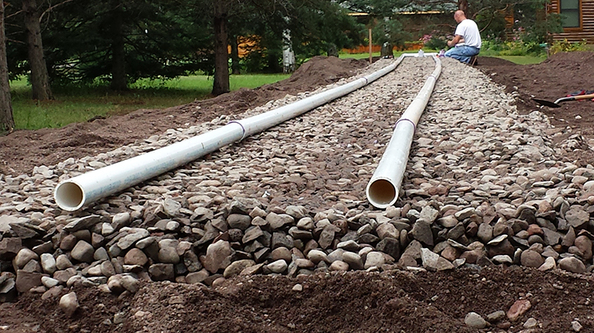
This past summer, the MPCA's Barb McCarthy, like many people who were planning to sell their home or lake place, needed to have her septic system inspected and given a clean bill of health before her house could change hands. This requirement is one of several "triggers" many Minnesota counties have adopted in order to identify and upgrade or replace septic systems that do not meet current standards.
But knowing what she does about the soils where she lives, "I didn't even bother with an inspection," says McCarthy who works in the MPCA Subsurface Sewage Treatment System (SSTS) program. "I knew my existing system wasn't going to meet standards because of where I live in St. Louis County (near Duluth). The soils here are not suitable for the type of system I had in place."
By "not suitable" she meant there are only a few inches of permeable soil above several feet of mostly impermeable clay, a fact that was reinforced earlier this summer when soil scientists from around the country met in Duluth for a national conference hosted by the National Resources Conservation Service (NRCS).
They visited McCarthy's property and a few other sites near Duluth to dig pits and analyze the resulting soil profiles. The soil pit on McCarthy's property revealed about six to eight inches of soil suitable for a septic system drainfield and several feet of basically impervious red clay (see photo below).
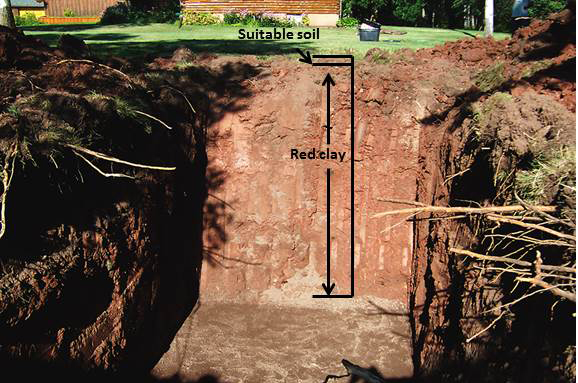
Getting the right "profile"
For adequate treatment, wastewater needs to travel through at least 36 inches of suitable existing soil or other filter medium, such as sand, at just the right speed, not too fast or too slow. There also needs to be at least three feet of separation between where wastewater enters the treatment field and the seasonal high water table (the depth where the soil is saturated during the wettest part of the year) in order to avoid contaminating ground water. In McCarthy’s case, the depth to groundwater was not an issue, but the composition of the soil certainly was.
Before designing a septic system for a homeowner, a septic professional must first dig a hole to analyze the soil conditions (soil profile and distance to seasonally saturated soils) and provide the homeowner with design options that would work at that particular site.
In some cases, the soil profile is such that a drainfield can be built rather simply by digging shallow trenches and applying a layer of clean gravel in which is embedded perforated piping through which effluent is distributed. This is known as an in-ground trench system. Oftentimes, however, existing conditions require building a sand mound to provide the proper soil profile and separation from groundwater needed to adequately treat septic waste and meet current standards. A mound system was definitely required at McCarthy's residence.
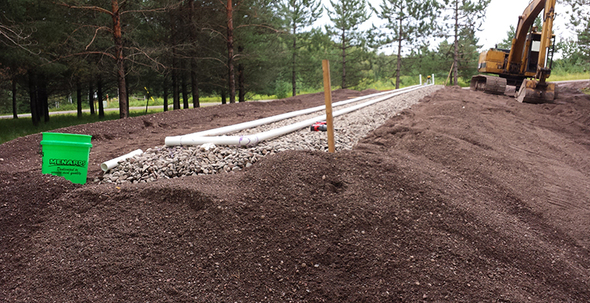
Building the mound
McCarthy worked with her septic system designer and installer to pick a suitable location for the mound system that would service the 2,100 square foot, three-bedroom home. Many trees had to be removed to make room for the mound. And because the existing suitable soil layer in her yard is only six inches deep at its thinnest, the mound needed 30 to 32 inches of washed sand. Sand containing silt and clay and other "fines" can clog the spaces between sand grains.
Placed on top of the sand is a rock bed that is 5 feet by 85 feet (see photo above). The rocks help to disperse effluent into the underlying sand bed. The rocks too must be cleaned of fine materials to prevent them from being washed down into the sand where they can clog the system. Drainfield rock is larger than an inch and half across.
Perforated effluent distribution pipes are installed on top of the rock. The pipes are then then covered with additional rock to protect the pipes.
The rock bed is covered by a special fabric material that allows air and water to pass through but prevents topsoil and sand from entering the rock bed. The filter fabric is then covered with loam and sandy loam and then topsoil so grass will grow on the mound.
Liquid and solid waste generated by sinks, bathtubs, showers and toilets runs from the house via a pipe known as a “building sewer” to a combination septic tank/pump tank (above). McCarthy’s septic tank is 1,000 gallons which then flows into a 500 gallon pump tank or dose tank.
McCarthy’s system is designed to treat 300 gallons of wastewater each day to the mound via a supply pipe (pictured above). Wastewater is pumped to the mound throughout the day through a series of four “doses” of about 70 gallons each when the float is activated and the pump turns on. This allows time between doses for the wastewater to effectively move through the mound sand and into the underlying soil.
“It works like the sump pump in your house,” McCarthy says. “It will draw down to a certain level in the tank and then shut off until the pump tank fills back to that level and another dose is sent to the mound.”
The wastewater is sent to the mound under pressure that has been calculated to ensure wastewater will fill the entire length of the perforated piping located within the mound and be dispersed along the entire length of the mound and not just one portion where it could pool up. When the pump shuts off, water remaining in the supply pipe drains back into the pump tank, preventing water in the pipe from freezing during the winter.
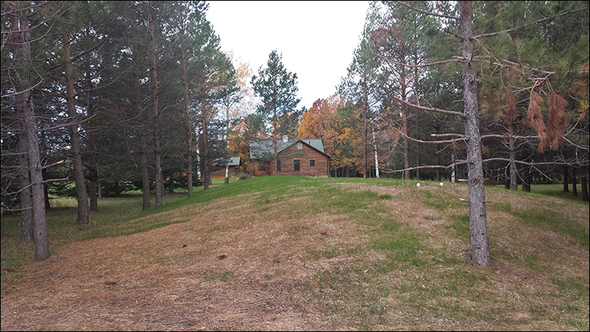
Insulation important for new septic systems
When completed, McCarthy’s mound measured 125 feet long and 40 feet wide at a total cost of more than $15,000. “When you average the cost of the system over its expected lifetime of 30 years or more you come up with a number that is not that different than what those who live in urban areas pay for their wastewater treatment,” McCarthy says. The big difference with the cost for a rural septic system is the investment is made up front, which can pose a challenge for some homeowners if they are not recouping some or all of that cost during a property transfer.
The mound’s large dimensions are needed on this site to ensure that the effluent is able to move through it at the proper rate and in a way that does not allow the effluent to surface at the ‘toe’ or downslope berm of the mound to keep the sewage below the surface.
McCarthy’s mound was completed in late summer, in time to get a good cover of grass started. Grass and other cover plants are important as they help provide insulation that will help prevent freezing problems, especially during the first winter following system construction. She plans to add straw this November to ensure there won’t be any problems. She also hopes there will be snow cover this year which provides additional insulation.
Protecting, maintaining a significant investment
It’s important year around to
avoid any type of vehicle or even much foot traffic on whatever type of
septic system is in place. Compacting the soil above the drainfield,
tank and pipes leading to and from the various components of a septic
system make it more likely that frost will reach these areas and cause
freezing problems. Planting native grasses and flowers over the mound
that don’t require as much maintenance as lawn grass is a good way to
lessen mound traffic.
To
keep a septic system working efficiently, and to avoid potentially
costly repairs or premature replacement, homeowners should contact a
septic system maintainer at least once every three years to have solids
removed from the septic tank, more often if you have a large family or
lots of visitors during the summer at your lake place. This prevents
solids from getting to the mound or drainfield and plugging it up.
At
least once a year homeowners should check the condition of inspection
pipes and tank covers to make sure they are securely in place and not
cracked, broken or missing. This prevents accidents and cold air from
entering during the winter months.
Contact a septic professional any time you notice something may not be working correctly in your septic system. Catching and fixing problems early will likely save money in the long run.The MPCA keeps a list of licensed septic professionals.
For more information on how to keep your septic system working well for many years, check the MPCA's information for homeowners webpage.
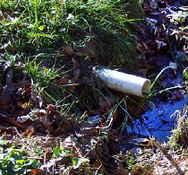
Locating and correcting straight-pipe discharges of septic waste is a priority for local units of government (LGUs) as well as the MPCA. The straight pipe law (Minn. Stat. 115.55 Subd. 11) provides an additional
tool for LGUs to use in correcting straight-pipe discharges within their
jurisdictions by facilitating a cooperative local-state enforcement process.
The law states that an inspector who discovers the existence of a
straight-pipe system shall issue a noncompliance notice to the owner of the
straight-pipe system and forward a copy
of the notice to the Agency. The
notice must state that the owner needs to replace or discontinue the use of the
straight-pipe system within 10 months of receiving the notice.
The notice
should include a specific date by which compliance should occur. If the owner does not replace or discontinue
the use of the straight-pipe system within 10 months, the owner of the straight-pipe system shall be subject to an
administrative penalty of $500 per month of noncompliance beyond the 10-month
period.
If the system owner fails to replace or discontinue the
straight-pipe discharge by the due date, the LGU may referrer the case to the
MPCA. Referrals should be made to the MPCA by filling out the SSTS Enforcement
Referrals from Local Programs form.
At month 10 plus one day, the MPCA will
initiate the Administrative Penalty Order (APO) process. The MPCA will issue
subsequent combined APOs until the system owner has completely satisfied all
the required items.
The MPCA encourages LGUs to contact their assigned SSTS
field staff early in the process. MPCA staff can provide technical
assistance regarding what documentation the MPCA needs from the LGU to be able
to accept the referral after the initial 10-month period.
|
|