By Augustine Syrovy, Program Manager, MIOSHA Consultation Education and Training Division
Portable fire extinguishers are one of the most common pieces of safety equipment found in all industries. Designed to put out small fires before they develop into larger, more hazardous ones, portable fire extinguishers are easy-to-use and highly effective. However, despite their prevalence, some essential requirements are often overlooked.
Employers rightfully prioritize the inspection, maintenance and testing of portable fire extinguishers, but may fail to educate employees on their proper use and the risks of fighting fires.
Employee Training Requirements
If an employer provides portable fire extinguishers for employees to use, they must also provide training that covers:
- The general principals of using a fire extinguisher.
- The hazards involved with early-stage firefighting.
This training must be given when an employee starts working and at least once a year after that.
What the Training Should Cover
The training doesn’t have to be in a classroom and can be provided by the employer. Employees can learn by:
- Reviewing instructions on the fire extinguisher label and manual.
- Conducting a safety walkthrough to identify fire hazards in the workplace.
Employees should also learn to recognize the common risks when a fire is too big to handle with an extinguisher. As a fire grows, it can create dangerous conditions, such as:
-
Thick smoke that makes it hard to breathe.
-
Extreme heat that can cause burns.
-
Low visibility that makes it difficult to find an exit.
-
Blocked escape routes that could trap employees inside.
Knowing when to evacuate instead of trying to fight a fire is critical for workplace safety.
For more details on portable fire extinguisher requirements, review our General Industry Standard Part 8, Portable Fire Extinguishers at Michigan.gov/mioshastandards.
|
 |
A reminder that MIOSHA’s Administrative Standard Part 11, Recording And Reporting of Occupational Injuries And Illnesses requires most employers of two key annual requirements:
-
Electronically Submit Form 300A Data: Most employers must submit their previous year’s MIOSHA Form 300A (or OSHA Form 300A) Summary of Work-Related Injuries and Illnesses to Federal OSHA using OSHA’s Injury Tracking Application (ITA) by March 2, 2025.
-
Post Form 300A in the Workplace: Employers are also required to prominently display the Form 300A at their workplace, providing a summary of work-related injury and illness data, from Feb. 1 to April 30.
Who Is Required to Report?
-
Employers with 100 or More Employees in High-Hazard Industries: Must electronically submit OSHA Form 300 (Log of Work-Related Injuries and Illnesses) and Form 301 (Injury and Illness Incident Report).
-
Employers with 20 to 249 Employees in High-Hazard Industries: Must submit OSHA Form 300A (Summary of Work-Related Injuries and Illnesses).
-
Employers with 250 or More Employees: Must submit Form 300A if routinely required to keep OSHA records.
Exempt Employers
Employers with 10 or fewer employees at all times during the previous calendar year are exempt from routinely keeping OSHA injury and illness records. Additionally, establishments classified in certain low-hazard industries are exempt unless specifically requested in writing by OSHA.
For a full list of industries exempt from recordkeeping, see Part 11, Appendix A (Page 24).
For additional details, visit OSHA's Recordkeeping Requirements page at osha.gov/recordkeeping.
By Brian Paul, MIOSHA Construction Safety Supervisor
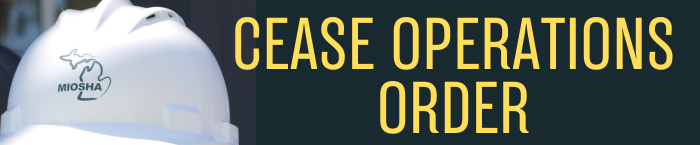 MIOSHA has the authority to take action when employers fail to correct cited safety violations. One enforcement tool is a cease operation order, which can be issued in lieu of a notice of failure to abate when an employer does not address workplace hazards within the required timeframe. If an employer does not comply, MIOSHA refers the case to the Attorney General’s Office, which can initiate legal proceedings in circuit court.
Under Section 45 of the Michigan Occupational Safety and Health Act (MCL 408.1001 et seq.), “If an employer fails to comply with a final order of the board, the department may issue an order directing the employer to cease operating or render inoperable, in accordance with the order of the department, as is necessary to eliminate the hazard which is the subject of the order. When a cease operation order is not appropriate or not obeyed, the department shall refer the matter to the department attorney who shall promptly institute proceedings in the circuit court for the county in which the violation exists to enforce the department's orders.”
What Happens During Issuance of Cease Operation Order?
When MIOSHA issues a cease operations order, tags are placed throughout the jobsite, including on buildings, equipment and staging areas where that employer is performing work. The affected employer must stop all work until the cited violations are corrected and MIOSHA verifies abatement. Typically, no work can resume on the jobsite, even unrelated tasks, until the order is lifted.
A company representative must sign the cease operations order, acknowledging receipt and the required corrective actions. After the order is in place, MIOSHA representatives then monitor the jobsite daily to ensure compliance. If the contractor disregards the order, MIOSHA escalates the case to the Attorney General’s Office which would initiate proceedings in the circuit court to enforce the order.
2024 Cease Operation Orders
In 2024, MIOSHA’s Construction Safety and Health Division (CSHD) issued a total of two cease operation orders to an employer that failed to provide abatement to correct multiple alleged safety violations.
-
First Cease Operation Order: On April 23, 2024, a cease operation order was issued for failure to abate multiple citations issued on March 5, 2021. The employer failed to correct the following alleged citations:
-
Construction Standard Part 45, Fall Protection
-
Citation 1, Item 1a. 1926.501(b)(11): Each employee on a steep roof with unprotected sides and edges 6 feet (1.8 m) or more above lower levels shall be protected from falling by guardrail systems with toeboards, safety net systems or personal fall arrest systems.
-
Citation 1, Item 1b. 1926.503(a)(1): The employer shall provide a training program for each employee who might be exposed to fall hazards. The program shall enable each employee to recognize the hazards of falling and shall train each employee in the procedures to be followed to minimize these hazards.
-
Construction Standard Part 11, Fixed and Portable Ladders
-
Citation 1, Item 1c. 408.41126(2): Unless the stepladder is equipped with a handrail, the top step and cap shall not be used to stand on.
-
Construction Standard Part 1, General Rule
-
Citation 2, Item 1.408.40114(1): An employer shall develop, maintain, and coordinate with employees an accident prevention program, a copy of which shall be available at the worksite.
-
Construction Standard Part 21, Guarding of Walking and Working Areas
-
Citation 2, Item 2. 408.42159(2): A floor, platform, stair, runway, or ramp shall be free of hazardous projections.
This cease operations order was lifted after the general contractor hired another contractor to replace the contractor.
-
Second Cease Operation Order: On Nov.15, 2024, failure to abate citations were issued for failure to abate citations issued on Sept. 4, 2024. This order was issued for the employer’s failure to correct the following alleged citations:
-
Construction Standard Part 10, Cranes and Derricks
-
Citation 1, Item 2a. 1926.1427(c): The employer must ensure that each operator is certified or licensed to operate the equipment.
-
Citation 1, Item 2b. 1926.1427(f): Through an evaluation, the employer must ensure that each operator is qualified by a demonstration of:
- (i) The skills and knowledge, as well as the ability to recognize and avert risk, necessary to operate the equipment safely, including those specific to the safety devices, operational aids, software and the size and configuration of the equipment. Size and configuration includes, but is not limited to, lifting capacity, boom length, attachments, luffing jib and counterweight set-up.
- (ii) The ability to perform the hoisting activities required for assigned work, including, if applicable, blind lifts, personnel hoisting and multi-crane lifts.
The second cease operations order was eventually lifted after abatement was completed.
 Join the Western Michigan Industrial Hygiene Society (WMIHS) for an engaging virtual conference on February 13, exploring the latest industrial hygiene challenges in emerging industries. This all-day event will feature expert presentations on cannabis, distilleries and breweries, highlighting key safety and health concerns for professionals working in or regulating these industries.
📅 Date: Thursday, Feb. 13, 2025 🖥️ Format: Virtual Zoom Meeting (9 a.m. – 5 p.m.) 💰 Cost:
- Members of WMASSP/WMIHS/MIHS: $30 per person
- Non-members: $40 per person
- Students: Free
Featured Presentations
9-10:15 a.m. | Sip on Safety: The Bourbon Industry from a Safety Professional
Pat Hart, Campari America, Wild Turkey Distillery This presentation will delve into the unique challenges faced within the rapidly growing bourbon industry. Key topics will include the specific safety concerns related to handling barrels, an industry-specific approach to managing safety and health risks, and a brief overview of the science behind bourbon production.
10:30–11:45 a.m. | Yeast Flatulence or Eructation (CO2): What are the Effects and How to Control It and Other IH Concerns in Breweries
Dave Huizen, Ph.D., CIH – Occupational Health and Safety Associate Professor, GVSU Brewing and fermentation operations use yeast to convert sugars into CO2 and ethanol. An industrial hygiene concern in breweries is exposure to CO2. Low levels of CO2 exposure can cause cognitive effects and increased fatigue due to physical demands combined with CO2 exposure. Additional industrial hygiene concerns are associated with cleaning and sanitizing chemicals and grain dust exposures.
🥪 11:45 a.m. to 12:30 p.m. | LUNCH BREAK
12:30-2:00 p.m. | Marijuana Impairment at Work
William J. Judge, JD, LL.M., Drug Screening Compliance Institute This session will provide an overview of the current legal landscape—38 states allow medical marijuana use, and 24 states permit adult recreational use. State laws vary significantly, with some prohibiting employer discrimination for off-duty use, while others limit action to workplace impairment. What does Michigan law provide? How should employers navigate these challenges? This session will explore the answers.
2:15-3:30 p.m. | Work-Related Asthma in the Cannabis Industry
Kenneth Rosenman, MD, Professor of Medicine and Chief, Division of Occupational and Environmental Medicine, MSU Dr. Rosenman will discuss lung conditions, including an asthma-related fatality, that have occurred due to worker exposures in the cannabis industry.
3:45-5 p.m. | MIOSHA State Emphasis Program – Cannabis
Jamie Green, CSP, MIOSHA This session will cover MIOSHA requirements and applicable standards — including agriculture, general industry and construction — specific to the cannabis industry.
Register Today!
🔗 Register and pay by credit card at wmihs.org by Wednesday, Feb. 12. Upon payment, the Zoom meeting link will be provided on the confirmation page and in your email receipt.
For registration issues, contact bwisniewski@myairlife.com.
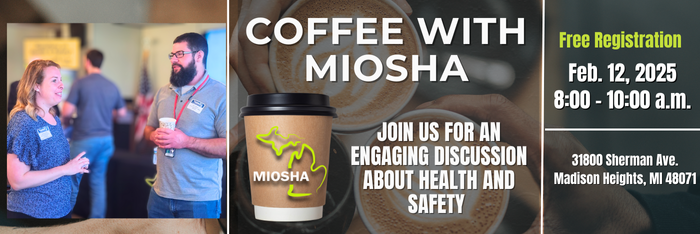 MIOSHA and the Associated Builders and Contractors (ABC) of Southeastern Michigan invite Michigan employers and employees to join us for an informal networking event focused on workplace safety and health.
Coffee with MIOSHA events are designed for safety professionals, offering a unique opportunity to:
- Network with MIOSHA administrative, enforcement, and consultative staff.
- Ask questions and discuss workplace safety challenges.
- Learn about MIOSHA’s programs and services to enhance safety and health.
Event Details:
-
When: Feb. 12, 2025, 8 – 10:30 a.m.
-
Where: 31800 Sherman Ave., Madison Heights, MI 48071
RSVP Now or scan the QR code below to register:
There have been two work-related fatalities reported to MIOSHA in 2025. The information below shares preliminary details about the fatalities reported to MIOSHA, which is believed to be covered by the MIOSH Act. The description reflects information provided to MIOSHA at the initial report of the incidents and are not the result of any official MIOSHA investigation.
Preliminary summaries of the 2025 incidents:
Two cement finishers were grinding and polishing a concrete floor in a customer's pole barn. When the employer had not heard from them by 8:30 p.m., he contacted the homeowner, who found both employees unconscious. The 43-year-old victim was pronounced deceased at the scene, while the second employee was hospitalized in critical condition. The employees had used propane-powered equipment in the enclosed barn without ventilation.
A 42-year-old laborer was pulling a trailer with a side-by-side utility task vehicle (UTV) when the trailer came off the hitch. The trailer’s tongue went underneath the truck causing it to collide with a stationary metal pole. The pole penetrated the cab of the truck fatally injuring the victim.
Dec. 30, 2024 – Reinspection Assignments Jan. 9, 2025 – Cannabis - State Emphasis Program (SEP) Jan. 10, 2025 – Hazard Communication Standards - Inspection Procedures Jan. 13, 2025 – Indian Country Inspections/Investigations and Interventions Jan. 22, 2025 – Reporting of Known or Suspected Occupational Diseases
Variances from MIOSHA standards must be made available to the public in accordance with Part 12, Variances (R408.22201 to 408.22251). MIOSHA variances are published online at: Michigan.gov/mioshavariances.
Quick Links
Agency/Division Instructions/Memorandums Air Contaminants Initiative Asbestos Program CET Request for Consultative Assistance Services (RCA) CET Training Calendar Construction Safety and Health Division (CSHD) DVD/Video Library Service Employee Safety, Health, and Discrimination Complaint Forms Fall Prevention Campaign (STOP FALLS. SAVE LIVES.) General Industry Safety and Health Division (GISHD) Hazard Communication/GHS Laboratory and Equipment Services Michigan Alliances Michigan Safety and Health Achievement Recognition Program (MSHARP) Michigan Voluntary Protection Program (MVPP) MIOSHA FOIA Request MIOSHA News MIOSHA Publications MIOSHA Recordkeeping MIOSHA Standards MIOSHA Take A Stand Day MIOSHA Training Institute (MTI) MIOSHA Updates MIOSHA Variances Radiation Safety Section Residential Construction Strategic Plan and Initiatives Telephone, Mailing and Email Addresses
|