The Environmental Services monthly employee newsletter
April is Earth Month - a great time to reflect on the progress the Met Council is making toward developing a Climate Action Plan - and to highlight how MCES staff are shaping its direction through a Councilwide inclusive process.
To date, more than 60 MCES employees have talked with Climate Action Plan Team members about the current state of our division's climate-related work. People have expressed excitement about the possibility of further gains we can make. Our Integrated Water Planning Team is serving as a conduit across our large, complex division to provide ongoing input to the Council's planning team.
Gathering information about our current efforts
MCES employees have shared information about dozens of efforts to measure and/or reduce our greenhouse gas emissions and adapt to changes that the region is already experiencing. Here's a small sampling:
- Groundwater modeling of future climate scenarios
- Optimizing aeration processes at the wastewater treatment plants to use less energy
- Improvements to work scheduling to reduce trips to interceptor and metering facilities
- Landscaping improvements to handle increased rainfall
- Calculating and reporting greenhouse gas emissions
"The breadth and depth of our current work is impressive and will be a solid foundation to create new goals from," said Sara Smith, manager of Sustainability Support, acting manager of Operations Support Services, and a co-lead of the Climate Action Plan Team. "We appreciate the commitment and enthusiasm of staff for this work."
Continue on MetNet.
|
MCES is developing a strategic divisionwide approach to energy management. This Energy Management System is needed since wastewater treatment is energy intensive. At approximately $17 million per year, energy is our third largest expense after debt service and labor costs. Plus, this purchased energy is our single greatest contributor to climate change - as energy use is responsible for about 85% of human-caused greenhouse gas emissions.
A cross-functional team, led by David Ponder, environmental analyst in Sustainability Support, and Trevor Prater, engineer in Process Engineering, is currently documenting our energy consumption (see chart below) and process mapping all the ways we approach energy use - from construction planning to operations and maintenance to asset management. The team's assessment of strengths, weaknesses, opportunities, and challenges will inform how MCES will move forward to address climate change and cost, while ensuring reliable and resilient energy service that, literally, powers our mission.
"I'm proud of the extensive energy conservation we've accomplished across MCES over the years," said Leisa Thompson, general manager. "We're now writing the next chapter of our energy management approach to provide greater value to our community - further protecting the environment while supporting our region's prosperity."
Working with input from across the division, the Energy Management Team is looking at how MCES approaches energy management:
-
Energy efficiency and conservation through equipment and operational changes, like building systems and process optimization of pumps
-
Energy recovery by generating heat or electricity from waste process by-products
-
Renewable energy sources, like electricity from solar power
-
Tariff and cost management using tools like demand management, load shifting and pricing structures
-
Power system resiliency and safety to ensure continuity of our work, such as facility electricity distribution systems, arc flash mitigation, and back-up energy supply sources
Continue on MetNet.
|
Climate change is increasing the frequency and magnitude of extreme rainfalls. Managing this stormwater and conserving groundwater are two ways property owners can be partners in water protection. The Water Resources team in MCES supports local governments by offering grants to demonstrate best management practices for stormwater management and reuse.
Between 2015 and 2019, the team recommended, and the Council approved, more than $2.5 million in grants for 26 projects to cities, watershed districts, and other public entities in the metro area. The results include capture and reuse of millions of gallons of stormwater for irrigation; improved water quality in area water bodies; and in one case, flood prevention for a mosque.
Read how these stormwater grants helped communities adapt to climate impacts:
- Directing runoff away from a mosque
- Reusing stormwater for irrigation
Continue on MetNet.
Stormwater grant projects at Masjid An-Nur, a mosque in North Minneapolis, and City of Hugo.
A high-tech addition to the Metro Plant's Machine Shop is helping our machinist mechanics make much more precise metal parts while nearly recouping MCES's investment in two years. Machinist mechanic William Nelson raised the idea of purchasing a computer numerical control (CNC) lathe a few years ago, based on a previous job experience of going from manual equipment to a CNC lathe and seeing a dramatic increase in precision of the parts he could produce.
Our machinist mechanics use machine tools such as lathes, milling machines, and grinders to produce metal parts for install in equipment in our wastewater collection and treatment system. The new machine they are using is a CNC lathe. A machinist mechanic manually measures parts in a computer-aided design format, inputs this detail into a computer, and indicates what tool should cut specific surfaces, then the CNC lathe uses computerized controls and machine tools to create the specified metal parts. The CNC lathe is designed for turning round parts, such as shafts, sleeves, or tubes.
"The machine and setup costs totaled about $230,000 when we installed it in July 2019," said John Tierney, manager, Mechanical Planning & Maintenance. "Now, nearly two years later, the CNC lathe has saved MCES approximately $180,000 by making our own parts, and the precision of the parts is so much better than with traditional manual lathes. This is very helpful with parts we can't find information about or parts that are no longer being manufactured. For equipment such as pumps and pump shafts, we can take it apart and re-engineer it, measure it up, and make the part. Vendors can do this, too, but at a cost. Our material costs are relatively low."
Continue on MetNet.
|
MCES Construction Services will be recognized with the 2020 Outstanding Achievement Award in Occupational Safety during the 2021 Virtual Minnesota Safety and Health Conference, May 4 and 5.
"Last year was definitely a challenging year, unlike no other in the past, and our staff stepped up to the challenge and focused not only on COVID-19 requirements, but overall safety on the jobsite. Management is proud of all our staff in everything they do, including the ongoing focus on occupational safety that brings this recognition," said Jim Sailer, manager, Construction Services. "This is a well-deserved award."
MCES Construction Services had excellent safety performance in 2019 and 2020, achieving a zero Reportable Injury Rate and Days Away Restricted Transfer rate, according to data tracked by Mike Rhode, senior safety specialist, Environmental Health and Safety.
Continue on MetNet.
MCES recently released two videos to showcase our role in protecting water quality and public health, and fostering growth in the region. Staff are encouraged to use these videos for outreach and engagement opportunities. You might even share them with your family and friends.
Wastewater Treatment for Kids (10 minutes) is a refresh of an MCES presentation created in the early 1990s. It has been one of the most-visited features on the Met Council's external website. Visitors have downloaded the materials nearly 1,000 times per month over the last 10 years. New materials include the video as well as PDF slides for educators and families.
|
Team develops automated evaluation method
A team that designed an automated method for evaluating standard operation procedure (SOP) work has earned a Keystone Team Award. The team members from Performance Excellence & Analytics are Greg Bimberg and Ambika Shashikumar, senior computer systems specialists; Todd Jameson, dashboard analyst; and Graham Rico-Johnson, business systems analyst 3. Additional team members are Kris Hess, business systems analyst 3, Administration & Communications, and Kevin Sederstrom, applications developer 4, Information Services.
Last October, Scott Bowes, manager of Training & Program Supervisors, was looking for a way to generate an automated report that he and the program supervisors could use to evaluate their SOP development work. Being able to pull multiple sources of data into a single report would provide a one-stop shop for reviewing the status of SOPs, set priorities for SOP development, and set staff goals and performance indicators. Bowes asked Betsy Haag, principal administrative specialist in Operations Support Services, to lead the project.
"This team of individuals went above and beyond to help me work through an outline of what was needed and who would need to be involved, then worked individually as well as collectively to coordinate using several data systems to generate the requested report," Haag said. "This report will improve the efficiency of our program supervisors and allow Operations staff requesting work from them to see what is already in progress and when the work is projected to be done."
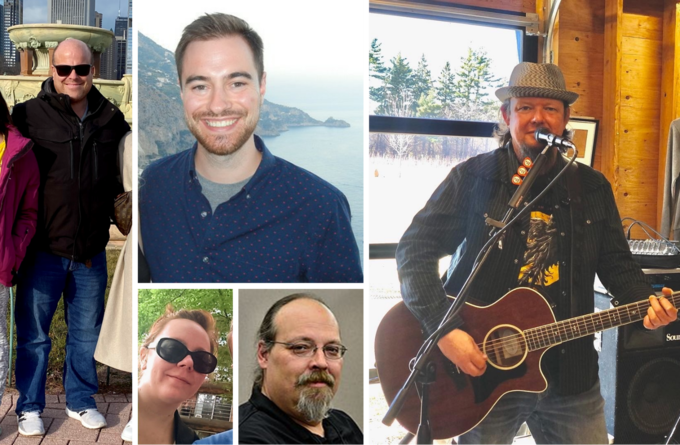 Clockwise from left: Greg Bimberg; Graham Rico-Johnson; Todd Jameson; Kevin Sederstrom; Kris Hess
 
Randy Gelner excels as mentor
For his work on training and instructing numerous new employees, a Keystone Award was presented to Randy Gelner, an electrician in Electrical Planning & Maintenance who works out of the Regional Maintenance Facility. Gelner was the main mentor and instructor for new employees in his group who were assigned to the Interceptor Services workforce.
"Randy was instrumental in training and instructing these new employees," said Chuck LaPierre, Electrical Planning & Maintenance manager, in nominating Gelner. "His commitment to MCES and Maintenance & Security has ensured a well-trained professional staff for the future reliability of our business. Through Randy's dedication and unselfish work ethic, he has ensured that his experience and knowledge will be carried forward with our future workforce."
See full award details on MetNet.
|
A recap of recent Met Council announcements relevant to MCES
-
Chair Zelle addresses Chauvin trial verdict and anti-racism trust agreement: In an email last week to all employees, Chair Charlie Zelle reflected on the verdict in the Chauvin trial, the recent killing of Daunte Wright, and all the work there is to do in the fight for equity and racial justice. He also shared with staff a commitment the Met Council signed to participate in the Regional Anti-Racist and Economic Justice Trust.
-
New process for COVID-19 Leave requests related to vaccine reactions: MCES has a new process for submitting COVID-19 Leave requests related to the vaccine. Staff may use COVID-19 Leave if they have a reaction to the vaccine and need to take time off. Staff may not use this leave to get a vaccine.
-
Apply by May 10 for next MentoringWorks cohort: The Met Council's 2021 virtual program offers quarterly starts that last six months. Submit your mentor or mentee application now to be considered for the second group, which starts with a virtual introductory session May 20.
-
New Learn login screen and process: Logging into Learn will look different starting the week of May 10. MCES employees should login selecting "Employees with Council-issued email addresses log in using their network account."
-
Schedule a Microsoft consultation: Do you have a manual and repetitive process you would like to make more efficient? Schedule a consultation with the Microsoft experts in Enterprise Content Management to find a solution. Microsoft tools - SharePoint, Teams, Forms, Planner, and many more - can be used together to automate and improve your workflows.
-
Earn $40 - Complete a health assessment by May 31: All employees who have HealthPartners medical or dental coverage through the Met Council are invited to participate in the online assessment, which poses questions about nutrition, exercise, emotional health, life satisfaction, and sleep, and generates customized recommendations based on your results.
Full information on MetNet.
COVID-19 RESOURCES
Anniversaries
Congratulations to these employees celebrating milestone anniversaries!
40 YEARS
Mitch Berg, lab analyst 2, Analytical (Lab) Services, Metro Plant
15 YEARS
Steve Eppel, security specialist, Maintenance & Security, Metro Plant
10 YEARS
Mike Olerich, principal contract administrator, Construction Services, Metro Plant Construction Field Office
5 YEARS
Jack Barland, senior environmental scientist, Water Resources, Metro Plant
Monica Lorentz, lab technical coordinator, Analytical (Lab) Services, Metro Plant
Ashley McQuiston, senior metering and alarm system operator, Interceptor Services, Regional Maintenance Facility (RMF)
Naoise Moe, interceptor service worker 1, Interceptor Services, Mound Lift Station
Wayde Schroeder, assistant business unit manager, Interceptor Services, RMF
James White, interceptor service worker 2, Interceptor Services, Mound Lift Station
Sadie Wolf, contract administrator, Construction Services, Blue Lake Construction Field Office
Staffing changes
Posted by Human Resources since the March Update
DEPARTURES
Kenneth Knudsen, contract administrator, Construction Services, Seneca Plant Construction Field Office (CFO)
Thomas Veilleux, principal contract administrator, Construction Services, Metro Plant CFO
Story idea? Contact Deb McKinley by email: deb.mckinley@metc.state.mn.us.
|