Volume 33, Issue 1, Winter 2025
This year Michigan Occupational Safety and Health Administration (MIOSHA) is celebrating a major milestone: 50 years of protecting the health and safety of Michigan’s workforce. Since 1975, MIOSHA has been committed to creating safer and healthier workplaces for employees statewide. As we reflect on this journey, we also look forward, reaffirming our commitment to continuous improvement and advancing our motto of "Educate Before We Regulate."
Milestones of Impact
Over the past five decades, MIOSHA has achieved significant milestones that have shaped our approach to workplace safety and health. Here are just a few highlights:
-
Reducing Injury and Illness Rates: Michigan’s injury and illness rate has significantly improved —from 8.8 per 100 workers in 1977, peaking at 11.5 in 1994, to a record low of 2.8 in 2023.The progress reflects the impact of MIOSHA’s consultation, education and enforcement efforts, along with all of the efforts from employers and employees to make workplace safety and health a priority.
-
MIOSHA Asbestos Program 1986: Groundbreaking legislation in 1986 and 1988 set the standard for handling asbestos hazards, safeguarding workers and the public alike from the dangers of asbestos exposure. Learn more at Michigan.gov/mioshaconstruction.
-
Michigan Voluntary Protection Program (MVPP) 1998: The launch of the MVPP Program marked a new chapter in workplace safety, recognizing employers who go above and beyond in implementing exemplary safety and health management systems. Learn more at Michigan.gov/MVPP.
-
MIOSHA Training Institute (MTI) 2009: More than 33,845 attendees have benefited from practical, hands-on workplace safety and health training through MTI, an innovative and collaborative program that provides affordable occupational safety and health training to employees and employers across the state. Learn more at Michigan.gov/mti.
Looking Ahead
As we celebrate these achievements, we remain focused on the future. MIOSHA will continue to innovate, collaborate and adapt to the evolving needs of Michigan’s workforce. Together, with our partners in labor, business, and education, we can build on this legacy and ensure Michigan remains a leader in workplace safety and health.
Thank you for being a part of MIOSHA’s journey. Here’s to another 50 years of progress, partnership, and protection.
|
 |
By Nikki Clark, Safety and Health Manager, Construction Safety and Health Division
An underground utility and road-building contractor was cited by MIOSHA following a workplace accident that left an employee with a severe arm injury. The incident occurred on May 29, 2024, at a highway construction site where the worker was operating a handheld cut-off saw to cut a concrete storm drainpipe.
According to a report submitted by the employer, the employee sustained a deep cut to the upper arm and was taken to the hospital for treatment and surgery. The Construction Safety and Health Division (CSHD) launched a referral inspection the following day to investigate the circumstances surrounding the injury.
Inspection and Findings
On May 30, 2024, a Compliance Safety and Health Officer (CSHO) initiated a referral inspection. During the initial visit, the CSHO collected administrative records, took photographs, conducted private employee interviews and inspected the handheld saw involved. While the saw blade had been removed, the CSHO recorded its identification number for further investigation.
Additional interviews conducted on May 31, 2024, revealed the following:
The injured employee had been employed for about a year and was primarily a road grade checker but occasionally assisted the pipe crew.
- The foreman reported that the employee had been trained to use the saw but was unaware why the blade “kicked back” during the incident, stating that blade pinching typically caused the blade to stop, not kick back.
- The tail Man, responsible for pipe installation, stated that the pipe cracked because the ground was uneven. This crack caused the blade to pinch, leading to the kickback.
On June 3, 2024, the CSHO contacted the saw blade supplier and learned the following:
- The blade used was designed for cutting fresh (green) concrete and intended for walk-behind saws, not handheld saws.
- The blade was not suitable for cutting cured concrete, such as the storm sewer pipe involved in the incident.
On June 17, 2024, the injured employee confirmed they had not been trained on the differences between blades for cutting various types of concrete, despite receiving general saw training upon hire.
|
 The handheld saw involved in the incident, equipped with a blade designed for cutting green concrete, which was improperly used on cured concrete.
Citations and Penalties
On July 12, 2024, MIOSHA issued one serious citation under Construction Standard Part 1, General Rules.
- 408.40114(2)(a). Accident prevention plan does not provide instruction for the work activity being performed. Worker cutting a cured concrete pipe with a gas-powered saw equipped with a blade designed to cut green concrete - $3,500
Total Proposed Penalties – $3,500
The employer appealed the citation and reached a settlement agreement, agreeing to ensure corrective actions were taken. The employer received a 50% penalty reduction and paid $1750 in penalties.
Naomi Starks, Industrial Hygienist, General Industry Safety and Health Division
MIOSHA's General Industry Safety and Health Division conducted a health inspection of a zinc-alloy foundry and identified numerous health hazards leading to violations.
In April 2022, MIOSHA initiated the inspection of the establishment after receiving an employee complaint about toxic fumes and inadequate personal protective equipment (PPE). The foundry, which produces zinc alloys for die casting, plating, and galvanizing, involves operations such as melting, pouring, molding, packaging, warehousing, and storage.
During the inspection, personal air monitoring found elevated exposures of carbon monoxide (CO). Direct-reading instruments recorded 8-hour time-weighted averages (TWA) of 20 – 24 parts per million (ppm), with ceiling limits ranging from 100 – 200 ppm. The Permissible Exposure Limit (PEL) for CO in general industry is 35 ppm as an 8-hour TWA, according to MIOSHA General Industry Standard Part 301, Air Contaminants in General Industry, and the ceiling limit is 200 ppm. The ceiling limit means the employee's exposure shall not be exceeded during any part of the workday.
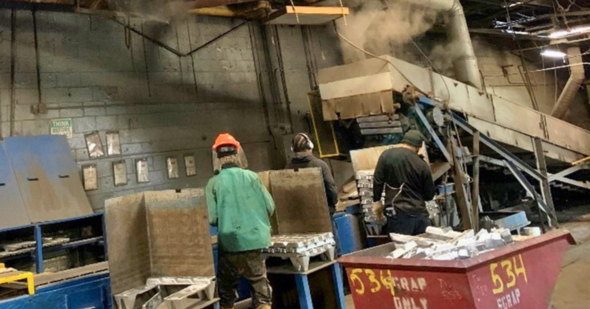 Workers gather and stack zinc ingots from a conveyor.
Citations and Penalties
The inspection resulted in three serious and four other-than-serious citations issued against the employer. The violations are listed below. Some of them were grouped into single citations:
General Industry Standard, Part 309, Cadmium in General Industry
- 1910.1027(d)(1)(i). An initial workplace assessment had not been conducted to determine employee exposure to cadmium.
- 1910.1027(m)(4)(i). Employees who had potential exposure to cadmium were not trained on cadmium or its hazards.
General Industry Standard, Part 310, Lead in General Industry
- 1910.1025(d)(2). An initial assessment had not been made to determine employee exposure to lead.
- 1910.1025(l)(1)(i). Employees that had potential for exposure to airborne lead had not been informed of the content of Appendices A and B of the lead standard.
General Industry Standard Parts 430 Hazard Communication
- 1910.1200(h)(1). Employees had not been effectively trained on hazard communication, including the elements of the standard, the health and physical hazards of the chemicals they worked with, including exhaust byproducts such as carbon monoxide, warning properties, emergency procedures and first aid measures.
General Industry Standard Part 451, Respiratory Protection
- 1910.134(c)(2). Deficiencies identified in the implementation of a voluntary respiratory protection program included the following:
- Improper storage of respirators.
- Incomplete employee information and training on the content of Appendix D of the Respiratory Protection Standard.
- No partial written respirator program.
- No medical evaluations for employees who voluntarily wore elastomeric half face respirators.
General Industry Standard Part 520, Ventilation Control
- 325.52007. The exhaust ventilation was inactive and broken in an area where concentrations of carbon monoxide (CO) were measured approaching the permissible ceiling limit. As a result, furnaces were running and propane-powered forklifts were operating, both generating CO.
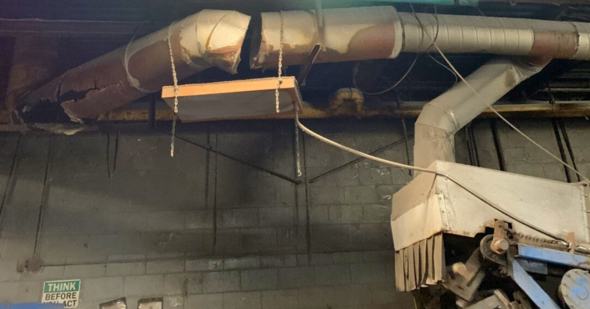 Damaged furnace ventilation ductwork
High-Hazard Industry Profile
Primary Metal Manufacturing, classified under North American Industry Classification System (NAICS) code 331, is one of 10 high-hazard industries targeted in MIOSHA 2024–2028 strategic plan for reductions in injury and illness rates. This subsector employs approximately 18,900 workers across 387 Michigan employers, accounting for 3.1% of all manufacturing jobs in the state.
Employees in this sector can be exposed to a wide range of safety and health hazards, including exposure to air contaminants (e.g., dusts, CO, isocyanates and various amines and phenols), molten metals, confined spaces, large mobile equipment and occupational noise.
Resources for Employers
MIOSHA offers resources to help employers address workplace hazards:
-
Publications and Standards: Access detailed information at Michigan.gov/mioshapublications.
-
Free Consultation and Training: MIOSHA’s Consultation Education and Training (CET) Division provides onsite consultations, hazard surveys, and training at little to no cost. Request assistance at Michigan.gov/cet.
By leveraging these resources, employers can protect workers while achieving compliance with MIOSHA standards.
By Earl Streacker, Personal Safety Professional, Marathon Petroleum
The Marathon Petroleum Corporation's Detroit Refinery processes sweet and heavy sour crude oils into products like gasoline, distillates, asphalt, natural gas liquids, heavy fuel oil, fuel-grade coke, chemical grade propylene, propane and slurry. The site employs 540 Marathon employees and has been a Michigan Voluntary Protection Program (MVPP) Star site since 2010.
Origin of the Campaign
As a proud Michigan MVPP STAR site, the Marathon Detroit Refinery continuously seeks innovative ways to enhance workplace safety and health. In 2023, two recuring themes emerged from safety-related incidents and near misses: gaps in situational awareness and hazard recognition. This realization led to the creation of the Better Way Campaign, a collaborative initiative developed during a joint health and safety meeting between union and company representatives.
While previous efforts —such as reinforcing Stop Work Authority, the Go/No Go program and using monthly safety meetings, newsletters, start-of-shift discussions and bi-weekly safety videos —had been implemented, progress remained limited. This problem was then brought to the refinery's Safety and Health Committee.
The safety and health committee took up the challenge after our behavioral-based safety facilitator shared a key observation during a meeting. The facilitator would ask workers in the field, “Is there a better way to do this task?” and the simple question often led to significant safety insights and a commitment to explore safer work practices. Recognizing the importance of proactive hazard recognition, we set our sights on reinventing our culture where every employee feels empowered to contribute to safety improvements. From that meeting, The Better Way campaign was created.
|
Implementation of the Campaign
The Better Way Campaign officially launched in November 2023, starting with refinery managers leading monthly sequential safety meetings. During these sessions, they introduced the campaign's core principles and distributed specially designed coins engraved with the question: "Ask yourself, is there a better way?”
This personal touch not only reinforced the message but also encouraged open dialogue about safety practices among all employees and contractors. The managers emphasized the significance of carrying the coin as a constant physical reminder to evaluate tasks critically and to consider alternative, safer methods. To encourage participation, a recognition program was established. Workers in process units were randomly approached and asked if they had their Better Way coin. Employees who had their coin and demonstrated safe work practices with proper PPE received tokens of appreciation.
Additionally, employees who suggested “better ways” to complete tasks safely were rewarded for their creativity and proactive thinking. This recognition program not only incentivized participation but also celebrated the workforce's commitment to continuous improvement.
Impact and Outcomes
The Better Way campaign has sparked countless conversations around hazard recognition and encouraged employees to find innovative ways to perform routine tasks safely. By fostering an environment where workers feel comfortable discussing potential hazards and sharing their ideas, we are increasing individual ownership over safety practices. This cultural shift has led to heightened awareness and proactive engagement in safety discussions throughout the refinery. The success of this campaign is reflected in the increased number of safety dialogues among employees, as well as the growing willingness to challenge the status quo when it comes to daily operations. While we have not established formal metrics to quantify changes, anecdotal feedback and workforce engagement reflect the campaign’s success. The refinery has observed:
- Increased safety discussions among employees.
- Greater willingness to question and improve traditional operations.
- A decrease in recordable incidents and high-severity potential near misses.
|
Join the Ranks of Michigan’s MVPP STAR Sites!
MIOSHA’s MVPP program honors employers excelling in workplace safety and health.
With 27 STAR sites, including Marathon Petroleum’s Detroit Refinery, MVPP showcases the power of partnerships to create safer workplaces Open to general industry and construction, STAR status offers:
✅ Recognition for outstanding safety achievements. ✅ Reduced workplace hazards and improved employee protection. ✅ Enhanced safety culture and continuous improvement.
Ready to elevate safety? Learn more:👉 Michigan.gov/MVPP
By Mike Krafcik, MIOSHA Communications Specialist
Tweddle Group and Food Bank of Eastern Michigan Honored with MIOSHA CET Awards
MIOSHA is proud to recognize two outstanding organizations for their exceptional workplace safety and health management systems as part of its CET Awards program.
Tweddle Group, a leading provider of product support technology, has received the prestigious CET Gold Award, which highlights organizations that go above and beyond compliance to create a culture of safety. Since the Gold Award’s inception in 1994, only 93 Michigan companies have achieved this honor.
“Tweddle Group’s dedication to workplace safety and health is inspiring,” said MIOSHA CET Director Tarah Kile. “This Gold Award reflects their commitment to excellence and sets the stage for even greater achievements in the future.”
 Members of the Tweddle Company's safety team celebrate the company's CET Gold Award during a recognition ceremony on Jan. 16, 2025.
The Food Bank of Eastern Michigan has been awarded the CET Silver Award for its proactive approach to workplace safety. The Silver Award is given to organizations whose Total Case Incident Rate (TCIR) and Days Away, Restricted or Transferred (DART) rates are below the industry average for the current and prior year. Silver award winning companies must also have at least 20 key safety measures in place across all system areas, and an active safety committee to ensure ongoing protection.
Celebrating Excellence in Safety and Health Both organizations have demonstrated the power of proactive safety and health initiatives, fostering cultures that prioritize hazard recognition, employee engagement and continuous improvement.
MIOSHA congratulates Tweddle Group and the Food Bank of Eastern Michigan on these well-deserved honors. For more information about MIOSHA’s CET Awards, visit Michigan.gov/CET.
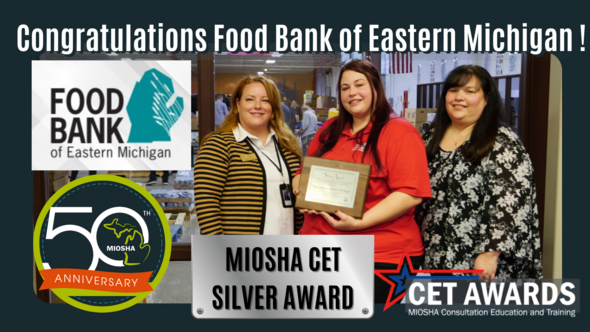 Left to right: MIOSHA CET Director Tarah Kile presents the MIOSHA CET Award to FBEM Safety and Compliance Specialist Samantha Ford and FBEM Chief Operations Director Tina Martinez on Dec. 11, 2024.
 |
Cintas Recognized with MVPP Rising Star Award
Cintas Corporation K15 in Westland received MVPP Rising Star recognition, acknowledging the company’s outstanding commitment to workplace safety and health. The MVPP (Michigan Voluntary Protection Program) Rising Star award is granted to organizations demonstrating excellence in safety practices, continuous improvement, and fostering a culture of safety. Cintas’s achievement highlights their dedication to ensuring the well-being of their employees and promoting a safe work environment.
This recognition underscores the company’s proactive approach to workplace safety and sets a strong example for others in the industry.
The MVPP program is open to all qualifying Michigan employers with injury and illness incident rates below the industry average for each of the last three years.
Learn more about becoming an MVPP Star site at Michigan.gov/MVPP.
|
Quick Links
Agency/Division Instructions/Memorandums Air Contaminants Initiative Asbestos Program CET Request for Consultative Assistance Services (RCA) CET Training Calendar Construction Safety and Health Division (CSHD) DVD/Video Library Service Employee Safety, Health, and Discrimination Complaint Forms Fall Prevention Campaign (STOP FALLS. SAVE LIVES.) General Industry Safety and Health Division (GISHD) Hazard Communication/GHS Laboratory and Equipment Services Michigan Alliances Michigan Safety and Health Achievement Recognition Program (MSHARP) Michigan Voluntary Protection Program (MVPP) MIOSHA FOIA Request MIOSHA News MIOSHA Publications MIOSHA Recordkeeping MIOSHA Standards MIOSHA Training Institute (MTI) MIOSHA Updates MIOSHA Variances Radiation Safety Section Residential Construction Strategic Plan and Initiatives Telephone, Mailing and Email Addresses
|