Volume 31, Issue 3, Fall 2023
Bart Pickelman, MIOSHA Director
September is National Suicide Prevention Month. MIOSHA is encouraging employers across Michigan to share the importance of employee mental health and wellness by promoting suicide prevention dialogue, training, and resources. Together, we can save lives.
The construction industry has the second highest rate of suicide of any occupation in the United States at 53.3 per 100,000 workers, according to the Centers for Disease Control (CDC).
"Suicide is one of the construction industry’s worst-kept secrets, and it is killing people," said MIOSHA Director Bart Pickelman. “We know how a strong safety culture can positively impact employees’ well being and are committed to working with Michigan employers to strengthen their workplace safety and health."
MIOSHA has no regulations that address workplace stress, however our website has mental health resources available to assist employers and employees in the workplace. As part of MIOSHA's 2024-2028 Strategic Plan, we are dedicated to promoting OSHA and State of Michigan mental health services for workers.
During Construction Suicide Prevention Week (Sept. 4-8), MIOSHA organized a Construction Suicide Prevention event to highlight the high number of suicides in the industry and provide resources to employers and employees. If you are having trouble coping with work-related stress, talk with someone who can help, call or text 988, or visit 988lifeline.org to reach the National Suicide Prevention Lifeline.
|
 |
Michigan Voluntary Protection Program Best Practice: Bakelite Synthetics
By Rich Sajdak, Safety/Health Manager, Bakelite Synthetics Beaver Creek Plant
A strong Safety Culture at the Bakelite Synthetics Beaver Creek facility in Grayling has led to a great safety record along with robust employee participation.
Bakelite's Beaver Creek facility strives for safety excellence and has a focus on critical risk reduction. We challenge our employees to identify hazards/critical risks and take action to prevent incidents/injuries. We utilize Gensuite, an electronic based reporting system to enter and document issues to closure. This electronic system will then report out to all employees the status of each incident.
Safety is our Value. We live “safety first” – its personal, with each of us accountable. Our work is never more important or urgent than performing it safely.
We apply our “Life Saving Rules” to any person on Bakelite’s premises. A key aspect to this involves what we call “Personal Safety Mindset”
- We incorporate safety aspects into our daily behavior at work and at home.
- We talk to each other when we observe dangerous behavior and positively recognize others when they behave safely.
- We influence each other to develop a Safety Mindset.
Our Safety Culture promotes ownership and engagement, to align and focus on what matters the most in terms of Safety.
About Bakelite:
In 2021, Bakelite acquired Georgia Pacific Chemicals, an integration of two companies with legacies of safety, innovation, and success.
Bakelite's headquarters is based in Atlanta, and the combined company has approximately 1,500 associates and 21 manufacturing sites in ten countries.
Bakelite Synthetics Beaver Creek facility (formerly Georgia Pacific Chemicals) located near Grayling, Michigan has approximately 32 employees. The facility manufactures industrial resins, formaldehyde, and urea formaldehyde concentrate (UFC) . The industrial resins are manufactured in a batch process and formaldehyde and UFC are manufactured in a continuous stream process.
The Bakelite Synthetics Beaver Creek facility has been a Michigan Voluntary Protection Program (MVPP) STAR level worksite since 2007.
|
 |
By Gloria Keene, Manager, MIOSHA Training Institute
Summer is almost gone, and fall is almost here. However, protecting the safety and health of Michigan workers is always in season!
As we head into the Fall season, here are some exciting things we want to share about the MIOSHA Training Institute (MTI).
Effective Oct. 1, 2023, MIOSHA will implement the following MTI program changes:
- The Fundamentals of Industrial Hygiene is now a two-day course due to the overwhelming requests made on the MTI Student Evaluation Forms.
- “Mobile Aerial Work Platforms” replaces the title “Part 32 Aerial Work Platforms.” This course is an elective for the Construction and Level Two General Industry Compliance Programs. It remains a one-day course.
- “Part 39 and 40 Electrical Standards for General Industry” replaces “Parts 17, 39, and 40 Electrical Standards for General Industry and Construction.” Part 17 and Construction are removed from the title. The course is no longer an elective for the Level One and Level Two Construction Certificate Programs but will remain a one-day program.
MTI Graduates: MIOSHA and Macomb Community College recognized 115 MTI graduates from 2022 at the annual Michigan Safety Conference on April 18. MIOSHA Director Bart Pickelman acknowledged the graduates for their educational achievements during the graduation ceremony.
The MTI certificate program offers participants an opportunity to be recognized for their educational efforts and increased technical expertise. There are six certificate programs, which include General Industry Safety and Health, Construction Safety and Health, MIOSHA Compliance for General Industry, MIOSHA Compliance for Construction, Safety and Health Management Systems and Occupational Health.
To learn more about MTI and what it can do for you, please contact MIOSHA’s Consultation Education and Training Division at 517-284-7720 or visit www.michigan.gov/mti.
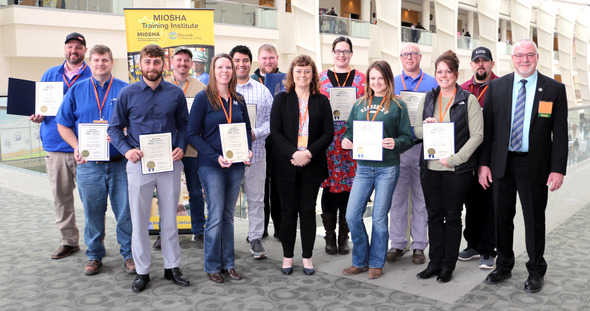 MIOSHA Director Bart Pickelman acknowledged the 115 MTI graduates from 2022 for their educational achievements during a ceremony at the Michigan Safety Conference April 18, 2023.
Nikki Clark, Safety and Health Manager, MIOSHA Construction Safety & Health Division
Three weeks after a massive apartment flood, the MIOSHA Construction Safety and Health Division (CSHD) received a written complaint about the flood which resulted from a pipe burst in January. The complaint also included allegations that a restoration contractor mishandled asbestos containing building materials at the worksite.
A MIOSHA industrial hygienist launched an onsite inspection within eight working days of receiving the complaint. The investigation determined untrained employees without protective equipment had cleaned up drywall ceiling material which contained asbestos when the employer, a restoration contractor, failed to assess and address asbestos hazards at the worksite in a timely fashion.
Typically, asbestos appears as a whitish, fibrous material that may release fibers that range in texture from course to silky. Generally, undisturbed or intact asbestos is not a hazard, but it can be found in many installed building materials constructed prior to 1981 (i.e., roofing, flooring, mastics/glues, wall system materials including drywall joint compound and plaster, siding, etc.). The heaviest exposure to asbestos occurs in the construction industry, primarily during renovation or demolition when asbestos is removed or disturbed in older buildings.
Asbestos exposure can cause disabling respiratory diseases and cancer if the fibers are inhaled or ingested. After initial exposure, disease symptoms generally do not appear until 20 years or later.
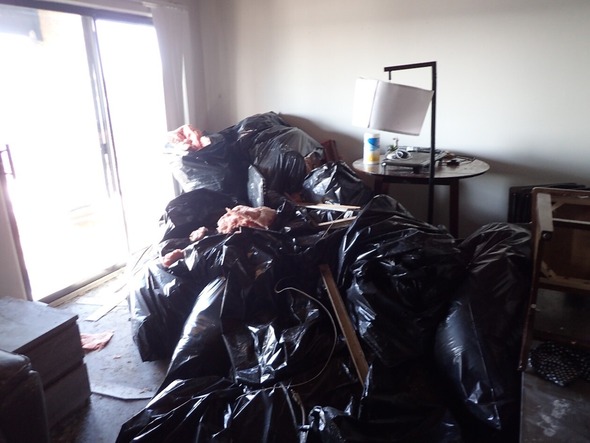 Debris from the water damaged ceiling containing asbestos is pictured in garbage bags during the MIOSHA inspection of the flooded apartment.
Summary of Inspection Findings:
- Water damage caused an interior apartment ceiling to cave-in, and the ceiling material was at least partially cleaned up by a Restoration Contractor. This ceiling cleanup work occurred immediately after the property damage occurred. The apartment building was originally constructed prior to 1981.
- The Water Restoration Contractor had bulk samples collected at the worksite by an accredited asbestos inspector, and these samples were analyzed for asbestos by a qualified laboratory. However, these samples were not collected until three days after the employees performed the initial cleanup of the ceiling debris. The private laboratory utilized by the employer confirmed the ceiling material contained 2% Chrysotile asbestos.
- CSHD collected six bulk samples of the ceiling material during the inspection. The MIOSHA Laboratory determined four of six bulk samples collected by CSHD contained 2% Chrysotile asbestos.
- Interviews with the Restoration Contractor’s employees determined they were not trained to perform asbestos work, and required worker protections and engineering controls were not implemented during the initial cleanup work. The final cleanup at the worksite was conducted by an accredited asbestos contractor.
Citations Issued:
- MIOSHA issued seven Serious citations to the contractor for failure to comply with MIOSHA requirements, set forth in MIOSHA Standard Part 602, Asbestos Standards for Construction:
- Item 1-1: 1101(f)(1)(i) – Failure to conduct employee personal exposure monitoring.
- Item 1-2a: 1926.1101(g)(10) – Failure to provide training for Class IV asbestos work.
- Item 1-2b: 1926.1101(h)(3)(i)(A) – Failure to provide appropriate respiratory protection.
- Item 1-2c: 1926.1101(i)(1) – Failure to provide protective clothing.
- Item 1-2d: 1926.1101(j)(3) – Failure to provide decontamination allowances.
- Item 1-3a: 1926.1101(k)(3)(i) – Failure to determine the presence of asbestos at the site timely.
- Item 1-3b: 1926.1101(k)(3)(ii) – Failure to communicate the presence of asbestos to employees.
- The original penalty assessed was $12,000. The contractor provided sufficient documentation of abatement and entered into a Penalty Reduction Agreement (PRA). The employer paid $6000, 50% of the original penalty.
To ensure worker safety while performing construction work in buildings built prior to 1981, suspect building materials in the work area should not be disturbed or removed until an accredited asbestos building inspector has adequately sampled these suspect materials and determined the presence or absence of asbestos, according to MIOSHA's Asbestos Standards for Construction.
MIOSHA Asbestos Program: Launched in 1986, the primary function of the program is to ensure people working with asbestos are properly trained and that the individuals performing asbestos removal comply with rules governing the work activity. These rules are designed to protect not only the individual employee performing asbestos abatement work, but also the general public that occupy the area or building in which the work occurs.
Asbestos abatement workers, supervisors, project designers, inspectors, and management planners must successfully complete the appropriate initial or refresher training requirements and become accredited before working in Michigan.
Verify an Asbestos Accreditation in Michigan.
For more information or general asbestos questions, call the MIOSHA Construction Safety and Health Division: (517) 284-7680.
By Benjamin Block, Industrial Hygienist, General Industry Safety and Health Division (GISHD)
A 49-year-old Ann Arbor hotel maintenance worker died from carbon monoxide (CO) exposure after entering the hotel's third-floor boiler room in the fall of 2022.
The Victory Inn and Suites of Ann Arbor employee was a 24/7 on-call maintenance worker and lived at the hotel with his family. On the afternoon of Nov. 28, 2022, the employee left his room to do laundry, and afterwards, it appeared he took an elevator to the unoccupied third floor, where the facility’s boiler mechanical system was located.
The boiler system often failed to provide the large volume of hot water necessary for hotel operations, and it was not uncommon for the employee to receive work orders to inspect, refire, and perform other boiler repair maintenance, including on weekends. According to the hotel video surveillance footage which authorities later obtained, the employee unlocked the two double doors to the boiler room with the only set of keys, entered, and then closed the doors behind him.
Reported Missing
At 9 p.m. that night, the employee's girlfriend and two sons searched the premises after he failed to return to his room. The front desk staff was unable to review the security camera footage since only managers had access to the system. The following morning, the Ann Arbor Police Department arrived at the hotel in response to a welfare check issued for the employee’s son, who did not arrive at school. Responding police officers were informed the employee was missing when they made contact with the girlfriend. When officers reviewed the hotel's security footage with a manager, the employee was seen entering but never exiting the third-floor boiler room the previous day.
The Ann Arbor Fire Department responded and had to break down the deadbolt of the locked boiler room door. The first responders discovered the employee slumped against the boiler room’s wall in a seated position with his legs outstretched with a hand tucked underneath his sweatshirt, appearing to clutch at his chest. Responders did not attempt resuscitation as they determined the employee died long before their discovery. Shortly after entry into the boiler room, responders noticed a burning sulfur-like smell and began to experience lightheadedness and dizziness. The room was evacuated, and fire fighters used a device to survey the room for any atmospheric hazards.
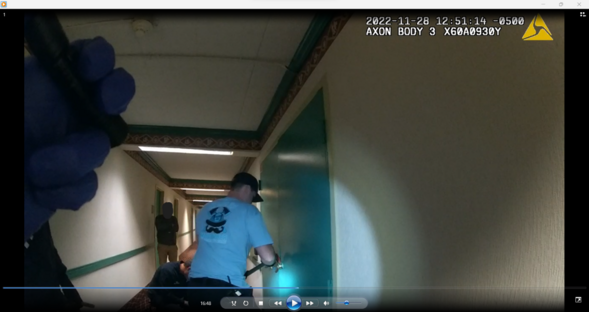 Body camera video shows Ann Arbor fire fighters attempting to break open the door leading into the third-floor boiler room.
No Carbon Monoxide Alarm
Immediately after fire fighters re-entered the boiler room, the department’s meter maxed out, with an instantaneous CO concentration of 499+ parts per million (ppm). The MIOSHA eight-hour, time-weighted-average limit for CO is 35 ppm, the five-minute ceiling limit is 200 ppm, and airborne concentrations exceeding 1,200 ppm are considered immediately dangerous to life or health. Responders re-entered the room in turnout gear and self-contained breathing apparatus in an unsuccessful attempt to locate the source of CO. Later testing revealed that the concentration of CO in the room exceeded 1,000 ppm (the upper testing limit of their equipment). It was determined the room was not equipped with either a functional CO alarm or metering device.
In the worker's autopsy, the cause of death was attributed to CO poisoning. The autopsy report revealed elevated levels of carboxyhemoglobin, a compound formed in red blood cells when CO binds to hemoglobin. Carboxyhemoglobin prevents red blood cells from performing their critical function of transporting oxygen to cells in the body because the CO binds far more tightly to hemoglobin than the oxygen does, and it displaces oxygen from the red blood cells. Carboxyhemoglobin values exceeding 50% are typically lethal, but even concentrations in the range of 10-30% have caused death. The postmortem carboxyhemoglobin level of the hotel maintenance employee was greater than 50.2%.
Through use of the Coburn equation, the employee’s carboxyhemoglobin value was converted into an estimated CO exposure level of 363.2 ppm in the air. However, this value is conservative and likely underrepresents the exposure experienced by the employee as there was uncertainty regarding the time of death and other factors that influence results produced by the equation.
Poor Ventilation
The MIOSHA investigation revealed the fatal CO concentrations in the boiler room resulted from improper and poor ventilation practices. Fire fighters observed that the boiler’s exhaust stack was covered by a large metal plate and the room’s cold air intake was covered with plastic garbage bags. Upon removal of the obstructions, the CO levels in the boiler room quickly returned to normal background levels.
The investigation also determined in the months prior to the incident, the employee was tasked with repairing areas of the facility’s roof to prevent further leaks and water intrusion due to local rainstorms. It was also revealed the hotel received multiple safety citations from state officials and local fire officials since 2015. These citations included violations of multiple boiler and fire safety rules including the installation of a boiler without a permit, improper functional controls on a boiler, and an “unsafe heating appliance”.
Interviews and employer records revealed that the employee had no prior experience or training regarding the maintenance, operation, and hazards of the boiler equipment and heating, ventilation, and air conditioning systems. The employee often sought assistance from other employees regarding the boiler and its operations and had also requested the employer hire a third-party to work on the device as he was uncomfortable working with the boiler. The employer never provided the employee with training regarding the operating procedures, hazards, and safeguards of the job.
|
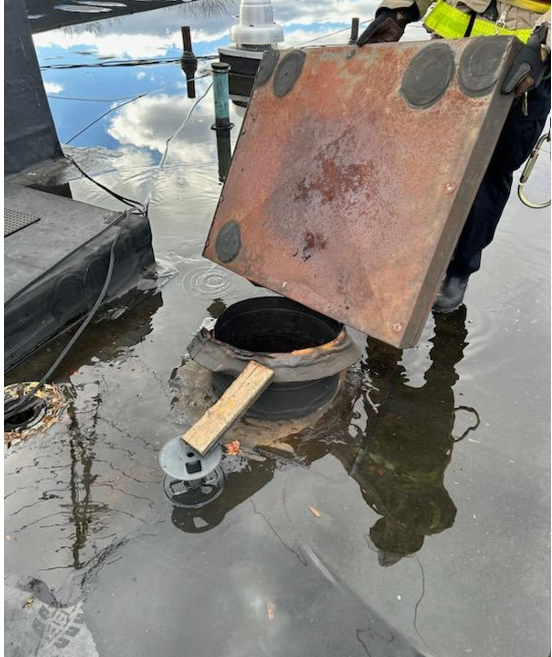 Photo of the steel plate that covered the exhaust vent stack for the third-floor boiler system.
Regulatory Violations Identified
Following a months-long fatality investigation and a companion inspection by the MIOSHA General Industry Safety and Health Division, eight citations were issued to the employer for its failure to comply with the following MIOSHA regulations:
Note: The citations have been appealed and may be subject to change.
Willful-Serious Violations
General Industry Standard Part 1, General Provision
- Rule 408.10011(a): The employer did not provide training to a newly assigned employee (the maintenance employee) regarding the operating procedures, hazards, and safeguards of the job.
General Industry Standard Part 301, Air Contaminants for General Industry
- Rule 325.51103(a)(iii): An employee’s exposure to a substance (CO) exceeded the ceiling limit specified for that substance in table G-1-A.
Serious Violations
General Industry Standard Part 520, Ventilation Control
- Rule 325.52005(1): The employer did not provide a supply ventilation system to ensure a flow of air into the working environment (the boiler room) to equally replace the volume of air exhausted.
- Rule 325.52010: The discharge location of the exhaust systems permitted exhausted air to reenter a workroom or other buildings directly, through air supply systems without substantial dilution
General Industry Standard Part 39, Design Safety Standards for Electrical Systems
- Rule 1910.303(g)(1): Access to an electrical panel in the establishment's maintenance room was blocked by equipment and debris, a condition that did not permit the ready and safe operation and maintenance of the panel.
General Industry Standard Part 54, Powered Groundskeeping Equipment
- Rule 408.15416(2): The safety mechanism on each of two partially filled portable containers used to fuel powered groundskeeping equipment had been removed.
General Industry Standard Part 305, Asbestos Standards for General Industry
- Rule 1910.1001(j)(3)(i): The building had not been surveyed to determine the presence, location, and quantity of asbestos-containing and presumed asbestos-containing materials at the worksite. The material in question was thermal system insulation in the form of pipe insulation/wrap and mudded fittings in the establishment's first and third floor boiler rooms.
General Industry Standard Part 430, Hazard Communication
- Rule 1910.1200(e)(1): A written hazard communication program addressing chemicals had not implemented in the workplace. Employees worked with and were exposed to hazardous chemical-containing products during hotel maintenance and housekeeping-related activities.
By Shannon Matsumoto, Manager, MIOSHA Standards and FOIA Division
General Industry Standard Part 73, Fire Brigades
MIOSHA held a public hearing June 14, 2023, on General Industry Standard Part 73: Fire Brigades. The current rules are being revised to adopt by reference the National Fire Protection Association (NFPA) standard 1971 Standard on Protective Ensembles for Structural Fire Fighting and Proximity, 2007 and 2013 editions. Due to other legislation, the Michigan Occupational Safety and Health Act, Act 154 of 1974 was amended to require the director of Labor and Economic Opportunity to promulgate rules regarding a firefighter’s use of firefighting foam concentrate containing a perfluoroalkyl or polyfluoroalkyl substance (PFAS).
General Industry Standard Part 8, Portable Fire Extinguishers
MIOSHA is amending General Industry Standard Part 8, Portable Fire Extinguishers to adopt portions of federal standards 29 CFR 1910.155 and 1910.157 for clarification for employee response to fires, and to further clarify employer responsibilities to determine employee actions related to fires.
Construction Standard Part 9, Excavation, Trenching and Shoring
MIOSHA is amending Construction Standard Part 9, Excavation, Trenching, and Shoring to add the word “vertically” to R 408.40945 “Trenching Boxes and Shields,” to match federal OSHA. These rules are also being amended to add definitions that are listed in federal OSHA’s Subpart P “Excavations.”
Construction Standard Part 26, Steel Erection
MIOSHA is amending the Construction Standard Part 26, Steel Erection to adopt by reference federal OSHA’s, Subpart R – Steel Erection, except for sections 29 CFR 1926.753, “Hoisting and Rigging,” and 1926.761, “Training,” as these are covered under Michigan rules within Construction Standard Part 26, Steel Erection in the following rules, R 408.4609, “Hoisting and rigging,” R 408.42610, “Multiple lift rigging procedure,” R 408.42655, “Special training.”
The final versions will be added to the MIOSHA standards web page once they are approved.
By Mike Krafcik, MIOSHA Communications Specialist
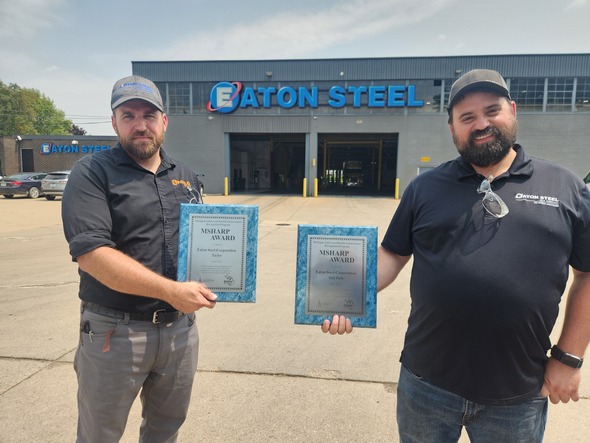 Eaton Steel Corporation safety managers are pictured during an award ceremony for two Eaton Steel bar facilities recognized with MIOSHA's MSHARP certification on Aug.2, 2023.
A pair of Detroit-area steel distribution facilities operated by the same company were recognized for achieving one of MIOSHA's top workplace safety and health award status.
Eaton Steel Bar Corporation's Oak Park and Taylor facilities were awarded the Michigan Safety and Health Achievement Recognition Program (MSHARP) certification from MIOSHA in June. The metal merchant wholesaler facility was recognized for its state-of-the-art camera system used to analyze all safety incidents and accidents. The MSHARP award recognizes workplaces that have achieved excellence in their safety and health practices, placing these companies among the elite few that go above and beyond MIOSHA standards.
The MIOSHA Onsite Consultation Program operates MSHARP and works with employers to help them become self-sufficient in managing occupational safety and health. MIOSHA onsite consultants provide feedback on best practices, offering an incentive of a 24-month exemption from regular scheduled MIOSHA inspections.
Visit michigan.gov/MSHARP to learn about MSHARP and MIOSHA’s other cooperative programs for employers.
|
Furniture Company Achieves Rising Star Status
A West Michigan based office furniture manufacturer was recognized as a Rising STAR participant in the Michigan Voluntary Protection Program (MVPP).
Nucraft Furniture in Comstock Park received MVPP Rising Star status for the company's successful efforts in partnering for excellence in workplace safety and health. The 240-person company was noted for having a company culture that promotes management commitment, employee involvement, and a desire to excel to promote safety and health for all.
MVPP is a MIOSHA cooperative program designed to assist employers and employees by providing a mechanism and a set of criteria designed to evaluate and recognize outstanding safety and health management systems.
The Rising Star award provides the "stepping stone" for those establishments that have the desire and potential to achieve Star Status within one to three years. Rising Star participants have a good safety and health management system and have incidence rates at or below the industry average for two out of the last three years.
"We are incredibly honored to receive this prestigious safety award from MIOSHA. This recognition is a testament to our unwavering commitment to ensuring the well-being and security of our associates and customers," said Scott Petzold, Nucraft Furniture's vice president of human resources.
There are two levels of recognition in the MVPP — the Michigan Star and Rising Star Programs.
-
Michigan Star: designed for workplaces that have an exemplary safety and health management system with injury and illness incidence rates below the industry average for the last three years.
-
Rising Star: provides the "stepping stone" for those establishments that have the desire and potential to achieve Star Status within one to three years. Rising Star participants have a good safety and health management system and have incidence rates at or below the industry average for two out of the last three years.
|
 |
Quick Links
Agency/Division Instructions/Memorandums Air Contaminants Initiative Asbestos Program CET Request for Consultative Assistance Services (RCA) CET Training Calendar Construction Safety and Health Division (CSHD) DVD/Video Library Service Employee Safety, Health, and Discrimination Complaint Forms Fall Prevention Campaign (STOP FALLS. SAVE LIVES.) General Industry Safety and Health Division (GISHD) Hazard Communication/GHS Laboratory and Equipment Services Michigan Alliances Michigan Safety and Health Achievement Recognition Program (MSHARP) Michigan Voluntary Protection Program (MVPP) MIOSHA FOIA Request MIOSHA News MIOSHA Publications MIOSHA Recordkeeping MIOSHA Standards MIOSHA Training Institute (MTI) MIOSHA Updates MIOSHA Variances Radiation Safety Section Residential Construction Strategic Plan and Initiatives Telephone, Mailing and Email Addresses
|