After some design work, a lot of math to calculate flow and pressure rates, and a bit of trial and error, Winburn achieved the goal of creating an efficient, simple, low-cost truck wash system that can be adjusted to accommodate a variety of needs. With the flip of a valve, crew members can set the system to spray only the top, only the sides and bottom, or the entire vehicle. Another valve adds the corrosion inhibiting wash solution.
“It took some time, planning and math,” Winburn said. “I like math, so I enjoyed it. It was a lot of fun putting it together.” The controls that turn the system on and off are genius in their simplicity. The main valve is mounted on the wall with a two-foot-long handle attached. Long cables attached to the end of the handle run to the entrance and exit doors of the wash bay. A quick pull on the cable at the entrance opens the valve and turns on the water pressure. After driving the vehicle through the oversized shower system, the driver simply pulls the cable near the exit door to turn it off. Crewmembers stay high and dry while the truck gets a quick and thorough cleaning. A process that used to take five or ten minutes and expose drivers to cold, wet mist now takes less than two minutes.
“Every minute saved going through the truck wash is that many more minutes the truck gets to stay on the road, doing what its primary function is, keeping the roads safe,” Winburn said.
Making it even better
Because the initial goal was to keep the system low cost and get it up and running quickly, Winburn knew there would be opportunities to make it more efficient, after it was proven to perform.
“I achieved all the goals of the project and am now looking at ways to improve it,” Winburn said.
Potential enhancements include increasing the water pressure with a booster pump, investigating better nozzles that would produce a more even spray pattern, and automating how the system is turned on and off.
“If I was going to improve the on/off from the mechanical cable system, I would probably put a photo eye on the inside that would run for a certain amount of time, so you could trip it, drive through, then it would shut itself off,” Winburn said.
Using automatic garage door-type openers that would activate the system is another option he may investigate.
“One thing at a time,” Winburn said.
To help spread the word of La Grande’s new truck wash system with other maintenance crews, and to hear more suggestions for improvement, a video highlighting Winburn’s creation is being shared with others.
Reprinted with permission from March 2018 edition of InsideODOT.
Do you have an idea that has helped make your job easier?
Share it with T2 at T2Center@odot.state.or.us.
The Interactive
Highway Safety Design Model (IHSDM), a suite of software analysis
tools that support data-driven
safety analysis (DDSA), helps transportation agencies evaluate the
safety and operational effects of geometric design decisions on highways.
IHSDM includes six evaluation modules that provide quantitative
information on the expected safety and operational performance of a highway
design: Crash Prediction, Policy Review, Design Consistency, Traffic Analysis,
Intersection Review, and Driver Vehicle. The latest version
of IHSDM—released in March—expands data entry and reporting options to include
mileposts. It also expands the scope of a tool that allows users to conduct
economic analyses using Crash Prediction Module evaluation results on crash
frequencies and severities.
Use of IHSDM is gaining momentum among transportation agencies
as a way to validate design decisions and potentially save time during the
design process. Before proceeding with a project to remove a 2-mile bottleneck
on I-225, the Colorado Department of Transportation (CDOT) wanted to know how
the project would affect safety on the I-225 and downstream I-25 corridors. To
answer the question, CDOT worked with the Every Day Counts DDSA team to analyze
a combination of alternatives and effects using the IHSDM Crash Prediction
Module. The results of the analysis showed no significant adverse impact on
safety.
Download
IHSDM software free of charge. For information on IHSDM, contact Abdul Zineddin
of the Federal Highway Administration Office of Safety Research and
Development.
For information on using IHSDM for DDSA, contact Jerry Roche of
the FHWA Office of Safety or John McFadden of the FHWA Resource Center.
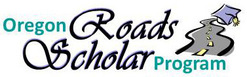 During the first half of 2018, an
additional 22 participants completed the Level 1 Roads Scholar program
requirements and an additional four participants completed the Level 2 Roads
Scholar program requirements. Those
Successful individuals are:
Level 1
- Kasey Olsen (Benton County)
- Bruce Brown (Clackamas County
- Blake Richardson (City of
Redmond)
- Mark Hamlin Brindle (City of
Central Point)
- Erick Johnson (Multnomah County)
- David Mills (City of The Dalles)
- Jay Dennis (City of Bend)
- Scott Pierce (City of Milwaukie)
- Travis Spooner (City of
Milwaukie)
- Dustin Howell (City of Philomath)
- Brett Marshall (City of Talent)
- Kent Alexander (Wasco County)
- Wesley Anderson (Wasco County)
- Mark Justin Bales (Wasco County)
- Ryan Delco (Wasco County)
- Charles Evans (Wasco County)
- Jeff McCall (Wasco County)
- Mac Proffitt (Wasco County)
- Greg Showalter (Wasco County)
- Joey Springs (Wasco County)
- Doug Hamby (City of Eugene)
- Chad Dlouhy (Sunriver Owners
Association)
Level 2
- Thomas Sagers (ODOT)
- Matthew Mosier (City of
Hillsboro)
- Laryn Macauley (City of
Springfield)
- Garry Black (City of Philomath)
If you are one of these
individuals, your certificate was mailed to your supervisor mid-July.
With the addition of these recent
graduates, 589 participants have completed the Level 1 program and 40 have
completed the Level 2 program to date.
Our congratulations go out to these individuals on their
accomplishment! We also extend our
appreciation to the agencies of Oregon for participation in and support of the
Roads Scholar program.
We will soon be scheduling RS-3,
RS-4, RS-5, and RS-6 classes on the West side of the state as well as RS-14 in
various locations across the state. If
you are interested in hosting, please contact us at (503) 986-2855 or T2Center@odot.state.or.us.
As always, Roads Scholar classes
are posted on our training
calendar as they are scheduled.
|
 T2 Center Director
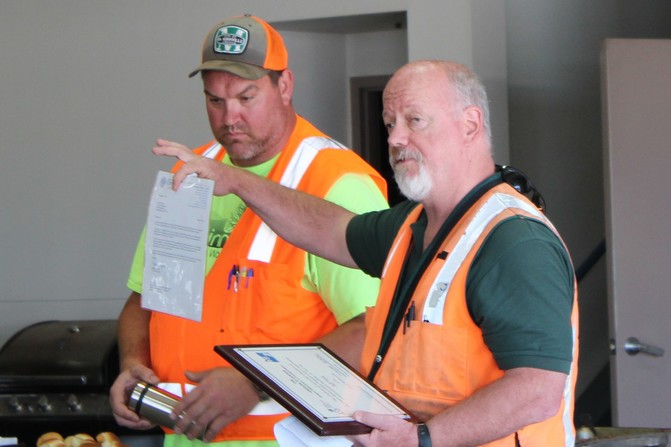 City of
McMinnville Public Works Superintendent, David Renshaw, presenting Streets
Maintenance Utility II worker, Jeff York, his Road Scholar certificate.
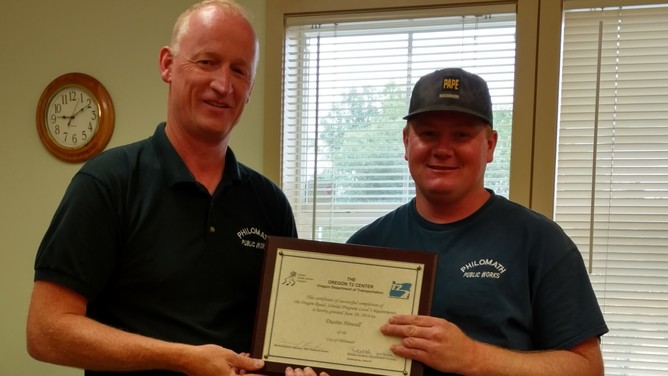 City of Philomath Operations Supervisor, Garry Black presenting Dustin Howell his Level 1 certificate.
Now from FHWA, you can e-Subscribe for MUTCD-related updates!
We’ll send you a notification whenever there’s something new posted to the
MUTCD’s What’s New page. Staying connected is now easier than ever!
1.
Just go to the MUTCD
website.
2.
Look for the
eSubscribe envelope near the upper left corner.
3.
Enter the e-mail
address at which you would like to receive notifications.
4.
Enter your
preferences.
That’s it—you’re signed up! You can change your preferences or
unsubscribe at any time. And be sure to tell a friend or colleague!
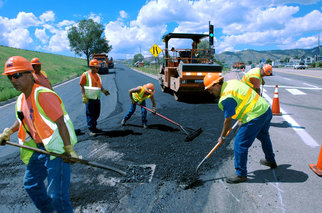 Staying Safe In Extreme Heat
During the intense heat of the summer, it’s hard to stay
cool when working outside. That’s why it is tempting for employees to skip
wearing their personal protective equipment on the hottest days of the year.
Vests, Gloves and other PPE can quickly make workers feel hot and sweaty,
Safety glasses may fog up and impede vision, and hard hats can make the head
feel uncomfortable and sticky in extreme temperatures.
If employees are removing their PPE for even brief
intervals, they are putting themselves at risk. Supervisors and other
co-workers may not be saying anything about it because you know how miserable
employees are in the heat. Here are some
ways to mitigate heat for workers while keeping them safe.
During the summer, your workers
will overheat quickly. This won’t be helped by the addition of thick leather
gloves, heavy work boots and other PPE gear. Your crews should be taking frequent
breaks. Supervisors and employees should be keeping a close eye on everyone and
making sure to get out of the heat at predetermined intervals and drink cool
water. Remember that each person’s internal thermostat is different, and some
people may need more frequent breaks than others. “Skin conditions irritated by
heavy fabrics and non-breathable material can become inflamed further by
intense heat.”1 Pay attention to new employees who may not recognize the dangers
of heat and are not accustom to the heat and type of work.
Workers will need
a place where they can remove items such as hard hats, goggles, gloves and ear
plugs to allow their bodies’ temperatures to lower quickly. The location should
be convenient to the jobsite and either be shaded or air-conditioned. In
addition to having plenty of cool water available in the break area, consider
additional options such as personal cooling wraps, damp cloths, cooling towels
and depending on location water misters.
Issue your workers PPE that
provides ventilation. Hard hats with
vents to provide as much air circulation as possible, and ventilated gloves to
offer both circulation and flexibility.
Safety glasses that keep moisture out (anti-fog) or side vented goggles
can also provide relief to employees. Employers should also look into providing
sunscreen, cooling bandanas, sweat bands, neck shades, sweat liners and in extreme
working conditions consider cooling vests for employees can assist in employee
safety.
Employees should also remember to follow these same
practices at home, and employers should encourage employees to follow safe work
practices.
1. from https://www.equipmentworld.com/ppe-is-still-important-in-the-heat/
|
This month, TC3 has expanded its broad curriculum by launching Benchmarking
and Best Practices for State Equipment Fleet Management, Instructor
Preparation, and Intelligent Compaction. These courses offer something a little
different for those in the transportation industry and are all available
at no cost through the end of July!
Benchmarking
and Best Practices for State Equipment Fleet Management
Most agencies defer to a strategic plan when making decisions about resource
allocation and implementing long-term improvements. This course, recommended
for 2.5 PDHs, discusses how to track performance metrics based upon whats
important in an agencys long-term strategy. This course also covers topics such
as developing performance metric targets, measurement techniques, internal and
external benchmarking, performance gaps, limitations of benchmarking, and
benchmarking best practices.
Upon completion of this course, participants will be able to:
- Identify a proper mix of performance measures;
- Develop and report effective performance metrics for
agency, fleet, and shop activity levels;
- Describe the differences between internal and external
benchmarking;
- Identify what an agency should do with benchmarking
data;
- Explain the limitations of benchmarking; and
- Identify best practices.
Instructor
Preparation
Regardless of personality or experience, all instructors can learn how to
best leverage their strengths, engage with their students, and convey
information as clearly and succinctly as possible. This course, recommended for
3 PDHs, provides tools and lessons aimed to help instructors develop and refine
their skills and position them for success. This course specifically focuses on
traditional, classroom-based instruction.
Upon completion of this course, participants will be able to:
- Explain basic methods and approaches that can be used
to conduct effective training;
- Describe strategies for fostering a positive learning
environment for adult learners; and
- List wa ys to develop, practice, and improve instructor
skills.
Intelligent
Compaction
Compaction is one of the final and most essential processes in roadway
construction. This process is needed to reach the desired uniform density,
which in turn ensures long-lasting support, stability, and strength. This
course, recommended for 2 PDHs, aims to teach construction personnel on the benefits,
use, and interpretation of intelligent compaction data. To maximize the
performance of intelligent compaction, several construction personnel need to
be involved in the collection, use, and analysis of the data.
Upon completion of this course, participants will be able to:
- Define intelligent compaction (IC);
- List the reasons to employ IC over
traditional methods;
- Describe the benefits of IC;
- Summarize the process of highway construction
using IC;
- Explain the training and personnel requirements
required for successful IC implementation;
- Describe how IC data analysis is used to
improve the uniformity of compaction;
- Describe the process of analyzing data and IC
software outputs available;
- Describe general IC quality control plan characteristics;
- Describe responsibilities of quality control
personnel during IC construction activities;
- Describe the key inspection checks for IC
field operations; and
- Summarize typical IC acceptance.
The following free publications are available from the T2 Center. You may order as many copies as you wish. Available while supplies last. To request your copies, call us at 503-986-2855 or email us.
NCHRP Synthesis 521: Investment Prioritization Methods for Low-Volume Roads
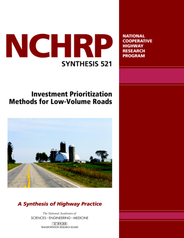 The report documents current practices used by transportation agencies to make investment decisions about LVRs. The intention of the report is to help transportation officials in charge of resource allocation decisions at state departments of transportation (DOTs), as well as at regional and local agencies, respond to the challenge of accounting for broader economic, social, and environmental implications of LVR projects. The report also addresses the challenge that decision makers may face to communicate the value of such investments to stakeholders in an era of limited funds and constantly changing demands on the transportation system. The primary focus of the synthesis is on investment prioritization methods. However, the research also touches on a range of decision-making issues including funding program definition, programmatic resource allocation, and other planning and management activities that directly affect investments made in LVRs.
|
Identification of High Pedestrian Crash Locations
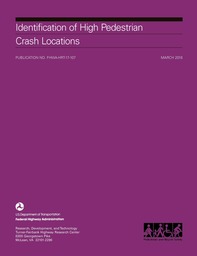 An initial step in reducing the frequency of pedestrian crashes is identifying where they occur or where there is a concern they are likely to occur. As part of a Federal Highway Administration project, the Guidebook on Identification of High Pedestrian Crash Locations was developed to present a process to assist State and local agencies in identifying high pedestrian crash locations such as intersections (points), segments, facilities, and areas.(1) This document summarizes the research efforts to develop the five-step process. Several cities and States were contacted to establish the criteria used to identify and rank high pedestrian crash locations. In all cases, crash data are being used. In some cases, other variables are considered, especially when developing the list of sites for treatments. For example, Los Angeles uses a score that considers the age of the pedestrian and a health and equity index in addition to the number of injury crashes and the number of fatal crashes. Several of the cities create unique lists for intersections, facilities, and areas, recognizing that treatment selection would be different for these element types. The methods used to identify and evaluate sites with a high crash frequency have evolved in recent decades. The availability of geographic coordinates (latitude and longitude) for crashes has resulted in the ubiquitous use of geographic information system platforms for displaying the locations and density of crashes on maps.
|
Bridge Preservation Guide
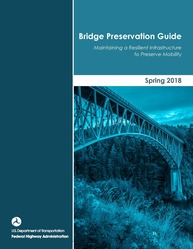 State departments of transportation (DOTs), local agencies, and other bridge owners face significant challenges in addressing the needs of their aging infrastructure. Due to limited funds and increased competition for funds among highway assets, bridge owners are challenged to cost effectively preserve and maintain their bridges to support overall highway mobility. However, having a “worst-first” approach to bridge management by focusing only on replacing poor bridges while ignoring the maintenance needs of good and fair bridges is inefficient and cost-prohibitive in the long term.
A successful bridge program seeks a balanced approach to preservation and rehabilitation/replacement. Bridge owners are striving to be more strategic by adopting and implementing systematic processes for bridge preservation as an integral component of their overall asset management.
This guide defines bridge preservation terms and identifies commonly practiced bridge preservation activities. It also provides guidance to State governments and other bridgeowning agencies on establishing or improving existing bridge preservation programs as part of an asset management program.
|
Safety Evaluation of Centerline Plus Shoulder Rumble Strips
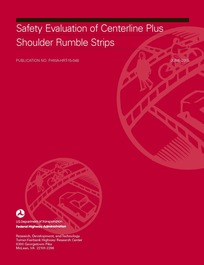 The Federal Highway Administration organized a pooled fund study of 38 States to evaluate low-cost safety strategies as part of its strategic highway safety effort. One of the strategies selected for evaluation was the combined application of centerline and shoulder rumble strips. This strategy is intended to reduce the frequency of crashes by alerting drivers that they are about to leave the travelled lane. Geometric, traffic, and crash data were obtained at treated two-lane rural road locations in Kentucky, Missouri, and Pennsylvania. To account for potential selection bias and regression-to-the-mean, an Empirical Bayes before-after analysis was conducted, using reference groups of untreated two-lane rural roads with similar characteristics to the treated sites. The analysis also controls for changes in traffic volumes over time and time trends in crash counts unrelated to the treatment. The combined results for all States indicate statistically significant crash reductions for all crash types analyzed. The crash type with the smallest crash modification factor (CMF) (i.e., the greatest crash reduction) is head-on, with a CMF of 0.632. Run-off-road and sideswipe-opposite-direction crashes have estimated CMFs of 0.742 and 0.767, respectively. For run-off-road, head-on, and sideswipe-opposite-direction crashes combined (i.e., lane departure crashes), the estimated CMF is 0.733. For all crash types combined, CMFs of 0.800 for all severities and 0.771 for fatal+injury were estimated. Intersection-related and animal crashes were excluded from the evaluation. Benefit-cost ratios were estimated to range from 20.2 to 54.7, depending on the treatment cost and service life assumption, which varied by State. These results are based on conservative service life assumptions.
|
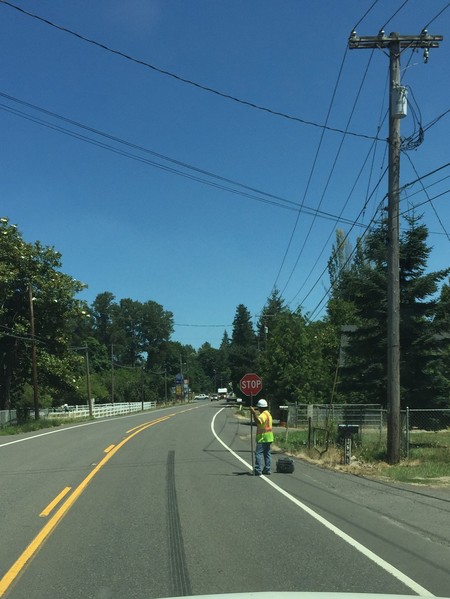 There are several problems with this Flagger’s
position and stance. It is safer for you when flagging to hold the
Stop/Slow in your right hand while performing your flagging duties. If
you hold the support pole in your left hand you must either move it into your
right hand when you signal traffic to proceed, or you must direct traffic with
your right arm which is further from the traffic you control.
Another thing to remember is to NEVER turn your back
to traffic while flagging, even if the traffic approaching your flagging
position appears to be slowing down. It is crucial for your personal
safety to be able to quickly recognize danger if an errant vehicle swerves in
your direction or fails to stop.
Your escape route needs to be at 90 degrees from the flow of
traffic. Therefore, be sure when deciding on your flagging station
location you do not have any obstacles which can hinder your quick escape from
the traffic flow. In this picture the flagger has hindered their escape
with their cooler and there is a mailbox and metal bar blocking their ability
to move quickly off the road.
Remember, You can also place a cone on the shoulder next to
your station to assist oncoming traffic in seeing your flagging station.
Materials
quality, equipment, and construction methods used in pavement
preservation improved significantly in the past 20 years, leading to
longer lasting preservation treatments. Various publications document design
procedures and materials for concrete preventive maintenance, but less
information was available on construction best practices. To address this, the
Missouri Department of Transportation (MoDOT) published a report
consolidating case studies from several States for six concrete pavement
restoration techniques. MoDOT also published a technical brief for each case
study: cross-stitching,
dowel bar
retrofit, diamond grinding,
full depth repair,
partial depth
repair, and slab
stabilization. For information, contact Jason Dietz of the FHWA Resource Center.
|