Getting Ready for Your Next Compliance Inspection
Are you ready for your next compliance inspection? Owners/operators are required to have a compliance inspection at your facility at least every 3 years and 90 days before the expiration date of your operating permit.
|
-
A compliance inspection must be done for active and inactive tanks.
-
Owners/Operators must have a licensed UST Compliance Inspector complete the compliance inspection. Here’s a list of licensed Compliance Inspectors.
-
Reach out to a licensed compliance inspector and get your inspection scheduled at least 90 days and up to 180 days before your operating permit expiration date.
- Review your financial responsibility (FR) paperwork to make sure it is available and current. For more information on financial responsibility, please visit UST Financial Responsibility.
- Your facility is required to have at least one Class A, Class B and Class C operator. Make sure that you have at least one Class A, Class B, and Class C operators at your facility. Also check to see if anyone has left who is Class A or B certified. You can look up the current operators by looking up your facility in the Facility Summary Sheets for your county. This is located at Facility Summary Sheets.
- You are required to perform a facility walkthrough inspection every 30 days. Check to make sure that you have at least 12 months of inspections available at all times. This is a checklist of things that you need to check each month to ensure your facility is operating the way it should be. You may also download the form at MT DEQ WalkthroughInspectionForm.pdf.
- Your automatic tank gauge (ATG) must conduct a 0.2 gallons per hour (gph) or 0.1 gph tank leak test on each tank at least once every 30 days. The last 12 months of these test results must be kept. Make sure that you have these records and that they are passing. Your ATG must also be checked annually for functionality. Make sure you have a copy of the annual test form like the one located here.
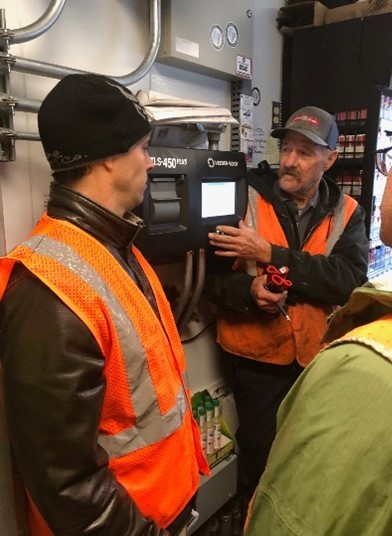
- Interstitial monitoring for your tanks and piping must be recorded every 30 days. This is typically a LIQUID STATUS or SENSOR STATUS. The monthly records and the annual test must be kept for at least 12 months. You must test all of these sensors annually for operability. The annual sensor test form is located here.
- If you are using interstitial monitoring (IM) as your primary method of piping leak detection, your containment sumps must be tested for liquid tightness at least once every 3 years. Make sure you have a copy of the latest test and it is current. The test form for hydrostatic testing is this sump test form.
- If you have single wall pressurized piping with mechanical leak detectors, it is required to be line tightness tested every 12 months. Make sure your last line tightness test is current. Each testing technician will be able to provide you with a copy of the test results. Retain this record for at least 12 months.
- Your automatic line leak detectors (both Electronic and Mechanical line leak detectors) are required to be tested every 12 months to check to ensure that the line leak detector will detect a leak of 3 gph at 10 psi. Make sure your last leak detector functionality test is current. Retain this record for at least 12 months. The test form for functionality testing is this test form.
- Your electronic line leak detectors (ELLDs) must conduct a line tightness test at 0.2 gph or less at least once every 30 days OR conduct a line tightness test at a leak rate of 0.1 gph or less at least once per year. Make sure that you have these records and that they are passing. Retain this record for at least 12 months.
- If your facility has suction piping, your U.S. suction piping may require a line tightness test every 3 years. Make sure your last line tightness test is current and passing. Each testing technician will be able to provide you with a copy of the test results. Keep these results for at least 3 years.
- If your records indicate that you use Statistical Inventory Reconciliation (SIR) as your monthly leak detection method, you must have the last 12 months of records available. Your meter totalizers (in your dispensers or at your POS system) must be recorded each operational day. You must measure inventory, delivery amounts, and dispensing data every operational day and before and after deliveries. These results must be recorded for 30 days or in accordance with your SIR vendor’s requirements. The last 12 months of monthly records must be kept available for inspection.
- Check your metal tanks and/or piping to see if they have impressed current cathodic protection. For these systems [i.e. systems that were installed on an existing tank system and uses a rectifier (DC power source)], a log must be maintained at least every 60 days. The log should show that the voltage or amperage gauge on the rectifier has been checked to see that the power is on and it is operating. The following information should be included in the log: voltage and/or amperage reading, the number of hours recorded from an hour meter (if equipped), status of a red or green indicator light, a name or initials, and the date. A cathodic protection test must be performed every 3 years. Make sure you have a current passing test within the last 3 years. The form for the corrosion protection test is this corrosion test form.
- Check your metal tanks and/or piping to see if they have galvanic (with anodes) corrosion protection. This is a coated steel tank (or piping) with sacrificial anodes attached to it. These anodes corrode instead of the tank itself. A cathodic protection test must be performed every 3 years. Make sure you have a current passing test within the last 3 years. The form for the corrosion protection test is this corrosion test form.
- Your facility has spill buckets for spill containment at the tank fill. You are required to have your spill buckets tested every 3 years to verify that they are liquid tight. Make sure you have a current passing test within the last 3 years. The form for the corrosion protection test is this spill bucket test form. Retain this record for at least three years. This does not apply to aboveground tanks with underground piping.
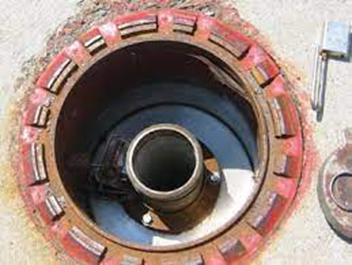
- Check your paperwork to see if your facility has drop tube shut off (DTSO) valves at the tank fills for overfill protection. These valves limit the amount that the tanks can be filled to 95% or less. You are required to have this tested every 3 years to verify that all are functional. Make sure you have a current passing test within the last 3 years. The form for the overfill protection test is this overfill test form. Retain this record for at least three years.
- Check your facility to see if it has a high-level alarm for overfill protection. This alerts your delivery driver to stop filling the tank. The maximum amount the tanks can be filled is 90% or less. You are required to have this tested every 3 years to verify that this is functional. Make sure you have a current passing test within the last 3 years. The form for the high level alarm test is this overfill test form. Retain this record for at least three years.
- Check your facility to see if it has ball float vent restrictors for overfill protection . Ball float vent restrictors close off the tank vents during delivery when the product reaches 90 percent. This alerts your delivery driver to stop filling the tank. The maximum amount the tanks can be filled is 90% or less. You are required to have these tested every 3 years to verify that they are functional. If a ball float vent restrictor fails this test, it cannot be repaired and must be replaced by another approved device. Many of these vent restrictors cannot be accessed and tested. If this is the case, it must be replaced by another approved overfill device, such as DTSO or high-level alarm. The form for the overfill protection test is this https://deq.mt.gov/files/Land/UST/Documents/PDFfiles/Montana_C-5_BFVV_and_Flapper_Valve.pdf. If they can be tested, retain this record for at least three years.
Much of the information for your facility is available online on our Facility Summary Sheets. This information is sorted by county and is available on the Facility Summary Sheet web page.
- We recommend that you use a three-ring binder with tabbed dividers to keep all of your records organized or store your files electronically and make sure they are organized and easily accessible.
- Keep phone numbers for your delivery company, your inspector, your technician, and the UST Leak Reporting Line handy.
Hotline for Reporting Leaks: Monday through Friday 8:00 a.m. to 5:00 p.m. call 1-800-457-0568. After hours and holidays call 1-406-324-4777. NOTE: You must report to a live person. Leaving a message does not constitute a report.
For additional information, contact the DEQ UST program at (406) 444-5300, by email at dequstprogram@mt.gov or visit our website at https://deq.mt.gov/twr/Programs/ust
Petroleum Release Status Report as of June 30, 2022
Petroleum Releases Confirmed and Resolved from January 1 to June 30, 2022)
- New Releases Confirmed: 13
- Releases Resolved (Closed): 20
Summary of Total Petroleum Release Activity*
- Total Confirmed Releases: 4,806
- Total Releases Resolved (Closed): 3,888
- Total Unresolved (Active) Releases: 918
*Note these total numbers are from the start of the DEQ program and include Releases with the status “Transferred to Another Program or Agency.” The other agency or program could be the EPA or another state-lead program (e.g. the DEQ State Superfund Program).
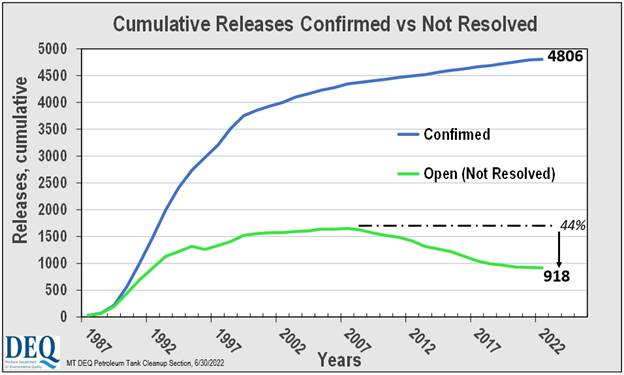 Petroleum Vapor Intrusion Screening
Petroleum vapor intrusion (PVI) is the migration of petroleum-only vapors from the subsurface into nearby or overlying structures. These vapors originate from petroleum-contaminated soil and/or groundwater and in some cases the vapors may accumulate in structures to levels that could pose safety hazards, or acute or chronic health effects.
PVI has been a risk at petroleum release sites for decades, but recent studies have improved our understanding of how petroleum-vapors attenuate in the subsurface and therefore provide a better understanding of when structures are at risk of PVI. Montana DEQ updated its Vapor Intrusion Guide (MontanaVI_Guide_FINAL.pdf (mt.gov)) to include a PVI Screening process to better identify when structures are at risk and need to be sampled.
There are three main steps to the PVI Screening process. Step one includes completing a Conceptual Site Model (CSM) to gather all the necessary information and data needed to accurately apply the screening distances as well as to identify sites where screening distances shouldn’t be applied due to precluding factors.
After completion of a CSM a lateral inclusion zone is applied, this is the second step in the PVI Screening process. The lateral inclusion zone is a 30-foot horizontal distance between the edge of a building and a source of contamination. Buildings that fall outside of the lateral inclusion zone can be removed from any further PVI assessment. Buildings that fall within the lateral inclusion zone need additional screening using a vertical screening distance, this is the final step in the PVI Screening process.
When a building is within 30 lateral feet of contamination there needs to be at least 8 feet of vertical separation between the highest point of soil/groundwater contamination and the lowest part of the structure’s foundation unless contamination contains light non-aqueous phase liquids (LNAPL). When LNAPL is present the vertical screening distance is increased to 15 feet between highest point of contamination and lowest point on a structure. When there are feet of clean vertical distance between a structure and contamination (or 15 feet when LNAPL is present) the building can be removed from any further PVI assessment.
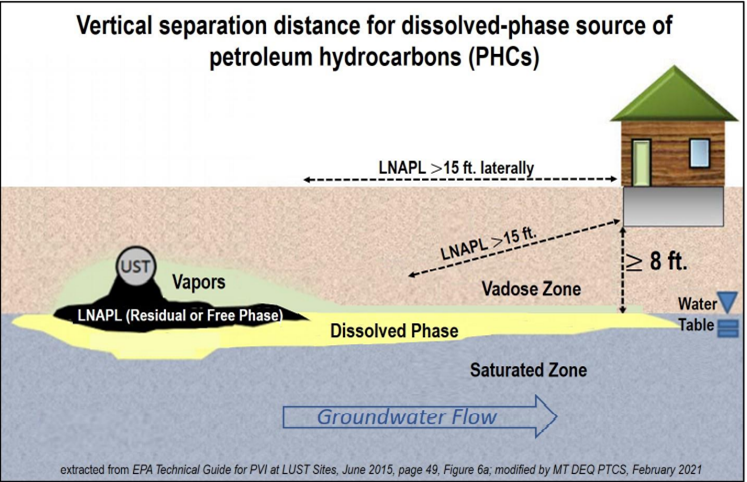 When buildings do not screen out vertically because they don’t meet the appropriate minimum vertical screening distances, the structure needs to be assessed for PVI which typically requires vapor sampling. PVI sampling will be covered in Part 2 of this series which will be included in the next MUST news publication.
|