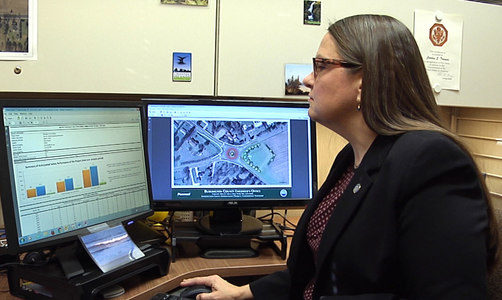 the regional metropolitan planning organization - worked with county agencies and FHWA to develop data-driven road safety assessments.
“We’ve implemented those road safety assessments on a regional basis. That’s been very important,” said Amy St. Peter, the association’s assistant director. “We’re using data out in the field to collect more information with a human factor expert to help us identify what behaviors, what environmental factors, what infrastructure contribute to those crashes and how we can mitigate those.”
The Minnesota Department of Transportation (MnDOT) used DDSA tools to develop road safety plans for each of its 87 counties.
“It was a partnership between the county engineers and MnDOT, as well as the Federal Highway Administration,” said Sue Miller, county engineer for Freeborn County. “We were able to sit down and say, ‘What can we do together to make this data-driven process work for us?’”
The analysis showed that half of fatalities across the State were on local roads, so MnDOT shared funding with the counties to help them implement the plans, based on the data.
“The DOT really understood that if you want to make a true safety difference, then we have to get that money down to the local level to start shifting the culture,” Miller said.
Ultimately, DDSA allows agencies to make safety investments with more confidence.
“We know that we’re saving lives,” said St. Peter. “It could be our friend, our neighbor, our co-worker, but we know that people are here and they’re healthy and they’re safe because of the work we’re doing.”
Learn More
FHWA offers a variety of resources to help the transportation community use data-driven safety analysis (DDSA) to make informed decisions, better target investments, and reduce severe crashes on roads.
See FHWA’s DDSA library for case studies, a DDSA toolbox, webinars, and videos.
Watch a video that explains DDSA approaches and highlights success stories or view an EDC-4 webinar on DDSA.
Contact Jerry Roche of the FHWA Office of Safety or John McFadden of the FHWA Resource Center for information and technical assistance.
Reprinted with permission from FHWA Innovator Issue 60.
|
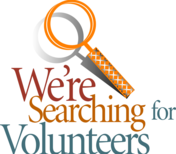 The T2 Center is seeking volunteers from the Oregon community to fill two openings on our steering committee. One vacancy is for a municipal/city representative and one is for a tribal representative.
The Oregon T2 Center steering committee is an important component of the T2 Center’s operations. The steering committee is not a governing board, but rather members provide advice, guidance, and expertise on Local Technical Assistance Program (LTAP) related functions.
Oregon T2 Center steering committee members represent local, state, federal, and tribal agencies that are served by the Oregon T2 Center. The members serve as a link to various stakeholders and are crucial in helping the T2 Center achieve its mission.
Benefits of Steering Committee Membership
There are many benefits to being a steering committee member, including:
- Opportunity to meet and interact with local, state, and federal public works leaders from across Oregon.
- Ability to make suggestions and provide direct feedback regarding the training, technical assistance, and services provided by the Oregon T2 Center.
- Platform for local challenges to be brought and discussed with an experienced and knowledgeable group.
Expectations
- Steering committee members are asked to attend one to two meetings per year in Salem. Meetings typically are no more than two hours in length.
- Members are asked to be open and to honestly communicate their thoughts on issues brought to the committee.
- Members are also asked to be proactive in bringing concerns or areas of need to the attention of T2 staff.
- Members assume the role of advocates for the T2 Center and provide input on ways the needs of both the T2 Center and the communities and agencies served by the program can be met.
- From time to time, steering committee members may be asked for their input by email between meetings.
Criteria
- Must be from a municipality or tribal agency.
- Must be able to commit to a two-year term.
- Must be able to travel to Salem to attend meetings.
- Must have an interest in, and knowledge of, public works topics.
To Apply
If you are interested in applying and meet the criteria above, contact Rebekah Jacobson at Rebekah.a.jacobson@odot.state.or.us or (503) 986-2854.
|
During the first half of 2017,
15 program participants completed their Level 1 Roads Scholar requirements
and 10 program participants completed their Level 2 Roads Scholar
requirements. Those successful individuals are:
Level 1:
Jeffrey Dolgin
(City of Eugene) Robert Compton
(City of Hillsboro) Tom Claussen
(City of Hillsboro) Perry Maupin
(City of Klamath Falls) Hance Woody
(City of Oregon City) Michael
Chaddic (Wasco County) David Troxel
(Wasco County Justin Severance (City of
Prineville) Kala Reyes (City of Redmond) Preston Romanick (City of
Redmond) Keegan Kook (City of Redmond) Manny Ghiselline (City of
Wilsonville) Sean Byrne (City of
Wilsonville) Travis Wootan (Clackamas
County) Mark Shafer (Columbia County)
Level 2:
Mark Olson (City of Beaverton) Travis Williams (City of
Beaverton) Nick Gilbert (City of
Hillsboro) Everett Luff (City of Redmond) Jerry Zimmerman (City of
Redmond) Chris Kochis (City of The
Dalles) David Rubrecht (Josephine
County) Dan Shipley (Josephine County) Keith Blair (Oregon DOT) Patrick Coffeen (Oregon DOT)
Our
congratulations go out to these individuals on their accomplishments, which
demonstrate a significant commitment to self-improvement and personal
development. We also extend our appreciation to the agencies and tribes of Oregon for participation in and support of the Oregon Roads
Scholar program.
With the
addition of these 15 recent graduates, 537 program participants have now
completed the Roads Scholar Level 1 certificate requirements
since the program began in the Fall of 2001.
We will be
offering Roads Scholar Level 1 classes, RS-1 Basics of a Good Road, RS-2 Drainage:Key to Roads that Last, RS-9 Maintenance Math, and RS-10 Introduction to Survey and Grade Checking in
Sweet Home, White City, North Bend, and Oregon City; and the Level 2 class, RS-16
Emergency Preparedness and Response in Redmond, Hillsboro, and Philomath this
Fall. There are still room in most of these classes; see the training calendar for additional
information and registration.
RS-7 Effective
Communication Skills and RS-8 Environmental BMPs 2, will be held at the 2017 Street
Maintenance and Collection Systems Fall School October 24th through 26th in Newport. Additionally, the Level 2
class RS-18 Winter Road Maintenance will be held at the Fall School. Registration is available at http://oregon.apwa.net/EventDetails/12057.
To become a
host for Roads Scholar classes or if you just have questions,
please contact Linda Milligan at the T2 Center by calling (503) 986-2855 or
emailing T2Center@odot.state.or.us.
 T2 Center Director
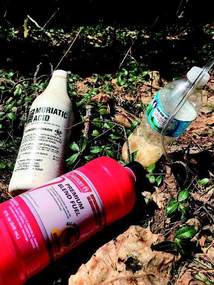 Amy I. Terry Kentucky LTAP, Marketing, Outreach and Publications Manager
Highway workers face many potential dangers on a daily basis when they work on the side of the road. One danger they may not expect to face is exposure to waste from methamphetamine (meth) labs.
Five to six pounds of toxic waste is produced for every pound of meth manufactured. Those running the labs will often dump the waste or lab equipment on the side of the road without regard for the hazards it can cause to people and the environment. It is important that your road crew know what to look for and what to do.
“Our crew ran across some items while cleaning out a drain,” said Ron Allbritten, Street and Solid Waste Manager for the city of Murray. “Our policy is to contact the local police,” he continued. “They handle the items and open an investigation.”
Mark Brasher, County Engineer and Director of Public Works for Daviess County, said they handle it in a similar way. “We haven’t run across it a lot, but when we do we contact the sheriff’s office immediately,” he said. They do not touch it for safety reasons, and also so the sheriff’s department can investigate.
Although it can look like any other trash dumped on the side of the road, waste from meth labs may contain trace amounts of the chemicals used, which are toxic. The fumes can cause itching and burn the eyes, throat, and lungs if inhaled. Physical contact with the chemicals can burn the skin and cause severe respiratory damage.
What to Look For
- Unusual, strong odors like cat urine, ether, ammonia, nail polish remover or similar chemicals
- Pills that look like common cold pills or packaging from cold pills that contain ephedrine or pseudoephedrine
- Containers for antifreeze, lantern fuel, drain cleaner, starter fluid
- Red-stained coffee filters, bed sheets, or pillow cases
Road crews in KDOH District 9 handle things similar to Daviess County and the city of Murray. “In District 9, the road crew calls me and I call the Kentucky State Police,” said Allen Ravenscraft, Safety Coordinator for KDOH District 9. “KSP has a response team that handles the discarded items.”
Should you find items that you suspect come from a meth lab, do not investigate on your own. If your agency does not have a procedure in place on how to handle these types of items, it is best to contact local police or the sheriff’s office and move away from the area. However, it is a good idea to work with local law enforcement before you are faced with this issue to establish a procedure that will keep everyone safe.
If you have come in physical contact with items or inhale the chemicals, seek medical attention immediately. Signs of exposure to meth chemicals include headache, nausea, dizziness, fatigue, shortness of breath, coughing, chest pain, lack of coordination and burns. Until medical personnel can arrive, you should decontaminate yourself and your clothing as soon as possible. Remove contaminated clothing and flush exposed skin, eyes and hair with water for at least 15 minutes. Thoroughly wash your skin with soap and water when possible.
The Kentucky Department for Environmental Protection, Division of Waste Management has set regulated standards for decontamination and for certification of cleanup contractors. To view the tiered response criteria or to see a list of certified contractors, visit them at http://waste.ky.gov/SFB/MethLabCleanup/Pages/default.aspx. They can also be reached at 502-564-6716.
By providing this information to your crew, you have given them the knowledge necessary to stay safe should they face discarded meth equipment.
©2017 University of Kentucky, Technology Transfer Program (T2)
Reprinted with permission from T2, Kentucky Transportation
Center
|
County Road Ball-Banking
Project
by Michael Swan
Over the
course of July and August, and continuing into early September, two interns
hired by the T2 Center have been performing field work and data analysis to provide assistance to 19 of Oregon’s counties in meeting the
requirements of Sections 2C.06 through 2C.15 of the Manual on Uniform Traffic Control Device (MUTCD). These sections require that all roads
functionally classified as collectors or arterials, having an Annualized
Average Daily Traffic greater than 1,000, regardless of jurisdiction, have curve
warning signs brought up to current standards.
Many of Oregon’s counties do not have sufficient staff to perform the
work to determine the signing requirements.
ODOT’s T2 Center successfully applied for a grant through the National
Highway Traffic Safety Administration to perform this work on behalf of those
19 counties.
There are approximately 360 segments of county roads with a total of nearly 1,000 miles
to be analyzed. Each roadway segment
must be driven 3 times in each direction to ensure accurate data. With the travel between segments, and to and
from the office, the interns will have logged ten thousand miles or more by the time the project is completed.
The information is collected using the Curve Advisory Reporting System
by Rieker, Inc. and then the data is analyzed using Rieker software. To date, the interns
have completed over 80 percent of the field work and over 60 percent of the
data analysis. When the project is
complete, the 19 counties will receive a report detailing the MUTCD
requirements, the raw data collected, and the results of the analysis. The counties will then need to evaluate the
results and make decisions regarding the signing upgrades, if required. This endeavor will help provide
uniformity in curve signing and improve safety for Oregon's motorists.
With ever-changing technology, we are working to update the
lending library to be more user friendly.
We now have a searchable and sortable list of videos on our website and
over 200 titles are now available online!
For those that wish to have a paper or PDF of the video catalog, you can
download it to a PDF or hardcopies are still available through T2.
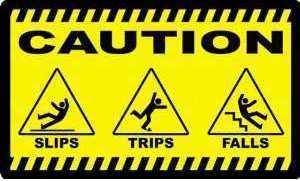 Slips, trips, and falls can happen at any time and
location. They can result in serious
injury, and in the worst case scenario, death. According the National Safety
Council, “falls are the third leading cause of unintentional death in the U.S.,
accounting for nearly 32,000 deaths in 2014.”
Most slips and falls happen from walking on uneven surfaces,
tripping over hazards on the ground, or slipping in inclement weather.
Falls from heights can occur when entering and exiting
equipment; improper ladder usage, and improper or damaged fall protection gear
when working from heights.
So what can be done to avoid falling at work and at home?
- Take extra time, slow down, and pay attention to
where you are walking.
- Keep areas well lit. Maintain parking lots,
pathways, and walkways from broken, slick or raised surfaces.
- If you see a trip hazard, such as an electrical
cord or cable, move it or mark it to warn others.
- Avoid walking while distracted, including reading,
talking, or texting.
- Clean up all spills immediately. Sweep shop
floors that may have debris that has fallen off of equipment.
- Use
ladders correctly by making sure both ladder feet are on firm, even surfaces,
and always use a ladder according to manufacturer’s recommendations.
- During inclement weather, use extreme caution
and wear footwear with good traction.
- Slow down and shorten your stride when walking
in slick, icy conditions. If available, use boot chains or ice grips (ice trekkers).
Another prime location for injury is when you are entering
and exiting equipment. Use three points of contact to reduce your potential for injury, and always face the equipment when entering and exiting rather than
“walking out of the equipment.”
Take the time to slow down and recognize hazards.
|
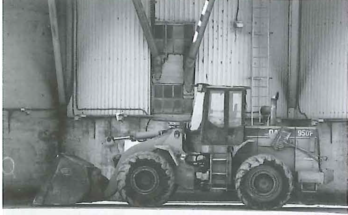 Maintenance garages, equipment yards, and road work zones can be dangerous places. Heavy equipment operates close to workers on foot in areas busy with activity and noise. Unsafe backing maneuvers in these environments can increase the risk of death or injury and cost many thousands of dollars for repair and replacement of damaged equipment.
"Going in reverse is not a natural maneuver because the blind spots, especially on larger vehicles, can be huge," says Ben Rank, a loss control specialist with Cities and Villages Mutual Insurance Company in Wisconsin. "But sometimes there is no alternative but to back a vehicle."
Rank says that street and highway departments can prevent workplace backing accidents by following best practices and raising awareness through good training. He emphasizes three key principles for safe backing and offers additional tips.
Key Backing Principles
- Avoid the need to back up: Operators should park defensively and leave room to pull away going forward when leaving a job site instead of backing. Another option is to use a route or location that accomplishes the task while moving forward.
- Use a trained spotter: If backing up is the only option, use a spotter with good technique and hand signals. Make sure spotters work from the driver's side, stay visible, watch for obstructions, and communicate with the driver. Establish a consistent standard throughout the agency that all operators and spotters understand.
- Get out and look: When it is necessary to back up and there is no spotter around, Rank recommends the simple GOAL (Get Out And Look) technique. Do a complete 360 of the vehicle and the area around it to assess possible blind spots, distances, height clearance, and the presence of any activity or workers that could interfere with a safe backing operation.
Additional Backing Tips
- Position mirrors for clear sight lines before operating the vehicle
- Make sure the backup alarm is working; if it is not or fails during maneuver, use a spotter
- Keep driver's window down to hear and be heard, as well as the passenger window when backing or driving in the vicinity of workers on foot
- Tum off the radio or other distracting devices; give complete attention to the backing operation
- Minimize the number of work activities near moving equipment
- Install signs in work areas that alert employees on foot about the location of moving vehicles
- Don't allow riders in the back during the backing maneuver
- Check for changing conditions in the area if the vehicle is stationary for more than two seconds
- Sound the vehicle horn a designated number of times to signal a backing maneuver to all crew members
- Back slowly, at a walking speed
- Do not back more than 50 to 100 feet before stopping and rechecking the area for a clear zone
- Follow more stringent guidelines in confined areas and for night work
Standard Operating Procedures
Rank recommends that public road agencies incorporate these rules into their standard operating procedures. Training that regularly reinforces safe practices like these also prepares equipment operators, spotters, and all workers to take preventive action.
Technology such as truck-mounted cameras are helping improve safe operation, but Rank cautions against relying on technology alone. Instead, use the above principles and tips to insure a safer, successful backing operation.
Reprinted with permission from the Iowa LTAP "Technology News" July-September 2016 issue, which was adapted with permission from the Summer 2014 issue of Crossroads Newsletter, a newsletter of the Wisconsin Transportation Information Center.
|
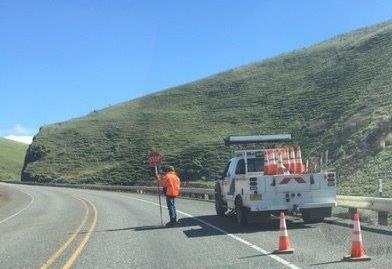 |
Answer to What's Wrong with this Picture
Individual flaggers should always consider their personal
safety as their top priority, while at the same time protecting their coworkers
and the lives and property of all road users, and managing traffic. Usually the safest location for a flagger to
stand is on the road shoulder when stopping the first vehicles. As long as the flagger can be seen on the
shoulder, he/she does not need to move from that location. Only move out near the road
centerline when it increases the ability to see or be seen, and never
stand in the path of moving or stopped vehicles. It is preferable to stand sideways (facing
the centerline) so there is little possibility of being struck from
behind. Hold the paddle in the right
hand and motion traffic with the left hand.
This position and operation allows maximum visibility of and for the
flagger.
Flaggers should plan a readily accessible escape route in
case of an emergency, typically at 90 degrees to the path of oncoming vehicles.
The flagger’s vehicle, and any other work vehicles, should
be at least 100 feet from the flagger station.
In the photo, the flagger’s pickup is blocking his most
effective, quickest escape route. He is
standing out on the road with his back to approaching traffic. And he is holding the paddle in his left hand
rather than his right.
The two cones on the shoulder preceding his location are
often used to help bring attention to the flagger station. Some agencies require them. They can be a good safety addition.
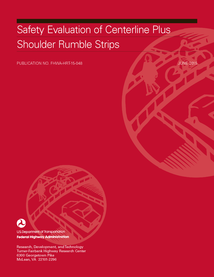 Safety Evaluation of Centerline Plus Shoulder Rumble Strips
The Federal Highway Administration organized a pooled fund study of 38 States to evaluate low-cost safety strategies as part of its strategic highway safety effort. One of the strategies selected for evaluation was the combined application of centerline and shoulder rumble strips. This strategy is intended to reduce the frequency of crashes by alerting drivers that they are about to leave the travelled lane. Geometric, traffic, and crash data were obtained at treated two-lane rural road locations in Kentucky, Missouri, and Pennsylvania.
The combined results for all states indicate statistically significant crash reductions for all crash types analyzed. The crash type with the smallest crash modification factor (CMF) (i.e., the greatest crash reduction) is head-on, with a CMF of 0.632. Run-off-road and sideswipe-opposite-direction crashes have estimated CMFs of 0.742 and 0.767, respectively. For run-off-road, head-on, and sideswipe-opposite-direction crashes combined (i.e., lane departure crashes), the estimated CMF is 0.733. For all crash types combined, CMFs of 0.800 for all severities and 0.771 for fatal+injury were estimated.
For a free copy of this report, contact T2.
|
Have you been waiting to see what TC3's trainings have to offer? Test drive
"Construction Inspection of Structures: Rehabilitation and Maintenance of
Structures" and "Critical Path Method (CPM) Scheduling," new
courses available at no cost through September 2017!
TC3's training
store (part of the AASHTO bookstore) offers more than 130 online courses.
For states
that financially support the TC3, all courses in the curriculum are free
24/7.
Registrants must sign in before they will see the price that applies to their account.
The Rehabilitation and Maintenance course is the fourth course in the
Construction Inspection of Structures Series. This course serves as an
introduction to the repair of concrete and steel structures. Topics include inspection
activities, repair procedures, joints and bearings, bridge deck removal and
rehabilitation, and structural steel and concrete coatings.
This course, which is recommended for 5 PDHs, is designed for individuals
with an interest in bridge construction in the following roles: minimal
experience and/or entry level construction engineers, inspectors, and
technicians.
Upon completion of this course, participants will be able to:
- Describe the role of bridge plans, specifications, and
drawings as part of construction inspection activities;
- Describe the general process of selecting appropriate
bridge repair and rehabilitation activities;
- Explain structural repair procedures for concrete and
steel structures;
- Describe the various types of joints and bearings used
in structural repair;
- Explain considerations for bridge deck removal;
- Compare bridge deck replacement to deck rehabilitation;
and
- List inspection activities used for steel and concrete
coatings used during bridge rehabilitation.
CPM scheduling is a step-by-step project management technique for planning
that defines critical and noncritical tasks with the goal of preventing delays
to a project. This course focuses on what a CPM schedule is, some of the basic
terms and concepts related to CPM scheduling, and how to build and develop a
baseline schedule.
This course is designed for construction field personnel, including new
employees, technicians, inspectors, or others with little or no CPM scheduling
experience. It’s also applicable to anyone interested in learning more about
CPM schedules.
Upon completion of this course, participants will be able to:
- Define CPM scheduling;
- List the components of a CPM schedule;
- Define and calculate forward pass, backward pass, and
total float;
- Describe the elements and application of a baseline
schedule; and
- Explain how to plan a schedule based on the CPM
schedule.
Did You Know?
All TC3 trainings are broken up into modules ranging from 30 minutes to 1.5
hours. The courses are designed so you can go at your own pace and absorb the
information.
Additionally, you don’t have to finish a training in one sitting. You can
exit a course and return to complete it as many times as you wish. The learning
management system will keep track of your training progress and will open where
you left off each time you log back in.
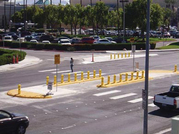 The safe
transportation for every pedestrian (STEP) program the Federal
Highway Administration is promoting in Every Day Counts round four (EDC-4)
includes five proven countermeasures to get pedestrians safely across the road
at uncontrolled crossing locations.
- Crosswalk visibility
enhancements, such as crosswalk lighting and enhanced signing and marking,
help drivers detect pedestrians.
- Raised crosswalks are a
traffic-calming technique that can reduce vehicle speeds and encourage
drivers to yield to pedestrians.
- Pedestrian
refuge islands provide a safer place for pedestrians to stop at
the midpoint of the road before crossing the remaining distance, which is
particularly helpful for pedestrians with limited mobility.
- Pedestrian
hybrid beacons provide a stop control treatment at locations
where pedestrian volumes aren’t high enough to warrant a traffic signal.
They are a useful device for higher speed multilane roads.
- Road diets,
also an EDC-3 innovation, reconfigure a roadway cross-section to better
accommodate all users’ needs. It can reduce vehicle speeds and the number
of lanes pedestrians need to cross and create space to add new pedestrian
facilities.
See FHWA’s Proven Safety
Countermeasures web page for more information on STEP
countermeasures and strategies to improve pedestrian safety.
|
Enhanced Winter Road Maintenance Workshop – October 3 in Keizer
The Oregon Counties Engineers and Surveyors (OACES) are
sponsoring a free workshop addressing Enhanced Winter Road Maintenance.
This is a hands-on workshop for supervisors, managers, and
decisions makers who give direction to winter crews on product choices,
defining applications rates, and how and when they should be applied.
Agencies’ sharing of current practices and outcomes will
be greatly welcomed! Information and workshop registration can be found at: www.co.marion.or.us/PW/Roads/oacesworkshop
Williams Pipeline Emergency Response Training
On October 19th from 1:00 pm to 3:00 pm, the City of Gresham is hosting Pipeline 101 and Pipeline Emergency Response as well as a review of the July sinkhole incident. To register for this free workshop, contact the T2 Center.
|