|
Miles City Short Stop Release Closed!
In October 2020, DEQ issued a No Further Corrective Action (NFCA) letter for Release #4800 at the Miles City Short Stop Convenience Store (Short Stop), bringing closure to one of the largest and most impactful petroleum release sites from a retail gas station ever reported in Montana.
The release was reported to DEQ in October 2010 following a complaint of petroleum vapors in an adjacent apartment building and was later confirmed when gasoline (free product) was observed in a groundwater monitoring well at the Short Stop. Following a failed tank tightness test, the owner/operator of the Short Stop removed the two existing underground storage tanks (USTs) and replaced them with new fiberglass reinforced plastic USTs. The petroleum release was attributed to a single perforation in the bottom of one of the USTs. Based on a review of the Short Stop’s UST inventory control records, an estimated 9,700 gallons of premium unleaded gasoline were released to the environment from July to October 2010.
DEQ initiated an emergency response based on the significant volume of gasoline impacting the groundwater, confirmed petroleum vapor intrusion (PVI) at the adjacent apartment building, and the potential threat of PVI at other nearby buildings including the United States Post Office. DEQ used Leaking Underground Storage Tank (LUST) Trust funds to contract an environmental consulting company to assist with emergency response activities, investigation, cleanup, and monitoring.
Vapor mitigation systems were installed at both the apartment building and the US Post Office using a combination of soil vapor extraction (SVE) and positive pressure to prevent vapors from entering the buildings. Vapor mitigation systems were also installed at two other nearby buildings in response to the PVI threat.
A groundwater monitoring well network was installed and approximately 8,532 gallons of gasoline were recovered from the subsurface using vacuum trucks from November 2010 through April 2011. SVE systems removed an additional 6,144 gallons of petroleum hydrocarbons from November 2010 through June 2014 bringing the combined total removed to an estimated 14,676 gallons.
In April 2013, Cool-Ox™, a chemical oxidant and oxygen release compound, was injected to further remediate residual petroleum hydrocarbons in soil and groundwater at the Short Stop and near the downgradient Post Office property.
The successful fuel recovery and remediation efforts resulted in a diminishing dissolved-phase petroleum hydrocarbon plume. DEQ discontinued PVI sampling in the US Post Office and the apartment building in early 2015 based on available data set indicated the buildings were no longer threatened by the release.
Monitored natural attenuation continued through 2019 when dissolved-phase petroleum hydrocarbon concentrations fell below DEQ risk-based screening levels (RBSLs). All groundwater and remediation wells have been properly abandoned and remediation equipment removed from the site.
|
A change of season is not the only change that UST owners and operators can expect this fall. As of October 13, 2021, Montana UST systems must implement new requirements based upon 2015 EPA regulatory changes. An important part of the new regulations is the addition of a monthly walkthrough inspection procedure. Walkthrough inspections should be used as a tool to help you:
-
understand your system better;
-
find problems before they develop into something that can threaten the system;
-
protect the environment; and
-
help you avoid large repair costs by finding problems early.
UST owners/operators must complete their first walkthrough before the October 13th deadline and this article will explore how to complete a walkthrough inspection. To complete the inspections, you will need to fill out Montana DEQ’s Walkthrough Inspection Form or PEI RP 900. These monthly walkthrough inspections can be completed by the facility Owner, Operator, Class A, B, or C operators, or a 3rd party contractor.
While these steps are listed in order, the inspection can be completed in any order. It is also important to note that while this is called a monthly walkthrough, they must be performed at least every 30 days. Here are the 6 steps:
The first step of the walkthrough inspection is to visually check the spill prevention equipment for damage. Whoever performs the inspection will also take this time to check for any liquid or debris that need to be removed to allow the spill bucket to perform optimally. Liquid and debris removed from a spill bucket need to be properly disposed of.
The second step is to check for, and remove, obstructions in the fill pipe. The fill pipe is where fuel enters the tank. Fill pipes have required overflow protection mechanisms in place, and obstructions can render these mechanisms useless. When dealing with thousands of gallons of gasoline and flammable vapors it is important that these overfill protection systems work properly.
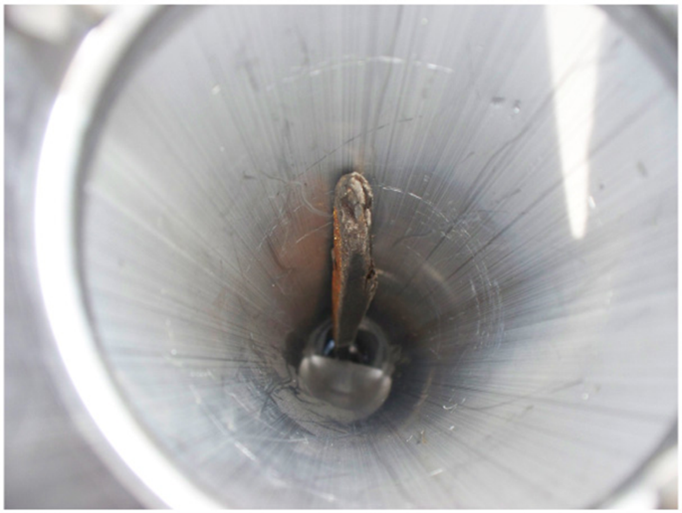 Figure 1: A gauge stick that has been placed into the fill pipe to obstruct the overflow protection device.
The third step is to check the fill cap to ensure that it is undamaged and fits tightly onto the fill pipe. The fill cap is responsible for ensuring that no outside product enters the tank. If the fill cap is not secure, outside sources such as water can threaten the integrity of the tank as well as damage the quality of the fuel in the tank.
The fourth step only applies to systems with double walled prevention equipment. For double walled spill buckets, you must check for leaks in the interstitial area. The interstitial area is the space between the inner wall and the outer wall of the spill bucket. If there are no present double walled spill buckets, then a simple “N/A” will suffice.
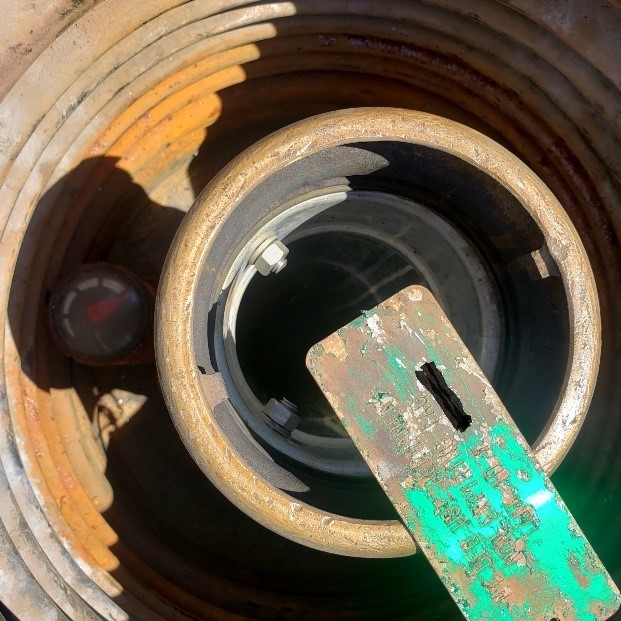 Figure 2. The gauge in the bottom of the sump on the left indicates an interstice that is full of water.
The fifth step is to check the release detection equipment to ensure that it is operating appropriately. This means that you must examine your automatic tank gauge for any alarms or messages. These gauges should be checked every day to ensure that the system is functioning properly, but these checks must be documented monthly as part of the inspection.
The sixth and final step is to ensure that the records of release detection testing are current and correct. This requires that records be reviewed to make sure that they are in order, passing, and documented correctly.
These six simple steps not only satisfy the requirements of the monthly walkthrough inspection, but help you keep a closer eye on your system. When doing walkthrough inspections make sure you make note of any problems that you find and get them fixed. Addressing these issues early will save money later down the road. Owners and operators who have been doing walkthrough inspections for a while have said that they can sleep better at night, and now have a better understanding of their system. So don’t just think of them as a requirement, but as something that helps you manage your system more efficiently while increasing safety and peace of mind.
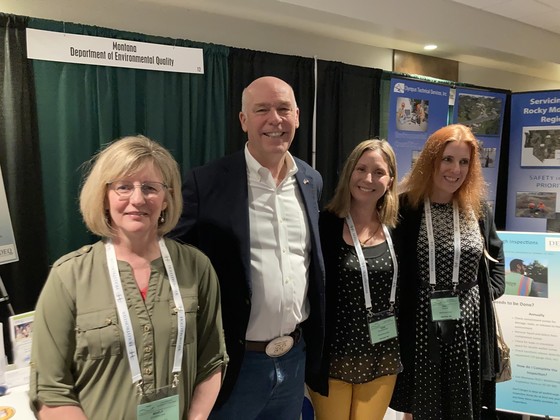 DEQ attended the Montana Petroleum Marketers & Convenience Store Association (MPMCSA) Convention in June. It was great to get out and see our stakeholders and we appreciate Governor Gianforte for saying hello.
|
|
Updates and Events
- MUST News is back! To sign up or cancel receiving the MUST News e-mail notification, or other DEQ notices, visit this website.
DEQ and PTRCB Staff Win EPA’s National Notable Achievement Award for Outstanding Cleanup/Revitalization Work
The team were recognized “for their exceptional commitment to collaboration and implementing creative strategies to reduce the time it takes to remediate LUST backlog sites in Montana, even during a global pandemic”, said Region 8 Land, Chemicals and Redevelopment Division Director Mark Smith. “Largely due to this effort, the backlog of LUST sites in Montana has decreased from over 1,000 open releases to approximately 682, a 32% reduction. This work directly protects human health and the environment by remediating releases from underground storage tanks.”
The awarded team includes Theresa Martella and Ben Bents from EPA Region 8, Amy Steinmetz, Jenny Chambers, Terri Mavencamp, Ed Thamke, Marla Stremcha, and Shannon Cala-Williams from DEQ, and Terry Wadsworth from the Montana Petroleum Tank Release Compensation (PTRC) Fund. The Montana LUST Team has been meeting monthly since 2015 to assess a LUST site backlog, identify common reasons for delays in remediation, create specific solutions to tackle those issues, and to put the strategies into action.
The Montana legislature responded by transferring $1 million to DEQ to address these sites. These funds have been used to remediate ineligible sites which would otherwise have continued to languish. The team will continue to work on updating of guidance documents, training materials, and holding educational events.
It was because of these ambitious, collaborative efforts, that Montana achieved 43 cleanups in FY2020, despite COVID-related challenges. These cleanups contributed significantly to Region 8 being the only EPA Region to achieve its LUST cleanup goals in FY2020.
Process Improvement Subgroup Update
The Montana Tanks Stakeholder Workgroup was formed in June 2020 to increase education, outreach, and communication among the three groups within or associated with the Montana Department of Environmental Quality (DEQ), the Underground Storage Tank (UST) Section, the Petroleum Tank Cleanup (PTC) Section, the Petroleum Tank Release Compensation Board (PTRCB), and external stakeholders such as petroleum marketers, petroleum facility owners/operators, and consulting companies. A Process Improvement Subgroup was organized to support the remediation and closure of leaking underground storage tank sites by improving processes used by owners, PTCS, PTRCB, and consultants.
The first project that the Process Improvement Subgroup tackled was to improve communication regarding groundwater monitoring. The Subgroup created a new PTRCB form that helps communicate to DEQ and PTRCB tasks associated with groundwater monitoring, work plan preparation, and reporting. The form provides a format where the expectations of each monitoring event, including wells to be sampled, the analytical suite, the depth to groundwater, etc., can be communicated. The form includes allowances for groundwater monitoring tasks that may contribute to additional time during sampling or reporting, such as the collection of intrinsic biodegradation indicators (IBI)or sampling from low-yield wells. The communication of tasks such as these will help refine the categorization of groundwater monitoring tasks and associated unit costs.
During development of the PTRCB form, it became apparent that updates were necessary to the guidance for groundwater monitoring work plans and reports. The updated Montana Groundwater Monitoring Work Plan and Report Guidance for Petroleum Releases consolidated previous abbreviated and standardized formats into one document. Additionally, the updated Guidance defined expectations for work plans, interim data submittals, reports, and the reporting of IBI data.
Use of these forms and guidance help DEQ receive the data necessary to evaluate the status of petroleum releases and progress the releases toward closures more efficiently, helps PTRCB properly categorize tasks associated with groundwater monitoring, and helps consultants understand expectations, reduce errors in project submittals, and receive reimbursement for identified tasks.
A similar approach is underway to improve communication with tasks associated with the remedial investigation of petroleum releases and cleanup of Petroleum Releases. Updates will be forthcoming as the Subgroup progresses in the development of these communication tools.
The Montana Groundwater Monitoring Work Plan and Report Guidance for Petroleum Releases can be found under “Guidance” at: https://deq.mt.gov/cleanupandrec/Programs/petrocleanup
The PTRCB Groundwater Monitoring and Sampling Unit Cost Worksheet can be found “Forms and Worksheets” at: https://deq.mt.gov/cleanupandrec/Programs/ptrcb
Does DEQ Know How to Reach You?
Over the last several years, DEQ has made attempts to reach owner/operators and responsible parties of petroleum storage tanks to address historical petroleum contamination. Contact information for these historical releases may need updating. It is the hope of the Petroleum Tank Cleanup Section (PTCS) to update its contact information so that when DEQ is provided with special funding for cleanup, it can reach out to the current property owner, owner/operator, and/or responsible party that may be eligible for this funding.
So how do you find out if your property has a petroleum release? There was a presentation on how to navigate to the petroleum release mapper as part of the 2021 Consultants Meeting where you can determine if your property has a known petroleum release. You can also find a list of all petroleum release locations in Montana at: https://deq.mt.gov/cleanupandrec/Programs/petrocleanup.
If you find that you have a release that is regulated by the PTCS, contact Deb Sutliff at dsutliff@mt.gov and provide her with the following information:
-
Contact Person:
-
Contact Phone Number:
-
Mailing Address:
-
E-mail Address:
-
Facility ID and/or Release Number:
|
|
|
|
|