings and two certification classes.
This school also hosted the second annual APWA Equipment ROADeo. 26 individuals competed in the ROADeo which included Backhoe, Excavator, and Skidsteer events. The top competitors from each event received recognition and a prize. The top two overall competitors received a belt buckle and a chance to compete at the national APWA ROADeo in Seattle, WA.
Backhoe Top Three Competitors
- Justin Kivett, Washington Co.
- Derek Johnson, City of Tigard
- Kris Leonard, City of Eugene
Excavator Top Three Competitors
- Derek Johnson, City of Tigard
- Justin Kivett, Washington Co.
- Robert Skinner, Clackamas Co. WES
Skidsteer Top Three Competitors
- Denis Kenny, City of Medford
- Justin Kivett, Washington Co.
- Kameron Frey, City of Medford
Top Three Overall Competitors
- Justin Kivett, Washington Co.
- Derek Johnson, City of Tigard
- Kris Leonard, City of Eugene
The next school will be held October 29-31 in Newport. Registration will begin in August.
|
A team of bridge maintenance practitioners from ODOT and OACES have prepared a two-day course titled, “Oregon Highway Bridge Maintenance Training”. The first in-person training took place in March with approximately 150 participants. The in-person instruction and web-based self-guided instruction is geared toward the needs of Local Agency and DOT bridge maintenance workers and engineers. Course participants will find coverage of specific areas of concern about their bridges with detailed presentations of specific techniques, as well as an overview of maintenance issues throughout the two-day Course. In-person training courses containing hands-on demonstrations of repair techniques are planned to be offered in March of odd-numbered years. The next course is scheduled for March 2021. Contact Holly Winston at ODOT for more information.
Topics include:
- Historical Perspective on Bridge Preservation
- Bridge Components and Elements
- Safety
- Concrete Patching
- Bridge Hits
- Specialty Bridge Maintenance Equipment
- Inspection and Load Rating Report Review
- When do you need an Engineered Design
- Deck Joints
- Bearing Maintenance and Replacement
- Environmental Issues for Maintenance
- Drift
- Scour
- Temporary Bridges
- Steel Repairs
- Deck Sealing and Thin Overlays
- Asphalt Wearing Surfacing and Membranes
- Timber Preventive Maintenance
- Timber Deck Replacement
- Timber Cap and Pile Repair
- FRP Strengthening
2019 presentations, handouts, and video files are posted at https://www.oregon.gov/ODOT/Programs/T2/Pages/OtherTraining.aspx.
|
During the last half of 2018, an additional 15 participants completed the Level 1 Roads Scholar program requirements and an additional three participants completed the Level 2 Roads Scholar program requirements. Those Successful individuals are:
Level 1
- Brant Holaday (City of Beaverton)
- Will Isley (Josephine County)
- Brandon Kalena (Josephine County)
- Ricardo Anselmo (City of Woodburn)
- Jeremy Turin (City of Gresham)
- Ed Allen (Curry County)
- William Allan Avery (Curry County)
- Gary Carter (Curry County)
- Charles Gage (Curry County)
- Scott Eaton (City of Salem)
- Phillip Reeser (City of Salem)
- John Cheatim (Jackson County)
- Tyrone Raber (Jackson County)
- Pat Jackson (City of Tualatin)
- Phillip Peterson (City of Harrisburg)
Level 2
- Melinda Olinger (City of Hubbard)
- Brian Parrett (City of Hillsboro)
- David Senz (City of Hillsboro)
If you are one of these individuals, your certificate was mailed to your supervisor in April.
With the addition of these recent graduates, 604 participants have completed the Level 1 program and 43 have completed the Level 2 program to date. Our congratulations go out to these individuals on their accomplishment! We also extend our appreciation to the agencies of Oregon for participation in and support of the Roads Scholar program.
Roads Scholar Spring Classes
RS-7, RS-8, RS-9 and RS-10
- May 28-29 in John Day
- May 30-31 in Redmond
- June 11-12 in White City
RS-18
To register for any of these classes, use the registration form or email us.
We plan to hold more RS-7, 8, 9, and 10 classes in the fall as well as RS-17. As always, Roads Scholar classes are posted on our training calendar as they are scheduled.
|
The ODOT Library has recently updated its collection to include study materials for the Fundamentals of Surveying exam, including the following:
From PPI:
- Fundamentals of surveying practice exam (2017)
- Surveyor reference manual (2015)
- Surveying solved problems for the FS and PS exams (2015)
From NCEES
- Fundamentals of surveying practice exam (NCEES, 2017)
These materials are available on a first-come, first-served basis with priority given to ODOT employees. The library can ship to offices outside of the Salem area, and check-out periods are up to two months. The library also carries study materials for FE and PE Civil Engineering exams, and PE Electrical and Power exams.
For more information, contact:
Laura Wilt, Librarian
Laura.e.wilt@odot.state.or.us
503-986-3280
|
ODOT is sponsoring National Highway Institute’s Strut-and-Tie Modeling (STM) for Concrete Structures on July 30th through 31st. Location for the training is Salem, Oregon.
STM provides engineers with a simplistic analysis and design tool for deep concrete bridge elements and disturbed regions that would otherwise require a rigorous refined analysis. STM has long been established as a reasonable analysis tool for disturbed regions and deep beams. However, this modeling tool has had difficulty being integrated into our bridge design state-of-practice, which has resulted in inappropriate use of the simplistic elastic beam theory design for deep beams and disturbed regions. In some cases, it has resulted in poor in-service performance. This training course serves as a significant step in providing the knowledge transfer necessary for STM to be used more frequently and more effectively.
For more information about the training and to register, click on the following link:
https://www.oregon.gov/ODOT/Business/Training/EGN01158_073019-073019_Strut-and-Tie.pdf
Did you know T2 has a lending library of videos?
As one of the many services we offer to local agencies and tribal governments, the video library has been around for many years. Given ever-changing technology, we are constantly making updates to how we do the video library.
We now have a searchable list of over 400 videos on our website and over 200 of the titles are available for online viewing! We are regularly adding to our library so keep checking back to see what is new. Check it out at https://www.oregon.gov/ODOT/Programs/T2/Pages/VideoLibrary.aspx.
We have also recently published the 2019 video catalog, which, for the first time includes videos that are available to watch online. To request your copy of the 2019 Video Library Catalog, contact the T2 Center at (503) 986-2855 or by email.
New Videos Just Added to the Library
The following videos are available to loan from the T2 Center. Up to two videos may be borrowed at a time for a two week period. Your only cost is return postage. To request your copies, call us at (503) 986-2855 or by email.
Construction Safety: Front End Loader Safety
This Front-End Loader Safety program will concentrate on the basic safe operations for the standard front-end loader. As an operator, you are a skilled professional who is responsible for an expensive piece of equipment, as well as the safety of those around you. Topics covered are Rollover Protection Structures (ROPS), Potential Problems, Hitching a Load, Rollover Prevention, Falls and Run-over Accidents, Articulated Four-Wheel Drive Loaders, Power Take Off (PTO), Basic Loader Safety Rules, Maintenance, Operating the Front-End Loader, and Travel and Trailering. 15 minutes.
Bucket Truck Safety
Bucket trucks are also known as aerial lift trucks. This equipment is used in every industry and comes with risks and hazards. Bucket trucks are used to elevate personnel to tasks above the ground. Serious injuries and deaths have occurred in construction, mining, tree trimming, public works and fire fighting. The program focuses on safe operation of the bucket truck including Training, Electrical Hazards, General Safety, Equipment Maintenance, and Emergency Response. 14 minutes.
Dump Truck Safety
Dump trucks can carry and dump material, tow equipment and trailers, spread salt and sand on icy roads and apply asphalt on roads. There are a variety of makes and models of trucks; therefore it is important to review the truck’s safety and maintenance requirements as outlined in the operator’s manual. This program discusses maintenance and operation of typical dump trucks with emphasis on safety. Topics covered are Maintenance, Inside the Cab, Operation, Load and Unload, and Driving Conditions. 11 minutes.
Trenching & Shoring Review
Evacuations and trench cave-ins account for a growing number of fatalities and serious injuries in construction. With little or no warning, an unsupported improperly shored or sloped trench or excavation wall can collapse and trap the workers below in seconds. This program is an overview of excavation and trench safety basics.
Topics discussed in this safety video include: planning for safety, locating any underground installations, contacting the utility companies involved and informing them of the proposed work, terminology and on-site safety practices, types of soil, trench boxes, shoring, testing and control requirements, testing atmospheres in the excavations, and daily inspections of excavations. 30 minutes.
Lockout-Tagout (Vehicle Procedures)
Lockout/Tagout program includes the adoption and utilization of written procedures for turning off and disabling machines and equipment whenever maintenance or servicing is performed on machines and equipment. The control of hazardous energy sources commonly known as Lockout/Tagout covers the use and maintenance of machines and equipment, in which the unexpected energy or startup of the machines or equipment or release of stored energy could cause injury to employees. Lockout requires that energy sources for equipment be turned off or disconnected and that the switch or energy source be locked. Topics covered are OSHA Standards, Identifying Energy Sources, Isolating Energy Sources, Lockout/Tagout Devices, Testing for Potential Energy Sources, and Outside Contractors. 16 minutes.
How To Comply With The New GHS Hazcom Program
The Global Harmonized System (GHS) is an International approach to hazard communication. It is based on major existing systems around the world, including OSHA's Hazard Communication Standard and the chemical classification and labeling systems of other US agencies. This program explains how to comply without changing the entire HAZCOM program. 15 minutes.
Skid Steer Safety
Skid steer equipment has become the number one workhorses for public works and construction. With trenchers, plows, grapples, buckets and hoes and hydraulic breakers as attachments, their versatility is limitless. This equipment can stop on a dime, spin in circles, climb, dig and a variety of other tasks. As interesting as they are to operate, there are potential risks to the operator and those working around them. The primary reason for injuries lies with untrained workers. Operators must be trained and qualified to operate the skid steer. 16 minutes.
|
Portable Ladder Safety
by Sue Raynor
Most of us at one time or another have chosen to grab a chair versus a ladder to grab items just out of reach, but were we taking chances?
According to the Bureau of Labor and Statistics in 2016 there were 697 fatalities from falling off a ladder and most of these fatalities occurred from falls from a ladder of 6-10 feet. Nationwide over 90,000 people are treated in emergency rooms for ladder related injuries. OSHA Ladder citations were the sixth highest cited offense.
Before selecting a ladder at work and at home ask yourself:
How high do I need to climb or reach?
How much weight the ladder can hold (person and tools)
What is the location of project, inside or outside, uneven ground, near power lines, etc.
Here are some basic rules to keep you safe:
- Read and follow all labels on the ladder
- Always choose the right ladder for the job, Do not use a wooden or aluminum ladder around power lines.
- Always inspect the ladder for cracks and damage. If it is damaged DO NOT USE.
- Always use a ladder that is the right height for the task,
- Always check the weight rating on the ladder
- Place the ladder on level firm even surfaces.
- Only allow one person on the ladder
- Do not place the ladder in front of doors
- Do not move or shift a ladder while standing on it.
- Always maintain a three point contact (two-hands and a foot, or two feet and a hand).
- Never wear slippery shoes
NIOSH (National Institute for Occupational Safety and Health) has a Ladder Safety App that can be downloaded for free. This free app contains Ladder Safety Tools and a ladder Angle Measuring Tool.
Ladder App for Apple
Ladder App for Android
|
FMCSA has released new resources to help CDL drivers, their employers, C/TPAs, MROs, and SAPs prepare for their roles in the forthcoming Commercial Driver’s License Drug and Alcohol Clearinghouse.
Mandated by MAP-21, this online database will contain information on drug and alcohol program violations committed by drivers subject to 49 CFR Part 382. This will ensure that FMCSA enforcement staff, State Driver Licensing Agencies, and State law enforcement personnel, as well as motor carriers and other employers of CDL drivers, have real-time information about these drug and alcohol program violations.
The Clearinghouse will be operational beginning January 6, 2020, with registration opening in fall 2019. Visit https://clearinghouse.fmcsa.dot.gov to learn more and to subscribe to receive email updates about the Clearinghouse from FMCSA, including when registration opens later this year.
Please send any questions to clearinghouse@dot.gov.
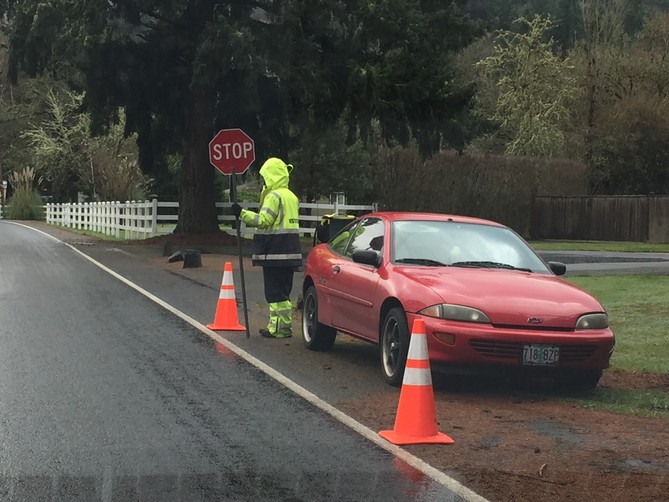 This flagger has made several mistakes which could greatly impact their safety and the safety of their team. The flagger’s vehicle is parked too close to the flagging station. All vehicles, including that of the flagger should be parked at least 100 feet from the flagger. The primary reason is due to what is known as visual-acuity behavior of drivers approaching the work zone. Drivers normally see large objects before they see small ones, therefore an approaching driver may focus their attention on the vehicle first and not see the flagger standing on the road shoulder. Having the vehicle at the flagging station also greatly inhibits the escape route for this flagger.
The flagger is also holding the stop/slow sign support in their left hand. MUTCD and the State of Oregon both direct the flagger to hold the stop/slow paddle in their right hand and direct traffic with their left hand. This is important as holding the stop/slow in the right hand permits the flagger to more readily turn their bodies toward the traffic they control and reduces the risk of being struck from behind. Finally, flaggers must be careful not to obscure their peripheral vision with either the stop/slow paddle or articles of clothing. This flagger while using their coat hood, lessoned their ability to hear and see traffic approaching their station.
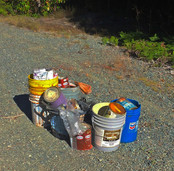 |
|
HAZMAT Awareness Refresher
This training is geared toward public works employees who may come across the scene of a hazardous materials or potential terrorist incident in the course of their work. It is intended to provide refresher training for those who have already taken the Hazardous Materials Awareness course. Awareness level training prepares participants to identify a hazardous materials spill, notify proper authorities, and stay safe until help arrives. The course explains the roles of other response personnel at a hazardous materials or terrorist incident. (1½ hours)
|
Check out the new video about the Safe Routes to School grant funding new sidewalks, crosswalks and more in Coos Bay. ODOT Region 3’s Gary Leaming and ODOT Communications’ Rod Stevens produced the story, which demonstrates the amazing benefits this newly funded program is providing.
|
The following publications are available in PDF format or hardcopies can be ordered from the T2 Center. You may order as many copies as you wish. Available while supplies last. To request your copies, call us at (503) 986-2855 or send an email to T2Center@odot.state.or.us.
Quantifying the Performance of Low Noise Rumble Strips
Shoulder or centerline rumble strips (RS) generate noise and vibration to alert drivers when they are departing the lane of travel. Although inexpensive to install, easy to maintain, and very long-lasting, RS are not installed on many roadway segments primarily due to noise concerns of nearby property owners. This study evaluated the feasibility of using sinusoidal RS as a substitute for rounded milled RS on roadway segments in Oregon with lane-departure crash problems. Exterior and interior sound levels and interior vibrations generated by rounded and sinusoidal RS strikes were compared to baseline and no-strike sound levels for 3 vehicle classes (passenger car, van, and heavy vehicle) to establish sound generation and alerts of the 2 designs. A total of 114 vehicle strikes of RS were recorded. Rumble strip strikes by the passenger car and van generated less exterior noise with the sinusoidal than with the rounded design. Interior noise generated by striking the sinusoidal design generated a clearly noticeable alert, suggesting that the sinusoidal rumble strip is still an effective countermeasure. Based on thresholds of human perception for vibration, both rumble strip types generated sufficient vibration to alert the driver. Results for the heavy vehicle were complicated due to bridging of the harrower rounded rumble strip by the tires. The wider cut of the sinusoidal RS generated a clearly detectable increase in exterior roadside noise for the Heavy Vehicle. Likewise, the sinusoidal design created a noticeable interior alert for the HV but the rounded design did not. Download a PDF of the report.
Rumble Strip Design Evaluation Based on Exterior Noise Using Finite Element Analysis
Using an alternative, physical-based approach for experimentation with rumble strips, twenty new rumble strip patterns were developed and investigated. The specific aim of this research was to identify modeled rumble strip designs that provide maximum safety by capturing driver attention through tactile and audible signals while also maintaining low noise emissions to the surrounding area. Specifically, this study used static state finite element analysis (FEA) to simulate the tire rolling on the rumble strip designs. Both the dBA level and the 1/3 octave analysis frequency spectra were extracted from each design simulation. The results from this modeling analysis together with published field measurements revealed six promising designs for future in-depth modeling and potential field analysis, including three new sinusoidal and three newly developed sawtooth designs. While different variations of the sinusoidal rumble strip design have been tested and implemented by other DOTs, the modeling results from this work suggest that this new sawtooth rumble strip design reduces exterior noise levels even more than published sinusoidal patterns. Download a PDF of the report.
Binder-Grade Bumping and High Binder Content to Improve Performance of RAP-RAS Mixtures
General reduction in pavement program funding levels over the past decade and the possible consequent increase in pavement road roughness within the next couple years created a need for low cost yet effective alternative ways to rehabilitate, preserve and maintain roadway network in Oregon. Recycling highway construction materials and minimizing the use of virgin materials can reduce the pavement life cycle costs, improve highway network condition, conserve natural resources, and protect the environment. Although using recycled asphalt pavements (RAP) and recycled asphalt shingles (RAS) is beneficial in many aspects, asphalt pavements with high RAP and RAS contents are more susceptible to cracking. Aged binder in RAP and RAS makes asphalt pavements more brittle and creates long-term durability problems. Using softer virgin binder grade (binder-grade bumping) and higher virgin binder content improve cracking performance of pavements with high amounts of RAP and RAS. However, careful considerations are required in designing asphalt pavements with high RAP and RAS. Softer virgin binder grade and higher binder content make pavements more resistant to cracking, but more susceptible to permanent deformation. Hence, a balance of the combination of RAP and RAS content, binder content, and binder grade should be considered in the mix design. In this study, the performance and cost benefits of using binder-grade bumping and increased binder content strategies in RAP and RAS mixture production in Oregon are quantified. To be able to provide recommendations for asphalt mixture design procedures, blending of binder around RAP is also quantified by using an innovative procedure developed in this study. Laboratory test results were used to develop mechanistic-empirical (ME) pavement models for asphalt mixtures with different RAP and RAS contents. Using the predicted performance from ME models and cost calculations for different combinations of RAP content, binder content, and binder type, life-cycle cost analysis (LCCA) were conducted to determine the performance and cost benefits of using binder-grade bumping and high binder content in Oregon asphalt mixtures. Binder-grade bumping and high binder content strategies recommended in this study are expected to increase the RAP and RAS content in asphalt mixtures, reduce the life-cycle cost, improve the cracking performance, and encourage the widespread use of high RAP/RAS asphalt mixtures in Oregon. Download a PDF of the Report.
Adjusting Asphalt Mixes for Increased Durability and Implementation of a Performance Tester to Evaluate Fatigue Cracking of Asphalt
Cracking is a common failure mechanism in asphalt concrete pavement structures. It is one of the main reasons for large road maintenance and rehabilitation expenditures, as well as reduced user comfort and increased fuel consumption due to high road roughness. The resistance of the pavement to this distress mechanism is dependent upon the ductility of the asphalt pavement mixture. The use of recycled asphalt materials in asphalt mixtures are also becoming increasingly common. A drawback of this practice is a reduction in ductility of the asphalt mixture, which causes a significant reduction in the fatigue life of the pavement in many cases. In Oregon, asphalt pavements are commonly failing prematurely due to cracking-related distresses, necessitating costly rehabilitation and maintenance at intervals of less than half of the intended design lives in some cases. For this reason, it is necessary to accurately quantify the impact of increasing the recycled asphalt content in asphalt pavement on the structural cracking resistance of the pavement through use of low-cost and efficient testing procedures that can be implemented easily. This study focuses on characterizing the cracking performance of asphalt pavements in Oregon by considering four tests commonly used to evaluate fatigue cracking resistance and proposing implementation of the most cost-effective and efficient test procedure for agencies and contractors. Also, the impact of asphalt mixture properties, such as binder content, air-void content, aggregate gradation, polymer modification, and aging, on cracking performance of asphalt mixtures was investigated. Mechanistic-empirical (ME) design modeling and life-cycle costs analysis were also conducted to determine cost and performance effectiveness of asphalt mixtures with varying properties. Finally, recommended strategies were proposed for Oregon to address the issue of early pavement fatigue failure based on the test results, statistical analysis, ME models, and life cycle cost analysis (LCCA). The goal of this study is to provide a better decision-making structure during the pavement design stage to address fatigue cracking susceptibility, with the intent of avoiding premature pavement failure and expensive early maintenance and rehabilitation. Additionally, the study aims to reliably facilitate an increase in recycled materials content in asphalt pavement through advanced testing procedures and design recommendations proposed in this study. These recommendations will reduce the life cycle cost of pavements in Oregon, reduce network-level pavement roughness and increase the sustainability of the paving industry. Download a PDF of the report.
Effects of High Strength Steel Bars and Steel Casing on the Response of Drilled Shafts
The amount of steel reinforcement in drilled shaft foundations has increased over the past several decades to account for anticipated seismic hazards. Increased reinforcement may lead to a higher frequency of anomalies within shafts due to the increased difficulty for concrete to flow through reduced clearance between the reinforcement. High-strength steel reinforcement and permanent steel casing may be used to mitigate this concern. However, use of a lower steel area my serve to reduce flexural stiffness, and depending on the method of construction, steel casing may result in reduced axial load transfer to the surrounding soil. Thus, existing analytical approaches need to be evaluated for modern construction methods, and new approaches developed if necessary to ensure desired performance criteria are met. Four full-scale instrumented test shafts with various composite cross-sections were constructed to investigate load transfer under axial and lateral loads and the effect of high strength steel reinforcement and steel casing. Empirical, region-specific axial and lateral load transfer models were proposed for use with drilled shafts constructed in the Willamette Valley. The effects of permanent casing on axial load transfer were determined, and synthesized with existing observations to provide an up-to-date reference on the reductions expected based on construction sequencing and installation methods. The lateral responses of the test drilled shaft foundations indicated that the high-strength reinforcement could be used without detriment to the lateral performance; and that the shafts with permanent steel casing responded in a more resilient manner than uncased shafts at the same nominal diameter due to their significantly greater flexural rigidity. Download a PDF of the report.
Use of Additional Lighting for Traffic Control and Speed Reduction in Work Zones
Performing roadway construction work at night exposes workers to hazards that are not present or as great during the daytime. Working at night requires illuminating the area where work is taking place in order to provide sufficient lighting for the workers to see their work and to illuminate the workers. Work area lighting may also have a positive impact on the speed of passing vehicles. Based on previous studies (e.g., SPR 751 and 769) vehicle speed reduction in the work zone during nighttime operations is assumed to be due in part to the lighting provided to conduct the work. The present study evaluated the impact of temporary work zone lighting on vehicle speeds. The study includes case studies on multi-lane preservation projects in Oregon in which different types of lighting systems were implemented: a light tower, balloon light, and a personal, wearable light. The research findings indicate that additional temporary roadway lighting helps to make workers more visible to motorists and equipment operators, and leads to slightly higher vehicle speeds. Implementation of additional temporary roadway lighting is recommended where the work operations contain concerns regarding visibility. Personal, wearable lights are also recommended for workers who are located away from large equipment and other light sources. Download a PDF of the report.
Eyes in the Sky: Bridge Inspections with Unmanned Aerial Vehicles
Interest in the use of unmanned aircraft systems (UAS) in bridge inspection is rapidly growing within State transportation agencies, due to potential cost and time savings, as well as safety benefits. In particular, UAS may provide the capability to reduce use of bucket trucks, climbing, and lane closures in some inspections, by enabling high-resolution video and still imagery of bridge elements to be acquired from multiple viewing angles using onboard cameras. Additionally, imagery acquired with the UAS can be post-processed and further analyzed back in the office, facilitating detailed analysis and a possible shift of some tasks from the field to the office. However, in evaluating the use of UAS in bridge inspection, it is critical to understand both the capabilities and limitations of UAS, the aspects of an inspection that UAS can and cannot be used to satisfy, the regulatory aspects of UAS use, and the recommended operational procedures and workflows. Additionally, to assist ODOT and other transportation agencies in deciding whether to implement UAS-based inspection programs and procedures, cost-benefit information is needed. This research project focused on addressing these needs. Because required inspections of communication towers pose similar safety and logistical concerns, this project also investigated the potential use of UAS in ODOT’s tower inspection program. Following a literature review and a detailed analysis of UAS components and advantageous characteristic for structural inspections, six bridge inspections and three tower inspections were conducted. The results were used to compile recommended safety and operational procedures and to assess, item-by-item, the required reporting elements of an FHWA inspection report that can or cannot be aided by use of UAS. Finally, the project findings were used in conjunction with data provided by ODOT to perform a cost-benefit analysis for use of UAS in bridge inspection. The analysis yielded an estimated average cost savings of approximately $10,000 per bridge inspection and showed a benefit-cost ratio of 9 if a UAS bridge inspection program is implemented. Download a PDF of the report.
Compliance and Surrogate Safety Measures for Uncontrolled Crosswalk Crossings in Oregon
This research aims to find readily observable and measurable field measures and geometric data to evaluate relative crosswalk safety performance. A literature review was conducted and crash data analysis was undertaken to determine the significant predictors for pedestrian crashes at unsignalized marked crosswalks. These factors were used to select nine sites for data collection. Video and radar equipment were used to collect pedestrian and traffic information at each of the sites. Both qualitative and quantitative analyses conducted at each site provided important insights into driver and pedestrian behavior. Ultimately, normalized entering volume (NEV) and no-stop percentage (NSP) are recommended as macro-level surrogate metrics that could be used to analyze pedestrian safety at unsignalized marked crosswalks. They are strongly associated with pedestrian-vehicle conflicts and are based on readily observable and measurable field measures and geometric data. Download a PDF of the report.
Construction of Efficient Cost-Effective & Sustainable Maintenance Facilities
The Oregon Department of Transportation (ODOT) manages about 89 maintenance stations. Many of these are reaching or beyond their life expectancy, inefficient, or functionally obsolete (e.g., unable to accommodate large modern equipment). There is an urgent need to systematically replace these buildings to support the maintenance mission of the agency. By reviewing literature, green building standards and rating systems, and other DOT regulations, and by conducting two case studies as part of an ODOT research project (SPR 792), best practices were identified to be considered when constructing new or renovating existing stations. First, optimizing building energy performance appears to be the single most important action that can result in cost savings and reduce its negative environmental impacts. To optimize energy use, it is important to perform initial commissioning of building systems ensuring that the HVAC and electrical systems (including sensors) are operating per manufacturer recommended specifications. Then, using building energy simulation tools is recommended to optimize energy performance and to identify areas where energy can be saved, or where waste energy can be harvested. Next, it was found making improvements in sustainability metrics for materials used in the greatest quantity on a mass (or volume) basis can result in significant improvements in overall sustainability performance. Also, prioritizing the use of regional materials for the most used building materials, especially those of greatest density (e.g., concrete), can significantly reduce environmental impacts of associated transportation, as well as stimulating the local/regional economy. Finally, focusing on materials that provide synergistic benefits in energy savings was found to be important for improving the overall sustainability performance of buildings. . Download a PDF of the report.
The following free publications are available from the T2 Center. You may order as many copies as you wish. Available while supplies last. To request your copies, call us at (503) 986-2855 or email us.
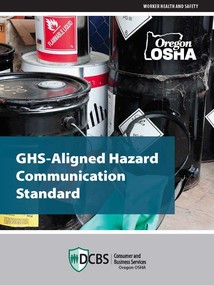 |
|
Oregon OSHA's GHS-Aligned Hazard Communication Standard
The essence of hazard communication is knowledge and understanding. We use thousands of chemical products throughout our lives, at home and at work, but most of us would not be able to distinguish safe products from hazardous ones without information and training.
OSHA’s Hazard Communication Standard (HCS) requires employers to train their employees to recognize chemical hazards – using the information provided on product labels and in safety data sheets – and to take the necessary precautions to protect themselves.
This guide introduces the concept of hazard communication as it aligns with the Globally Harmonized System of classification and labeling chemicals. This guide helps employers develop a hazard communication program and provides an overview of OR-OSHA's hazard communication rules.
|
It’s not just dust! What you should know about crystalline silica, silicosis, and Oregon OSHA silica rules.
Crystalline silica is the scientific name for a group of minerals containing silicon and oxygen. Crystalline means that the oxygen and silicon atoms are arranged in a specific pattern. Crystalline silica is a common mineral found in naturally-occurring and man-made materials such as sand, stone, and engineered stone countertops.
This guide tells you about the hazards of crystalline silica and teaches you about silicosis, what causes it, and how to prevent it.
|
|
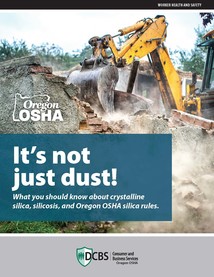 |
|