Volume 33, Issue 2, Spring 2025
MIOSHA will soon bid farewell to Construction Safety and Health Division Director Lawrence Hidalgo, Jr., who will retire on March 29, after 10 years of dedicated service. Lawrence’s leadership and commitment to worker safety have left a lasting impact on MIOSHA and the lives of Michigan workers.
Lawrence’s career began in the skilled trades as an electrician before he moved to Michigan in 1986. His passion for education led him to become the Director of the Electrician Training Program at Lansing Community College, all while attending Cooley Law School.
Among his many achievements, Lawrence played a key role in developing MIOSHA’s Operational Excellence Scorecards, an initiative that improved performance tracking and efficiency across the agency.
|
His dedication to workforce development extended beyond MIOSHA, serving as a commissioner on former Lt. Gov. John Cherry’s Commission on Higher Education and as a Lansing Community College trustee from 2013 to 2024, including multiple terms as chairman.
A licensed attorney, Lawrence practiced estate planning and bankruptcy law before joining MIOSHA in 2015. In retirement, he plans to use his legal expertise as a pro bono immigration lawyer. A father of three and grandfather of seven, he looks forward to spending more time with family while continuing to serve his community.
Reflecting on his career, Lawrence shared, “I loved every job I’ve done.” His passion, leadership and dedication to worker safety will be deeply missed, and we thank him for his service.
On behalf of MIOSHA, I extend our deepest gratitude to Lawrence and wish him the best in retirement.
|
Nikilia “Nikki” Clark, Safety and Health Manager, Construction Safety and Health Division
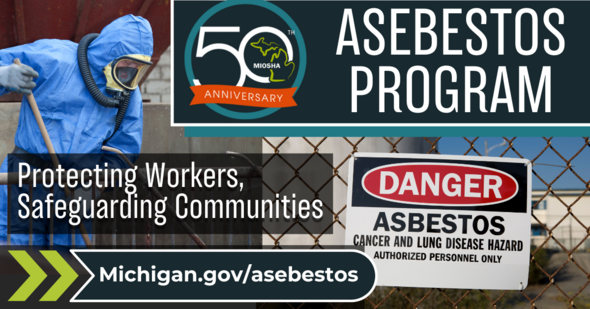 A new law aimed at enhancing workplace safety and health protections for Michigan workers will take effect April 1. House Bill 4185 (PA 17 of 2024) amends the Michigan Occupational Safety and Health Act of 1974 by adding asbestos-specific language to better regulate asbestos handling and exposure.
MIOSHA will apply the updated law to all friable and non-friable asbestos-related citations, reinforcing safety measures across industries.
The law introduces clear definitions for asbestos and asbestos-related violations in Sec. 4(2) and Sec. 4(3):
- Asbestos is defined as a group of naturally occurring minerals that separate into fibers, including chrysotile, amosite, crocidolite, anthophyllite, tremolite, and actinolite.
- An asbestos-related violation includes any violation of the act, an order issued under the act, or a MIOSHA rule or standard promulgated under the act, that involves demolition, renovation, encapsulation, removal, or handling of friable asbestos—or any situation that exposes an individual to friable asbestos.
Case Closing and Repeat Violation Timeframe
The law updates how and when an asbestos-related case is considered closed, outlined in Sec. 35(4)(a). A case is officially closed when:
- The citation becomes a final order.
- Satisfactory abatement documentation is received by the board.
- All civil penalties are paid on time, or MIOSHA complies with Sec. 36(6).
It also extends the repeat violation timeframe for asbestos-related violations. Under Sec. 35(4)(b), an employer will now be considered a repeat violator if another asbestos-related violation occurs within five years of the previous case closing date of an asbestos-related violation. Currently, MIOSHA's Construction Safety and Health Division (CSHD) considers a three-year timeframe for repeat violations.
Another major change is the limitation on penalty reductions for asbestos-related violations, detailed in Sec. 36(1). Starting April 1, 2025, asbestos-related citations will no longer qualify for Penalty Reduction Agreements (PRA), and the minimum serious penalty will be $400.
The law also caps penalty reductions at 95%, with specific percentage limits based on:
-
Size of the business – up to 70% reduction
-
Good-faith efforts of the employer – up to 25% reduction
-
History of previous citations – up to 10% reduction
MIOSHA will use penalty calculation worksheets to ensure compliance with these new provisions. These worksheets apply to citations issued under:
At the MIOSHA Construction Safety and Health Division Director or manager’s discretion, a deterrent effect may be imposed on asbestos licensing violations.
MIOSHA Asbestos Program
Since 1986, the MIOSHA Construction Safety and Health Division's Asbestos Program has worked to ensure that asbestos abatement activities are conducted safely, protecting both workers and the public. Since its inception, the program processed over 5,900 asbestos management plans. In 2024, the program approved 179 asbestos training courses and conducted 206 compliance investigations, reinforcing Michigan’s commitment to asbestos safety.
For more information on asbestos safety training, licensing and compliance, visit Michigan.gov/asebstos.
Lillian Brezzell, Industrial Hygienist, General Industry Safety and Health Division
On Nov. 15, 2023, MIOSHA initiated an inspection at an automotive parts manufacturing facility following the death of a 60-year-old maintenance worker from complications of Legionnaires' disease. The inspection resulted in a citation for the employer's failure to maintaining its water system free of high concentrations of Legionella bacteria.
Background
More than three months earlier, on Friday, Aug. 11, the maintenance worker called in sick. By Sunday, Aug. 13, the worker’s condition had worsened, leading to hospitalization and eventual transfer to a specialized care facility. On Sunday, Aug. 20, the employee died from the illness. The employer did not learn that the worker had died from complications of Legionnaires' disease until the day of the funeral.
According to the employer, the maintenance worker had no open maintenance tickets or special work assignments. As a result, the employer had little knowledge of the employee's job tasks in the days leading up to the illness. When the employee was off work, there was no immediate reason to suspect their illness was connected to workplace exposure, the employer stated.
Several weeks later, on Sept. 28, a machine operator from the same facility called in sick and was hospitalized. The employer stated they began to fear a potential Legionella outbreak when they learned about the machine operator's hospitalization for Legionnaires' disease. The employee was admitted to the ICU, where they remained for 18 days in critical condition, suffered a heart attack and required ventilation while unconscious for several days. MIOSHA subsequently opened a separate inspection to address the employer’s failure to report the employee’s hospitalization.
History of Legionella
Information provided by the local county health department revealed in September 2020, the employer had two workers hospitalized due to complications from Legionnaires’ disease. In October 2020, the Michigan Department of Health and Human Services (MDHHS) investigated the facility for possible Legionella contamination. Health officials collected 15 water samples, one of which tested positive for Legionella. As a result, the employer implemented corrective actions, including:
- Setting hot water tanks to 120°F.
- Establishing a cleaning schedule for the ice machine.
- Disinfecting and enclosing the air compressor's condensate water barrel.
- Developing a biweekly cleaning schedule for welding barrels.
MIOSHA Inspection and Findings
Legionella bacteria thrive in stagnant water sources at temperatures between 68°F and 110°F, typically spreading through aerosols or mist. MIOSHA's inspection focused on identifying potential water sources and job tasks that could generate exposure.
MIOSHA's inspection noted that the facility lacked air conditioning and cooling towers—common sources of Legionella contamination—suggesting the bacteria likely originated from other water systems within the plant. The facility primarily used municipal water for operations, except for a brazing furnace.
During the walk-around, MIOSHA identified several potential sources of exposure, including uncovered water barrels used by spot welders, two stagnant-water parts washing tanks (maintained at 150°F), handwashing stations and an ice machine. The wastewater tanks, which reached temperatures of 200°F, and the facility’s water system condenser were also inspected.
Further investigation revealed a third employee was also diagnosed with Legionnaires’ disease. The employee suffered from a respiratory illness for over three months but was never hospitalized. The employee believed their illness was the result of a reoccurring sinus infection that was unresponsive to antibiotics. The employee got tested for Legionella after learning of the contamination within the facility.
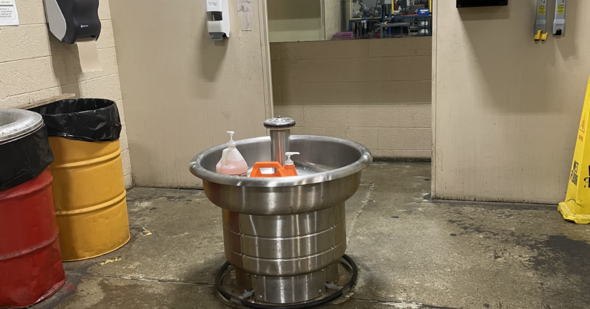 A handwasher station was one of four locations where Legionella was detected.
Water Testing and Results
MIOSHA tested water from 19 locations in the facility, including parts washers, handwashing stations and drinking fountains. Legionella pneumophila serogroup 1 was found in four samples: the women's bathroom sink, a handwashing station, a parts washer and the men's urinal. This strain matched the clinical sample from the deceased employee, as confirmed by MDHHS.
Citations and Penalties
On July 2, 2024, MIOSHA issued one serious and three other-than-serious citations related to the death of the maintenance worker and the two additional employees who contracted Legionnaires’ disease at work. Some citations were grouped into single citations with a combined penalty.
MIOSHA Administrative Standard Part 11, Recording and Reporting of Occupational Injuries and Illnesses
- Rule 408.22129(4): The employer failed to record a work-related injury or illness on the MIOSHA 300 log within 7 calendar days of receiving information that the injury or illness occurred. $900
- Rule 408.22139(2): The employer failed to report the hospitalization of an employee to MIOSHA within 24 hours of learning of the employee's inpatient hospitalization.
- Rule 408.22139(11): The employer failed to report a work-related fatality of an employee to MIOSHA once learning of the employee's death. $900.00
Act 154, Michigan Occupational Safety and Health Act, Act 154 of 1974
- Section 11(a): Employees were exposed to Legionella bacteria from water sources inside the facility. A maintenance worker died after contracting Legionnaires' disease, a second employee was hospitalized for an extended period of time with Legionnaires' disease, and a third employee was ill for several weeks after developing Legionnaires' disease. Penalty: $6,300
Total Proposed Penalties – $8,100
The employer appealed the citation and reached a settlement agreement, agreeing to ensure corrective actions were taken. The employer received a penalty reduction and paid $7,750 in penalties. The case was closed on Aug. 23, 2024.
By Dequetta McDonald-Bey & Ayla Desjarlais, Cintas Service Managers, First Aid and Safety Division, Romulus
 Cintas Health and Safety Vision
- Every Cintas location is free from injury, illness, collision, and fire.
- Every partner is engaged in continuously improving health and safety
- Cintas is widely recognized as one of the world’s leaders in health and safety performance
Cintas is the largest mobile-delivery first aid supplier in North America, with more than 500,000 first aid cabinets in circulation. Our AEDs, eye wash, training & compliance courses, PPE and first aid supplies help workers across North America stay safe on the job. Our facility in Romulus has 50 employee-partners with a proven track record of safety excellence, driven by continuous engagement. In recognition of this commitment, Cintas Romulus achieved MVPP Rising Star certification in June 2024.
At Cintas, we ensure safety is at the forefront of our partners daily routines by providing weekly, monthly and yearly safety initiatives. Below are some of our most effective safety best practices that help create a world class safety culture.
Our weekly location meetings focus on critical safety topics, including:
- Upcoming severe weather alerts
- Reported near misses and unsafe acts from other Cintas locations
- Group discussions on best practices and safety solutions
Each meeting ends with a Stretch & Flex session, which is a group stretch that helps avoid strains and avoidable injuries while on the job.
Each of our partners participates in the Cintas Safety Lead Program, which requires them to submit at least two near-miss reports or best practices per month. These leads are submitted via QR code and provide visibility into unsafe situations, allowing our team to address hazards proactively. In addition to our Safety Lead program, all Cintas locations use an electronic scorecard to track monthly and quarterly compliance action items, such as: van inspections, fire extinguisher inspections, housekeeping checklist, first aid, AED, eyewash inspections and record keeping compliance.
A Cintas van participates in a safe van drill during 45P Cintas First Aid & Safety's 2024 Annual Safety Day.
Annual Safety Day
Finally, we hold an annual Safety Day where we get together as a location to cover key safety trainings as well as perform hands-on evaluations on Bloodborne Pathogens (BBP), SMITH driving drills, power and installation tools, field safety, industrial athlete training, hazard communication and ladder safety. Locally we pair this with a spirit day celebration where we enjoy grilling out or a food truck. Its a great opportunity to spend time together as a location and celebrate our safety wins for the year, as well as cover hands on training!
Join the Ranks of Michigan’s MVPP STAR Sites!
MIOSHA established the MVPP program in 1996 to recognize employers with exemplary safety and health management systems that go above MIOSHA requirements. The MVPP program is open to all qualifying Michigan employers with injury and illness incident rates below the industry average for the past three years.
To earn MVPP Star status, companies undergo a rigorous application process, including a comprehensive safety and health program review, site visits, and employee interviews to verify that the workplace meets and exceeds MIOSHA’s strict safety and health criteria.
Learn more about becoming an MVPP Star site at Michigan.gov/MVPP.
MIOSHA Forms New Alliance with Incompass Michigan to Promote Safer Workplaces
By Mike Krafcik, MIOSHA Communications Specialist
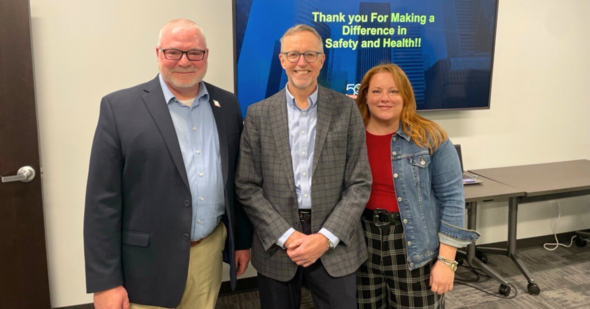 Left to right: MIOSHA Director Bart Pickelman, Incompass Michigan President and CEO Todd Culver and MIOSHA CET Division Director Tarah Kile at the MIOSHA Alliance signing on March 24, 2025
MIOSHA has signed a new five-year Alliance Agreement with Incompass Michigan, a statewide network of mission-driven human service providers dedicated to advancing community access and inclusion for all.
This marks MIOSHA’s 23rd active alliance as part of its ongoing effort to build collaborative relationships that strengthen workplace safety and health across Michigan.
Through the alliance, Incompass Michigan will work alongside MIOSHA to raise awareness about key safety and health topics affecting its member organizations and the individuals they serve. The group will share information about OSHA and MIOSHA emphasis programs, promote upcoming training opportunities and support outreach on workplace hazard prevention—particularly related to ergonomics, slips, trips and falls.
The agreement also supports collaboration on initiatives that address injuries experienced by individuals with disabilities in workplace settings. MIOSHA will contribute through regular participation in Incompass Michigan’s annual conference and member webinars, and by offering consultation and training services through its CET Division.
“This alliance reflects our shared commitment to building safer, healthier workplaces for all,” said MIOSHA Director Bart Pickelman. “We’re proud to partner with Incompass Michigan and support the important work their members are doing in communities across the state.”
“Incompass Michigan members provide essential services that often involve physical demands and unique safety challenges,” said Todd Culver, President and CEO of Incompass Michigan. “This partnership with MIOSHA ensures our members have access to valuable safety training, resources and expertise that help keep their teams and clients safe.”
MIOSHA’s Alliance Program is open to trade and professional organizations, government agencies, businesses, labor groups, and schools. With a written agreement in place, partners formalize their collaboration with MIOSHA to promote education, training and awareness surrounding workplace safety and health.
To learn more about the MIOSHA Alliance Program, visit Michigan.gov/Alliance.
Quick Links
Agency/Division Instructions/Memorandums Air Contaminants Initiative Asbestos Program CET Request for Consultative Assistance Services (RCA) CET Training Calendar Construction Safety and Health Division (CSHD) DVD/Video Library Service Employee Safety, Health, and Discrimination Complaint Forms Fall Prevention Campaign (STOP FALLS. SAVE LIVES.) General Industry Safety and Health Division (GISHD) Hazard Communication/GHS Laboratory and Equipment Services Michigan Alliances Michigan Safety and Health Achievement Recognition Program (MSHARP) Michigan Voluntary Protection Program (MVPP) MIOSHA FOIA Request MIOSHA News MIOSHA Publications MIOSHA Recordkeeping MIOSHA Standards MIOSHA Training Institute (MTI) MIOSHA Updates MIOSHA Variances Radiation Safety Section Residential Construction Strategic Plan and Initiatives Telephone, Mailing and Email Addresses
|