Hennepin County is proposing to modify our hazardous waste
fee schedule for 2019. The current fee
schedule has been in place since January, 2017. The public hearing on fees is
scheduled before the Hennepin County Board’s Budget and Capital Investment Committee
on November 1, 2018 from 9:00 am - noon.
The proposed revision calls for a 5% increase in both base
fee and volume rate for hazardous waste generator operations and a 5% increase
for hazardous waste facility operations.
Public Comment
If you have comments or questions regarding the proposed
schedule, please contact Bruce Forness at 612-348-8690 or e-mail him at: bruce.forness@hennepin.us
If you prefer to testify at the public hearing, please
contact the Clerk to the Board at 612-348-4019. If you would like to submit
written comments on the proposed fees, please send them to:
Hennepin County
Board of Commissioners, Attn: Clerk to the Board
A2400, Hennepin County Government
Center
300 S. 6th St.
Minneapolis, MN 55487
Many
businesses have been able to improve their processes or substitute products,
resulting in less hazardous waste generation. Businesses may not realize how
much the reduced waste has impacted their hazardous waste generator size until
they are reporting the waste amounts during the annual re-licensing process. Reducing
a company’s hazardous waste generator size isn’t automatic when those updated
numbers are reported. There are several items that must be submitted to us to
demonstrate that you are eligible for a generator size reduction.
The process
includes the following steps before a size change can be approved:
- Contact the most
recent inspector that visited your site, they can help you determine which
waste streams to count prior to submitting the documentation.
- Provide an
explanation of what processes have changed resulting in the reduced waste generation,
and how you expect that the company will be able to stay at the lower generator
size.
- Document and submit
the waste generation amount per month. Several years of data is usually
required showing that the numbers fall within the new generator size requested.
- Inspector reviews
documentation submitted and brings to a group meeting for discussion.
- Inspector contacts
you regarding the decision made. If a size change is warranted, you will be
informed on timing for the size change.
Following these steps ensures that the
same process is followed for all businesses requesting a downgrade in generator
status.
Inspections are conducted for many
reasons, primarily to review a company’s hazardous waste management activities.
While inspections are regulatory in nature, the inspector can also provide clarification
and technical assistance to help employees better understand the hazardous
waste rules.
Types of inspections include:
Drop in inspection
- Inspector is in the area and drops in to
determine whether a hazardous waste license is needed or not.
- Licensing forms may be completed during the
inspection.
Routine inspection
- Frequency is based on a company's hazardous
waste generator size and risk.
- Companies generating waste with a greater
environmental risk, are inspected more frequently, as well as those who have
mismanaged hazardous waste in the past.
- To prevent incomplete inspections, ensure that
there are always knowledgeable staff available on-site, capable of representing
the operation during an inspection.
Follow-up inspection
Occurs when a recent previous inspection was
incomplete or to verify that violations observed during a prior inspection have
been corrected.
Complaint inspection
- Conducted due to receiving a complaint regarding
hazardous waste management or other environmental issue at a business.
- Investigate the validity of the complaint.
- Obtain details to ensure the business
understands rules applicable to what was alleged.
- Work with the company to resolve the
situation, as necessary.
Closure inspection
- Occurs as the result of a closure
notification.
- Documents the present conditions at the site
- All hazardous materials and wastes must be
shipped offsite; a company must not move hazardous waste to a new location.
Hennepin County recognizes generators and facilities for having a hazardous waste program that is in full compliance with hazardous waste rules and regulations.
Since April 2018, the county has conducted 61 inspections where generators have been in full compliance. The no violations listing not only shows that it is possible for any size generator or facility to be in full compliance at the time of the inspection, but that it also happens with some frequency.
Click here for a printable list of the 61 generators without a violation (PDF). This list also contains generator size.
Hennepin County maintains a list of enforcement outcomes from hazardous waste violations on our website to reinforce the importance of compliance with hazardous waste and tank regulations. The list includes recently resolved civil and criminal cases, including fines and penalties assessed by the U.S. Environmental Protection Agency, the Minnesota Pollution Control Agency or Hennepin County. All of the cases originated from violations found during hazardous waste generator, hazardous waste facility or tank inspections at businesses in Hennepin County.
The county has resolved four enforcement cases for hazardous waste violations since April 2018.
Construction Materials Inc, St. Louis Park Violations: Failure to operate to prevent a release Generator size: SQG Outcome: $828.00 fine
Great Northern Corp, Brooklyn Park Violations: Failure to list the emergency coordinator contact information on its emergency telephone posting; Failure to abide by the general hazardous waste manifest requirements Generator size: SQG Outcome: $578 fine
Island Park Auto and Marine, Mound Violations: Faiulre to obtain a hazardous waste generator license Generator size: VSQG Outcome: $828.00 fine
TCR Engineered Components LLC, Brooklyn Center Violations: Failure to label containers with a clear description and the word's "Hazardous Waste"; Failure to conduct and document weekly hazardous waste container inspections; Failure to record elementary neutralization unit inspections on an inspection log Generator size: SQG Outcome: $1,028.00 fine
Click here for a printable list of these enforcement outcomes (PDF).
If you have any questions regarding compliance with environmental regulations or wish to report a violation, call 612-348-3777 and ask for the environmental specialist on call or email environment@hennepin.us.
The 2019 hazardous waste licensing process will be starting
soon. The hazardous waste portal administrator for each location that is
subject to annual licensing (generator size is LQG, SQG or VSQG), will be sent
email notification in early November, telling them that their 2019 management
plan summary (MPS) is now available for review and
revision. Operations that are currently licensed by Hennepin County
as Minimal Generators (MIG) are not subject to the annual license renewal
process.
The portal administrator must ensure that someone representing
the operation is reviewing all of the information on the electronic MPS form
and making adjustments that accurately reflect your waste management practices
and quantities generated during calendar year 2018. After all required fields
have been reviewed and updated, the portal administrator is responsible for
submitting the MPS on behalf of the operation, certifying that the information
has been reviewed and updated as necessary. The portal administrator will be
unable to submit the MPS if there are any required fields that have not been
updated.
The due date for completion of the 2019 MPS is December 15, 2018.
License fees for the 2019 license period will be calculated using the most
current information that has been reported and approved by Hennepin County
staff at the time of invoicing in February 2019.
Hennepin County has created an iCalendar feed to help you
remember all of the generator licensing deadlines, including due dates for
management plan summaries, license payments and printing/posting your new
generator license.
You can subscribe here if you have calendar software that
accepts the iCalendar format.
Use this link to access your calendar in any web browser.
Hazardous waste inspectors visit generators to determine
compliance with the hazardous waste regulations and laws defined in Minnesota
Rules chapter 7045, Minnesota statute, and Hennepin County Ordinance 7. Listed
below are some of the most common hazardous waste rule violations observed by
inspectors during compliance inspections along with some tips for how to avoid
those violations.
1. Waste Evaluation
Violation: Disposing of unevaluated or inadequately evaluated
products or materials used at your site as nonhazardous waste.
- Tip: Contaminants are generally introduced to products from the process where
they are being used. Remember, you can use generator knowledge to assume your
waste is hazardous, but you may need to test your waste for certain
characteristics or properties such as heavy metals, flashpoint, pH and VOCs, to
show it is nonhazardous.
2. Labeling
Violation:
Missing or smudged waste description.
- Tip: Hazardous waste containers must be labeled with the words “Hazardous
Waste,” a description of the waste and the accumulation start date.
3. Open Container
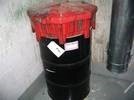 Violation: Though funnel is covered,
it is not designed with a closure device to withhold contents if overturned.
|
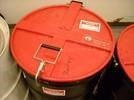 Correct: Container is closed and
has a closure device that is designed to withhold contents if container is overturned.
|
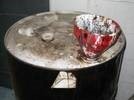 Violation: Open funnel. When
done adding waste to the drum, this funnel must be removed and bung screwed
shut.
|
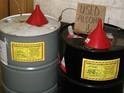 Correct: Plastic funnels are
removed from the container and the bungs (closure device) are secured.
|
4. Universal Waste Lamp Management
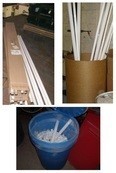 |
|
Violation: Lamps (intact or broken) are not stored
in appropriate containers. For more information on storing broken lamps and
avoiding breakage see page two of this document.
The
three photos to the left show different examples of lamp violations.
|
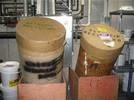 |
|
Correct: Used lamps are stored
in closed containers and in a manner to prevent breakage. Containers are
properly labeled “Universal Waste – Lamps” or “Used Lamps” or “Waste Lamps.”
Containers are the appropriate size. |
5. Record keeping
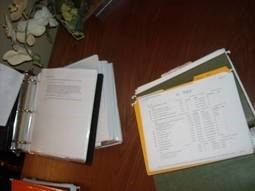 Violation: Evaluation records not kept at the licensed
site or made easily available for inspection.
Violation: Three years of disposal records were not
available, including facility-signed manifests for all hazardous waste
shipments, used lamp receipts, battery receipts, electronics receipts, etc.
Violation: Missing or incomplete SQG or LQG training
records for hazardous waste personnel.
- Tip: Keep
your hazardous waste records organized. If you have a lot of records, maintain
separate records for each year. Make sure back-up personnel know the location
and have access to the records.
|
This year’s MnTAP Intern Symposium, held August 16, featured 15 projects at companies around the state. The interns highlighted the opportunities they have identified for saving water, energy, and waste during their 3-month internships.
Click here to view the event program and here to view the list of projects.
Your business may be able to address waste reduction and energy efficiency projects sooner and faster with the help of a MnTAP intern. Learn more on the MnTAP website.
Industrial Energy, Water, and
Waste Reduction with a MnTAP Intern:
The Minnesota Technical
Assistance Program (MnTAP) at the University of Minnesota is now scoping
projects for the 2019 intern program. MnTAP places engineering students
on-site for three months over the summer that can help you to identify
opportunities, collect data, research strategies, and implement changes that
will result in energy efficiency, water conservation, waste reduction, and cost
savings. MnTAP is looking to partner with over 10 industrial businesses
throughout the state of Minnesota. Applications are accepted through
January, but priority is given to sites that apply early.
To get started, call or email
the MnTAP Intern Administrator Nathan Landwehr (landwehr@umn.edu, 612-624-4697). He
will schedule a project scoping site visit where we can discuss opportunities
and develop the intern project objectives.
The EPA has launched a national system for tracking hazardous
waste shipments electronically. This system, known as “e-Manifest,” has
modernized the nation’s cradle-to-grave hazardous waste tracking process while
saving valuable time, resources, and dollars for industry and states.
By enabling the transition
from a paper-intensive process to an electronic system, the EPA estimates
e-Manifest will ultimately reduce the burden associated with preparing shipping
manifests by between 300,000 and 700,000 hours, saving state and industry users
$75-$90M annually.
Follow this link to learn
more about e-manifests: https://www.epa.gov/e-manifest/learn-about-hazardous-waste-electronic-manifest-system-e-manifest
The Minnesota Pollution
Control Agency is updating their factsheet in 2018. Here is a link to the
current factsheet (PDF) https://www.pca.state.mn.us/sites/default/files/w-hw1-07.pdf
|