Things to Consider Before Deciding to Dispense E15 or Higher Blends at Your Underground Storage Tank Facility in Montana
|
|
Before a facility begins to receive and sell E15 (or higher blend ratios), certain topics should be known and addressed. This article is a good resource but not the definitive word on the process. Please contact the UST Program for clarification and assistance with any other UST matters.
A little background: EPA defines E15 as gasoline blended with 10.5% to 15% ethanol. In 2011, EPA approved E15 for use in model year 2001 and newer conventional vehicles through a Clean Air Act waiver request based on significant testing and research. Stations are not required to sell E15.
Vehicles approved for E15 use are:
- Flexible Fuel Vehicles (FFVs)
- Model year 2001 and newer conventional cars, light-duty trucks, and medium-duty passenger vehicles.
Vehicles and engines prohibited from using E15 are:
- All motorcycles
- All vehicles with heavy-duty engines, such as school buses, transit buses, and delivery trucks
- All off-road vehicles, such as boats and snowmobiles
- All engines in off-road equipment, such as lawnmowers and chain saws
- All model year 2000 and older conventional cars, light-duty trucks, and medium-duty passenger vehicles.
EPA’s Office of Transportation and Air Quality developed additional requirements for E15 to reduce the risk of misfuelling because the fuel is only approved for use in light-duty vehicles and trucks 2001 and newer. Stations selling E15 (defined as 10.5% to 15% ethanol) must adhere to the following requirements:
- Product transfer documents must accompany all deliveries of fuel for E15 use.
- The retail station must participate in the fuel quality survey; register at http://www.rfgsa.org
- Ethanol in E15 must meet ASTM D4806. Reid vapor pressure is limited to 9.0 psi in the summer.
|
Checklist for Installing E15 or Blender Pump Dispensing Equipment or Converting Underground Storage Tanks in Montana
Underground Tanks:
- Check with your licensed installer and the UST Program about your intent to dispense E15. Fill out and submit a copy of the Underground Storage Tank Biofuel Installation / Conversion Checklist at least 30 days before the scheduled changeover. If a new installation is planned, you must provide all necessary information for the installation before a permit can be issued. Remember, there are over 60 individual parts of a UST system that need to be certified for use with E15. When doing any piping or tank installation or upgrades, Energy Act requirements also apply. This means installing double wall piping as well as dispenser and tank top sumps with sensors with these changes. This information and more can be found at http://deq.mt.gov/Land/ust/ustPermitting.
- Notify your UST insurance carrier to determine whether it has additional requirements for E15 fuels.
- Contact your insurance company to determine any requirements impacting coverage related to E15 sales. Complete an amended Montana Certificate of Financial Responsibility showing coverage of E15 storage and dispensing.
- If using an existing tank, clean the tank of all water and sediment. Ensure no water is present to protect the quality of your ethanol-blended fuels and your customers’ vehicles (see API Publication 2015, “Cleaning Petroleum Storage Tanks,” and NFPA 326, “Standard for the Safeguarding of Tanks and Containers for Entry, Cleaning, or Repair,” 2010 Edition).
- Determine compatibility of existing UST equipment. Replace incompatible UST equipment. Install UL-listed E15 dispenser, hanging hardware, and shear valve. Keep equipment compatibility records.
- Ensure all visible fittings and connections at the top of the tank are tight (no vapors escape, and no water enters).
- Ensure the sump and spill containment covers will prevent water from entering the system. Identify the E15 fill port and paint the access cover according to API RP 1637. Make certain transport drivers cannot make fuel deliveries to the wrong fill pipe.
- As a precaution to address residual sludge and gum deposits that will be dissolved by ethanol, industry recommends the tank to be filled to 80% of capacity and kept as full as possible for seven to 10 days. The residual impurities will be more diluted in a larger quantity of E15, reducing the risk of vehicle problems. This practice is also likely to expose any problems related to sludge and gum deposits during the initial inspection period.
- Conduct a tightness test of the tank system (0.1 or 0.2 gallon/hour leak rate) with an automatic tank gauging system immediately after the tank is filled to confirm the integrity of the system and that the leak detection equipment is operating properly. Report any failed test results as unusual operating conditions within 24 hours.
- If installing a blender pump, ensure that the ethanol content is updated in the control system for each fuel delivery since the percentage changes according to geography and season.
- Calibrate the dispenser meter at the time of conversion or new installation and two weeks later to verify meter accuracy with E15.
- Label the dispenser with the required EPA E15 label; if E10 and E15 are dispensed from the same hose, add a label stating the 4-gallon minimum fueling volume. Consider using hangtags, pump toppers, and other signage to educate your customers. Price sign inserts, curbside signs, and decals are available from industry associations, including the Retail Ethanol Resources website (http://www.ethanolretailer.com).
Dispensing Equipment:
- Notify the nearest fire department (and/or local first responders) that the site will soon be dispensing alcohol-blended fuels. Verify that fire extinguishers and other onsite safety equipment (necessary to respond to leaks, spills, fires, etc.) are ethanol compatible.
- Use a 5–10-micron alcohol-compatible dispenser filter. Do not use 10-micron gasoline or 30-micron diesel filters.
- Calibrate the dispenser meter at the time of conversion or new installation and two weeks later to verify meter accuracy with E15.
- Label the dispenser with all E15 logos, cautionary labels, and trade commission decals. Use nozzle covers stating that E15 is not gasoline or diesel. Add logos for blender pump fuels and indicate that they are for FFVs only. Consider using hangtags, pump toppers, and other signage to educate your customers. Price sign inserts, curbside signs, and decals are available from industry associations.
Stations must use EPA-approved dispenser and hose configurations. Options include:
- A shared E0/E10/E15 hose, which requires a purchase of four gallons minimum (“four gallons minimum” label must be displayed)
- A dedicated dispenser selling E10 or less.
Maintenance and Operation:
- Train site operators and emergency response personnel responsible for this location on ethanol fuel safety procedures and the differences relative to gasoline.
- Check for water regularly. Ensure that no water is contaminating your fueling system. If water is suspected or detected, track down its source and fix the problem immediately. The best way to guard against contamination is to properly clean and maintain the fueling system. Confirm no leaks exist in the tank fill cap and containment reservoir before beginning your E15 operation.
- If the product seems to pump slowly, check and replace filters. Persistently clogged filters could indicate moisture or another source of contamination.
Final Thoughts on E15 Upgrades
Every effort has been made to ensure that this article is accurate, complete, and comprehensive. However, this article is not intended for use as a “how to” guide for individuals or organizations performing conversions. It is intended to be used as a guide and resource document. Upgrading the tank systems and forecourt to offer E15 can be an expensive investment. We strongly encourage you to engage professional support during installation to ensure fuel integrity and systems compatibility.
Petroleum Tank Cleanup Section 2019 Special Legislative Funding
Background
The 2019 Montana Legislature transferred one million dollars from the Petroleum Tank Release Cleanup Fund (PTRCF) to the DEQ Waste Management and Remediation Division’s Petroleum Tank Cleanup Section (PTCS) to help address petroleum-tank release sites (Releases) during Fiscal Years 2020 and 2021 (July 1, 2019, through June 30, 2021). This 2019 Special Legislative Funding (SLF) was allocated to PTCS to address Releases where remediation work had not progressed due to lack of financial resources and no readily apparent liable person exists. The PTCS’ goals were to investigate, cleanup, and resolve (close) as many Releases as possible. PTCS created a project plan to transparently and fairly allocate the funds to sites where other funding sources were not available.
Project Selection
Funding is limited for cleanup on Releases that are not eligible for the PTRCF, Federal Leaking Underground Storage Tank (LUST) Trust Grant, Brownfields, and/or where owners do not have the ability to pay for cleanup costs not covered by other funding sources. PTCSs backlog of unresolved legacy Releases includes about 570 of the 3,754 Releases confirmed prior to January 2000. These legacy Releases represent a variety of closure challenges including the following: access to the petroleum-contaminated source material to apply effective cleanup, responsible party and property ownership issues, and availability of funding for cleanup. The 2019 SLF was used to investigate, cleanup, and close legacy Releases that may have been PTRCF eligible and needed assistance to meet their co-pay, ineligible for PTRCF reimbursement because they pre-date the PTRCF, owners who do not have an ability to pay for cleanup, or if there was no other funding available and the owner did not not meet Montana's definition of an owner or operator.
PTCS experience gained over the last decade with managing multiple funding sources has promoted significant program efficiencies in coordinating cleanups and closing Releases. Improved efficiencies include use of updated investigation and remediation methodologies, completing work on multiple sites using one Task Order, revising procedures, and improved stakeholder outreach and involvement. PTCS effectively partnered and collaborated with other agencies, DEQ sections, non-governmental organizations, local governments, and the regulated public with a common goal to clean up the environment, protect communities, and redevelop Montana properties.
Example Project: Former Garth Taylor Ranch
The Former Garth Taylor Ranch is located about 5 miles north of Dillon on Montana Highway 91 North in Beaverhead County. The site is a 1-acre parcel surrounded by farmland. This release was confirmed in 1992 when petroleum-contaminated soil was found during the removal of two 500-gallon USTs that were removed from the north portion of this property. No additional work had been conducted at the site. The current property owners have lived there since 2015 and never owned or operated the former USTs.
DEQ used the 2019 SLF to install five soil borings to investigate the remaining petroleum-contaminated soil in the former UST location. The May 2021 soil sampling results were below Montana cleanup standards. The release was reviewed by DEQ and approved for closure in July 2021.
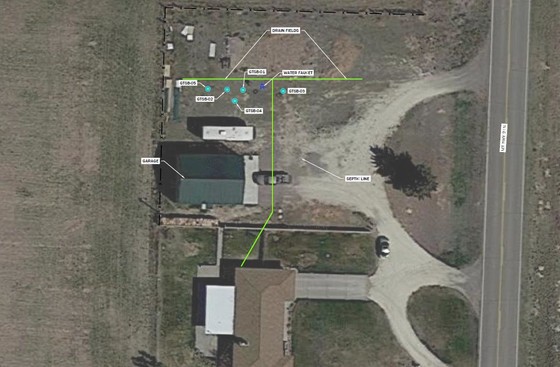 Aerial view of the former Garth Taylor Facility showing the location of the soil borings (teal-colored
dots) installed during the 2019 remedial investigation in the former underground storage tank area
|