Volume 32, Issue 4, Fall 2024
Bart Pickelman, CIH, MIOSHA Director
After 34 years of dedicated service to MIOSHA and the state of Michigan, Ron Ray, Technical Services Division (TSD) Director will retire at the end of November.
Ron’s journey with MIOSHA began in March 1990 as a Lab Scientist. His attention to deal earned him a promotion in March 2000 to Quality Assurance Officer for the laboratory. In 2002, Ron briefly left MIOSHA to serve as Program Manager for the Licensing and Certification Section in the Department of Consumer and Industry Services. However, he returned in July 2004 to become the MIOSHA Laboratory and Equipment Services Section Manager.
In July 2011, Ron’s commitment to workplace safety and health and his exceptional work ethic led to his promotion to Director of MIOSHA's Management and Technical Services Division, which eventually became TSD. Under Ron’s leadership, TSD has been instrumental in advancing MIOSHA’s mission of protecting the health and safety of Michigan workers, by providing critical support through laboratory and equipment services, information and technical services, standard promulgation, grant, budget, and other financial activities and oversight of the Radiation Safety Section. Ron’s tireless dedication and deep expertise have had a lasting impact on the division and the agency.
|
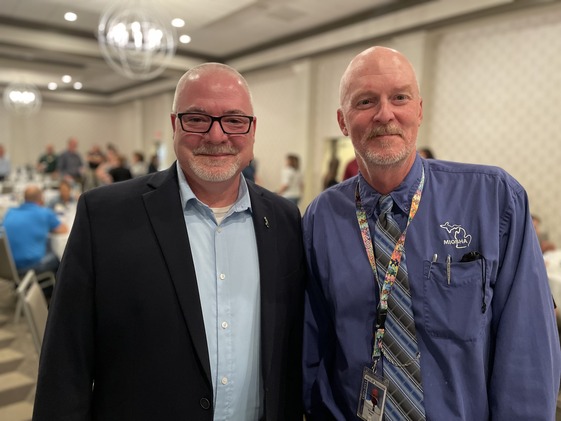 MIOSHA Director Bart Pickelman (left) with MIOSHA Technical Services Division Director Ron Ray, who will retire in November following 34 years of public service with the State of Michigan
By Gloria Keene, MTI Program Coordinator
 As we transition from summer to fall, we are excited to share some great news from the MIOSHA Training Institute (MTI).
Effective October 1, MTI scholarships will now be available for MTI boot camps! This is an expansion of the existing scholarship program, which previously only covered individual seminars. Now, students can apply for scholarships that cover 50 percent of the regular seminar fee for both individual seminars and boot camps. There is no limit to the number of seminars or boot camps for which an individual can apply for a scholarship.
MTI Boot Camps
-
Level One General Industry (GI) Boot Camp: This boot camp is ideal for safety and health coordinators, committee members, and others interested in general safety and health. Participants will begin the process of developing a safety and health program and become familiar with MIOSHA standards. Upon completion, participants will earn the MTI Level One General Industry Safety and Health certificate and the OSHA General Industry 10-Hour card.
-
Level One Construction Boot Camp: Designed for those involved in construction, this boot camp provides the foundation for understanding employer responsibilities, hazard recognition, and worker protection. Successful participants will earn the MTI Level One Construction Safety and Health certificate and the OSHA Construction 30-Hour card.
-
Level Two Safety and Health Management Systems (SHMS) Boot Camp: Tailored for managers and safety coordinators, this boot camp provides in-depth information on managing workplace safety and health systems. Upon completion, participants will receive the MTI Level Two Safety and Health Management Systems certificate.
All MTI seminars are taught by experienced MIOSHA Consultation Education and Training (CET) consultants and offer continuing education credits, providing students with recognition for their educational achievements and technical expertise.
For more information and to enroll in MIOSHA Training Institute courses, visit www.michigan.gov/mti.
By Kathlyn Bernardoni, Industrial Hygienist; Mark Scott, Industrial Hygienist Specialist; Nicholas Rodriguez, Workplace Safety Representative; and Todd Strong, Workplace Safety Representative, General Industry Safety and Health Division (GISHD)
A catastrophic explosion that injured several workers at a Michigan tape manufacturing facility led to MIOSHA issuing over two dozen safety and health citations totaling nearly a half-million dollars in penalties.
MIOSHA’s enforcement actions followed an 18-month investigation that began on October 17, 2022, after the explosion hospitalized four employees, three of whom sustained serious injuries. The explosion occurred during troubleshooting of a seized batch process operation involving the Churn 3 vessel, which contained a toluene-based, glue-like mixture.
The Churn 3 vessel had seized two weeks prior to the explosion. During that time, the facility stopped attempts to inert the vessel or monitor for explosive atmospheres. The toluene-based substance continued to off-gas, creating an explosive environment inside the vessel. On Oct. 13, 2022, the atmosphere in the vessel ignited, triggering a flash fire and explosion. Potential ignition sources included a degraded lithium-ion battery that had fallen into the vessel and sparks from unapproved tools being used to break apart the seized material.
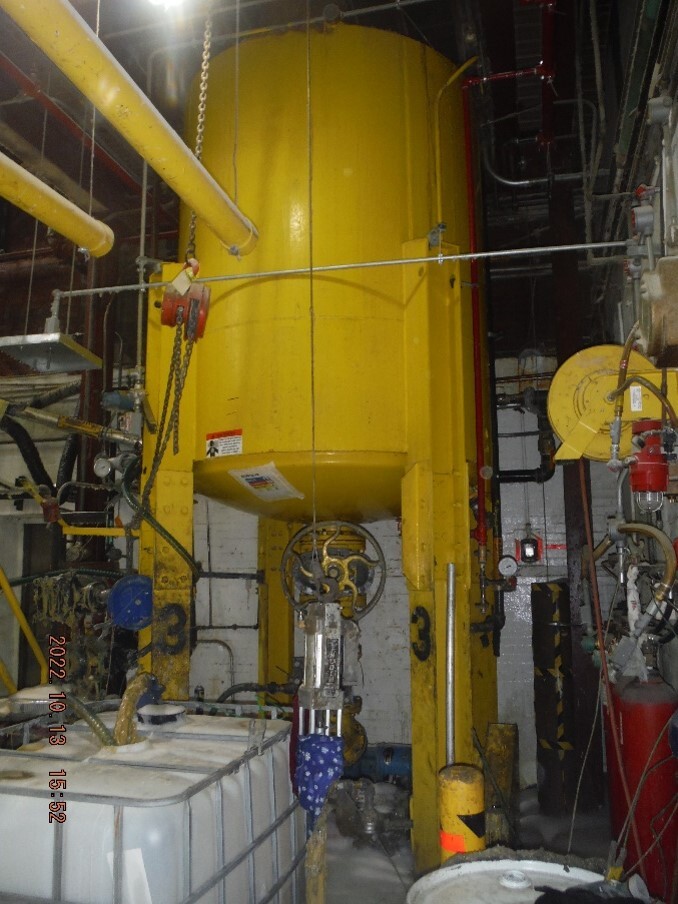 Churn 3, the vessel that contained the seized material. The top of the vessel extends through the mezzanine, where employees manually add dry ingredients.
The loading platform for Churn 3 was located on a balcony above the wet mix/coatings area. Access to the platform was only available through an overhead fire door designed to close automatically in the event of a fire. Although the door began to close during the explosion, it did not fully isolate the area because a powered industrial truck was obstructing its path. MIOSHA conducted a separate inspection to address the egress hazard.
During the investigation, MIOSHA also observed fugitive dust around the Churn 3 loading area. Safety data sheets for materials used in the batch process indicated combustible dust hazards. A sample collected from the platform tested positive for explosivity, prompting a second inspection to address the combustible dust hazard.
Explosion Contributing Factors
-
Churn 3 handled batches ranging from under 10,000 pounds to over 10,000 pounds of flammable liquids, depending on the adhesive being produced. While the employer stated in its emergency contingency plan that it was not covered by the Process Safety Management (PSM) standard, it had voluntarily opted to follow PSM guidelines. However, many elements of the PSM program were not maintained. PSM applies to processes involving more than the threshold quantity of a regulated chemical, and the interconnected vessels in the coatings area exceeded the threshold for flammable liquids.
-
The employer normally used dry ice to create a protective blanket over the toluene to prevent igniting vapors. However, during troubleshooting, the dry ice funnel was removed, and no alternative inerting methods were used.
-
The employer deprioritized recommendations from their insurance carrier concerning explosion hazard protection.
-
Churn 3 was not designed or constructed with adequate safety features to mitigate the hazards associated with flammable liquids and combustible dust. Flammable liquid standards require that equipment handling such materials be designed to control vapor concentrations, inert the internal atmosphere, suppress or relieve explosion pressure, or contain the peak explosion pressure.
-
The employer also failed to implement sufficient hot work oversight and practices to control hazardous working conditions, including the frequent presence of combustible dust and flammable vapors in the work area.
 An overhead door was prevented from closing due to a powered industrial truck in the entry way
Citations and Penalties
On March 26, 2024, MIOSHA issued 16 serious, 13 willful-serious, and two other-than-serious citations related to the flash fire/explosion investigation with total penalties amounting to $468,000.The employer filed an appeal. A summary of the citations is listed below, with some citations grouped into single citations.
MIOSHA Administrative Standard Part 11, Recording and Reporting of Occupational Injuries and Illnesses
- Rule 408.22129(4): Employer did not record injuries on the MIOSHA logs within 7 days. $900.
- Rule 408.22141(1): Employer did not electronically submit their OSHA logs in 2021 and 2023. $900.
General Industry Standard Part 75, Flammable Liquids
- Paragraph 1910.106(h)(7)(iii)(a): Electrical wiring and equipment were not adequately installed. $6,300.
- Paragraph 1910.106(h)(7)(i)(a): Precautions were not taken to prevent the ignition of flammable vapors. Grouped with 1910.119(k)(1).
- Paragraph 1910.106(h)(7)(ii)(b): Hot work was not done under the proper supervision. Grouped with 1910.119(k)(1).
- Paragraph 1910.106(h)(4)(iv)(b): Employer did not have adequate explosion mitigation for the Churn 3 Adhesives Mixer. $63,000.
General Industry Standard Part 430, Hazard Communication
- Paragraph 1910.1200(g)(1): Employer did not have safety data sheet for adhesive intermediate materials. $6,300.
General Industry Standard Part 433, Personal Protective Equipment
- Paragraph 1910.132(a): Employer did not provide or require fire-resistant clothing in a classified area. $6,300.
- Paragraph 1910.132(d)(2): Employer did not verify that the required workplace hazard assessment for personal protective equipment had been performed through a written certification. $6,300.
General Industry Standard Part 591, Process Safety Management of Highly Hazardous Chemicals
- Paragraph 1910.119(c)(2): Employer did not obtain employee or employee representative input when developing the hazard analysis and the other elements of the PSM plan. $6,300.
- Paragraph 1910.119(c)(3): Employer did not provide employees or employee representatives access to process hazard analysis (PHA) or process safety information (PSI). Grouped with 1910.119(c)(2).
- Paragraph 1910.119(d)(2): Employer did not maintain PSI pertaining to the safe operating limits of the process or account for deviations. $6,300.
- Paragraph 1910.119(d)(3)(i): Employer did not maintain adequate information pertaining to the equipment in the process. Grouped with 1910.119(d)(2).
- Paragraph 1910.119(d)(3)(ii): Employer did not document that equipment complies with any recognized and generally accepted good engineering practices (RAGAGEP). $63,000.
- Paragraph 1910.119(e)(3)(i): Hazards of a process inadequately addressed. $6,300.
- Paragraph 1910.119(e)(3)(vii): Inadequate process hazard analysis; no qualitative hazard evaluation. Grouped with 1910.119(e)(3)(i).
- Paragraph 1910.119(e)(6): PHA was not revalidated or updated every 5 years. $63,000.
- Paragraph 1910.119(f)(1): Employer did not develop and implement adequate written operating procedures. $6,300.
- Paragraph 1910.119(f)(2): Operating procedures were not accessible to employees. Grouped with 1910.119(f)(1).
- Paragraph 1910.119(f)(3): Operating procedures were not certified annually. Grouped with 1910.119(f)(1).
- Paragraph 1910.119(g)(1)(i): Employer did not provide training to each employee regarding process upset conditions. $6,300.
- Paragraph 1910.119(g)(2): Employer did not provide refresher training at minimum 3-year intervals. Grouped with 1910.119(g)(1)(i).
- Paragraph 1910.119(h)(2): The employer did not properly evaluate, inform, or train contractors. $6,300.
- Paragraph 1910.119(j)(2): Employer did not implement written procedures to maintain integrity of process and equipment. $63,000.
- Paragraph 1910.119(j)(3): The employer did not train employees for process upset or online maintenance activities. Grouped with 1910.119(j)(2)
- Paragraph 1910.119(j)(4)(i): Inspections and tests were not performed on all process equipment. Grouped with 1910.119(j)(2).
- Paragraph 1910.119(j)(4)(ii): Inspections and tests did not follow RAGAGEP. Grouped with 1910.119(j)(2).
- Paragraph 1910.119(j)(4)(iii): Inspections and tests did not follow recommended inspection schedules. Grouped with 1910.119(j)(2).
- Paragraph 1910.119(j)(4)(iv): Employer did not maintain adequate documentation of inspections and tests. Grouped with 1910.119(j)(2).
- Paragraph 1910.119(k)(1): The employer did not issue a hot work permit to mitigate ignition hazards introduced during work on and near a covered process. $63,000.
- Paragraph 1910.119(o)(1): The employer did not evaluate compliance every 3 years with the PSM standard. $63,000.
In addition, MIOSHA issued one serious citation in a companion inspection to address the egress hazard. A summary of the citations is listed below.
General Industry Standard Part 75, Flammable Liquids
- Paragraph 1910.106(h)(3)(i)(b): There was no approved means of egress from the churn 3 loading platform. $6,300.
Lastly, MIOSHA issued three serious citations in an additional companion inspection to address the combustible dust hazards. A summary of the citations is listed below.
ACT 154, Michigan Occupational Safety and Health Act, Act 154 of 1974
- Section 11(a): Employees were exposed to fire, explosion and deflagration hazards associated with the manufacturing of adhesive intermediates involving combustible dust during the Churn 3 blending process. $6,300.
General Industry Standard Part 2, Walking-Working Surfaces
- Paragraph 1910.22(a)(1): Employer did not maintain a sufficient combustible-dust housekeeping program. $6,300.
General Industry Standard Part 430, Hazard Communication
- Paragraph 1910.1200(h)(3): Employees were not trained on the hazards of combustible dust. $6,300.
Total Proposed Penalties – $468,000
by Jeremy Hidalgo, Construction Safety Supervisor, Construction Safety and Health Division (CSHD)
A framing contractor was ordered to pay penalties resulting from safety citations connected to the death of a 22-year-old construction worker at a Bloomfield Township home in 2022.
Following the incident, the employer refused to cooperate with the investigation, prompting MIOSHA to take legal action to compel compliance for over 18 months.
On Dec. 7, 2022, the worker was installing windows on a second-story dormer using an elevated work platform attached to a boom forklift. The forklift tipped over sideways, causing the worker to fall and possibly strike his head on trees and the concrete below. The victim later died at the hospital.
Employer Non Compliance
At the start of the investigation, a MIOSHA safety officer contacted the employer and conducted an opening conference over the phone. When the safety officer requested to meet at the worksite, the person who answered—possibly the owner—refused, stating they would never return to the site. As a result, MIOSHA issued an administrative subpoena to obtain additional information. Despite the lack of cooperation, the safety officer was able to collect measurements and photographs of the site and equipment.
When the owner did not respond, MIOSHA requested assistance from the Michigan Attorney General Office's Labor Division. After several months, a motion to compel was granted in October 2023.
The owner continued to refuse cooperation, prompting the Attorney General's Office to file a contempt motion, which was granted in March 2024.
|
 A 22-year-old construction worker was killed on Dec. 7, 2022, after a forklift platform he was standing on tipped over, causing him to fall.
Citations and Penalties
Facing the possibility of jail time, the owner finally provided MIOSHA with the requested information, and employee interviews were conducted by the safety officer. On July 12, MIOSHA issued 10 serious citations to the subcontractor, totaling $59,000. To achieve a deterrent effect, no deductions were granted for the citations issued.
MIOSHA issued six (6) citations under Construction Standard Part 12, Scaffolds and Scaffold Platforms
- Rule 408.41243(2) Missing guardrail on sides of elevated work platform with employee not wearing fall protection; employee exposed to falling up to 25 feet in height to grade. $7,000.
- Rule 408.41243(4) No fall protection provided or in use by employee; employee exposed to falling up to 25 feet in height to grade. $5,000.
- Rule 408.41243(5) Leveling devices not being used and/or not functional at the time of the incident; employees exposed to forklift overturning sideways (laterally) as boom was elevated over 40 degrees - $7,000.
- Rule 408.41243(7) Forklift with employee located inside elevated work platform not being returned to the ground before repositioning; employees were exposed to forklift overturning (laterally) - $7,000.
- Rule 408.41243(8) Employee operating forklift with another employee being elevated in a work platform exceeding 1/3 of its rated capacity. Employees were both exposed to the sideway overturning (laterally) of the forklift - $7,000.
- Rule 408.41245 No training provided to employee operating an extendable boom rough terrain forklift with employee and work platform attached to the forks. Employees were exposed to forklift overturning sideways (laterally) - $7,000.
MIOSHA also issued two (2) serious citations to the subcontractor under Construction Standard Part 1, General Rules.
- Rule 408.40114(1) Failure to develop, maintain, coordinate with employees a written Accident Prevention Program (APP). $3,000.
- Rule 408.40119(1) Failure to maintain adequate housekeeping at the site. $4,000.
MIOSHA also issued one (1) serious citation to the subcontractor under Construction Standard Part 13, Mobile Equipment.
- Rule 1910.178(6) No certification of operator training of an extendible boom rough terrain forklift. Two employees were exposed to the overturning sideways (laterally) of the forklift. $7,000.
MIOSHA also issued one (1) serious citation to the subcontractor under Construction Standard Part 6, Personal Protective Equipment .
- Rule 1926.100(a) No hardhat worn by employee in elevated work platform. $5,000.
Total Proposed Penalties: $59,000
The mission of the MIOSHA Construction Safety and Health Division is to prevent death, injury and disease through eliminating or reducing construction worker exposure to safety hazards, physical hazards and chemical hazards.
If you are interested in the MIOSHA standards and publications related to construction hazards, visit michigan.gov/mioshapublications.
By Mike Krafcik, MIOSHA Communications Specialist
 One of the most consequential industries in the Michigan, the construction sector employs over 200,000 employees statewide, according to the U.S. Bureau of Labor Statistics. As a cornerstone of Michigan’s economy, responsible for building and maintaining essential infrastructure, it also presents significant health hazards to workers. Prioritizing safety and health on construction sites is crucial to protecting workers and ensuring their well-being.
Common Health Hazards in Construction
1. Respiratory Hazards
-
Silica Dust: Exposure to respirable crystalline silica dust from cutting, grinding, or drilling concrete and stone can lead to silicosis, a severe lung disease. Prolonged exposure may also increase the risk of lung cancer.
-
Asbestos: While less commonly used today, asbestos, a mineral-based material resistant to heat and corrosive chemicals was widely used in buildings built before 1981. Asbestos exposure in construction can occur in older buildings during renovation or demolition activities, when asbestos containing materials can become airborne and inhaled by workers. Exposure to asbestos is associated with lung cancer, mesothelioma, and asbestosis.
-
Volatile Organic Compounds (VOCs): Found in paints, solvents, and adhesives, VOCs can cause respiratory irritation, headaches, and long-term health issues with prolonged exposure.
2. Noise Hazards
- Construction sites are often noisy environments, with equipment like jackhammers, saws, and heavy machinery generate high decibel levels. Prolonged exposure to loud noise can lead to hearing loss and other auditory issues. Employees should wear hearing protection when exposed to loud noise levels to protect their hearing and reduce the risk of hearing loss.
3. Lead
- Workers may encounter lead in old paint during renovation or demolition projects. Lead exposure occurs via inhalation and through ingestion of lead and can cause neurological damage and other severe health problems, especially with long-term exposure.
4. Ergonomic Hazards
- Construction work often involves heavy lifting, repetitive motions, and awkward postures, leading to musculoskeletal disorders (MSDs). Over time, this can result in chronic pain, injuries, and reduced work capacity.
5. Heat Stress
- Outdoor construction workers are particularly vulnerable to heat stress, especially during the summer months. Prolonged exposure to high temperatures can lead to heat exhaustion, heat stroke, and other heat-related illnesses.
Preventive Measures and Best Practices
To mitigate these safety and health hazards, it is essential for construction employers and employees to adopt robust safety practices and preventive measures:
-
Implementing a Safety and Health Program (SHP): A comprehensive SHP can help identify potential hazards, establish health and safety protocols, and ensure compliance with health and safety regulations.
-
Providing Personal Protective Equipment (PPE): Ensuring that workers have access to and are trained in the proper use of PPE, such as respirators and hearing protection is vital to preventing worker injuries and illnesses.
-
Conducting Regular Health and Safety Training: Ongoing health and safety training helps workers stay informed about potential hazards and reinforces safe work practices. Training should cover topics such as hazard recognition, emergency procedures, and proper equipment use.
-
Promoting Ergonomics: Educating workers on proper lifting techniques, encouraging regular breaks, and providing tools and equipment that reduce strain can help prevent musculoskeletal injuries.
-
Monitoring Environmental Conditions: Regularly assessing noise levels, air quality, and temperature conditions on-site can help prevent exposure to harmful levels of dust, chemicals, and heat.
-
Encouraging a Positive Safety Culture: Creating a positive workplace culture that prioritizes health and safety encourages workers to report hazards, participate in health and safety programs, and look out for one another.
The Role of MIOSHA in Promoting Workplace Safety and Health
Our Consultation Education and Training (CET) Division provides free, statewide safety and health assistance to employers and employees – without penalties or citations. Our team of occupational safety experts, construction safety consultants, and industrial hygienists offer customized services for management and staff. Through partnerships like the MIOSHA Alliance Program, construction companies can access valuable resources to improve safety and health practices.
Visit Michigan.gov/cet for a full list of services, including consultative visits, awards, grants, and more. Complete an online request for assistance at michigan.gov/cetrca.
by Mark Ginter, MIOSHA Cooperative Programs Specialist
MIOSHA Alliances are formal, voluntary partnerships between MIOSHA and external organizations, aimed at promoting higher levels of worker safety and health. These alliances create opportunities to exchange ideas, address concerns, raise safety issues, and advocate for the elimination of serious workplace hazards. In 2023, the MIOSHA Alliance program celebrated its 20th anniversary, marking two decades of cooperative outreach with Michigan employers.
Over the years, the alliance program has facilitated countless interactions with employers and employees through conferences, tradeshows, jobsite visits and training sessions. As the needs of employers have evolved, so has the alliance program, which underwent significant changes past year to foster further growth and better meet the needs of employers. Key improvements include the creation of a dedicated role to oversee the program, the introduction of new alliance categories, and adjustments to alliance agreements terms and reporting process.
Establishment of the MIOSHA Cooperative Programs Specialist
Traditionally, MIOSHA’s cooperative programs, including alliances, were managed by departmental managers and individual Alliance liaisons. While this approach was effective, it became clear that dedicated resources were necessary to promote the program’s growth. In summer 2023, MIOSHA created the Cooperative Programs Specialist position. This role oversees the entire Alliance program, supports the liaisons, and focuses on expanding the program’s reach and impact.
Introduction of Multiple Alliance Categories
Recognizing that not all Alliance members perform year-round activities or require the same services, MIOSHA introduced new categories to better serve each the needs of each alliance:
-
Partner Alliances: Geared toward organizations that routinely interact with their Liaisons, request consultative support or field activities, or have regular activities related to the Alliance.
-
Affiliative Alliances: Catered to members who focus on limited activities, such as annual conferences, tradeshows, or outreach efforts that may not require quarterly reporting.
-
Ambassador Status is available to Alliance members who consistently perform at a high level, offering recognition and benefits during the renewal process.
Extended Alliance agreement term and improved reporting
Previously, Alliance agreements were established for a three-year period. To provide additional time to focus on Alliance activities rather than preparing for the next cycle, Alliances have been expanded to a five-year period. The extended period allows more time for impactful outreach efforts and new opportunities within the Alliance. Additionally, MIOSHA has streamlined its quarterly and annual reporting processes, making it easier for both liaisons and members to track and document activities.
Current alliance agreements will remain in place and not changed until the time of renewal. Liaisons will reach out before the agreement expiration date to discuss the best-fit category for each member. The updated reporting formats will begin rolling out immediately.
For more information about the MIOSHA Alliance program or specific inquiries, visit michigan.gov/mioshacooperative or contact MIOSHA Cooperative Programs Specialist Mark Ginter at GinterM@Michigan.gov.
|
 |
By Mike Krafcik, MIOSHA Communications Specialist
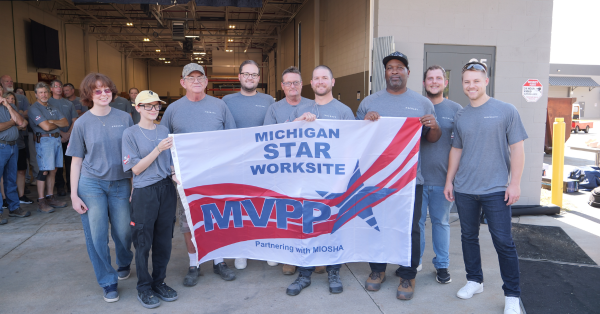 Members of the Nucraft Furniture Company safety team are pictured during Nucraft's MIOSHA MVPP Star award Ceremony on Sept. 18, 2024
Nucraft Earns MVPP Status
Nucraft Furniture has become the 26th Michigan company to achieve Michigan Voluntary Protection Program (MVPP) Star status, the highest safety and health distinction in the state,
MIOSHA presented Nucraft with the MVPP Star award and plaque at its Comstock Park facility on September 18. The 305-employee office furniture manufacturer was honored for exceeding MIOSHA’s worker protection requirements and maintaining injury and illness rates below the industry average for the past three years.
“Nucraft’s commitment to workplace safety and employee well-being is truly impressive,” said MIOSHA Consultation Education and Training Division Director Tarah Kile. “Their proactive efforts, from innovative solutions to strong leadership engagement, set a high standard for safety excellence.”
Nucraft earned the MVPP Rising Star designation in 2023, a crucial step toward achieving the Michigan Star, which recognizes the highest standards in workplace safety and health.
“I am so proud of our Nucraft associates achieving MIOSHA VPP Star status,” said Nucraft Furniture CEO Matt Schad. “It represents an enormous effort and continual dedication to making Nucraft a safe place to work. Congratulations to the Nucraft team."
Read the press release to learn more about Nucraft's MVPP award.
Learn more about becoming an MVPP Star site at Michigan.gov/MVPP.
 |
Rexair Completes Michigan Challenge Program
Rexair LLC. has successfully completed a three-year cooperative agreement with MIOSHA through the Michigan Challenge Program (MCP), further solidifying its commitment to workplace safety and health.
Founded in 1936, Rexair is known for manufacturing and developing The Rainbow, a water-based Total Home Cleaning System sold in over 80 countries across the world.
The company first joined the Michigan Challenge Program in 2021 and has since implemented significant improvements, including enhancing incident analysis, establishing safety goals, increasing safety committee involvement, developing Job Safety Analyses (JSAs), and creating a comprehensive safety inspection program.
"Rexair has transformed its organizational safety culture and climate in several ways, reducing exposure to occupational injuries and illnesses while positively influencing employees’ perceptions of leadership's commitment to safety," said MIOSHA Consultation Education and Training Division Director, Tarah Kile. "MIOSHA thanks Rexair for accepting and completing this challenge."
The Michigan Challenge Program (MCP) offers employers a unique opportunity to develop an effective safety and health program through a three-year cooperative agreement with MIOSHA.
Rexair was honored to participate in the Michigan Challenge Program," said Rexair Human Resources Manager Kari Wineland. "The opportunity to fine-tune our safety and health program along with the great in-person training provided by MIOSHA was well received and appreciated by everyone.
Workplace safety makes good business sense. Learn how you can develop a winning strategy to support your employees’ safety and health—while boosting your company’s bottom line. Apply for the Michigan Challenge Program today!
|
 |
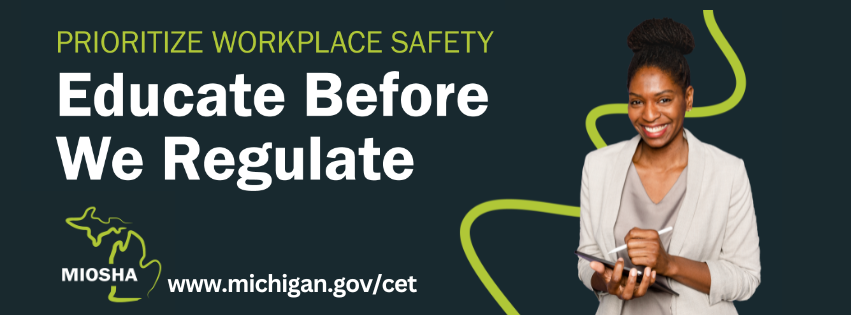  |
Quick Links
Agency/Division Instructions/Memorandums Air Contaminants Initiative Asbestos Program CET Request for Consultative Assistance Services (RCA) CET Training Calendar Construction Safety and Health Division (CSHD) DVD/Video Library Service Employee Safety, Health, and Discrimination Complaint Forms Fall Prevention Campaign (STOP FALLS. SAVE LIVES.) General Industry Safety and Health Division (GISHD) Hazard Communication/GHS Laboratory and Equipment Services Michigan Alliances Michigan Safety and Health Achievement Recognition Program (MSHARP) Michigan Voluntary Protection Program (MVPP) MIOSHA FOIA Request MIOSHA News MIOSHA Publications MIOSHA Recordkeeping MIOSHA Standards MIOSHA Training Institute (MTI) MIOSHA Updates MIOSHA Variances Radiation Safety Section Residential Construction Strategic Plan and Initiatives Telephone, Mailing and Email Addresses
|