Volume 32, Issue 2, Spring 2024
Bart Pickelman, CIH, MIOSHA Director
As we begin the spring construction season, it's important to remember excavation and trenching is one the most dangerous and deadly construction activities.
Cave-ins are perhaps the most feared trenching hazard. However, other potentially fatal hazards exist in trenching and excavation operations, including asphyxiation due to lack of oxygen, inhalation of toxic fumes and drowning.
MIOSHA has investigated five fatal excavation accidents from 2018 to 2022, including two West Michigan brothers killed in a trench collapse while installing drainage for a pole barn in 2022.
Effective Jan. 3, MIOSHA amended Construction Standard Part 9, Excavation, Trenching, and Shoring. Among the changes, definitions were added to modernize standards in order to bolster worker safety and health protections.
For OSHA Region 5 Trench Safety Week 2024, MIOSHA continued to participate and promote excavation and trenching courses offered in Michigan during the spring and summer.
MIOSHA's trenching and excavation webpage offers resources with additional information on trenching hazards and solutions. MIOSHA adopted OSHA's national emphasis program on excavation and trenching operations to help prevent future incidents. The MIOSHA Consultation Education and Training (CET) Division provides free onsite consultation assistance, hazard surveys, and training to employers. To take advantage of our resources, submit your request online or call 517-284 -7720.
|
 |
By Mike Krafcik, MIOSHA Communications Specialist
The MIOSHA Training Institute (MTI) is an innovative and collaborative program that provides top-notch and affordable occupational safety and health training to employers across the state. As of 2023, 33,845 participants have taken an MTI course, ensuring that more companies are achieving compliance with MIOSHA standards and advancing their workplace safety and health.
Kent County Road Commission Employee Safety Superintendent George Smith is one of 15 students to obtain all six MTI certificates: (Level 1 Safety and Health General Industry, Level 2 Compliance for General Industry, Level 1 & 2 — Safety and Health Construction, Level 2 Safety and Health Management Systems and Occupational Health).
Smith pursued the MIOSHA certifications following his promotion to safety superintendent in 2015, as a position created after a department construction foreman was killed after being struck by a motor grader in 2014.
"I wanted to dig into it and learn as much as I can to keep my employee's safe," Smith said.
Smith spent a two-year period obtaining six MTI certificates and taking other MTI courses.
"If you're interested in safety, in my opinion, it's a must. The information you get from them, you can't get it anywhere else, it's very valuable," Smith said.
|
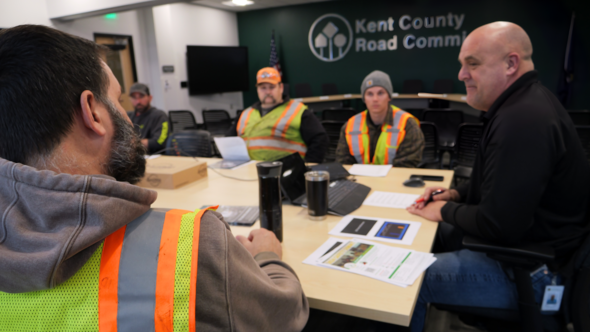 Kent County Road Commission Employee Safety Superintendent George Smith (right) is pictured during a weekly safety committee meeting with his staff members.
Smith credits his experience in the MTI program as a pivotal step to implementing a robust workplace health and safety culture at the road commission.
Smith leads weekly department safety committee meetings and teaches an OSHA 10-hour course to his mechanics and an OSHA 30-hour construction course in his spare time.
"If everyone knows what I know, they are going to follow those rules," Smith said. I never want to have to go to a loved one and tell them their family member isn't coming home today."
Beyond workplace benefits, some MTI graduates have even earned promotions and job offers because of their completion of certificate programs.
For a complete list of scheduled MIOSHA Training Institute courses, check out the MIOSHA Training Calendar at www.michigan.gov/mti.
By Lauren Wilson, Safety Supervisor, General Industry Safety and Health Division (GISHD)
A 75-year-old general laborer was killed while riding a zero-turn lawn mower that crossed over a retaining wall before it flipped onto its side, fatally crushing the worker.
The employee was mowing grass at a fruit farm while working alone during the July 10, 2023 incident. The fatal mishap occurred when the laborer tried to maneuver the lawn mower on a slope, along a narrow seven foot strip of grass between a tree and the edge of a 27-inch retaining wall.
The lawn mower had a rollover protection system (ROPS), including a U-shaped metal bar on the frame extending over the driver to reduce the risk of an operator being crushed during a rollover. For the ROPS system to be effective, the driver must be secured in the seat using a seatbelt.
In this case, the lawn mower slipped off the grass and over the retaining wall before it landed on its side. The employee was thrown from the seat, and the metal bar from the ROPS system struck his head and neck, pinning him to the ground. Later that afternoon, a coworker found the unresponsive employee trapped under the mower. The worker was pronounced dead at the scene, and his cause of death was due to mechanical asphyxia, according to medical examiners.
|
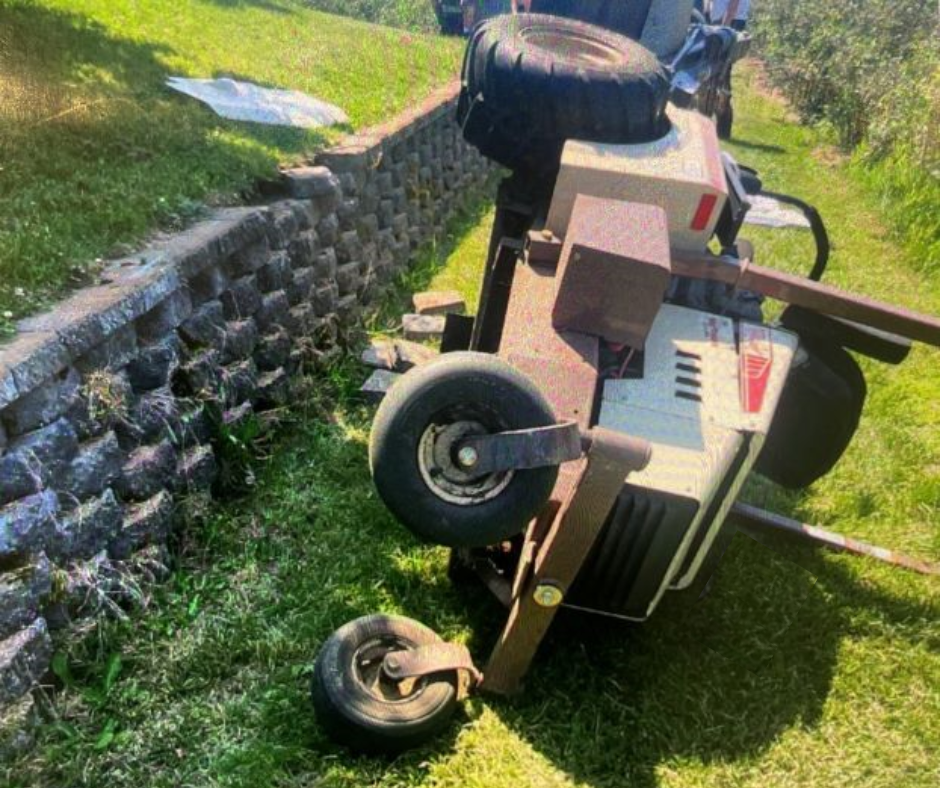 Pictured is the flipped over riding lawn mower involved in a worksite fatality on July 10, 2023.
MIOSHA's investigation determined the employee was not wearing a seatbelt at the time of the incident. Additionally, the employee was operating the lawn mower across the face of a 27-degree slope when it was not specifically designed to operate on steep slopes. The investigation resulted in two serious citations.
A summary of the citations is listed below.
Act 154, Michigan Occupational Safety and Health Act, Act 154 of 1974
- Section 11(a): The use of a seatbelt was not enforced when a rollover protection system was being utilized while an employee was operating a riding zero-turn lawn mower.
General Industry Standard Part 54, Powered Groundskeeping Equipment
- Rule 408.15443(4): An employee was permitted to operate the lawn mower across the face of an approximately 27-degree slope.
Nikki Clark, Safety and Health Manager, MIOSHA Construction Safety & Health Division
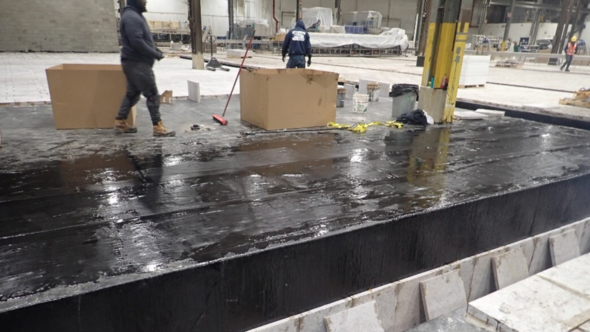 An employee was not wearing respiratory protection while scooping silica containing materials during MIOSHA's first visit to the worksite.
In February 2023, MIOSHA Construction Safety and Health Division (CSHD) received a complaint alleging epoxy caused injuries and burns to workers inside a machine factory. The chemicals weren't disposed of properly, and employees working in an underground tank were exposed to epoxy fumes. One employee was left hospitalized with burns caused by the epoxy material, according to the complaint.
MIOSHA launched an inspection of the employer who installed an epoxy base on the flooring and granite floor tiles on top of the epoxy at the factory, which was in the process of being converted into a lead acid battery production facility.
According to the employer's safety data sheet, the epoxy was a skin sensitizer, with components of the applied epoxy that included a hardener/catalyst, thinner and a resin. A quartz powder or graphite powder was also added to the epoxy, depending on the application.
According to the employer’s injury and illness records, five employees sought medical treatment for burn-like contact-dermatitis injuries in the groin, forearm, wrist, and armpit areas. The injured employees were prescribed antibiotics and steroids for their injuries, according to medical reports.
The employees became sensitized to the epoxy after they either mixed or applied epoxy resin at the worksite. Those employees who experienced contact dermatitis were assigned to other job duties not involving epoxy mixing or application.
Special care should be taken to ensure employees are not exposed to skin or respiratory sensitizers. Once a person’s skin or respiratory system is sensitized to any chemical, they can suffer a severe allergic type reaction even if exposure levels are minimal.
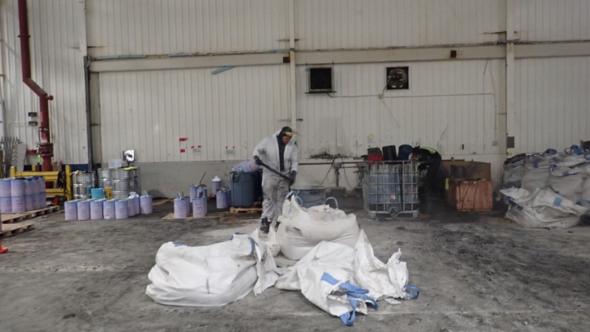 An employee was not wearing respiratory protection while scooping silica containing materials during MIOSHA's first visit to the worksite.
A MIOSHA industrial hygienist conducted personal air monitoring for employees who mixed quartz with the other constituents that make up the epoxy, to determine the employees’ exposure to Respirable Crystalline Silica (RCS). Quartz is a type of crystalline silica, a known carcinogen. Tiny crystalline silica particles or “respirable” particles can travel into lungs and cause silicosis or lung cancer. In 2022, MIOSHA launched a state emphasis program (SEP) to reduce employee exposures to RCS and prevent silicosis.
During the inspection, MIOSHA analyzed quartz flour and quartz powder samples from the worksite. It was determined quartz flour contained 87% crystalline silica and the quartz powder contained 99% crystalline silica. Air monitoring tests concluded an employee was exposed to 82 µg/m3 of RCS, calculated as an 8-hour time-weighted average (TWA) when they shoveled quartz powder and flour into an epoxy mixture used for floor tile installation.
An employee performing this work was observed not wearing respiratory protection during MIOSHA’s initial visit at the worksite. The Permissible Exposure Limit (PEL) for silica in construction is 50ug/m3 of RCS, as an 8-hour TWA, according to MIOSHA Construction Standard Part 690, Silica in Construction.
MIOSHA's safety and health inspections resulted in seven serious citations and eight other than serious citations. The employer has paid a total of $6,400 in penalties as a result of a settlement agreement.
Construction Safety and Health Standard Part 690, Sicilia in Construction
- Rule 1926.1153(d)(1). Employee exposed to RCS above PEL, 50ug/m3 of RCS, as an 8-hour TWA (Serious).
- Rule 1926.1153(d)(2)(i). The employer did not assess its employees’ exposure to RCS.
General Industry and Construction Safety and Health Standards Parts 42 & 92 & 430 Hazard Communication
- Rule 1910.1200(g)(8). The employer did not have, or have access to, the safety data sheet (SDS) for the quartz mixture or graphite powder.
Construction Safety and Health Standard Part 6, Personal Protective Equipment
- Rule 408.406174(4). The employer did not require the use of Personal Protective Equipment (PPE). MIOSHA observed employees not wearing protective clothing when installing tile over tacky epoxy. Employees utilized solvents, alcohol Alkyl Glycidyl Ether, solvents, to remove epoxy from their skin.
Construction Safety and Health Standard Part 8, Handling and Storage of Materials
- Rule 408.40820(4). Stacked lumber had protruding nails
Construction Safety Standard Part 11, Fixed and Portable Ladders
- Rule 408.41113(1). Employees working in an approximately 4-foot-deep pit not provided a ladder for access and egress.
- Rule 408.41126(3). Employees using a step ladder as a straight ladder for access and egress to a pit.
Construction Safety and Health Standard Part 45, Fall Protection
- Rule 1926.501(b)(4)(ii). Each employee on a walking/working surface was not protected from tripping in or stepping into or through a hole/pit
Construction Safety and Health Standard Part 35, Confined Space
- Rule 1926.1205(e). Failure to cancel a Confined Space Entry Permit when entry operations have been completed.
- Rule 1926.1206(k). Failure to record all required information on the Confined Space Entry Permit.
General Industry and Construction Safety and Health Standard Part 451, Respiratory Protection
- Rule 1910.134(c)(2). Improper voluntary use of respirators at the worksite while entering a confined space.
Construction Safety and Health Standard Part 18, Fire Protection and Prevention
- Rule 408.41877(2). Three propane tanks were stored inside the warehouse. Storage of Liquified Petroleum (L.P.) gas within buildings is prohibited.
- Rule 408.41863(1). Employer was storing 160 gallons of Ether inside the warehouse. Not more than 25 gallons of flammable liquid shall be stored within a room outside of an approved wood or metal cabinet.
- Rule 408.41861a(6). A 500-gallon propane tank was stored within 10 feet of the building. LP-gas containers with a water capacity per container of more than 125 gallons This case underscores the importance of rigorous enforcement and proactive measures to ensure workplace safety, and it illustrates the swift and decisive action MIOSHA took in the interest of protecting workers.
Construction Safety and Health Standard Part 20, Demolition
- Rule 408.42031(1). The employer did not provide a demolition survey of the area being renovated.
Michigan Voluntary Protection Program (MVPP) Best Practice:
Honeywell in Muskegon
By Andy Garceau, Senior Health Safety & Environmental Engineer, Honeywell
The Honeywell Burdick & Jackson Muskegon facility is a manufacturer of high-purity solvents, deoxyribonucleic acid (DNA) and ribonucleic acid (RNA) reagents. This process purifies raw chemicals through distillation, filtration and blending to produce high-purity solvents.
Examples of products produced by the site include:
- High-purity solvents including BioSyn™ for DNA, RNA and peptide synthesis
- Anhydrous solvents for moisture-sensitive organic synthesis, organometallic chemistry, combinatorial chemistry, and other related applications
- Solvents and inorganics for general laboratory use.
Honeywell has been a MVPP member since 2019, is certified according to RC14001:2015 and is a member of the American Chemistry Council.
Best Practice Share
Honeywell Muskegon implemented a pre-shift dynamic stretching program In January.
Dynamic vs. Static Stretching (Cleveland Clinic)
The growing popularity of dynamic stretching sets it in contrast to static stretching. While dynamic stretching is based on movement, static stretching involves moving a joint as far as it can go and holding it for a length of time, typically 30 to 90 seconds.
According to Dr. Anne Rex, static stretching fell out of favor as a warm-up routine because research found that static stretching induced some detrimental effects, like reducing maximal strength, power and performance after a single bout of a static stretch.
“When you’re static stretching the muscles aren’t warmed up," she notes. " It’s really more of a relaxation movement. So, the better recommendation would be to do static stretching as part of the cool down process instead.”
That said, Dr. Rex also notes that static stretching has earned something of a bad reputation about being used prior to activity.
“But the most recent studies say that it’s still a very effective way to stretch and increase the range of motion of a joint and it can be used in a short duration stretch as part of a complete dynamic warm-up," Rex said. “There’s still absolutely a role for static stretching but the longer you stretch, the more there’s going to be a negative impact on performance. So, if it’s part of a complete dynamic warm-up, you’d hold the stretch for around 15 to 30 seconds, not 60 to 90 seconds.”
Static stretching after exercise, she says, can also help prevent post-workout stiffness because it can help put muscles back at their pre-exercise length.
Muskegon Honeywell partnered with the insurance giant Chubb Group to develop a customized stretching program for the site to include both dynamic and static stretches. Chubb performed several ergonomic evaluations at the facility to best customize an interactive nine-minute pre-shift dynamic stretch routine.
Instead of simply creating a poster to follow, the nine-minute interactive video can be played and followed along by all employees. Prior to rolling out this program, the Chubb Group's environmental health safety and ergonomic risk control principal consultant who developed the program, visited our worksite to train employees on how to safely perform the dynamic stretches. We recognize that all employees would be able to perform all the stretches, but the training allowed employees to ask questions and find alternative ways to perform the stretches.
|
 |
Partnerships, Alliances and Awards
by Mike Krafcik, MIOSHA Communications Specialist
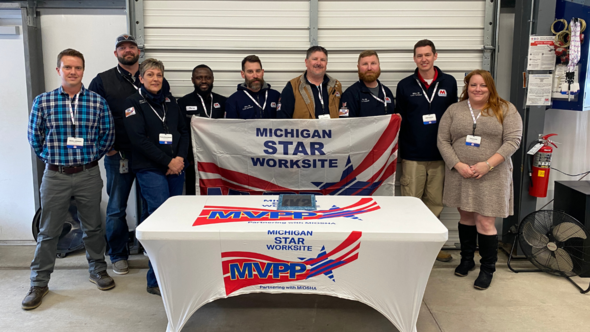 MIOSHA Occupational Safety Consultant Chris Johnson (far left) is pictured with Marathon Petroleum Niles Terminal employees and MIOSHA CET Director Tarah Kile (far right) at the Marathon MVPP award ceremony March 21, 2024.
Marathon Petroleum Corporation Niles Terminal Earns MVPP Status
Marathon Petroleum Corporation's (MPC) Niles Terminal received MIOSHA's (MVPP) Star award.
As the most prestigious safety and health award given in the state, MPC's Niles Terminal joins a group of 26 Michigan companies with current MVPP Star status.
MIOSHA's Consultation Education and Training (CET) Division presented the MVPP Star award and plaque to Marathon Petroleum staff members in Niles on March 21.
“MIOSHA is proud to recognize Marathon Petroleum’s Niles Terminal for establishing a company culture that promotes excellence in workplace safety and health,” said MIOSHA Consultation Education and Training Division Director Tarah Kile. “Implementing best practices for increased employee safety and health, exemplifies a true dedication to safety among management and employees at this facility.”
MPC's Niles terminal is operated under the company's Midstream segment which handles bulk receiving, storage, and distribution of refined petroleum products that includes gasoline, ultra-low sulfur diesel, and kerosene.
"We are honored that our Niles terminal has been recognized by MIOSHA as a VPP Star site,” said Marathon Petroleum Corporation Vice President of Terminals Regina Zolnor. “This award is a significant accomplishment that reflects the commitment of our employees to operating safely and being a good neighbor to the Niles community. I am proud of our team for achieving this recognition.”
More information about MPC can be found on the company's website at www.marathonpetroleum.com.
The MVPP program is open to all qualifying Michigan employers with injury and illness incident rates below the industry average for each of the last three years.
Learn more about becoming an MVPP Star site at Michigan.gov/MVPP.
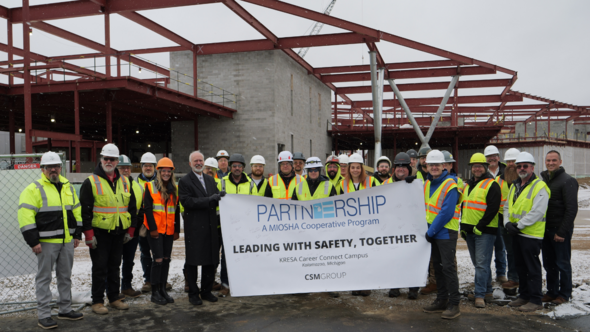 (Holding banner left to right) MIOSHA Construction Safety and Health Division Director Lawrence Hildago and CSM Group CEO Stuart Mason are pictured during the MIOSHA/CMS Group partnership signing at the site of a new Kalamazoo Regional Education Service Agency building on March 18, 2024.
MIOSHA and Kalamazoo-based CMS Group Inc., partnering employers and trade contractors entered into a level two workplace safety and training agreement, with a focus on zero worker injuries and incidents during the construction of the Kalamazoo Regional Education Service Agency (KRESA) Connect Campus and Kalamazoo Country Club.
Approximately 50 contractors and subcontractors involved in both KRESA and Kalamazoo Country Club construction projects signed the agreement which endorse the ultimate goal of zero injuries through construction safety policies and procedures.
"Injury and illness rates are much lower at partnership sites compared to non-partnership sites," said MIOSHA Construction Safety and Health Division Director Lawrence Hidalgo. "These partnerships are built on a common vision to provide all trades people and subcontractors a healthful and safe work place through leadership, responsibility, and accountability in furthering worker health and safety at all levels."
"At CSM Group, the safety and well-being of our employees is paramount," said CSM Group Inc. CEO Stuart Mason. "Our partnership with MIOSHA underscores our unwavering commitment to creating a workplace where everyone feels secure and valued. Together, we aim to achieve significant and measurable reductions in workplace deaths, injuries, and illnesses, setting a new standard for safety excellence."
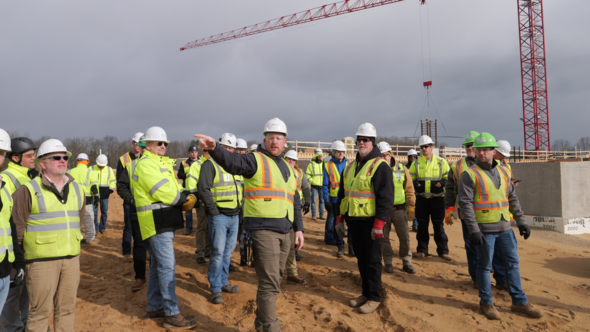 CSM Group staff provided a site walk-thru for contractors, subconractors and MIOSHA staff at the Kalamazoo Country Club construction site March 20, 2024.
About the Projects:
KRESA Career Connect Campus – The KRESA Career Connect Campus will be a centralized facility holding most of Kalamazoo County's Career and Technical Education (CTE) programs. The first phase consists of a two-story structure expected to be completed by fall 2024.
Kalamazoo Country Club – The current expansion to the Kalamazoo Country Club includes the addition of an 11-hole golf course and two-story clubhouse with amenities such as a bowling alley, multiple dining rooms and lounges, locker rooms, a tennis facility, swimming pools, and a two-story parking deck.
Read the full press release to learn more about CMS Group's outstanding safety and health record.
All MIOSHA partnerships are an opportunity for employers, employees and/or their representatives and stakeholders to establish a cooperative relationship with MIOSHA to encourage, assist and recognize their voluntary efforts to focus on and eliminate serious hazards and achieve a high level of safety and health.
By Thomas Shaver, Manager, MIOSHA Standards and FOIA Section
General Industry Standard Part 8, Portable Fire Extinguishers
MIOSHA held a public hearing on Sept.18, 2023, to amend General Industry Part 8, Portable Fire Extinguishers, to meet fire protection requirements, further employee response to fires, clarify employer responsibilities, and determine employee actions related to fires. This went into effect Feb. 2, 2024.
Construction Standard Part 9, Excavation, Trenching and Shoring
MIOSHA amended Construction Safety Part 9, Excavation, Trenching, and Shoring, to add the word “vertically” to R 408.40945, “Trenching Boxes and Shields,” to match OSHA, and to add definitions listed in OSHA’s Subpart P, “Excavations.” This went into effect Jan. 3, 2024.
Construction Standard Part 26, Steel Erection
MIOSHA is amending Construction Safety Part 26, Steel Erection, to adopt by reference Subpart R, except for 1926.753 “Hoisting and Rigging” and 1926.761 “Training,” which are currently covered under Michigan rules which we adopt by reference in R 408.42601.
Radiation Safety Part 5, Administrative Rules for Ionizing Radiation Rules Governing the Use of Radiation Machines
MIOSHA held a public hearing on Aug.16, 2023, to amend the Ionizing Radiation Rules Governing the Use of Radiation standard, and to add an entirely new ruleset titled Part 5, Operator’s Qualifications. These rules establish qualification requirements for individuals engaged in medical x-radiation technology, address the improper performance of medical x-radiation technology, and ensure that individuals and patients are not exposed to unnecessary radiation.
MIOSHA Administrative Standard Part 4, Procedures
MIOSHA is amending the Administrative Standard, Part 4, Board Procedures, to rescind unnecessary rules, add language to allow the filing and service of documents by email and facsimile, add language to establish procedures for the issuance and service of subpoenas by the board, and modify timelines for filing exceptions and responses. MIOSHA is also amending the rules to remove duplicate provisions now contained in the Michigan Office of Administrative Hearings and Rules’ uniform hearing rules R 792.10101 to R 792.11903, as well as updating the rules to make them consistent with existing practices authorized by the board.
Safety and Health Standard Part 11, Recording and Reporting of Occupational Injuries and Illnesses
MIOSHA is amending the Administrative Standard, Part 11, Recording and Reporting of Occupational Injuries and Illnesses, to be at least as effective as federal OSHA’s 1904 standard, “Recording and Reporting Occupational Injuries and Illnesses." This went into effect Feb.13, 2024.
Once approved, the final versions will be added to the MIOSHA Standards web page at michigan.gov/mioshastandards.
Quick Links
Agency/Division Instructions/Memorandums Air Contaminants Initiative Asbestos Program CET Request for Consultative Assistance Services (RCA) CET Training Calendar Construction Safety and Health Division (CSHD) DVD/Video Library Service Employee Safety, Health, and Discrimination Complaint Forms Fall Prevention Campaign (STOP FALLS. SAVE LIVES.) General Industry Safety and Health Division (GISHD) Hazard Communication/GHS Laboratory and Equipment Services Michigan Alliances Michigan Safety and Health Achievement Recognition Program (MSHARP) Michigan Voluntary Protection Program (MVPP) MIOSHA FOIA Request MIOSHA News MIOSHA Publications MIOSHA Recordkeeping MIOSHA Standards MIOSHA Training Institute (MTI) MIOSHA Updates MIOSHA Variances Radiation Safety Section Residential Construction Strategic Plan and Initiatives Telephone, Mailing and Email Addresses
|