Volume 31, Issue 2, Spring 2023
Bart Pickelman, MIOSHA Director
Work related fatalities from falls from elevation are on the rise nationwide, accounting for 680 of 5,190 workplace fatalities in all industries in 2021, according to the U.S. Bureau of Labor Statistics.
Falls from elevation are the leading cause of construction worker deaths, which increased 7.2 percent from 2020, accounting for 370 fatalities in 2021. These deaths were preventable.
Michigan Occupational Safety and Health Administration (MIOSHA) is supporting the federal Occupational Safety and Health Administration’s (OSHA) National Safety Stand-Down to Prevent Falls in Construction campaign May 1-5, 2023 by coordinating and participating in stand-down events across Michigan. A Safety Stand-Down is a voluntary event that encourages employers to talk directly with their workers about hazard recognition and how to implement appropriate safety measures.
MIOSHA is teaming up with employers and workers for other industry stand-down events which allows employers and workers to engage in dialogue about safety in their respective industries.
-
National Grain Safety Week March 27-31, 2023 (Each year, hundreds are injured or killed from preventable hazards while working in grain storage and handling in the U.S.)
-
Trench Safety Stand Down Week June 14-18, 2023, sponsored by the National Utility Contractors Association.
In Michigan, August 7-11, 2023, (MIOSHA) is partnering with employers to "Take a Stand" for workplace safety and health by dedicating our professional staff to visit Michigan high-hazard industries targeted by the MIOSHA. There will be NO citations or fines for participating workplaces. However, participants must agree to correct all serious conditions.
MIOSHA is reminding all Michigan employers of their duty to protect employees from fall hazards. Workers who are six feet or more above lower levels are at risk of serious injury or death if they should fall. To ensure protection, employers must provide fall protection and the right equipment for the job, including proper ladders, scaffolds and safety gear.
I want to thank all Michigan employers and employees in advance for participating in these stand-down events and most importantly for keeping safety and health as a focus on the job so everyone can return home unharmed at the end of their work shift.
|
By Jeff Nerem, Safety & Environmental Administrator for Rexair LLC
The MIOSHA Training Institute (MTI) certificate program offers participants an opportunity to be recognized for their educational efforts and increased technical expertise. There are six certificate programs which includes General Industry Safety and Health, Construction Safety and Health, MIOSHA Compliance for General Industry, MIOSHA Compliance for Construction, Safety and Health Management Systems and Occupational Health.
Typically it takes several years to complete all six MTI certificates, but Jeff Nerem finished his certifications in a little over 12 months.
Nerem is the safety & environmental administrator for Rexair LLC, a home cleaning product manufacturer based in Cadillac. Here's Jeff's story about his experience:
Rexair's former safety manager became ill before his health rapidly declined in late 2018. His eventual death caught everyone by surprise. Suddenly, Jeff became thrust into his new position at the 200-person manufacturing facility.
Jeff was tapped for the position since his military career was filled with risks and hazards associated with living and working on ships, similar to a 24-7 factory operation. Before Jeff retired from the U.S. Navy as a lieutenant commander, he investigated mishaps, accidents and injuries and over 50 ships as a Navy engineering auditor. Identifying and mitigating potential hazards had become second nature.
However, this new assignment was in the civilian world, where the risks and rules are different. Need an example? The Navy almost exclusively used OSHA's lockout/tagout practices since equipment and systems may need to be back in service immediately, "There was no time to search for the person with a padlock key when hundreds of lives depend on the equipment working immediately," Nerem said. "In the civilian world, urgency should not be there, so locks are the standard."
Jeff needed to get quickly up to speed on current safety regulations and programs governing industry. Good timing exposed him to the MIOSHA Training Institute (MTI) Program, an opportunity that seemed too important to pass up:
“With full support of management, I embarked on an ambitious training schedule. MIOSHA’s MTI Program offered classes throughout the state, for a nominal cost. The instruction was from employees within the MIOSHA Consultation Education and Training (CET) Division, engaged in educating employers. Several of the CET employees teaching the classes had a former enforcement background. The knowledge passed on was invaluable to our company in assisting in the review or in establishing new programs to ensure not just safety, but compliance.”
Although it did require extensive travel around the state, Jeff completed five of the Certification Courses within one year. After delays due to COVID-19, he was able to complete the sixth and final certification the following year.
It was time and effort well spent.
|
Shane Cappama, Terminal Manager at Marathon Petroleum Company: North Muskegon Terminal
The North Muskegon terminal, a bulk fuel storage and distribution facility near Lake Michigan first opened in 1952, before it was purchased by the Marathon Petroleum Company (MPC) in 1963.
Fuel truck drivers use the terminal's loading racks to transport gasoline and diesel fuel to suppliers across the country. The terminal achieved MIOSHA's Michigan Voluntary Protection Program (MVPP) Star Status in 2015.
Below are examples of MVPP best practices:
Ergonomics and labeling at the load rack
Labels and color-coded stickers have been placed at each of the truckload racks to communicate information to the drivers.
- Color-coded stickers inform drivers what fuel is available at each loading arm.
- The number on each arm is correlated with our system to make it easier for the driver to start the correct arm.
- Additional hooks were added to secure the load heads and to prevent swinging.
- A sign at each of the lane entrances indicates if a product is available.
- A video display screen 0allows drivers to enter their load information and communicate with other drivers who are required to see those messages before leaving the terminal.
|
Steps over piping between two tanks
Through an award from the MVPP program, Marathon purchased steps to increase worker safety inside a tank farm at the terminal. Previously, employees had to step over the pipes to access supply valves and jet nozzles. The stairs allow employees to walk over piping, thus eliminating a tripping hazard.
|
Vapor Recovery Unit Rewire project
In this project, electrical conduits were moved from the ground level to above the head to eliminate tripping hazards.
|
|
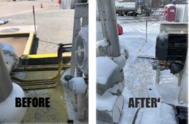 |
By Benjamin Block, Industrial Hygienist, General Industry Safety and Health Division (GISHD)
A commercial diver drowned during an underwater inspection of the Calkins Bridge hydroelectric dam in Allegan County on July 7, 2021. The diver was part of a team of two scuba divers and three onshore dive tenders.
One month before the deadly accident, the dive team devised an inspection dive plan, which prepped them for any potential hazards. The day before the dive, heavy rain in the area created drastically different conditions than originally anticipated.
The Calkins Bridge dam has powerhouse and spillway sections, and each section has an upstream and downstream side. A thin ‘log chute’ on the downstream side divides the powerhouse and spillway sections. At the end of the log chute, the waters from the spillway and powerhouse sections combine.
|
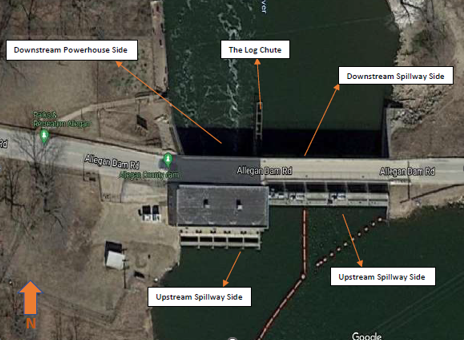 Pictured is a Google Earth image of the Calkins Bridge Dam located near Allegan, Michigan.
Initially, the team intended to inspect the dam’s upstream and downstream sections on the powerhouse side. On the day of the incident, during the pre-dive safety walkaround, the dive team observed the dam’s spillway was operational, along with turbulent and choppy water conditions resulting in strong currents. Due to this, divers decided to limit their inspection to one-half to three-quarters of the log chute.
No additional safety protocols, such as line-tending, were in place on the day of the fatality. The team’s standby diver (Diver C) was stationed on a dry surface platform on the dam's downstream lip underneath the powerhouse. However, the standby diver had no immediate access to his own diving gear. The team’s 12-foot boat was stowed in a fenced-in parking lot near the dam’s powerhouse, located over a half-mile from the nearest launch.
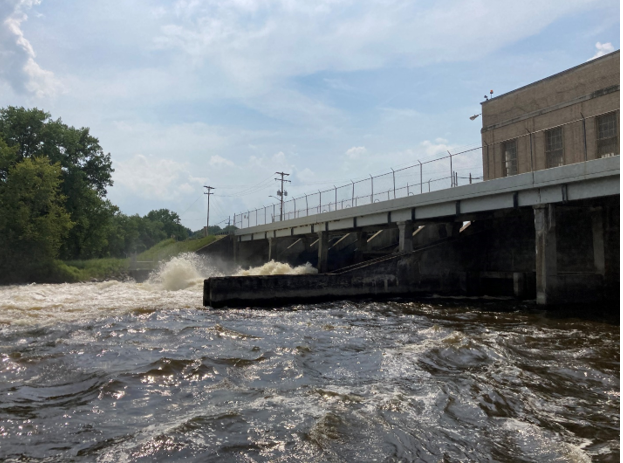 A photo of the Calkins Bridge Dam's downstream powerhouse section taken by Diver B. This photo shows the intensity of the spillway flow and choppy, murky, and turbulent current awaiting the divers.
Dangerous conditions
At 11:10 a.m., two scuba divers experienced dangerous conditions when they entered the water on the downstream side of the powerhouse. The surviving diver (Diver B) encountered zero-visibility underwater and choppy water at the surface, according to helmet camera footage. The team’s wireless communication system proved ineffective in the turbulent waters, and divers relied on infrequent visual contact to track each other. As the dive progressed, both divers lost visual contact with each other. The onshore dive tenders were unable to locate or readily communicate with either diver.
Neither diver was line-tended, but the dive was not terminated despite the inability of the divers or other dive team members to maintain continuous visual contact with each other.
(Diver A) was last observed on Diver B’s camera footage swimming toward the tail end of the log chute and in the direction of the spillway current. Due to the turbulent waters, the standby diver lost visual track of Diver A’s bubble trail along the log chute.
Diver A’s disappearance was recognized by his dive partner at 11:26 a.m. Subsequently, the standby diver detached himself from his fall protection system, climbed a ladder from the platform under the powerhouse, retrieved a company truck and boat, and drove two-thirds of a mile to the nearest boat launch before dispatching the boat into the river.
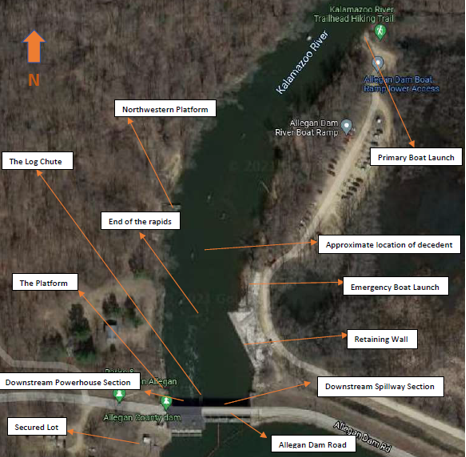 The team attempted to locate the missing diver using side-scanning sonar while searching the river in the boat before eventually contacting rescue services at approximately 12:00 p.m. Rescue services arrived at 12:05 p.m., and search efforts were immediately initiated. Responding rescue divers later commented on the strong current during rescue and recovery operations. The dam’s controlling authority eventually shut down the spillway side to aid the search efforts at 2:00 p.m. Diver A’s body was located roughly 150 yards downstream from the dam at 3:48 p.m.
Information extracted from Diver A’s dive computer revealed his rate nearly quadrupled within minutes around 11:26 a.m., which caused a rapid depletion of his remaining air. Shortly after 11:26 a.m., Diver A’s air supply was exhausted, and his breathing rate fell to zero. Following an autopsy, the diver's death was ruled a drowning, according to medical examiners.
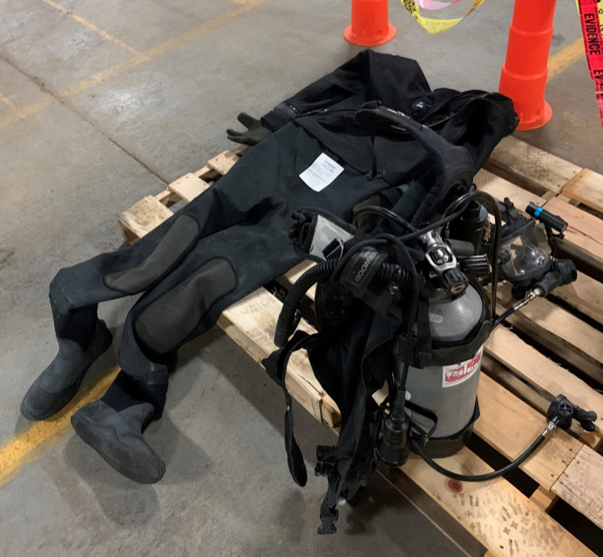 Diver A’s gear is pictured inside the Allegan County Sheriff’s Office evidence garage.
Regulatory violations identified
Following a nearly year-long investigation by the MIOSHA General Industry Safety and Health Division, eight citations were issued to the employer for its failure to comply with the following rules of Occupational Health Standard Part 504, Diving Operations.
Note: The citations have been appealed and may be subject to change.
- 1910.420(b)(1): The safe practices manual shall contain a copy of this standard and the employer’s policies for implementing the requirements of this standard.
- 1910.420(b)(2): For each diving mode engaged in, the safe practices manual shall include: i) Safety procedures and checklists for diving operations; ii) Assignments and responsibilities of the dive team members; iii) Equipment procedures and checklists; and iv) Emergency procedures for fire, equipment failure, adverse environmental conditions, or medical illness and injury.
- 1910.421(d): Planning of a diving operation shall include an assessment of the safety and health aspects of the following: 2) Surface and underwater conditions and hazards; 5) Diving equipment and systems; and 9) Emergency procedures.
- 1910.422(i): The working interval of a dive shall be terminated when: 1) A diver requests termination; 2) A diver fails to respond correctly to communications or signals from a dive team member; 3) Communications are lost and cannot be quickly re-established between the diver and a dive team member at the dive location; or 4) A diver begins to use diver-carried reserve breathing gas or the dive-location reserve breathing gas.
- 1910.424(c)(1): A standby diver shall be available while a diver is in the water.
- 1910.424(c)(2): A diver shall be line-tended from the surface or accompanied by another diver in the water in continuous visual contact during the diving operations.
- 1910.430(a)(2): Each equipment modification, repair, test, calibration, or maintenance service shall be recorded by means of a tagging or logging system and include the date and nature of work performed, and the name or initials of the person performing the work.
- 1910.430(j)(1): Except when heavy gear is worn, divers shall be equipped with a weight belt or assembly capable of quick release.
By Shannon Matsumoto, Manager, MIOSHA FOIA Section/Technical Services Division
MIOSHA General Industry Part 73, Fire Brigades
MIOSHA is in the process of reviewing General Industry Standard Part 73: Fire Brigades. The current rules are being revised to adopt by reference National Fire Protection Association (NFPA) standard 1971 Standard on Protective Ensembles for Structural Fire Fighting and Proximity, 2007 and 2013 editions. Due to other legislation, the Michigan Occupational Safety and Health Act, Act 154 of 1974 was amended to require the Director of Labor and Economic Opportunity to promulgate rules regarding a firefighter’s use of firefighting foam concentrate containing a perfluoroalkyl or polyfluoroalkyl substance (PFAS).
General Industry Part 23, Hydraulic Power Presses
MIOSHA recently amended General Industry Standard Part 23- Hydraulic Power Presses, to be comparable with federal Occupational Safety and Health Administration (OSHA) standard 1910.217(d)(3), “Mechanical Power Presses.” MIOSHA’s R 408.12363(3) formally stated “employee,” and was changed to “employer” to be in line with federal OSHA. Effective Date: March 27, 2023.
The final versions will be added to the MIOSHA standards web page once they are promulgated.
By Eric Allen & Dan Maki, Health and Safety Managers, Construction Safety and Health Division
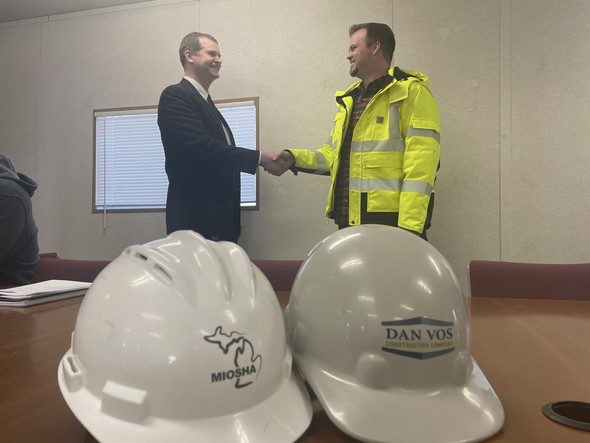 MIOSHA Construction Safety and Health Division health and safety manager Eric Allen is pictured with Dan Vos Constuction safety manager Colin Boughner during a March 15 partnership event in Hudsonville.
New Partnerships with Dan Vos Construction Co. and Walsh Construction Co. II
In March, MIOSHA entered into two new partnerships with construction companies committed to protecting workers at their job sites in Michigan.
MIOSHA entered into a partnership agreement with Walsh Construction Co. II, its subcontractors, and partnering unions March 2. The Chicago-based construction company is overseeing construction on the 3-mile interstate realignment project on I-496 in downtown Lansing. The $80 million project includes improvements related to drainage, traffic, motorist safety, superstructures, and 17 bridges. The project also includes a noise wall installation.
On March 15, 2023, MIOSHA entered into a partnership agreement with Dan Vos Construction Co., along with partnering subcontractors, and unions involved in the construction of a 70,000 square foot beef processing facility in Hudsonville, Mich. The new facility set to open in late 2023, will be triple the size of the existing beef processing facility on site. The new multi-million dollar facility will provide increased processing capabilities and increase overall plant efficiency.
In all MIOSHA's partnership agreements, construction companies endorse the ultimate goal of ZERO injuries through construction safety policies and procedures support the Quality of Life on this project by ensuring “Everyone goes home the way that they came to work.” The injury free vision of a workforce that is supported, motivated and inspired, must start with the construction craft men and women and their organizations who come from the local communities to build this project.
The leadership of MIOSHA, Walsh Construction Co. II, Dan Vos Construction Company, partnering employers, and partnering unions through a common vision, is committed to providing all trades people and subcontractors a healthful and safe work place and to demonstrate leadership, responsibility, and accountability in furthering work health and safety at all levels.
The practice of diligence, good judgment, and common sense by all project team members including subcontractors helps to create an environment in which the frequency of accidents is substantially reduced. Both general contractors, Walsh Construction Co. II and Dan Vos Construction Co., respective Safety and Health Programs have the total commitment of all management levels and receives top priority in its application.
MIOSHA Partnerships have demonstrated safer statistics than the rest of the construction industry when compared to National and State statistics. This is based on information that has been collected from the Bureau of Labor Statistics – Census of Fatal Occupational Injuries (CFOI) and Survey of Occupational Injuries and Illnesses.
MIOSHA has had many successful partnership sites over the years. If you are interested in speaking to someone at MIOSHA regarding a potential partnership, please contact the MIOSHA Construction Safety and Health Division at 517-284-7680.
Quick Links
Agency/Division Instructions/Memorandums Air Contaminants Initiative Asbestos Program CET Request for Consultative Assistance Services (RCA) CET Training Calendar Construction Safety and Health Division (CSHD) DVD/Video Library Service Employee Safety, Health, and Discrimination Complaint Forms Fall Prevention Campaign (STOP FALLS. SAVE LIVES.) General Industry Safety and Health Division (GISHD) Hazard Communication/GHS Laboratory and Equipment Services Michigan Alliances Michigan Safety and Health Achievement Recognition Program (MSHARP) Michigan Voluntary Protection Program (MVPP) MIOSHA FOIA Request MIOSHA News MIOSHA Publications MIOSHA Recordkeeping MIOSHA Standards MIOSHA Training Institute (MTI) MIOSHA Updates MIOSHA Variances Radiation Safety Section Residential Construction Strategic Plan and Initiatives Telephone, Mailing and Email Addresses
|