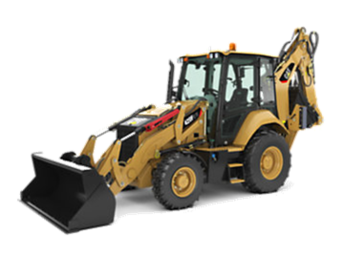 Some equipment dealers offer a special line of “certified” used products. These are generally lower-hour machines that have passed a rigorous inspection and meet very high standards of quality and performance. They are often backed by an attractive warranty and can represent a good alternative to new.
Remanufactured or rebuilt
Those premium-quality machines that are built to last forever may have a second life to offer. Some manufacturers and dealers restore these units to their original specifications and send them back to work. Consider having one of your older machines remanufactured or buy a rebuilt product from a reputable dealer. Taking advantage of that extra life not only saves money, but also reduces waste and conserves natural resources.
BE CREATIVE
While your Plan B for procurement might include rental or used equipment, don’t assume you need a larger fleet to accommodate a heavier workload.
There are other ways to get more work out of an existing set of assets.
Site design
Efficient workflow saves time and money. Look at your operation with a critical eye and take steps to streamline your processes and eliminate non-value-adding activities.
System matching
Heavy equipment is designed to function as a system. Be sure all aspects of your earthmoving system are sized right and equipped to work together efficiently.
Work tool selection
The right work tool can make all the difference when it comes to efficiency. If an existing machine isn’t handling a job, perhaps it needs a bigger blade or a larger bucket.
Maintenance discipline
A well-maintained fleet runs at top performance and is better able to do demanding work, quickly and economically.
Training
Operator skills vary widely and have a big impact on efficiency. Invest in training and you’ll get more done with your current fleet.
BE DISCRIMINATING
|
 No matter how effectively your fleet is performing today, it’s important to have a Plan B in your back pocket, just in case the workload in your community increases and you don’t have the funds to buy new machines.
Not every dealer is equipped to help you develop a solid plan. So be discriminating when it comes to choosing a dealer partner. Make sure they offer a full range of new, used and rental options and have the expertise to help you maximize the return on your equipment investment.
Reprinted with permission from CAT Equipment.
|
The Safety Circuit Rider program is off and running with the hiring of Michael Swan in January (see Director’s Corner for personnel updates).
The Safety Circuit Rider is available to city, county, and tribal employees responsible for transportation safety. He is available to assist with many things, including:
- helping to identify areas of improvement on the agency’s road network
- identifying crash sites by severity, number of crashes, or types of crashes
- identifying potential benefits for a variety of safety improvements for both spot and system wide crash reduction
- calculating benefit-cost ratios
- confirming the identification of both spot and systemic crash history that could use funding improvements to reduce the number of crashes and the severity of each crash
- helping to determine a potential fix for the safety concern
- determining what funding sources are available for the type of project needed
- navigating the funding application process through ODOT
- determining if the project has a good chance of being placed in the Statewide Transportation Improvement Program (STIP)
The safety projects will be funded based on ODOT Region (see ODOT region map) and the final list will be the responsibility of the ODOT Region Traffic Managers.
ODOT Region Traffic Contacts
Region 1 Traffic Manager – Sue D’Agnese (503) 731-3427
Region 2 Traffic Manager – Angela Kargel (503) 986-2656
Region 3 Traffic Manager – Shyam Sharma (541) 774-6335
Region 4 Traffic Manager – Joel McCarroll (541) 388-6189
Region 5 Traffic Manager – Tom Wallace (541) 963-1342
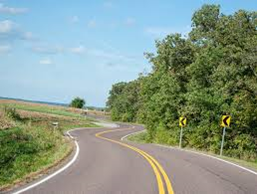
The 2009 edition of the Manual on Uniform Traffic Control Devices (MUTCD) included a mandate that all curves on arterials and collectors with an Average Annual Daily Traffic (AADT) count of 1,000 vehicles per day or more shall be appropriately signed. The actual language is:
“In advance of horizontal curves on freeways, on expressways, and on roadways with more than 1,000 AADT that are functionally classified as arterials or collectors, horizontal alignment warning signs shall be used in accordance with Table 2C-5 based on the speed differential between the roadway’s posted or statutory speed limit or 85th-percentile speed, whichever is higher, or the prevailing speed on the approach to the curve, and the horizontal curve’s advisory speed.”
The MUTCD goes on to state, “Horizontal Alignment Warning signs may also be used on other roadways or on arterial and collector roadways with less than 1,000 AADT based on engineering judgment.” The deadline for complying with this mandate is December 31, 2019. Section 2C.06 and table 2C-5 of the MUTCD provide guidance on the types of signs and their placement.
ODOT’s current standard tool to evaluate curve advisory speeds is Rieker CARS. This electronic, GPS-based system is much easier and faster to use than the old tube method. Each of ODOT’s Regions has their own unit and website login.
|
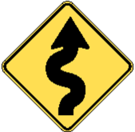 ODOT was able to purchase additional loaner units specifically for cities and counties to use on their roads. There are five units specifically set up for local agencies to borrow, on a first-come-first-served basis.
If a local agency wants to use a unit, they should contact Eric Leaming in ODOT’s Traffic-Roadway Section concerning the availability of a unit. The system comes with everything the local agency needs except for staff and a vehicle with which to collect the data. Eric provides in-person training when he drops off the unit and provides technical support throughout the loan period.
If a local agency has their system set up with milepoints that can be tied to a latitude and longitude, we can take that information and put it into the system to automatically name curve reports. Eric highly recommends this, as it saves time, reduces errors, and keeps everything straight. Washington, Clackamas, Multnomah, and Lane counties have all taken advantage of this feature.
ODOT is committed to assisting local agencies to meet these signing requirements and will provide as much assistance as possible.
Eric may be contacted at 503.986.3610 or at eric.s.leaming@odot.state.or.us.
|
We have recently added two new members to the T2 Center staff.
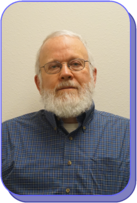 Michael Swan
Michael began working for the T2 Center in January as the new Safety Circuit Rider. Michael is no stranger to ODOT, having worked for the Department for 30 years before his retirement in 2004. During his time with ODOT, Michael worked as a construction inspector and surveyor, a roadway designer, and spent a number of years in the Local Government Section. After his retirement from ODOT, Michael worked for OBEC Consulting Engineers as a project manager from 2004 until his retirement in 2010.
While both at ODOT and OBEC, Michael was a member of the Oregon Association of County Engineers and Surveyors (OACES) and served on the liaison committee between OACES and the American Council of Engineering Companies of Oregon.
|
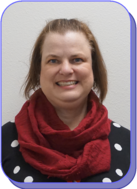 Lyndee Bahr
Lyndee came to us mid-January on a temporary assignment with over 20 years background in training and administrative work. She previously worked for the Oregon State Police for 10 years. She will be helping Linda Milligan out in the T2 office during the busy spring season while I will be out on maternity leave. Her assignment will go through June.
Please join me in welcoming these two talented individuals to our team!
|
 Oregon T2 Center Director
Our Emergency Bridge Assessment class has recently been updated, and our Circuit Rider trainers are ready to bring it to you.
This two-hour class teaches public works employees how to inspect a bridge after a seismic or other event that may have caused damage. It covers preparations that agencies should take prior to a seismic event, using the bridge inspection form, reporting the results of the inspection, and marking and closing a bridge when necessary.
Contact us at (503) 986-2855 or T2Center@odot.state.or.us to discuss bringing this class to your location.
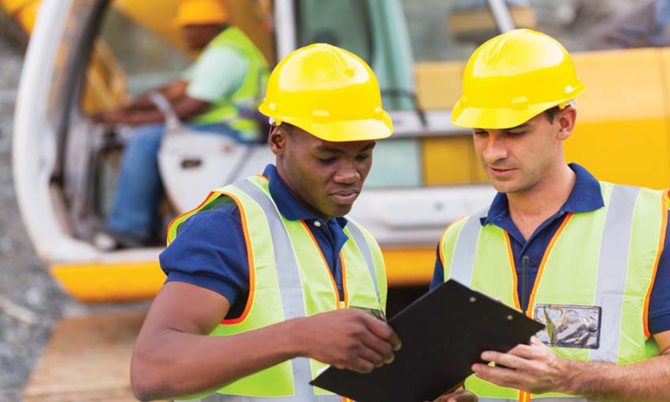 Public works employees are faced with hazardous situations every day, including working around or operating heavy equipment, dealing with motorists, working with dangerous products, and exposure to environmental issues (such as excessive heat or cold, poisonous plants, ticks, etc.). The number of potential hazards that road crews and other public works employees face is extensive, which is why it is important to have an understanding of common safety practices, foster a culture of safety, and have procedures for safe operations in place. The most important thing to remember in terms of safety is to use common sense and have the right attitude. If these two things are present, the rest will fall into place much easier.
Personal Protective Equipment (PPE)
A basic foundation of any safety program is a focus on personal protective equipment (PPE). This includes items such as safety vests, gloves, hard hats, steel toed work boots, eye protection, ear protection, dust masks, chaps, and so forth. From a management standpoint, it is essential that each employee is provided with training on who is required to wear PPE, why they are required to wear it, and when they are required to wear it.
Common PPE and Barriers
Most workers appreciate the value of safety, but they often don’t like the inconvenience of wearing PPE, or they don’t think an accident will happen to them.
Wearing hearing protection is an item that some employees balk at. As a supervisor or manager, you may hear statements such as, “If I wear it, I can’t hear other workers.” “I’m used to the noise.” “Protectors are uncomfortable.” “I’ve already lost some of my hearing.” Explain that the reality of not wearing hearing protection can lead to hearing loss, even complete hearing loss.
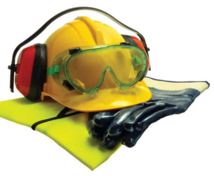 In some instances, workers may be required to wear hard hats. This is another PPE that workers sometimes balk about wearing. “It makes it hard to see.” “It’s not really going to help save my life if something falls on my head.” As a manager, facts are important here. Educate your employees about how hard hats resist and deflect blows to the head, how they act as shock absorbers, and that they shield the employee’s scalp, face, neck, and shoulders against splashes, spills, and drips. Also, remember that as a general rule, hard hats should be replaced every two years, if they are worn every day.
Additionally, if the hard hat has had direct impact, such as by falling debris, it needs to be replaced immediately.
Reflective vests and uniforms are another great PPE item, but again, some employees are resistant to wearing these items. “They’re not comfortable.” “The lime green color attracts bugs.” “They’re too hot.” All of these statements may be true, but the benefits of wearing this PPE outweigh the potential risks and discomfort. Explain that by wearing this PPE, motorists and fellow workers have a better chance of seeing the employee, which helps decrease their risk of getting hit, run over, seriously injured, or even killed. Explain why there are different standards for vests for night work versus day work. Also, educate employees on why it is important to keep vests relatively clean and to replace them periodically. A vest that is dirty will often cover the reflective stripes, thus decreasing the visibility and effectiveness of the garment. Keep in mind that vests will need to be replaced after they have been washed the designated number of times, as indicated by the manufacture on the garment’s label.
Getting Buy-In From Employees
If you are on the management side and you are looking at purchasing new PPE, for example hearing protection equipment, solicit feedback from your employees on what items they like and have found more comfortable. Find out what their experience has been with PPE that you are looking to reorder or replace. While you might not be able to provide everyone with their first choice, by incorporating your employees’ feedback in the process, you’ll often end up with better products and a better attitude toward your PPE and safety program.
Reprinted with permission from West Virginia LTAP.
|
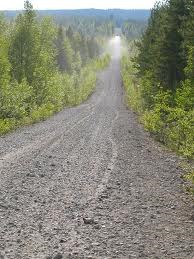 Like fingerprints, each unpaved road is unique. The wear surface may be gravel, crushed rock, or sand, but all have one thing in common: maintenance is required to keep the roadway in good driving condition.
Traffic displaces road surface material onto shoulders and into ditches, forming ruts in the roadway. Washboarding forms at stop signs, hills and turns, and in areas of acceleration or braking. Storms, runoff, and snowplowing also take their toll on unpaved roadways.
Following are 12 tips that can help you lengthen road maintenance intervals and avoid rework:
- To remove wash-boarding, cut the corrugations to their full depth, then regrade the area with moist material that will compact. (Corrugations filled with loose, dry materials will reform quickly in areas of high vehicle traffic.) Corrugations are best removed by using a scarifier or a serrated cutting edge.
- Articulating the rear frame toward the toe of the moldboard by 2 to 5 degrees helps reduce motor graders’ tendency to bounce and is extremely effective when cutting out washboards. This places one front tire slightly ahead of the other, allowing one tire to be on top of a corrugation while the other is in the bottom. As the tires roll up and down through the washboard, the front axle will pivot up and down, keeping the front mainframe stable. Don’t use the crab mode when scarifying wash-boarded areas. This can bend the scarifer shanks and/or linkage.
- Cut to the depth of major potholes to eliminate them. (Again, filling holes with loose, dry material is ineffective, as traffic quickly displaces the loose material and the holes reform.)
- Typically, begin road maintenance with the moldboard top approximately 2 inches ahead of the cutting edge, and then adjust to the material and conditions. Tip the moldboard forward or back to obtain and maintain the desired cutting-rolling action. Tipping the moldboard forward will increase moldboard throat clearance. Generally, a wider throat opening allows better material flow along the moldboard in a wide variety of soil types. Maintaining a rolling action on the material while working reduces the horsepower required and provides maximum productivity.
- Material buildup in the circle area may increase circle wear. It can also stop material rolling action and cause it to be bulldozed. Bulldozing material requires more horsepower and more traction and reduces motor grader productivity.
- Apply only enough downward pressure to accomplish the task. Excessive downward pressure on a hard, dry surface causes rapid cutting edge wear, requires more horsepower and fuel, and reduces productivity.
- The blade’s tip angle should be positioned with the cutting edge at 90 degrees to the road surface. In this position, downward pressure on the moldboard places less stress on the cutting edge and retaining bolts. The edges also tend to ride over objects, which helps prevent machine damage.
- For maximum machine stability when maintaining roadways, the motor grader’s main frame should be straight with the drawbar and circle-centered under the frame.
- For the widest possible pass on the travel surface, keep the moldboard angle as square to the frame as possible. If material starts to flow around the leading end of the moldboard, or the rolling action dies, increase the blade angle.
- Keep machine travel speed as high as possible for maximum productivity but low enough to prevent machine bounce (generally, 4 to 7 mph).
- Moldboard angles of 10 to 30 degrees are normally used in light, free-flowing material. Higher moldboard angles of 30 to 50 degrees are required when processing wet-sticky material, mixing large windrows, and ditching.
- To cut hard material or for finishing work, tip the moldboard further forward than the start position. When finishing, tip the moldboard top 4 to 5 inches ahead of the cutting edge so the cutting edge is approximately 90 degrees to the cut surface. This moldboard tip position will generally position the drawbar parallel to the finished grade.
As always, road conditions and your fleet are factors in your agency’s road maintenance practices.
Article adapted from the original in Caterpillar’s Governmental Solutions, Spring 2012. Also seen in Iowa LTAPs April-June 2015 Technology News
|
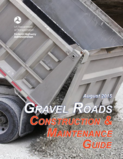 A comprehensive manual that addresses most issues that deal with gravel road maintenance, the Gravel Roads Construction and Maintenance Guide is designed for local agency officials, managers, and grader operators who are responsible for designing and maintaining gravel surfaced roads.
The T2 Center has resources available pertaining to gravel road construction, maintenance, dust control, grader operation, and many others. To order your free copy of the Construction and Maintenance Guide or to find out about other gravel road resources, contact the Oregon T2 Center at (503) 986-2855 or T2Center@odot.state.or.us.
|
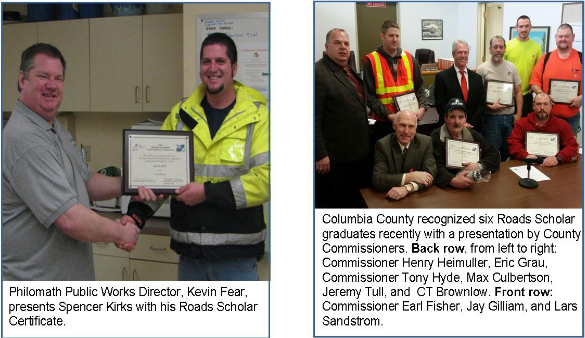 |
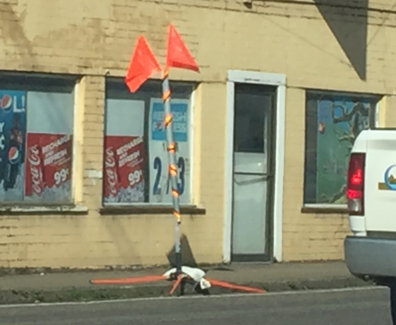 |
When placing and maintaining work zone signs you are required to remove the two warning flags when the sign is rolled up or turned away from traffic due to lunch breaks or other stoppages of work activity. The second issue here is the location of the sign stand. It is very important to place your sign and stand where it does not pose a risk to traffic. Here the stand is situated such that it encroaches onto the fog line at the very edge of the travel lane. Once the sign is opened, it would intrude into the traffic flow. It is preferable to place the sign and stand at a location which takes into account its proximity and impact to the travel lane.
 What Circuit Riders Do
by Bob Raths
The T2 Center currently has three trainers on staff who are often referred to as Circuit Riders. The three — Bill Kolzow, Tony Jobanek and Bob Raths—all retired from other transportation-related careers and work part time for the T2 Center.
Many of our customers ask, “Just what does a Trainer/Circuit Rider do?” and we are glad you asked. Our mission is to provide transportation-related training, education, and technical assistance to local transportation agencies throughout Oregon. In other words, our goal is to help you do your job better.
We attempt to visit every incorporated city, county, USFS, BLM, and tribal office in Oregon at least once a year. Visits by T2 trainers usually start in the spring and, in fact, are already underway for 2016. During that visit, the Trainer/Circuit Rider will:
- drop off a packet of transportation-related materials and technology
- inquire about any needs or questions you have that the T2 Center might be able to assist with, either while we’re there or through our many contacts
- describe the T2 Center’s free training classes
- help acquaint you with the T2 website and look for ideas to share
T2 Trainers teach a variety of free safety-related classes (currently 12 in all) at your workplace. In other words, we bring the training to you! We are often asked, “When will you be giving a class in my area?” The answer is, “When you make a request.” Interested organizations should review the classes currently offered by the T2 Center, decide which class or classes they are interested in, and request a date to be scheduled. We are continuously updating current class material and developing new classes as standards and customer needs change. T2 Trainers are also active with other organizations which offer training and employee development.
In addition to the three Trainer/Circuit Riders described above, the T2 Center also employs Michael Swan as a Safety Circuit Rider. Michael brings a wealth of transportation experience to the role, having worked as a construction inspector, surveyor, roadway designer and project manager with ODOT until his retirement in 2004. See the article on the next page for more information about the Safety Circuit Rider program and how it can help your agency to analyze and address safety issues.
To arrange for training delivered by one of our three Trainer/Circuit Riders, schedule a visit by our Safety Circuit Rider, or to obtain additional information regarding any of the T2 Center’s programs, please call (503) 986-2855 or email the Center at: T2Center@odot.state.or.us.
|
Rural Local & Tribal Road Safety Toolkit & User Guides
Toolkit: http://safety.fhwa.dot.gov/local_rural/training/fhwasa14072/isrltrst.pdf
User Guide #1: http://ruralsafetycenter.org/resources/list/improving-safety-on-rural-local-and-tribal-roads-site-safety-analysis-user-guide-1/
User Guide #2: http://ruralsafetycenter.org/resources/list/improving-safety-on-rural-local-and-tribal-roads-network-safety-analysis-user-guide-2/
The Federal Highway Administration’s (FHWA) Toolkit for Rural, Local, and Tribal Road Safety provides a step by step safety analysis process along with the tools, examples and resources. The accompanying User Guides give real world examples through two hypothetical typical scenarios.
Gone are the days of searching multiple websites or documents for information on rural road safety to make a meaningful impact on safety. The Toolkit and User Guides bring together the components of an effective safety process with the tools and resources and makes it possible to address safety conditions through this resource.
Traffic Incident Management Benefit-Cost Estimation Tool
Traffic incident management (TIM) strategies are major approaches to deal with safety and mobility issues resulting from traffic incidents on the roadways. These strategies support quick incident response, thereby shortening incident duration and controlling traffic delays around the scene.
This web-based tool features different subtools for eight different TIM strategies, and users are able to input their own parameters based on their local experiences and engineering judgment. The tool also provides default values for these parameters to facilitate quick TIM benefit cost evaluation, particularly for areas where targeted TIM strategies have not been implemented and no relevant data is available.
The tool can be used on any updated web-standard browser, and can be downloaded as a zip file from FHWA’s web site at http://www.fhwa.dot.gov/software/research/operations/timbc/
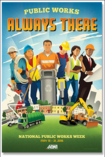 Every year National Public Works Week gets bigger and better. The number of participating municipalities continues to grow, which means the number of citizens who are exposed to the value of public works grows.
The 2016 National Public Works Week is May 15-21 and the theme is "Public Works Always There." This theme showcases the pervasiveness of public works. Communities depend on public works, and the men and women of the profession are always there and always ready. Posters are available through the APWA website: http://www.apwa.net/discover/national-public-works-week.
|
|